Author |
Message |
Tim Jones
Location: United Kingdom Joined: 05 Nov 2013
Posts: 37
|
Posted: Sat 21 Feb, 2015 12:36 pm Post subject: Authentic armour finishes |
|
|
Hello all,
I'm an occasional armour maker, and have found it very difficult to get nice finishes to my pieces (it's probably due to the fact that I'm terrible at planishing) and was wondering if anyone had some examples of historical finishes. To be more specific, the low to mid-end armour in a late 14th century to mid 15th century context.
Thanks
|
|
|
 |
Jonathan Fletcher

|
|
|
 |
Tyler Jordan
|
Posted: Sat 21 Feb, 2015 6:45 pm Post subject: |
|
|
Armor was expensive, but a good polish on armor could be several times the expense of the harness itself. Needless to say your bright mirror polish would be quite a conspicuous declaration of wealth. So low-mid end armor, though not raw, would probably have a pretty simple working polish. There's a lot of evidence that many armor pieces were originally painted as well.
|
|
|
 |
Tim Jones
Location: United Kingdom Joined: 05 Nov 2013
Posts: 37
|
Posted: Sun 22 Feb, 2015 3:28 am Post subject: |
|
|
It is as I feared. The matter is not helped by museum staff in the Victorian period cleaning original surfaces off because it didn't "look medieval enough".
I really like the finishes put on by Albert Collins and Radoslaw Ciszewski. They're done by hand and give a far more likely portrayal of the armour of an ordinary soldier. I've been trying to recreate the finish, albeit with an angle grinder and polishing mop....
I believe the main cause of my problems comes down to my planishing skill. It's far easier to polish something up if you've got a smooth surface to deal with. I think I'm going to have to go and buy some more tools...
|
|
|
 |
Tim Jones
Location: United Kingdom Joined: 05 Nov 2013
Posts: 37
|
Posted: Sun 22 Feb, 2015 6:54 am Post subject: |
|
|
I've done some experimenting. The one on the right was finished about two weeks before the one on the left, and at a time when I was trying to get a mirror finish. The one on the left is a more "munitions grade" piece.
Attachment: 246.91 KB
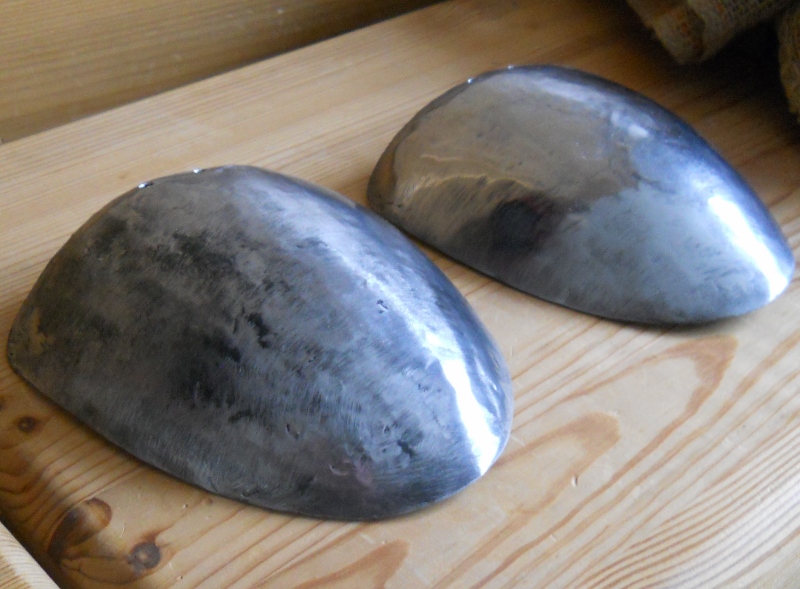
|
|
|
 |
Jeffrey Faulk
|
Posted: Sun 22 Feb, 2015 10:09 am Post subject: |
|
|
It was also common, especially in earlier periods-- not sure about later on-- to cover armour with fabric or leather. You could do this in various ways such as bunching or slashing the material to form various patterns. Velvet (or a modern synthetic alternative might be more durable) was a common choice, I believe.
|
|
|
 |
Adam Bodorics
Industry Professional
|
Posted: Sun 22 Feb, 2015 12:03 pm Post subject: |
|
|
Try working from the inside on an anvil, makes planishing redundant. You'll end up with a surface very similar to the originals in Landeszeughaus Graz (which is later than what you asked, but I think the method was the same at your specified date), which is neat in itself but is also pretty easy to polish if you're into that.
|
|
|
 |
Tim Jones
Location: United Kingdom Joined: 05 Nov 2013
Posts: 37
|
Posted: Sun 22 Feb, 2015 12:55 pm Post subject: |
|
|
That's the method I've already tried. I've found that it leaves a fairly nasty surface that has to be ground or planished, but that might just be me.
|
|
|
 |
James Arlen Gillaspie
Industry Professional

Location: upstate NY Joined: 10 Nov 2005
Posts: 587
|
Posted: Sun 22 Feb, 2015 7:07 pm Post subject: |
|
|
Water powered grinding and finishing wheels were often used on production armour, especially during the time of the popularity of the 'alwhite' style. There are a few pieces that show working -life finishes, but they are, as you might expect, very rare. I came across a helmet in my own work that shows some areas more or less protected by the decorative liner washer rivets. I'll post one or two when I figure out what folder they're in. It's second half of the 16th c., but it looks about the same as a late 15th c. Italian celata I saw in Munich years ago that had an intact finish under its brow reinforce.
jamesarlen.com
|
|
|
 |
Mark Griffin
Location: The Welsh Marches, in the hills above Newtown, Powys. Joined: 28 Dec 2006
Posts: 802
|
Posted: Mon 23 Feb, 2015 9:40 am Post subject: |
|
|
Quote: | t was also common, especially in earlier periods-- not sure about later on-- to cover armour with fabric or leather. You could do this in various ways such as bunching or slashing the material to form various patterns. Velvet (or a modern synthetic alternative might be more durable) was a common choice, I believe. |
But also legislated against to avoid shoddy work being hidden under expensive coverings. The basic rule. inspect the armour before it gets covered in velvet etc.
Tom, where in UK are you? I have a range of armour here made by different makers as well as original pieces. happy to help if I can.
But the bottom line is, what does the client want?
Currently working on projects ranging from Elizabethan pageants to a WW1 Tank, Victorian fairgrounds 1066 events and more. Oh and we joust loads!.. We run over 250 events for English Heritage each year plus many others for Historic Royal Palaces, Historic Scotland, the National Trust and more. If you live in the UK and are interested in working for us just drop us a line with a cv.
|
|
|
 |
Tim Jones
Location: United Kingdom Joined: 05 Nov 2013
Posts: 37
|
Posted: Mon 23 Feb, 2015 10:13 am Post subject: |
|
|
Quote: | But also legislated against to avoid shoddy work being hidden under expensive coverings. The basic rule. inspect the armour before it gets covered in velvet etc.
Tom, where in UK are you? I have a range of armour here made by different makers as well as original pieces. happy to help if I can.
But the bottom line is, what does the client want? |
I'm in Birmingham. I've managed to re-create Radoslaw Ciszewski's hand-finished style using an angle grinder and polishing mop, but I think I could do with getting the shapes nailed first.
It's not for any particular client, more my wish to get it "right".[/quote]
|
|
|
 |
Mark Griffin
Location: The Welsh Marches, in the hills above Newtown, Powys. Joined: 28 Dec 2006
Posts: 802
|
Posted: Mon 23 Feb, 2015 10:59 am Post subject: |
|
|
Not too far from me and i pop into Brum from time to time. You are also very close to Matt Finchen who is pretty hot on surfaces. He's hand filing a Mantua B1 for me sometime soon.
Basically there is no 'right' finish, although plenty wrong. Saw one completely Hammerited once... You can have everything from very rough from the forge to mirror bright and perfectly smooth. You'd need that before you went on to most other decorative stages. No point trying to blue something that's not absolutely perfect to start off with.
Currently working on projects ranging from Elizabethan pageants to a WW1 Tank, Victorian fairgrounds 1066 events and more. Oh and we joust loads!.. We run over 250 events for English Heritage each year plus many others for Historic Royal Palaces, Historic Scotland, the National Trust and more. If you live in the UK and are interested in working for us just drop us a line with a cv.
|
|
|
 |
James Arlen Gillaspie
Industry Professional

Location: upstate NY Joined: 10 Nov 2005
Posts: 587
|
Posted: Mon 23 Feb, 2015 11:03 am Post subject: |
|
|
Found it! Note the fact that the mirror polish is slapped on top of a rather coarse finish. Actual size of the polished area is about 3/4 inch.
Attachment: 96.16 KB
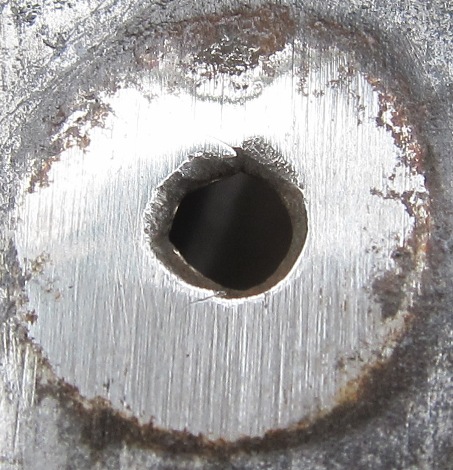
jamesarlen.com
|
|
|
 |
Tim Jones
Location: United Kingdom Joined: 05 Nov 2013
Posts: 37
|
Posted: Mon 23 Feb, 2015 12:23 pm Post subject: |
|
|
Mark Griffin wrote: | Not too far from me and i pop into Brum from time to time. You are also very close to Matt Finchen who is pretty hot on surfaces. He's hand filing a Mantua B1 for me sometime soon.
Basically there is no 'right' finish, although plenty wrong. Saw one completely Hammerited once... You can have everything from very rough from the forge to mirror bright and perfectly smooth. You'd need that before you went on to most other decorative stages. No point trying to blue something that's not absolutely perfect to start off with. |
I've found it to be quite a useful base...
I think I'll probably have to have a browse through some websites and see what kind of thing I want to do, or god forbid, just do it and see what happens.....
Quote: | Found it! Note the fact that the mirror polish is slapped on top of a rather coarse finish. Actual size of the polished area is about 3/4 inch |
That's the kind of thing Radoslaw Ciszkewski does. It looks really nice when it's almost highlighted by the polishing compound or general forge crud.
|
|
|
 |
Willy M
Location: Kingston Joined: 03 Jul 2011
Posts: 13
|
Posted: Wed 25 Feb, 2015 6:04 pm Post subject: |
|
|
The finish James shows is good at hiding slight imperfections and can still be quite shiny. Without that texture every imperfection even in the polishing itself is revealed.
Best and quickest way to polish I found is with a Baldor or similar buffer. The shafts are long and thick and the motor is vibration free so it does not transfer marks to your work. The 555 polish will give the highest polish you will ever need.
Use only one wheel for one size of grit polish then use soft or[img] hard felt wheels to finish.
With the buffer wheels free of guards and well out from the motor you should be able to reach any part of an object.
Works well on sword blades.
Of course this set up is not cheap, over $500 for a buffer and felt wheels run $80 or more and then add your polishing compounds.
Attachment: 316.62 KB
[ Download ]
Attachment: 359.58 KB
[ Download ]
|
|
|
 |
Mart Shearer
|
|
|
 |
|