Author |
Message |
Chris Arrington
|
Posted: Wed 19 Dec, 2007 12:47 pm Post subject: What was the traditional Manufacturing Method for ... |
|
|
What was the traditional Manufacturing method for creating the slot or opening in the cross guard thru which the tang of the blade passed.
My understanding is that most cross guards were cast in iron, steel, or brass and then worked by hand to the desired shape. So how was the opening/slot created? Obviously I can imagine it with modern tools and computer controlled machining techniques but how did a traditional smith do it?
|
|
|
 |
Sean Flynt

|
|
|
 |
Gary A. Chelette

|
Posted: Wed 19 Dec, 2007 1:26 pm Post subject: |
|
|
I would think much like they would an ax.
Make a small hole and insert a oblong piece to make it bigger and to the shape they want.
But I think casting is more likely. bronze or Iron can be cast with just a bit of clean up for a finished product.
I'm no sword maker and I've only made one rondel dagger, so I am just guessing.
Are you scared, Connor?
No, Cousin Dugal. I'm not!
Don't talk nonsense, man. I peed my kilt the first time I went into battle.
Oh, aye. Angus pees his kilt all the time!
|
|
|
 |
Gary A. Chelette

|
Posted: Wed 19 Dec, 2007 1:30 pm Post subject: |
|
|
Sean Flynt wrote: | Guards/crosses and pommels were forged and filed rather than cast, with the center pierced and spread while the piece was red hot. No reason they couldn't be drilled and filed cold, though. |
Thanks Sean,
I wasn't real sure on my answer and your post hit 3 seconds before mine.
Are you scared, Connor?
No, Cousin Dugal. I'm not!
Don't talk nonsense, man. I peed my kilt the first time I went into battle.
Oh, aye. Angus pees his kilt all the time!
|
|
|
 |
Rob Miller
Industry Professional
|
Posted: Wed 19 Dec, 2007 2:13 pm Post subject: |
|
|
The hot iron is punched through with a tool made for the job,then the iron is drawn out to the desired shape,the punch can be used again later in the job to cleanly open the hole for the tang to pass through,this can then be filed to fit when cool
Attachment: 49.31 KB

Attachment: 78.36 KB
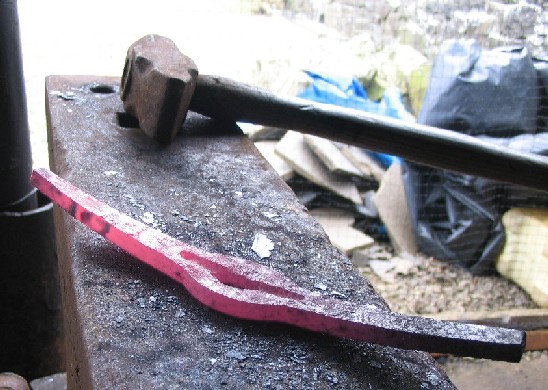
|
|
|
 |
Justin King
Industry Professional
|
Posted: Wed 19 Dec, 2007 6:26 pm Post subject: |
|
|
This beats drilling and filing by a LONG shot-minus heating time this can be done in a few minutes. Plus you keep the mass in the center and so can start with a smaller bar. Forging still has it's uses, nothing can do this faster short of a mill or a press.
|
|
|
 |
Chris Arrington
|
Posted: Thu 20 Dec, 2007 5:53 am Post subject: |
|
|
Thanks Guys ! Especially for the pictures.
I figured that method might be the case, but I wasn't sure.
I have a large piece (about 2' x 3' and somewhere between 3/8" and 1/2" thick) of mild steel that a friend gave me from a farm sale, and I was wondering about its suitability for cross guards.
|
|
|
 |
Rob Miller
Industry Professional
|
Posted: Thu 20 Dec, 2007 9:58 am Post subject: |
|
|
yes,the drift will widen the central portion of the bar,maybe adding 1/4",so if you want a fairly thin grip that would be fine i would think.I use a piece of tool steel,hardened and tempered,cut to the rough tang shape and slightly sharpened at the tip,to cut into the hot steel,the shoulders also provide a recess for the blade,so these can likewise be shaped to suit.The example here is for a type XX guard.the centre swells out a bit with the punching,this is cleaned up and filed eventually.
Attachment: 79.99 KB
[ Download ]
|
|
|
 |
Otto Karl
Location: Ulm, Germany Joined: 05 Dec 2007
Posts: 15
|
Posted: Sat 22 Dec, 2007 11:20 am Post subject: |
|
|
I donīt realy think about Guards were made from Cast Iron: they were suppoused to bear forceful blows, even if the Weapon was a "light" one, as a Rapier or a Smallsword; Cast Iron is strong but very britle. On the other hand, I think the best way to attach the guards is the exposed by the scotsman (sorry, I really don`t remenber his name), because there are specialized but simple Tools designed for that kind of Works.
|
|
|
 |
Jean Thibodeau

|
Posted: Sat 22 Dec, 2007 6:27 pm Post subject: |
|
|
Otto Karl wrote: | I donīt realy think about Guards were made from Cast Iron: they were suppoused to bear forceful blows, even if the Weapon was a "light" one, as a Rapier or a Smallsword; Cast Iron is strong but very britle. On the other hand, I think the best way to attach the guards is the exposed by the scotsman (sorry, I really don`t remenber his name), because there are specialized but simple Tools designed for that kind of Works. |
Cast Iron is brittle and has a very very high carbon content that can make it feel almost oily ( graphite like lubrication maybe ).
If I remember correctly it also crumbles in a granular way when machined. ( machine shop courses decades ago ).
The guard made by casting in modern swords by makers like Albion or A & A is a form of cast steel and the carbon content is much lower like mild steel and not brittle and although cast, is not " cast iron ".
I do think that forged guards might be theoretically better but for large production runs castings, if of reasonably good quality, are a cost savings for the makers and make the swords less costly for the buyers.
You can easily give up your freedom. You have to fight hard to get it back!
|
|
|
 |
Rob Miller
Industry Professional
|
Posted: Sun 23 Dec, 2007 5:40 am Post subject: |
|
|
Thats true Jean,
the 'Traditional' method is as outlined,but for production purposes casting is the obvious solution.If one were to want to create a blade using traditional techniques exclusively then casting is not an option.
I have made many forged crossguards,but now use casting on the majority of my pieces for uniformity.I also found that when forging iron to make a guard there were very often a lot of visible strands in the iron,some customers did not like this finish,being used to production pieces,so i have stopped using iron for that reason,which is a shame since it is very good to forge,and also not prone to rusting in the same way as mild steel.If i forge a cross now i use either mild steel or spring steel,which i anneal to file,and that is also very tough.
|
|
|
 |
Justin King
Industry Professional
|
Posted: Sun 23 Dec, 2007 7:24 am Post subject: |
|
|
Rob Miller wrote: | Thats true Jean,
I have made many forged crossguards,but now use casting on the majority of my pieces for uniformity.I also found that when forging iron to make a guard there were very often a lot of visible strands in the iron,some customers did not like this finish,being used to production pieces,so i have stopped using iron for that reason,which is a shame since it is very good to forge,and also not prone to rusting in the same way as mild steel.If i forge a cross now i use either mild steel or spring steel,which i anneal to file,and that is also very tough. |
I find this ironic, some smiths on this side of the pond will pay several times the going rate of steel to buy wrought iron. I'm sure the mainstream still sees these things with a modern eye but more and more I see a preference for authentic materials among sword collectors, as long as it dosen't sacrifice performance or useability (which is another modern irony since historical swords were used in much more earnest than modern repros, and I secretly suspect that most of us would cringe to see our beloved swords put to work for real by a man intent on killing an opponent).
|
|
|
 |
Bruno Giordan

|
Posted: Sun 23 Dec, 2007 10:45 am Post subject: |
|
|
Justin King wrote: | Rob Miller wrote: | Thats true Jean,
I have made many forged crossguards,but now use casting on the majority of my pieces for uniformity.I also found that when forging iron to make a guard there were very often a lot of visible strands in the iron,some customers did not like this finish,being used to production pieces,so i have stopped using iron for that reason,which is a shame since it is very good to forge,and also not prone to rusting in the same way as mild steel.If i forge a cross now i use either mild steel or spring steel,which i anneal to file,and that is also very tough. |
I find this ironic, some smiths on this side of the pond will pay several times the going rate of steel to buy wrought iron. I'm sure the mainstream still sees these things with a modern eye but more and more I see a preference for authentic materials among sword collectors, as long as it dosen't sacrifice performance or useability (which is another modern irony since historical swords were used in much more earnest than modern repros, and I secretly suspect that most of us would cringe to see our beloved swords put to work for real by a man intent on killing an opponent). |
the only solution is to reforge old items, e.g. old nails coming from the demolition of old farms.
Here in my region in Italy there are a lot of farms being restructured (badly) old bemas, often one undreed or more years old are removed, and many carry old nails made of cast iron.
Old gratings from the same environment could be employed.
To avoid destruction of old artifacts one could resort to new wrought iron, iron ore is abundant in my valleys but it would be very costly to set up an iron refinery as in old times there were many but running costs were farl lower than today.
|
|
|
 |
|
You cannot post new topics in this forum You cannot reply to topics in this forum You cannot edit your posts in this forum You cannot delete your posts in this forum You cannot vote in polls in this forum You cannot attach files in this forum You can download files in this forum
|
All contents © Copyright 2003-2025 myArmoury.com All rights reserved
Discussion forums powered by phpBB © The phpBB Group
Switch to the Basic Low-bandwidth Version of the forum
|