Author |
Message |
Michael Pikula
Industry Professional
|
Posted: Mon 15 Jun, 2009 1:28 pm Post subject: Early Partizan Spear project for Jean Thibodeau |
|
|
Last month Jean had gotten in touch with me about commissioning an early Partizan spear and we have been going back and forth about the details of the project. Since I have never forged a spear of this nature before I had to work through or figure out the sequence of steps that I would be going through to create this piece. After multiple attempts on some mild steel stock I worked out the most probable way of going about forging this spear and I wanted to show some progress shots of what is going on and how I go about my work. But first here are some basic ideas of what is going to be included in this piece.
- The spear is the have the profile of a drawing the Jean sent to me and is attached below, the midrib is to stand out and the spear should be suitable of a cutting attack as well a thrust.
- The lugs are to be more as part of, or and extension of the blade and not separate pieces, they should be capable of being used as an offensive feature, or a defensive feature.
- The spear will be mounted on a shaft with languetts
I was hoping to use L6 since I am familiar with the steel and heat treat but there was no way for me to achieve the width and thickness that I needed with the stock that I have and ordering a full sized bar of L6 big enough for this project would have ended up costing me more then what the spear costs so I decided to use W2 instead which will still deliver an excellent product. I started out with a 2 1/8" round piece that was 5" long and started working in my shape as you can see in the attached pictures. I realize that what you currently see looks a little rough and off, but after I pull the other lug and rough shape my socket I will proceed to hand forge the spear to the final shape and everything will "click."
Jean, please feel free to add your thoughts and comments. If there are any questions you can feel free to ask and I will do my best to answer them. I will add updates as they occur and the details that are involved in each stage. Right now I am just roughing everything in and getting my general shape and form in so I don't have a whole lot to get into.
Attachment: 90.05 KB
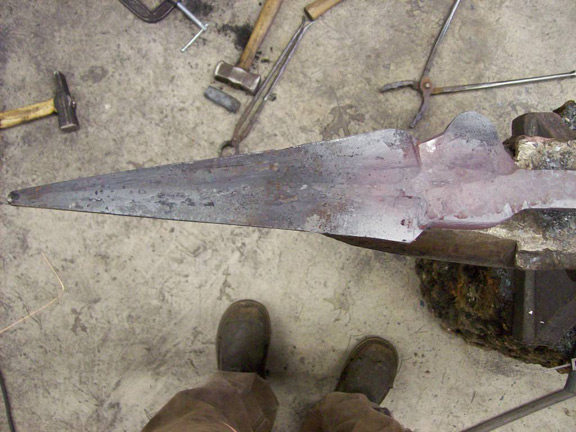
Attachment: 89.67 KB
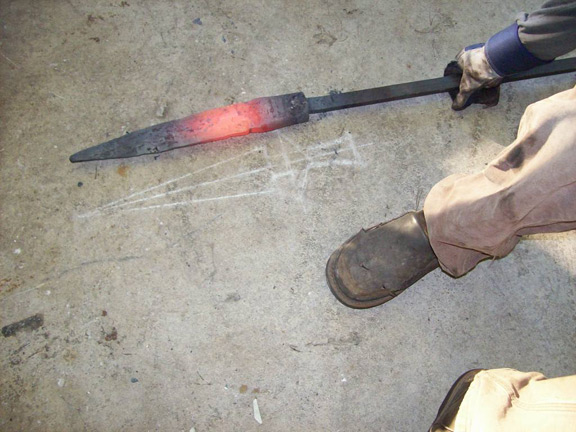
Attachment: 93.05 KB
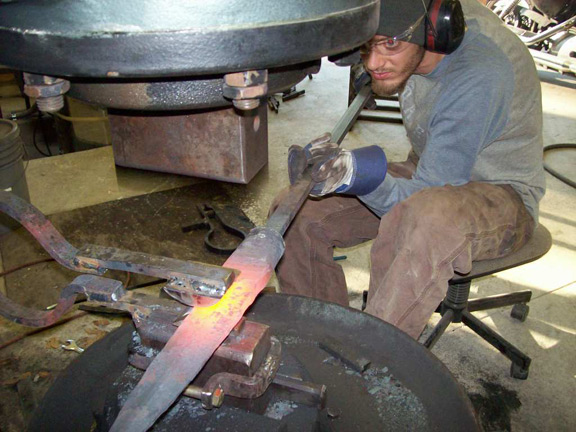
Attachment: 98.7 KB
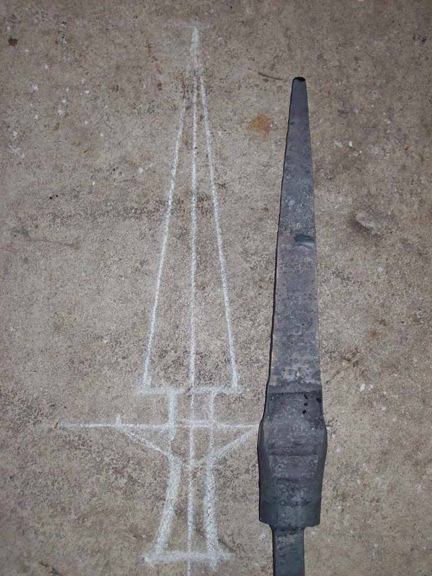
Attachment: 86.29 KB
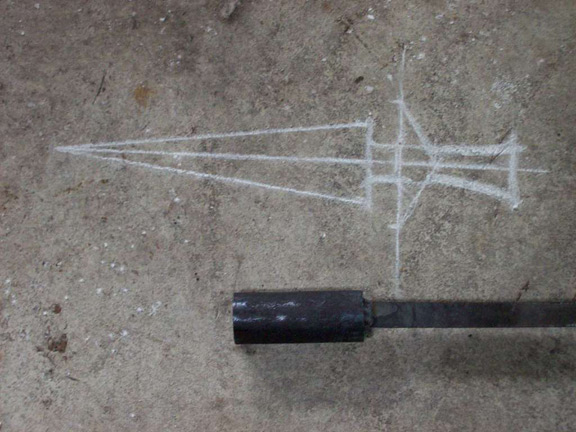
Attachment: 28.47 KB
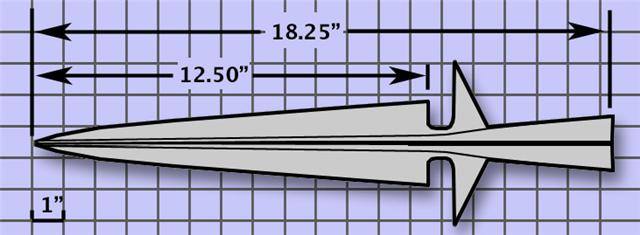
|
|
|
 |
Tim Lison
|
Posted: Mon 15 Jun, 2009 1:31 pm Post subject: |
|
|
Interesting! Can't wait to see some more in progress shots. It looks like it'll be a beauty!
|
|
|
 |
Scott Kowalski
|
Posted: Mon 15 Jun, 2009 2:05 pm Post subject: |
|
|
Very nice looking indeed Michael. I cannot wait to see this project finished. How long will the shaft be?
Scott
Chris Landwehr 10/10/49-1/1/09 My Mom
|
|
|
 |
Jean Thibodeau

|
Posted: Mon 15 Jun, 2009 6:42 pm Post subject: Re: Early Partizan Spear project for Jean Thibodeau, in prog |
|
|
Michael Pikula wrote: |
- The spear is the have the profile of a drawing the Jean sent to me and is attached below, the midrib is to stand out and the spear should be suitable of a cutting attack as well a thrust.
- The lugs are to be more as part of, or and extension of the blade and not separate pieces, they should be capable of being used as an offensive feature, or a defensive feature.
- The spear will be mounted on a shaft with languetts
Jean, please feel free to add your thoughts and comments. If there are any questions you can feel free to ask and I will do my best to answer them. I will add updates as they occur and the details that are involved in each stage. Right now I am just roughing everything in and getting my general shape and form in so I don't have a whole lot to get into. |
I edited Michael's post quote down to what I think is a very essential thing when a maker gets a commission and that is that his recap of what the spear should look like is dead on perfect.
We had a nice talk on the phone to be sure we where on the same page about design issues and his approach to things like the way the languettes will be inletted into 4 sides of the octagonal shaft, not welded to the head itself but will go inside the socket for a bit under a relief cut ( Hope I'm explaining this right using the right word ). They will stand out half way proud and have the corners rounded or broken for aesthetic and design reasons. ( Just an example about a small part of our design discussions ).
Now these details may evolve or change during the making if they need to, but the point above is that his way of thinking about how things should be put together is a very good match with what I like as logical design optimizing form and function: I like there to be a reason for a lot of what are subtle design decisions and the nice thing is that Michael's suggestions where exactly what I would do if I was making it and had the skills to do it myself.
What this conversation convinced me is that I can leave almost all of the details up to Michael as we seem to think alike.
I also believe that Michael has the ability to actively listen to what the client has asked for and he also was very clear in his questions to clear up anything that was unclear to him or to confirm that we where actually on the same page.
Also, seeing the work he did on another winged spear I am even more enthused about having asked him to work on this project.
Oh, well, my usual longwinded post. But a lot of the success of a commission, or any cooperative project, depends on good and clear communication and I am definitely very happy with the quality of the communication. As well, the conversation was a fun part of the process.
You can easily give up your freedom. You have to fight hard to get it back!
Last edited by Jean Thibodeau on Mon 15 Jun, 2009 6:57 pm; edited 1 time in total
|
|
|
 |
Jean Thibodeau

|
Posted: Mon 15 Jun, 2009 6:54 pm Post subject: |
|
|
Scott Kowalski wrote: | Very nice looking indeed Michael. I cannot wait to see this project finished. How long will the shaft be?
Scott |
If I remember correctly the shaft should be around 5.5" to 6' and with the head we are looking at around a total length of 7' to 7.5". ( Michael, if I have these numbers a little off go with my original specifications I'm just giving these off the top of my head ).
The idea is for a very stout shaft and a moderately short spear for a few of reasons:
1) It's supposed to me a manageable size for close fighting.
2) These " Épieu de Guerre " are military equivalents to a hunting boar spear and are related to winged spears or early partisans and I think tended towards the stout rather than the long.
3) The practical reason is that very long spears/pikes are a pain indoors unless one has very VERY high ceilings.
You can easily give up your freedom. You have to fight hard to get it back!
|
|
|
 |
Matthew G.M. Korenkiewicz

|
Posted: Mon 15 Jun, 2009 8:28 pm Post subject: |
|
|
A very interesting project that I will certainly be checking in on ...
One of the things I like to see is the maker / smith actively involved in discussing
the work as well as being able to photograph progress shots of the work being
done.
To me there always seems to be a discussion about whether one wants the maker /
smith more involved IN his / her shop AT work, as opposed to spending time online
answering questions, replying to comments, or fielding criticism. I'm always interested
as to whether a result mirrors motivation, self-discipline, and curiosity -- kinda ideally
hoping a person commissioning a project and the maker / smith he chooses for said
project come to some sort of shared / mutual revelation ... if you follow me.
|
|
|
 |
Michael Pikula
Industry Professional
|
Posted: Tue 16 Jun, 2009 8:53 am Post subject: |
|
|
I was really hoping to keep this thread on track with Jean’s project but I think that you bring up an interesting question that I would like to briefly touch on while the forge gets up to temp. I think Jean hit upon the most important factor of the maker customer relationship which is in fact good communication and an understanding of what the customers expectations are and doing your best to apply your skills and talents to exceed those expectations. Spending time online answering questions either privately or publicly is required to have that clear line of communication that keeps everyone happy. Being a one man show and literally living in shop means that I have to find a way to structure my day and manage my time so that I have a productive day in the shop but also do what is needed to have jobs coming into the shop or making my work available to those who might be interested in purchasing or commissioning it.
I’m still trying to work out the best way of going about this and I hope that spending time in forums such as this one and opening threads is a step in the right direction. If I spent all my time only at the forge and grinder I might be able to make the most knock your helm off stunning sword, but if I don’t spend the time to show and talk about that sword then the work will never be seen or known and the shop doors will be closed.
In simple terms I think a balance of both is needed, but if you have clear and consistent communication and do your best work then I think/hope that it will be a step in the right direction.
All that aside, today I’ll be pulling the second lug out and forming the blade and lugs into close to their final shape. When I do my hand forging I use water on the surface of the anvil and the hammer which creates a steam explosion that removes some of the scale and pitting that may have been forged into the surface when using the power hammer. I’m also planning on grinding in the profile between the bottom of the blade and top of the lugs to make sure I have the material and spacing that I need, and then true up the socket and let it cool slowly over night in some ceramic fiber so that I can drill my pilot hole for the socket. Depending on what time I get done I might not have time to get the pictures formatted for the thread tonight, but I will post them tomorrow at the latest.
|
|
|
 |
Michael Pikula
Industry Professional
|
Posted: Wed 17 Jun, 2009 9:18 am Post subject: |
|
|
And for another update, I got my measurements a bit off and ended up forging the base of the spear out more then I should have, so I ended up grinding in the profile as per Jean’s drawing. The transition between the tip and rest of the blade is touch narrow so I will end up forging that out a bit. One of the lugs ended up forging out nicer then the other, but after grinding in the profile things cleaned up fairly well. The overall shape is about 80% there, I want to get the socket done before I get everything set since the forging of the socket is the most complex and time consuming part.
Also I had some revelations as I was working yesterday. When I built my forge I wasn’t anticipating having to heat an object wider then about 3.5 inches. From tip to tip the lugs are 5 inches so I ran into a problem there. I took the blower off my gas forge and hooked up the coal forge, but since I don’t have any coal (lack of a decent supplier) I ran out to the store and picked up some hardwood charcoal (which they only had one bag of) and got to play the old fashion way. The whole process slowed down since I had to do slow heats so as not to burn the tips of the lugs which are thin, while getting the section up to heat that I needed to forge (much thicker)
And thinking ahead my heat treating set up uses 4” tubes for the salt bath, the lugs have to be heat treated as well and the spear won’t fit inside my gas forge. I don’t think that using my coal forge is a good idea so I am going to have to muster up another plan, I might end up using my smelting furnace as either a large forge, or purchase a short wide stainless tube and use the smelting furnace as a temporary salt rig. I still have some time since there will be grinding that needs to get done, but thought I would put it out there as an example of how you have to be flexible and come up to solution to problems that were not anticipated.
Attachment: 91.76 KB
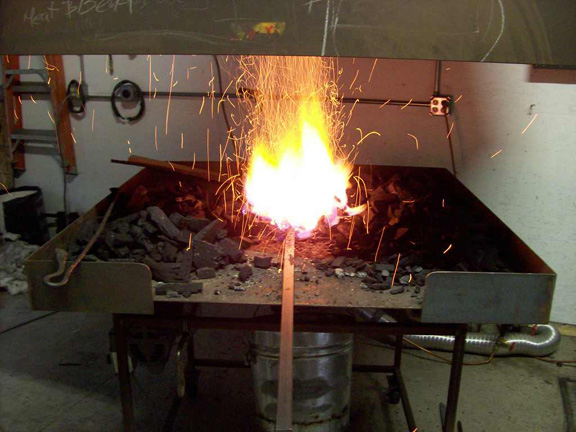
Attachment: 89.48 KB
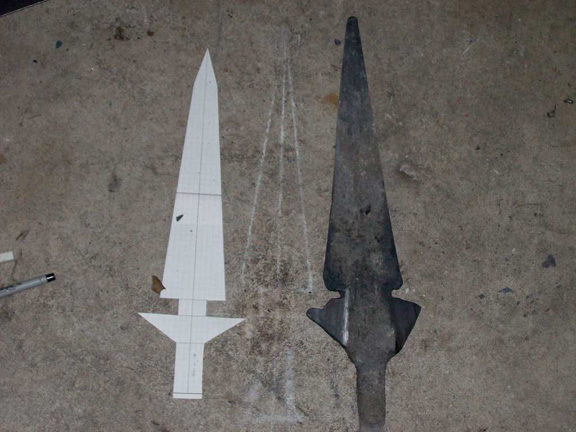
Attachment: 78.8 KB
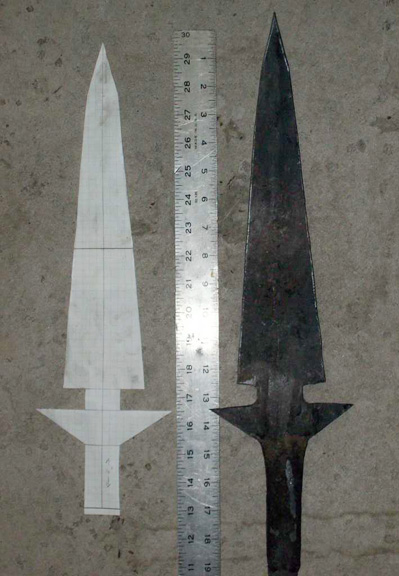
|
|
|
 |
Jean Thibodeau

|
Posted: Wed 17 Jun, 2009 10:29 pm Post subject: |
|
|
Seems to be getting there but I'm glad I'm not the one having to figure out how to get from A to B or from A to OOOOPs back to B, if you can understand what I mean.
The shape seems to be right and it seem like the lugs match up closer in the last pic and the point profile is more like my drawing and getting closer to it.
My designs always seem to have these little issues that make thing more difficult than they initially seem on paper or computer screen.
On the glass half full side it does mean that if you have to make a spear with this width again you will be experienced figuring out the work arounds.
Does seem like a lot of work and sweat from the forge ( heat ) and from the problem solving: Impressive and scary seeing how difficult this could be if one didn't have a good idea where to pound and push/pull/grind the steel into the wanted shape.
You can easily give up your freedom. You have to fight hard to get it back!
|
|
|
 |
Michael Pikula
Industry Professional
|
Posted: Tue 07 Jul, 2009 5:43 pm Post subject: |
|
|
So it has been a while since I posted any updates so I thought I would do a little updating.
For the heat treat I have decided to handle it in three different steps, first I will heat treat the blade in the salts and then use the torch to heat treat the lugs, since there will be enough material to have the lugs hold up to use I think the most important factor is to get the point and edge hard. These will all be done in one sitting and then tempered at the same time.
For actual progress, I drilled and drifted the socket, I still have to forge the final drift to get the socket shaped just right, that is lined up for tomorrow. Since we are going to be using an 8 sided haft the socket will be forged with 8 sides instead of 4, I think the design would call for the ridge to line up with the spine of the spear so I will be going about it that way instead of having a transition to a flat. Jean, if you would like this the other way around please let me know
Tonight I am going to start grinding the scale off and start doing some really basic grind work. I would like to see that the lugs and blade all line up and are straight and I have what I need to have a clean end product.
My camera died tonight so I don't know how many pictures I will be able to offer of progress shots but I will try to sucker a friend into coming out and snapping a few for me when they have time.
|
|
|
 |
Jean Thibodeau

|
Posted: Tue 07 Jul, 2009 10:59 pm Post subject: |
|
|
Michael Pikula wrote: | Since we are going to be using an 8 sided haft the socket will be forged with 8 sides instead of 4, I think the design would call for the ridge to line up with the spine of the spear so I will be going about it that way instead of having a transition to a flat. Jean, if you would like this the other way around please let me know
|
" the design would call for the ridge to line up with the spine of the spear " Yes that would be my preference.
You can easily give up your freedom. You have to fight hard to get it back!
|
|
|
 |
Matthew Stagmer
Industry Professional
|
Posted: Fri 10 Jul, 2009 7:11 am Post subject: |
|
|
Your work is inspiring Michael. Keep it up!
Matthew Stagmer
Maker of custom and production weaponry
Youtube.com/ThatWorks
|
|
|
 |
Michael Pikula
Industry Professional
|
Posted: Fri 17 Jul, 2009 10:15 am Post subject: |
|
|
I did a heat treat yesterday and of course I ran into a problem which renders my salt tubes useless for the spear. The level of the salt changes depending on the temperature and if I filled up the tube with salt to 3/4" from the top for the 1450 degrees that I need it would over flow when I up the temperature to 1600-1525 that I normally use. Due to the nature of salts and the dangers of a liquid at that temperature taking some salt out is not an option. I'm going to have to go back to the drawing board and figure out the best way to get this heat treated properly.
I'm sorry for the delay Jean, I want to get this done right for you above all else.
|
|
|
 |
Jean Thibodeau

|
Posted: Fri 17 Jul, 2009 7:20 pm Post subject: |
|
|
Michael Pikula wrote: | I did a heat treat yesterday and of course I ran into a problem which renders my salt tubes useless for the spear. The level of the salt changes depending on the temperature and if I filled up the tube with salt to 3/4" from the top for the 1450 degrees that I need it would over flow when I up the temperature to 1600-1525 that I normally use. Due to the nature of salts and the dangers of a liquid at that temperature taking some salt out is not an option. I'm going to have to go back to the drawing board and figure out the best way to get this heat treated properly.
I'm sorry for the delay Jean, I want to get this done right for you above all else. |
No worries about how fast you are going: This is plenty fast for most all custom projects and you are keeping us ( ME ) informed which is something not all makers are very good at.
Much better to take your time rather than rush things and have to start over from scratch.
You can easily give up your freedom. You have to fight hard to get it back!
|
|
|
 |
Maurizio D'Angelo

|
Posted: Sat 18 Jul, 2009 10:24 am Post subject: |
|
|
Michael Pikula wrote: | I did a heat treat yesterday and of course I ran into a problem which renders my salt tubes useless for the spear. The level of the salt changes depending on the temperature and if I filled up the tube with salt to 3/4" from the top for the 1450 degrees that I need it would over flow when I up the temperature to 1600-1525 that I normally use. Due to the nature of salts and the dangers of a liquid at that temperature taking some salt out is not an option. I'm going to have to go back to the drawing board and figure out the best way to get this heat treated properly.
I'm sorry for the delay Jean, I want to get this done right for you above all else. |
Hi Michael Pikula,
Maybe you should have been wrong to write Michael, 1600-1525 degrees Celsius is enough to melt steel. I think 850 degrees should be sufficient. I believe that the steel must have an average carbon content for using the salts.
That if in degrees Celsius.
Stainless evaporates to 2760 ° Celsius
Maurizio
|
|
|
 |
Maurizio D'Angelo

|
Posted: Sat 18 Jul, 2009 10:52 am Post subject: |
|
|
Update.
Fahrenheit to Celsius Converter.
I used the converter, it is clear that expressed in degrees Fahrenheit.
For me it is normal to think in Celsius.
1600 degrees Fahrenheit = 870 degrees Celsius.
All is ok.
My compliments for the work.
Maurizio
|
|
|
 |
Michael Pikula
Industry Professional
|
Posted: Mon 27 Jul, 2009 8:14 pm Post subject: |
|
|
Thanks for the kind words Maurizio!
I got a quick picture to show my progress. I'm pretty beat for the day so I'll save words for when I'm on the ball.
Attachment: 94.55 KB
[ Download ]
|
|
|
 |
Jean Thibodeau

|
Posted: Mon 27 Jul, 2009 8:28 pm Post subject: |
|
|
Michael Pikula wrote: | Thanks for the kind words Maurizio!
I got a quick picture to show my progress. I'm pretty beat for the day so I'll save words for when I'm on the ball. |
That is looking good and the central ridge is awesome and it's very much what the original design was meant to be like.
I think your standard finish is sort of a satin one and that is what I want, I would avoid an overpolished mirror like finish by the way ..... not sure if we discussed this part: Again, no rush and for a custom project things are progressing satisfactorily fast enough.
You can easily give up your freedom. You have to fight hard to get it back!
|
|
|
 |
Michael Pikula
Industry Professional
|
Posted: Thu 27 Aug, 2009 11:53 am Post subject: |
|
|
So today is the day of reckoning, Heat treat! The furnace is getting up to temp as I type, the water is ready, the tempering oven is on, and now it's time to do my best and keep all swords crossed that the quench doesn't produce the "ping" of profanity.
The haft came in this week and I put a quick coat of boiled linseed oil on to keep my dirty fingers from leaving marks all over the pole. It has the slightest hint of a warp, but over the whole distance it is less then .125"
I'll post how it went in a few hours.
And looks like we lost a corner off the spear so time to get back to the forge, I'll post some pictures later on, stay tuned.
|
|
|
 |
Jean Thibodeau

|
Posted: Thu 27 Aug, 2009 9:20 pm Post subject: |
|
|
Michael Pikula wrote: | So today is the day of reckoning, Heat treat! The furnace is getting up to temp as I type, the water is ready, the tempering oven is on, and now it's time to do my best and keep all swords crossed that the quench doesn't produce the "ping" of profanity.
The haft came in this week and I put a quick coat of boiled linseed oil on to keep my dirty fingers from leaving marks all over the pole. It has the slightest hint of a warp, but over the whole distance it is less then .125"
I'll post how it went in a few hours.
And looks like we lost a corner off the spear so time to get back to the forge, I'll post some pictures later on, stay tuned. |
Lost a " CORNER " that sound worrying ...... well I'm not worrying about the final product but I am concerned about your having to either fix things or worse start over !
You can easily give up your freedom. You have to fight hard to get it back!
|
|
|
 |
|