Author |
Message |
Harry Marinakis

|
Posted: Sun 19 Apr, 2015 5:11 am Post subject: |
|
|
For those you who make sheaths for your knives, how do you get the leather to bend around the broken back like this? Seems that if you bend the leather to form the broken back, then you'd get a wrinkle forming on both sides. Is it just a matter of stretching wet leather?
Viktor Abrahamson wrote: | 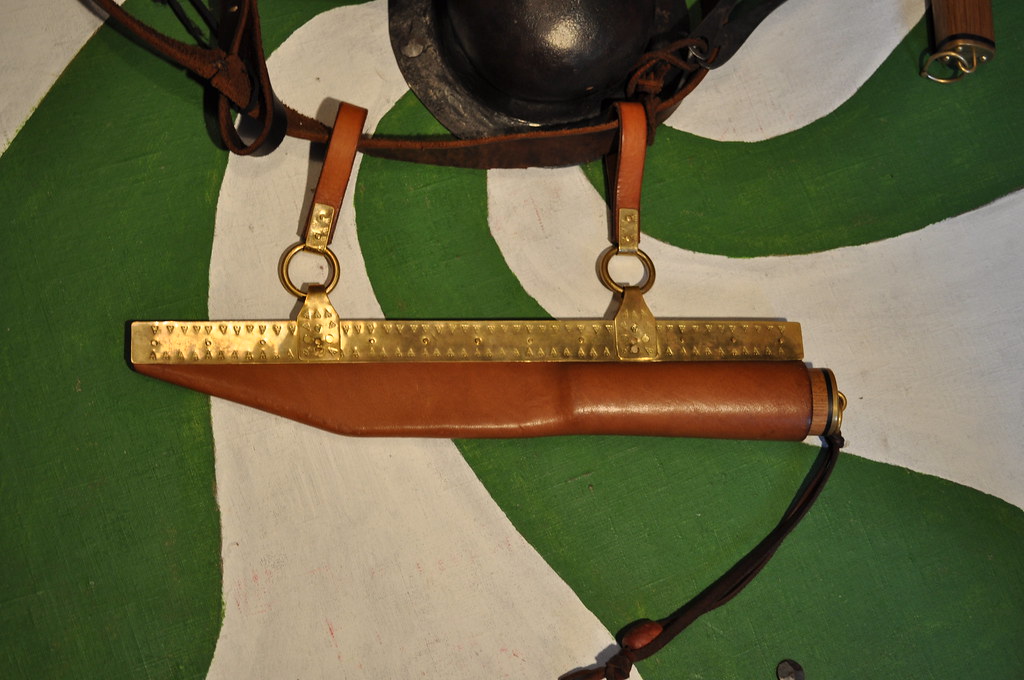 |
|
|
|
 |
G Ezell
Industry Professional

Location: North Alabama Joined: 22 Dec 2003
Posts: 235
|
Posted: Sun 19 Apr, 2015 10:04 am Post subject: |
|
|
Harry Marinakis wrote: | For those you who make sheaths for your knives, how do you get the leather to bend around the broken back like this? Seems that if you bend the leather to form the broken back, then you'd get a wrinkle forming on both sides. Is it just a matter of stretching wet leather?
Viktor Abrahamson wrote: | 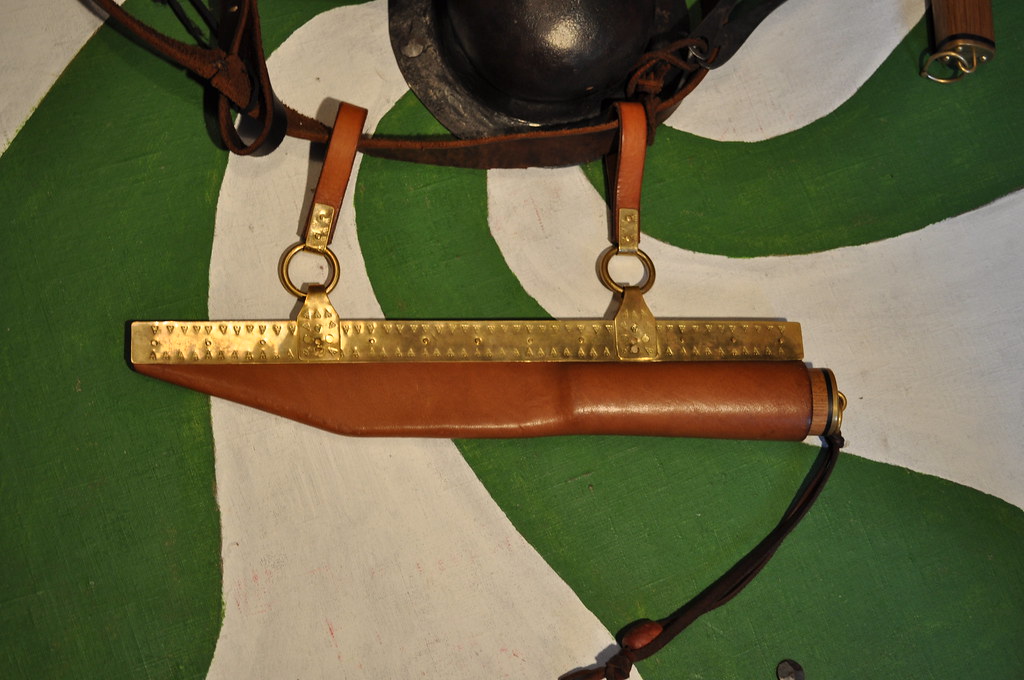 |
|
Yes, the leather along the spine must be stretched, poked, and prodded into submission... Some leathers are more cooperative than others, I've had my best luck with vegetable tanned leathers of no more than 9 oz weight allowed to soak in warm water for a few minutes. Wax the knife thoroughly, then wrap the entire knife in plastic wrap and tape up the seams. Wash your hands well, and trim your nails... Cut a piece of leather slightly larger than you actually need, and mark a center line on the flesh side, and also mark where the 'break' (also known as the hump) will be. I use an orange marker, I've found that most leather stains will completely hide the orange marks. Wet the leather thoroughly from both sides.
I use the corner of a rectangular piece of plexiglass, maybe 1/4 inch thick, to start forming the bend/break: pulling, stretching, and bending the leather over the corner until it conforms the the shape of the back of the blade, using the center line and marks for reference. Wrap the leather around the knife, shaping it as you go so that it fits the shape of the knife perfectly, then clamp the leather covered blade between two flat clean surfaces to allow it to dry overnight. Again, I use plexiglass, as it has nicely beveled edges that do not mark the leather, but a material that allows air to pass through, maybe a porous material, might actually work better. The next day remove the clamps and the leather is ready to be trimmed closer to its final shape, the metal fittings fabricated, and the tooling/embossing can begin. It is advantageous to have the metal fittings fabricated before tooling the leather and trimming it to its final shape as it is easier to fit the tooling to the fittings than the fittings to the tooling (it took me awhile to figure that one out)... the sheath needs to be snug to the knife but not so tight that it is impossible to remove the knife from the sheath, particularly if only an inch or two of the handle is sticking out....
" I have found that it is very often the case that if you state some absolute rule of history, there will be an example, however extremely unusual, to break it."
Gabriel Lebec
https://www.facebook.com/relicforge
|
|
|
 |
Harry Marinakis

|
Posted: Sun 19 Apr, 2015 10:45 am Post subject: |
|
|
Thanks George
|
|
|
 |
Harry Marinakis

|
Posted: Fri 27 May, 2016 5:40 pm Post subject: |
|
|
I bought an 12-inch seax from Łukasz Szczepański (from Sweden), and put a handle on it today.
Bronze bolster
Swedish Masur birch & walnut handle
Attachment: 101.46 KB
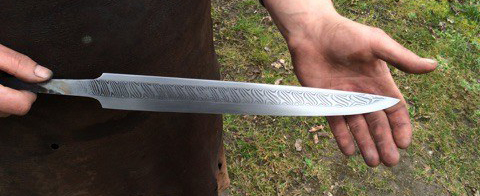
Attachment: 96.77 KB
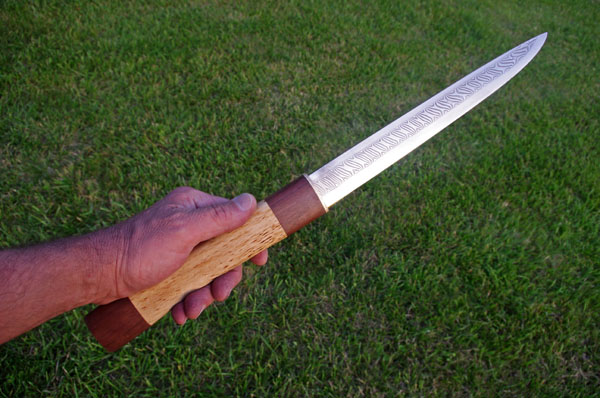
Attachment: 48.26 KB
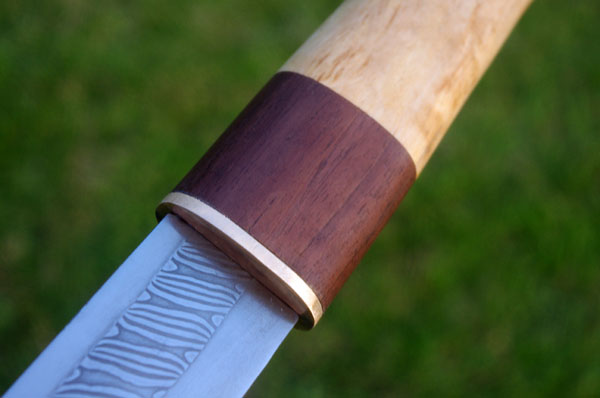
Attachment: 81.33 KB
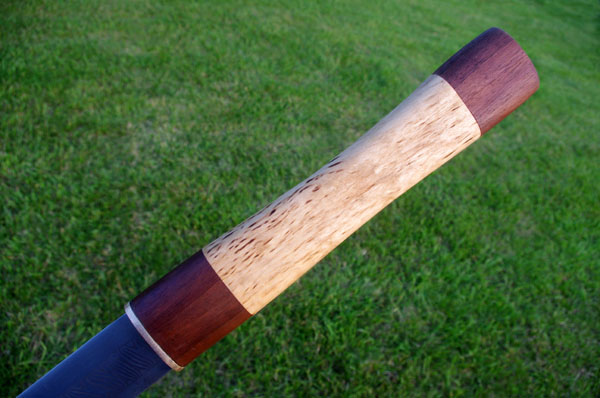
|
|
|
 |
Harry Marinakis

|
Posted: Thu 07 Jul, 2016 1:17 pm Post subject: |
|
|
Finished the sheath for the above seax
7-9 oz. veg tan leather (tooled)
30 gauge bronze sheet (stamped)
Overall 22 inches long
First attempt at something like this, definitely munitions grade work
Attachment: 84.12 KB
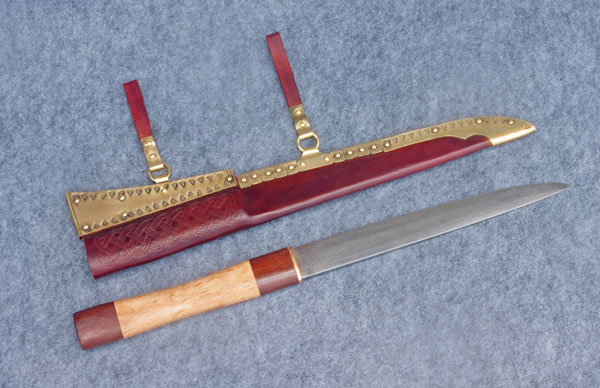
Attachment: 87.24 KB

Last edited by Harry Marinakis on Thu 07 Jul, 2016 2:29 pm; edited 1 time in total
|
|
|
 |
Leo Todeschini
Industry Professional

|
|
|
 |
Harry Marinakis

|
Posted: Thu 07 Jul, 2016 2:26 pm Post subject: |
|
|
Thanks Tod, but it's definitely quite rough. Your job is safe!
|
|
|
 |
Harry Marinakis

|
Posted: Mon 04 Mar, 2019 11:48 am Post subject: |
|
|
A friend gave me his commericial mass-produced "seax" and asked me to make a sheath for him.
Not my best work. Oh, well.
Attachment: 78.39 KB

Attachment: 77.62 KB
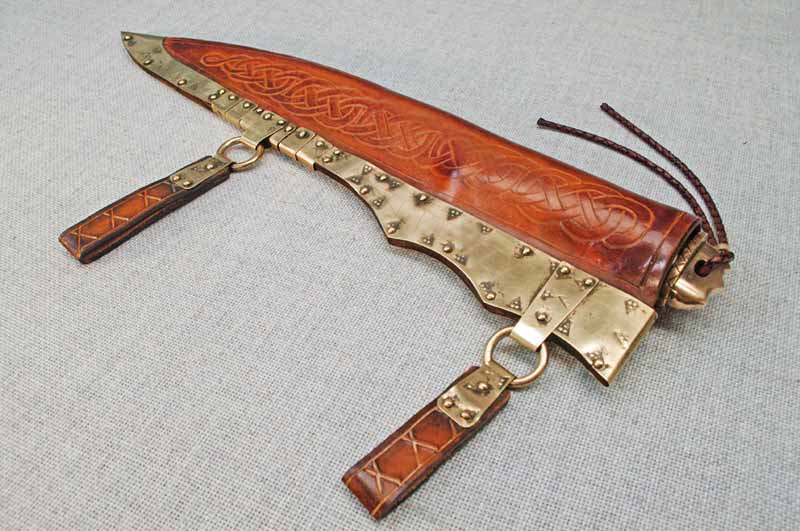
Attachment: 84.21 KB
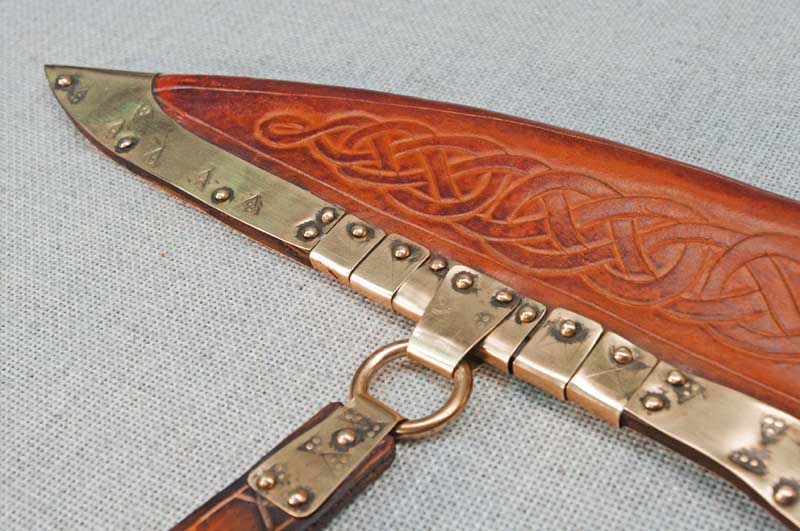
Firesteel Designs
Hand-crafted good lovingly infused with hemoglobin
|
|
|
 |
Mark Moore
|
Posted: Wed 06 Mar, 2019 1:07 pm Post subject: |
|
|
For 'not your best work'...that looks spot-on fantastic. Great job! ............McM
''Life is like a box of chocolates...'' --- F. Gump
|
|
|
 |
Tim Seaton
Location: San Jose calif Joined: 30 Jul 2005
Posts: 101
|
Posted: Sun 10 Mar, 2019 9:10 pm Post subject: Seaxes |
|
|
Sunday night Seax Porn
cheers
Attachment: 76.96 KB
[ Download ]
|
|
|
 |
Mark Moore
|
Posted: Mon 11 Mar, 2019 1:27 pm Post subject: |
|
|
Those are all very nice, but I like the middle one a lot....."Mr. Grumpy Face". ............McM
''Life is like a box of chocolates...'' --- F. Gump
|
|
|
 |
Scott Kowalski
Location: Oak Lawn, IL USA Joined: 24 Nov 2006
Posts: 818
|
Posted: Mon 11 Mar, 2019 6:44 pm Post subject: |
|
|
I agree with Mark on which is my favorite. Who is the maker of the middle one good sir?
Chris Landwehr 10/10/49-1/1/09 My Mom
|
|
|
 |
Chad Arnow
myArmoury Team


|
Posted: Mon 15 Jul, 2019 9:28 am Post subject: |
|
|
Just picked this one up. It's made by Thorkil and has a pattern welded blade.
Attachment: 43.36 KB

ChadA
http://chadarnow.com/
|
|
|
 |
Jeremy V. Krause
|
Posted: Tue 16 Jul, 2019 8:24 am Post subject: |
|
|
Very nice and simple Chad!
The pattern is nice and subtle- not overdone as we sometimes see.
What is the handle- looks a bit like bog oak.
Do you have a date on which this piece is based?
|
|
|
 |
Chad Arnow
myArmoury Team


|
Posted: Tue 16 Jul, 2019 8:31 am Post subject: |
|
|
Jeremy V. Krause wrote: | Very nice and simple Chad!
The pattern is nice and subtle- not overdone as we sometimes see.
What is the handle- looks a bit like bog oak.
Do you have a date on which this piece is based? |
Thanks! It was an in stock piece purchased via Etsy of all places. The handle is listed as "black oak." I don't have an exact date. The sheath brass work is supposed to be based on finds from Birka in Sweden.
ChadA
http://chadarnow.com/
|
|
|
 |
Harry Marinakis

|
Posted: Thu 05 Dec, 2019 1:51 pm Post subject: |
|
|
This is a small Latvian brooch seax that I just made for my wife.
I forged the knife from O-1 tool steel. The blade is just over 3 inches long (8 cm).
Handle is Swedish Masur Birch and bone. Bolster is bronze.
I made the sheath from veg tan leather, 24 gauge sheet brass, and rivets made from 10 gauge brass wire.
I made the rings from 10 gauge brass wire, and the chain from 12 gauge brass wire.
Attachment: 86.18 KB

Attachment: 70.76 KB
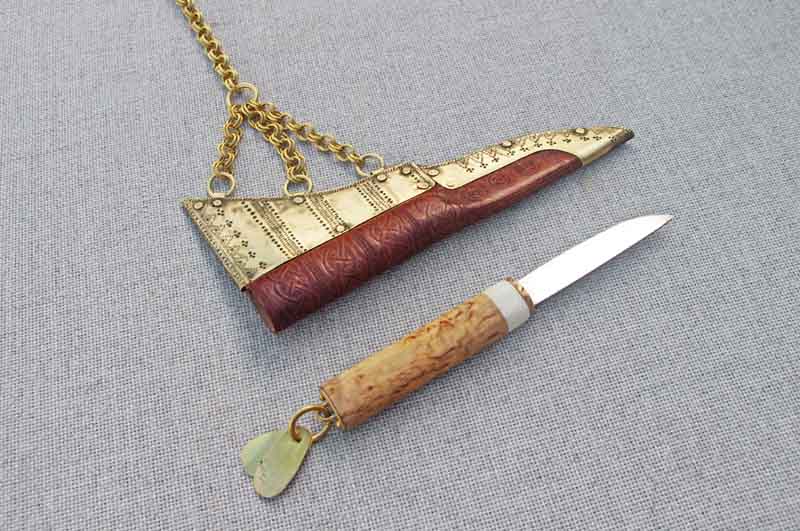
Attachment: 88.1 KB
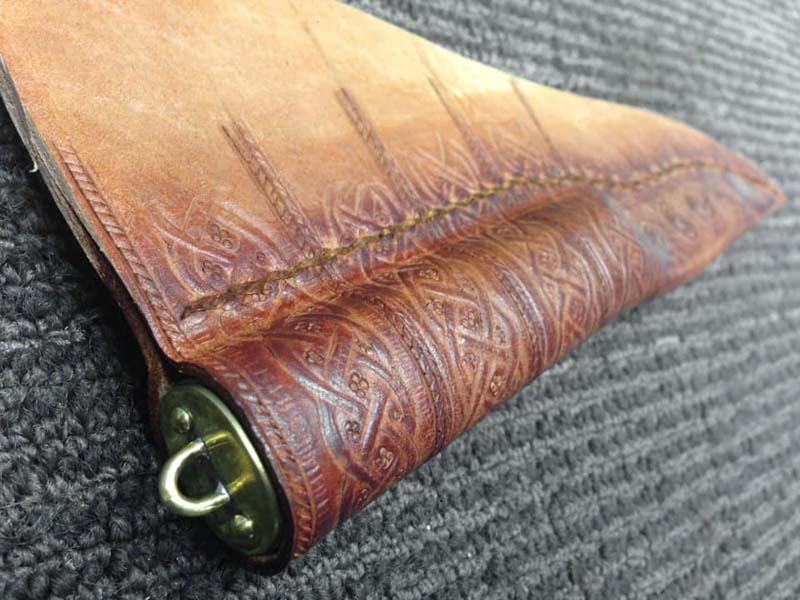
|
|
|
 |
Jeremy V. Krause
|
Posted: Wed 19 Feb, 2020 9:46 am Post subject: |
|
|
Hello everyone,
I don't believe I ever posted photos of my the seaxes in my collection.
Anyway here they are. Both made by Leo Todeschini of Tod's Stuff and Owen Bush. One is a replica of the Seax of Beagnoth and the other is a seax modeled after the Honey Lane example.
|
|
|
 |
Tyler C.
|
Posted: Thu 20 Feb, 2020 9:00 am Post subject: |
|
|
Jeremy V. Krause wrote: | Hello everyone,
I don't believe I ever posted photos of my the seaxes in my collection.
Anyway here they are. Both made by Leo Todeschini of Tod's Stuff and Owen Bush. One is a replica of the Seax of Beagnoth and the other is a seax modeled after the Honey Lane example. |
These are absolutely stunning! Thanks for posting.
|
|
|
 |
|