Posts: 5,981 Location: Birmingham, Alabama
Mon 14 Jan, 2008 7:10 am
Allen:
Here's the chape I made for a dagger scabbard. See this thread for details about the project:
http://www.myArmoury.com/talk/viewtopic.php?t...ght=rondel
I cut a dummy chape from flexible foam sheet (look in the scrapbooking supplies at Hobby Lobby, Michaels, etc.) This stuff is the same thickness as the 16 gauge steel I used for the final product. It's easy to trim the foam to shape and experiment, then use it as a template to cut the steel. I should have used thinner steel, but the good news is that this thickness was very forgiving of my trial-and-error forming. I used a bench vise for the majority of the forming, positioning the steel just-so and carefully tightening the vise, bending the steel the way I wanted. I see that Dan did the same thing, so that's two recommendations for a cheap bench vise. I'd recommend a $30 anvil, too. I used a pair of needle-nose pliers, inserted into the rough chape, as an internal support/mandrel while I hammered the piece lightly on an anvil to refine the form. Then I filed it, ground it, drilled and cut it, sanded and polished it, etc. I screwed up my original plans for the decorative cutout ( a trefoil pattern) because I had the wrong bit size and tried to improvise. To fix the resulting ugliness I just drilled one big hole and cut a "v" shape down to it. I actually like the finished cutout better than my original plan. The chape worked out O.K. in the end, but I'll do it differently next time, using a lighter gauge steel and forming it a bit more gently so I don't have to file out vise marks, etc.
I jokingly wrote at the time that the only way this could have been harder would be if had carved it from a single block of steel. That's an exaggeration, of course, but the point is that this would have been much easier with a lighter gauge steel. There's not welding here--just a tight seam up the back. Fits tight with friction alone, but I added a drop of JB Weld just to be safe.
Attachment: 46.19 KB
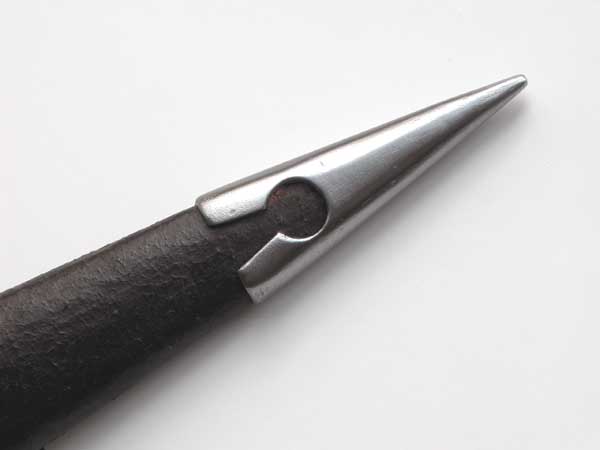