Author |
Message |
Jeremy V. Krause
|
Posted: Fri 06 Jul, 2012 10:11 am Post subject: Regarding Etching of Pattern-Welded Blades |
|
|
As this is not my typical period of interest I figured I'd throw it out there. . . .
Was it done in period or is this simply an unanswerable question?
|
|
|
 |
Timo Nieminen
|
Posted: Fri 06 Jul, 2012 1:15 pm Post subject: |
|
|
Al-Kindi described chemical treatment to bring out the patterns. In that translation, we have "etching substance" (pg 23). But it isn't clear whether he means etching or staining (i.e., patination, as done, e.g., on keris blades).
Biruni says ferric sulphate was used (i.e., names a chemical that was identified centuries later as ferric sulphate), which is an etchant.
"In addition to being efficient, all pole arms were quite nice to look at." - Cherney Berg, A hideous history of weapons, Collier 1963.
|
|
|
 |
Petr Florianek
Industry Professional

|
Posted: Fri 06 Jul, 2012 1:24 pm Post subject: |
|
|
Anglosaxon sources mention the blade "dyed with poison"
if you want to i can find a reference in "The sword in anglosaxon england"
|
|
|
 |
Petr Florianek
Industry Professional

|
Posted: Fri 06 Jul, 2012 1:50 pm Post subject: |
|
|
cant find the book physicaly, but my google fu reveals this
Attachment: 101.93 KB
[ Download ]
|
|
|
 |
Chris Gilman

Location: California Joined: 07 Dec 2007
Posts: 82
|
Posted: Fri 06 Jul, 2012 5:48 pm Post subject: |
|
|
If I may offer an educated guess: If the blade is a "Pattern" welded blade, with a deliberate pattern, perhaps yes, but I don't see a reason to etch a "Damascus" blade (watered steel by another name), since all good blades were made in this fashion, etching them makes little sense. I don’t think I have ever seen a Japanese blade etched in this pattern, so if it was ever done, it was a novelty and not common. However, after the invention of modern alloys, Damascus steel becomes "special" , then people etch it to show it off .
A similar thing happened in silver. Before machine made pieces of silver I don't think there were main stream pieces that used raising marks as a pattern. But after silver started to be machine made and handmade piece were indistinguishable by the average person and merely seen as more expensive, you see an increase in this raising hammer mark pattern, to show off that it was handmade. Prior to this, the raising marks would be planished out and the piece polished.
Chris
|
|
|
 |
Jeremy V. Krause
|
Posted: Sat 07 Jul, 2012 6:03 am Post subject: |
|
|
Petr Florianek wrote: | cant find the book physicaly, but my google fu reveals this |
Thanks Petr,
So here we have something. Good find.
|
|
|
 |
Gene W

Location: The South Of England Joined: 01 Dec 2010
Posts: 116
|
Posted: Sat 07 Jul, 2012 10:50 am Post subject: |
|
|
I'm not sure to which period or even culture you are referring, but the short answer is going to be 'yes'.
Discounting mere lamination, most examples of an actual deliberate pattern will have been etched to one extent or another to make them visible.
If you think of the traditional pattern welding seen in European blades right back to the classical period, then you should be thinking along the lines of what the Ottomans were doing with their blades. There is no way that a smith is going to make (for instance) a double row twistcore 'starry night' pattern with diferentially hardened steel cutting edges and then not bother to make it visible (see first and second pic below).
Here is some food for thought:
http://www.vikingsword.com/serpent.html
Even in wootz blades from asia, while a simple 'crystaline' wootz blade may or may not have been etched, it would be illogical for a smith to manipulate the particles of hard impurities while forging the wootz ingot, into complex and deliberate patterns only to leave those patterns invisible to the naked eye.
It takes a LOT of effort to manipulate a wootz ingot into a fine flowing pattern with ladders or swirls etc. If you want your holy warriors to appreciate this efort, to contemplate it's beauty and reflect on the "forty steps" upon which the faithful ascend to Heaven, or imagine the rivers of paradise in it's 'watered' flowing patterns.....
I'm sure you get the picture
Have a look at pictures 3 and 4 below and imagine how much effort it took to put that pattern in my Shamshir.
Than have a look at this article:
http://www.tms.org/pubs/journals/jom/9809/verhoeven-9809.html
Attachment: 81.04 KB
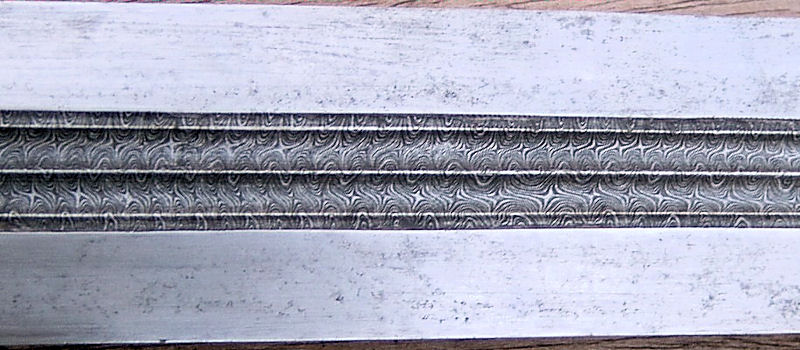
Attachment: 59.83 KB
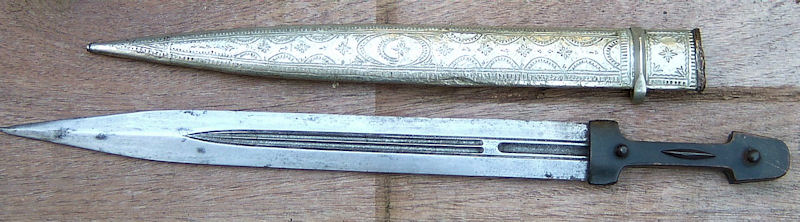
Attachment: 62.47 KB
[ Download ]
Attachment: 37.82 KB
[ Download ]
Last edited by Gene W on Sat 07 Jul, 2012 11:07 am; edited 2 times in total
|
|
|
 |
Gene W

Location: The South Of England Joined: 01 Dec 2010
Posts: 116
|
Posted: Sat 07 Jul, 2012 10:56 am Post subject: |
|
|
In some cultures of course the patterns produced by pattern welding are of as much or more importance than any other 'feature' of form or function.
Think about the 'pamor' of the Keris. In these it is possible to see how far the patterns can be etched and stained to produce the highest possible contrast.:
Attachment: 197.52 KB
[ Download ]
Attachment: 95.22 KB
[ Download ]
|
|
|
 |
Gene W

Location: The South Of England Joined: 01 Dec 2010
Posts: 116
|
Posted: Sat 07 Jul, 2012 11:03 am Post subject: |
|
|
In this Keris, the combination of skilled forging, etching, polish and stain all combine to produce a '3d' relief effect that means that even on a blade which may be pre-1800 the pattern 'pamor' is still beautiful and clear long after most of the final staining has faded:
Attachment: 230.47 KB
[ Download ]
Attachment: 128.3 KB
[ Download ]
|
|
|
 |
Leo Todeschini
Industry Professional

|
|
|
 |
|