Author |
Message |
Dan Dickinson
Industry Professional

|
Posted: Fri 11 Jan, 2008 4:21 pm Post subject: New scabbard completed.....comments and suggestions welcome |
|
|
I have just completed a new Poitiers scabbard for forum member Andrew Babbini. Andrew wanted a fairly simple scabbard, so i tried to follow that in the simple decoration of the mounts and chape.
The body of the scabbard is a poplar core covered in chocolate brown leather. The suspension is oxblood leather with hand forged buckles/belt-mounts. Comments and suggestions are welcome.
Dan
P.S. Sorry for the poor quality pics, photography is apparently not one of my talents.
Attachment: 20.37 KB
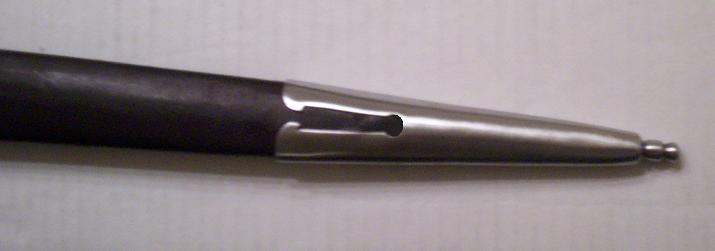
Attachment: 30.05 KB
[ Download ]
Attachment: 42.65 KB
[ Download ]
|
|
|
 |
Dan Dickinson
Industry Professional

|
Posted: Fri 11 Jan, 2008 4:40 pm Post subject: |
|
|
A shot of the back.
Attachment: 46.68 KB
[ Download ]
|
|
|
 |
Allen W
|
Posted: Fri 11 Jan, 2008 6:55 pm Post subject: |
|
|
Looks good. How did you make the chape?
|
|
|
 |
Dan Dickinson
Industry Professional

|
Posted: Fri 11 Jan, 2008 7:21 pm Post subject: |
|
|
I made it out of sheet metal with the seam up the back and the finial on the end welded on. I then removed the material from the cut-out decoration.
|
|
|
 |
Allen Andrews

|
Posted: Sat 12 Jan, 2008 5:46 am Post subject: |
|
|
That's nice, I really like how the chape turned out.
" I would not snare even an orc with a falsehood. "
Faramir son of Denethor
Words to live by. (Yes, I know he's not a real person)
|
|
|
 |
Jared Smith

|
Posted: Sat 12 Jan, 2008 8:06 am Post subject: |
|
|
I'd like to see a close up of the chape construction. It looks very good. Is it a one piece with welded seam up the back, or is only the finial welded on? Also, how did you make the finial?
Absence of evidence is not necessarily evidence of absence!
|
|
|
 |
Dan Dickinson
Industry Professional

|
Posted: Sat 12 Jan, 2008 8:36 am Post subject: |
|
|
I formed the chape out of sheet into a flattened cone with the ends meeting at the back, then inserted the finial into the small end. I then welded the seam at the back and around the end. The finial is a piece of steel rod that has been decoratively turned.
Hope this explanation helps,
Dan
|
|
|
 |
Thomas Parsons
|
Posted: Sat 12 Jan, 2008 9:05 am Post subject: |
|
|
Really nice! Just one question: why no matching hardware at the "hilt" end of the scabbard?
|
|
|
 |
Antal László

|
Posted: Sat 12 Jan, 2008 9:06 am Post subject: |
|
|
Looks great! How did You fix the chape?
|
|
|
 |
Chad Arnow
myArmoury Team


|
Posted: Sat 12 Jan, 2008 9:37 am Post subject: |
|
|
Thomas Parsons wrote: | Really nice! Just one question: why no matching hardware at the "hilt" end of the scabbard? |
While there are a number of examples of metal fittings at both ends of the scabbard (and often in between), it was not always done. In fact, there are many examples of scabbards in art with metal only on the point end of the scabbard.
ChadA
http://chadarnow.com/
|
|
|
 |
Allen W
|
Posted: Sat 12 Jan, 2008 10:21 am Post subject: |
|
|
I apologize if this is getting little old. I have made one scabbard in my life. The carving went well but inefficiently and I used too hard a wood. however I had to recycle a chape from a windlass scabbard as I had no idea mow to form one from commonly available hardware supplies. This is the main piece of information I look for in every scabbard thread. I read people talking of forming them on mandrel but what do you use for a mandrel? I also hear of using bee's wax when fitting leather wraps to both grips and scabbards but don't understand why or how? I don't want to badger you about the chape but the forming process has me stymied. Do you do your own welding and with what?
|
|
|
 |
Chad Arnow
myArmoury Team


|
Posted: Sat 12 Jan, 2008 11:05 am Post subject: |
|
|
Allen W wrote: | This is the main piece of information I look for in every scabbard thread. I read people talking of forming them on mandrel but what do you use for a mandrel? |
Some scabbard makers have built there own mandrels, I believe. Some have pieces of wood/metal with channels in them that they use to get the U-shape, then they bend it around the scabbard tip.
Others, depending on thickness of the wood and workability of the metal chape material, use the scabbarded sword as a mandrel. What better mandrel than the actual item the chape is ending up on?
ChadA
http://chadarnow.com/
|
|
|
 |
Thomas Parsons
|
Posted: Sat 12 Jan, 2008 2:16 pm Post subject: |
|
|
Thomas Parsons wrote:
Really nice! Just one question: why no matching hardware at the "hilt" end of the scabbard?
While there are a number of examples of metal fittings at both ends of the scabbard (and often in between), it was not always done. In fact, there are many examples of scabbards in art with metal only on the point end of the scabbard.
- I was just wondering if there was any particular reason for having opted for this layout...
|
|
|
 |
Dan Dickinson
Industry Professional

|
Posted: Sat 12 Jan, 2008 4:13 pm Post subject: |
|
|
Ok, let's see if i can keep the questions straight. First, the chape is fitted to the scabbard using a friction fit...i.e. shaped to fit quite closely placed as far as hand pressure will allow and then tapped into place the rest of the way with a rubber mallet.
Secondly, I didn't use a mandil for most of the shaping, but instead slowly bent it a little at a time, using a vice and rubber mallet and finishing with an armourer's stake towards the end. I'm afraid I don't do my own welding yet, but had a friend who own a body shop weld it with a MIG welder. After it was welded together I used the scabbard as a reference as I adjusted the fit. As far as beeswax.....I'm assuming that the reference you're referring to is using it as a sealant/reconditioner once the leather is in place.....not as a glue. For glue I used a commercially available leather cement.
Finally, as to why there is no locket at the mouth end of the scabbard:
Althoughs cabbards that often accompany many lower-end swords have lockets at the mouth, very few medieval scabbards (at least that i am aware of) had metal bands around the mouth just to have them there. Rather, most metal mounts found on the upper portions of scabbards seem to have served as attachment points for suspension rings .....since this scabbard uses knotted leather straps to attach it to the belt, metal mounts did not seem to fit/seem authentic.
I hope this helps,
Dan
|
|
|
 |
Aaron Schnatterly
|
Posted: Sat 12 Jan, 2008 6:20 pm Post subject: |
|
|
Chad Arnow wrote: | Allen W wrote: | This is the main piece of information I look for in every scabbard thread. I read people talking of forming them on mandrel but what do you use for a mandrel? |
Some scabbard makers have built there own mandrels, I believe. Some have pieces of wood/metal with channels in them that they use to get the U-shape, then they bend it around the scabbard tip.
Others, depending on thickness of the wood and workability of the metal chape material, use the scabbarded sword as a mandrel. What better mandrel than the actual item the chape is ending up on?  |
I do both, sometimes.
Aside from my anvil, 2 pairs of tongs, and my primary forging hammers, every other tool I use that is related to forging, dishing, raising, creasing, etc. was made by me.
The mandrels I use are steel, welded on to a hardy shank. I have a dozen different shapes, and will be making new ones often for new projects, armour work, etc. Most of my special-purpose hammers don't look like they did when I got them... I work some things hot, some cold, often a combination of both.
Nearly all of the tweaking I do uses mandrels or the anvil face. Once in a while, if I don't get quite the fit I want, I might use the scabbard itself as a mandrel, but that is exceptionally rare, and only to compress the sides in order to secure the piece. I don't do this often, as I don't want to wreck the piece in the final touches.
Allen W wrote: | Do you do your own welding and with what? |
As for joining, I generally gas weld, braze, or solder, depending on material and application. I also have MIG and TIG at my disposal.
The process of forming chapes (and other scabbard fittings) is not a simple discussion, nor a simple process. The better and more available the proper tools are (and they can change for nearly every different scabbard done), the better your chances for success. It also takes a lot of time and practice to develop the forging skills (forging, bouging, planishing, creasing...) and welding skill, plus the techniques used to add decorative elements such as the cutout window and finial that Dan added to his chape above.
|
|
|
 |
Sean Flynt

|
Posted: Mon 14 Jan, 2008 7:10 am Post subject: |
|
|
Allen:
Here's the chape I made for a dagger scabbard. See this thread for details about the project:
http://www.myArmoury.com/talk/viewtopic.php?t...ght=rondel
I cut a dummy chape from flexible foam sheet (look in the scrapbooking supplies at Hobby Lobby, Michaels, etc.) This stuff is the same thickness as the 16 gauge steel I used for the final product. It's easy to trim the foam to shape and experiment, then use it as a template to cut the steel. I should have used thinner steel, but the good news is that this thickness was very forgiving of my trial-and-error forming. I used a bench vise for the majority of the forming, positioning the steel just-so and carefully tightening the vise, bending the steel the way I wanted. I see that Dan did the same thing, so that's two recommendations for a cheap bench vise. I'd recommend a $30 anvil, too. I used a pair of needle-nose pliers, inserted into the rough chape, as an internal support/mandrel while I hammered the piece lightly on an anvil to refine the form. Then I filed it, ground it, drilled and cut it, sanded and polished it, etc. I screwed up my original plans for the decorative cutout ( a trefoil pattern) because I had the wrong bit size and tried to improvise. To fix the resulting ugliness I just drilled one big hole and cut a "v" shape down to it. I actually like the finished cutout better than my original plan. The chape worked out O.K. in the end, but I'll do it differently next time, using a lighter gauge steel and forming it a bit more gently so I don't have to file out vise marks, etc.
I jokingly wrote at the time that the only way this could have been harder would be if had carved it from a single block of steel. That's an exaggeration, of course, but the point is that this would have been much easier with a lighter gauge steel. There's not welding here--just a tight seam up the back. Fits tight with friction alone, but I added a drop of JB Weld just to be safe.
Attachment: 46.19 KB
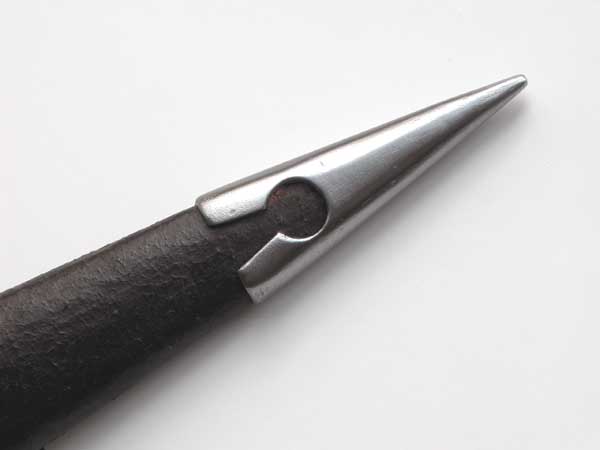
-Sean
Author of the Little Hammer novel
https://www.amazon.com/Little-Hammer-Sean-Flynt/dp/B08XN7HZ82/ref=sr_1_1?dchild=1&keywords=little+hammer+book&qid=1627482034&sr=8-1
|
|
|
 |
Sean Flynt

|
|
|
 |
Dan Dickinson
Industry Professional

|
Posted: Mon 14 Jan, 2008 11:28 am Post subject: |
|
|
I did make the buckles (they took and awfully long time for as small as they are). They should be a fairly simple forge weld (though not with propane). MAPP and oxy-acetelyn would probably work. Alternatively silver-soldering or brazing should to a good job. You could probably leave the ends butted if you use heavy enough material, though I'd worry about the ends interfering with the free movement of the tounge. Personally I used a piece of bar stock that I placed a hole in the center of and expanded outward to its present shape (thus avoiding the need to weld).
Hope this helps,
Dan
|
|
|
 |
Johan S. Moen
Location: Kristiansand, Norway Joined: 26 Jan 2004
Posts: 259
|
Posted: Mon 14 Jan, 2008 12:53 pm Post subject: |
|
|
Sean:
You could also buy some solid steel/brass/etc. plate, and saw/drill/file a buckle from that. It's a tedious process, it wastes a good deal of material, but it works.
Johan Schubert Moen
|
|
|
 |
Sean Flynt

|
Posted: Mon 14 Jan, 2008 12:54 pm Post subject: |
|
|
Dan Dickinson wrote: | Personally I used a piece of bar stock that I placed a hole in the center of and expanded outward to its present shape (thus avoiding the need to weld).
Hope this helps,
Dan |
Oooh! Brilliant solution! So I'll get some narrow flat stock, draw the shape on one end, drill it first then use files/Dremel to expand the hole to shape and finish the outside. Then I sand the piece and cut it from the bar (I figure the cut is the next-to-last task in order to have a more secure work platform/something to clamp in the vise). Finally, I round over the bar at the back of the buckle. Does that sound about right?
Mine will be for a chin strap, so it's not going to get as much stress as a sword belt. I can't wait to try this!
Thanks, guys!
-Sean
Author of the Little Hammer novel
https://www.amazon.com/Little-Hammer-Sean-Flynt/dp/B08XN7HZ82/ref=sr_1_1?dchild=1&keywords=little+hammer+book&qid=1627482034&sr=8-1
|
|
|
 |
|