Author |
Message |
Mikko Remes
Location: Finland Joined: 04 Apr 2006
Posts: 23
|
Posted: Wed 26 Apr, 2006 10:25 pm Post subject: A couple of swords I made... |
|
|
Hi.
This is my first post on myArmoury.com. Thought I'd share some photos of swords I reasently made. Hope you like 'em
First the katzbalger...
-mr
Attachment: 91.56 KB
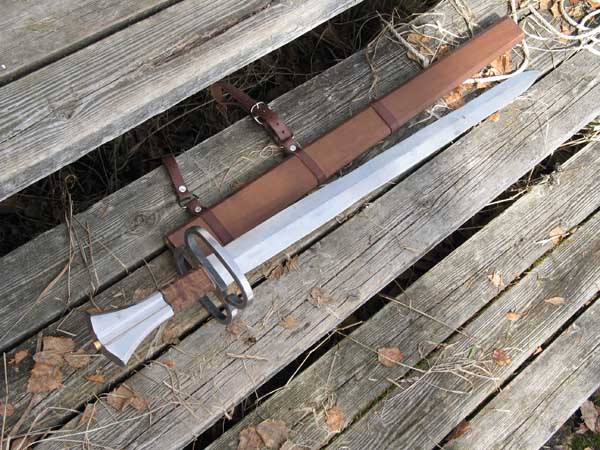
Hakkaa päälle!
Last edited by Mikko Remes on Sat 29 Apr, 2006 10:54 am; edited 1 time in total
|
|
|
 |
Mikko Remes
Location: Finland Joined: 04 Apr 2006
Posts: 23
|
Posted: Wed 26 Apr, 2006 10:28 pm Post subject: |
|
|
...and another shot.
-mr
Attachment: 85.91 KB
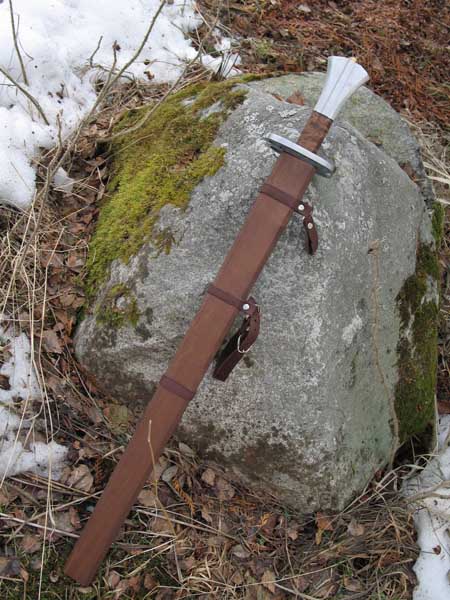
Hakkaa päälle!
|
|
|
 |
Mikko Remes
Location: Finland Joined: 04 Apr 2006
Posts: 23
|
Posted: Wed 26 Apr, 2006 10:29 pm Post subject: |
|
|
Enter the Joukahainen...
Attachment: 93.11 KB
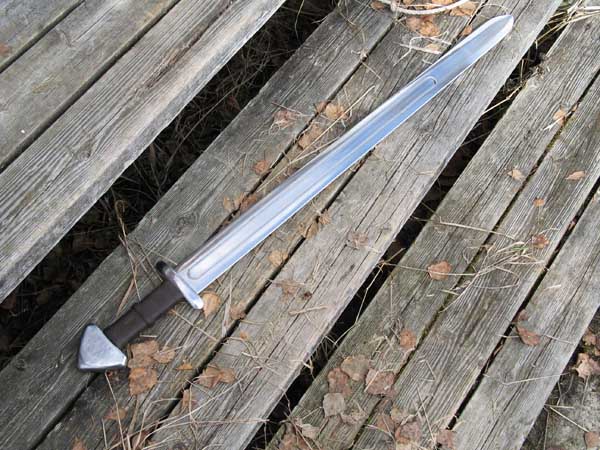
Hakkaa päälle!
|
|
|
 |
Mikko Remes
Location: Finland Joined: 04 Apr 2006
Posts: 23
|
Posted: Wed 26 Apr, 2006 10:30 pm Post subject: |
|
|
And the last shot.
Attachment: 67.54 KB
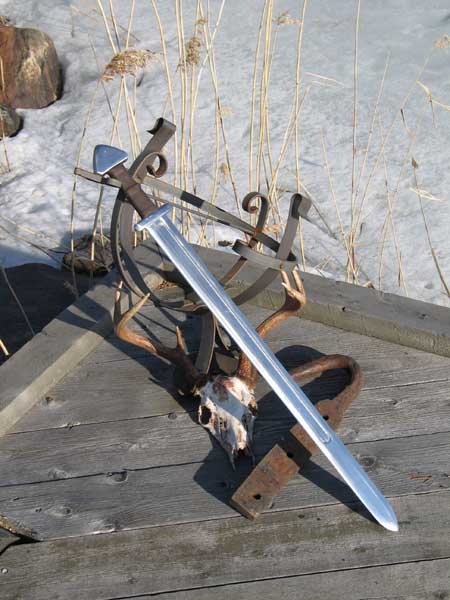
Hakkaa päälle!
|
|
|
 |
Jean Thibodeau

|
Posted: Wed 26 Apr, 2006 11:11 pm Post subject: |
|
|
Mikko;
Welcome, and they both look very good. Maybe you could give use a bit more information about how you made them and maybe some statistic: Weight, dimensions etc ..... How long you have been making swords and if you are making swords
for your own pleasure or if you make them professionally ?
By the way you can post more than one picture per post on this forum.
With the Katzbalger I see some potential for some nice filework on the guard maybe: Just a suggestion as it look very good as it is now, the lines are very good but those flat surfaces sort of invite some detailing.
You can easily give up your freedom. You have to fight hard to get it back!
|
|
|
 |
Mikko Remes
Location: Finland Joined: 04 Apr 2006
Posts: 23
|
Posted: Thu 27 Apr, 2006 1:11 am Post subject: |
|
|
Thanks for your comments.
I ground both of them. On the katz I used an old truck spring (correct?) and on the viking sword just some low-to-none carbon steel. That makes the viking basicly a wall-hanger...
The OA lenght of hte katz is about 90cm and it weights something like 1.2kg. Blade width is at the guard about 4cm. PoB lies about 20cm from the guard. The handle is waxed birch with a dark brown wash. The scabbard is made from alder. As with your suggestion about the file work, I agree. There could be some. I was going to twist the bar and then shape it to S but finaly decided leave it plain. Thats because the pommel. It has straight lines and no decoration. I wanted to give the katz a mean no-nonsense appearance.
The OA leght of the viking is about 94cm with a weight of 1.4kg. It has PoB about 25cm from the guard. The handle has an ash core with a thick leather riser glued on and covered with thin leather. I'm currently working on the scabbard and I quess it will be complete later today.
I make swords for my own pleasure. I made my first four years ago when I saw the FotR and fell in love with Arwen's sword. Since then I've made another elven sword, Gimli's walking axe x 2, a Zatoichi-like kane sword, a Spatha, a warhammer from a railroad spike and these two. I also make puukko-knives wich is a dear hobby along with swords. Once I even dreamed of making a profession out of them but decided that I enjoy it more when I don't _have_ to make them. I'm graduating within a month from Kuopio Academy of Design, Finland. That means that I don't have workshop anymore... I quess I have to build my own one day =)
-mr
Hakkaa päälle!
|
|
|
 |
Jean Thibodeau

|
Posted: Thu 27 Apr, 2006 10:07 am Post subject: |
|
|
One approach to making some professionally and not taking the fun out of it is to just make what you like and them see if you can sell it. The thing is to just avoid taking orders or commissions were you end up having to deal with missed deadlines and feeling forced to work on it when you don't feel inspired or where you must worry about doing what you promised to do.
So some become partime makers who don't really have to sell anything will set up a display table at a Medieval fair or sell just through internet word of mouth. ( You might even be able to sell stuff to people on this site if you wish using the marketplace Forum. )
I'm glad you took my suggestion about file work well, as I was worried I might offend you making the suggestion, if you interpreted it as criticism rather than just a comment.
I understand your choice to keep it a simple and Spartan design and any filework on the guard would need to be compatible to some similar work on the pommel. The thing is that the next one you make can be done differently, so you can have both.
The Viking in soft steel would make a good costume or reinactment piece, maybe ? For light sparring some heat treating might be better for durability ? For a wallhanger not a factor.
And welcome again.
You can easily give up your freedom. You have to fight hard to get it back!
|
|
|
 |
Shawn Shaw
Location: Boston, MA USA Joined: 07 Jan 2006
Posts: 115
|
Posted: Thu 27 Apr, 2006 11:16 am Post subject: |
|
|
Very nice...I'm working on my first sword these days.....I'll have pics when I have something that's ready for public viewing....
Do you have access to something to heat treat with? You can get a propane forge for ~$400 but it may not be long enough (that's my problem...making anything bigger than a dagger means I can't heat treat it in my gas forge).
You could also find a friendly potter who might let you borrow their kiln....
Anyways, I don't think you can heat treat the viking sword....without the carbon you're just not going to be able to make it much harder no matter what you do with temperature. Of course, you could always carburize it but you've already gone to all the trouble to polish/assemble it....I'd just leave it alone, personally, it looks quite nice.
|
|
|
 |
Bob Burns

|
Posted: Thu 27 Apr, 2006 11:58 am Post subject: |
|
|
Hi Mikko,
Welcome to what "I" consider to be by far the best Western European Sword website anywhere on the internet. All the profound experts are here, the finest swordsmiths and sword instructors on European swords to be found anywhere in the world, are here! I am in my first year of this fascinating passion and I cannot begin to tell you how helpful "myArmoury" has been to me and I do mean that with all sincerity! I would not say so if it were not true!
I like what you have done with your swords Mikko. My wife and I have a wish if we were wealthy, she'd like to have her own horticulture center and I'd like to have my own forge (although I would have to hire an expert to teach me from square one as I do not know diddly on how to make a sword) . Personally, I wish I lived near Minneapolis, MN or New Glarus, WI (except for the cold weather) as I'd love to go work for Arms & Armor or Albion Swords and learn things from the ground up as a grunt for a respectable grunt wage. The hell with the money actually, I'd be tickled to death just to have the opportunity (this is said at my present financial reality position in life and not if I were wealthy).
I look forward to reading your posts Mikko, as I am sure you have much to share!
Sincerely,
Bob
|
|
|
 |
Mikko Remes
Location: Finland Joined: 04 Apr 2006
Posts: 23
|
Posted: Thu 27 Apr, 2006 9:59 pm Post subject: |
|
|
Thank you all for your comments.
I just finished the scabbard for the viking. I think it turned out quite nice. Now I'll just have to figure out how to attach it to a belt or baldric... I'll post some pics as soon as I can.
cheers
-mr
Hakkaa päälle!
|
|
|
 |
Mikko Remes
Location: Finland Joined: 04 Apr 2006
Posts: 23
|
Posted: Thu 27 Apr, 2006 10:05 pm Post subject: |
|
|
Jean Thibodeau wrote: |
So some become partime makers who don't really have to sell anything will set up a display table at a Medieval fair or sell just through internet word of mouth. ( You might even be able to sell stuff to people on this site if you wish using the marketplace Forum. )
I'm glad you took my suggestion about file work well, as I was worried I might offend you making the suggestion, if you interpreted it as criticism rather than just a comment.
|
I never seem to be able to part with any blades I've made... That is why I made two axes of Gimli. One for the friend who ordered it and one for me.
And don't worry. None taken what so ever. It's always good to listen what people have to say about one's work...
-mr
Hakkaa päälle!
|
|
|
 |
Jean Thibodeau

|
Posted: Thu 27 Apr, 2006 10:33 pm Post subject: |
|
|
Mikko;
Have a look at the to this topic thread as it shows how to do the wrap of belt to scabbard. The picts showing the way to do it is a few replies down so scroll down to see it.
http://www.myArmoury.com/talk/viewtopic.php?t=6361
This should help figuring out how to do it to your Viking sword scabbard.
Oh, I know what you mean, I would have a great deal of difficulty selling what I made unless I made more than one, and them I would always want to keep the best or most recent one: But them if you make one you like more you can always sell a piece you are no longer attached to.
You don't have to make a business out of it if you don't want to, but selling the occasional piece could finance getting better tools or buying other swordmaker's work. Just keep making stuff you enjoy making and if you get good enough at it the desire to go commercial will either come or it won't.
Oh, their should be a market for puukko-knives or seax or small throwing axes or spear heads .......etc .....
Design being the first thing and quality heat treated i.e. Good sharp blades: There is always a market for these.
You can easily give up your freedom. You have to fight hard to get it back!
|
|
|
 |
Mikko Remes
Location: Finland Joined: 04 Apr 2006
Posts: 23
|
Posted: Thu 27 Apr, 2006 11:43 pm Post subject: |
|
|
And here's the scabbard. It was made from alder with sheet-metal 'rings'. I gave it a dark brown wash and later I treated it with "Danish Oil". Great stuff. Works fine for knife handels, also.
Thanks for the link. That's something I had in mind too. In smaler scale, though.
-mr
Attachment: 105.23 KB
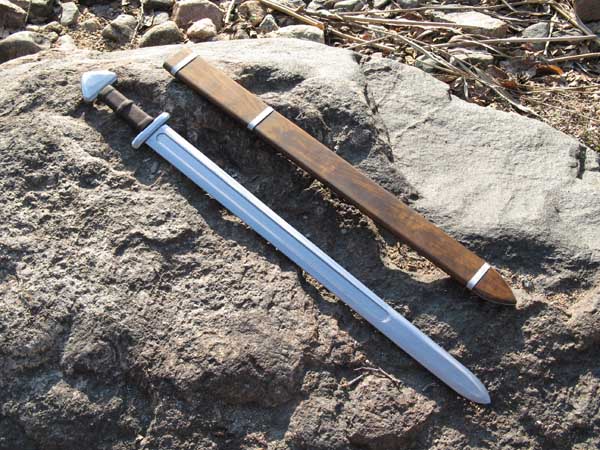
Attachment: 63.4 KB
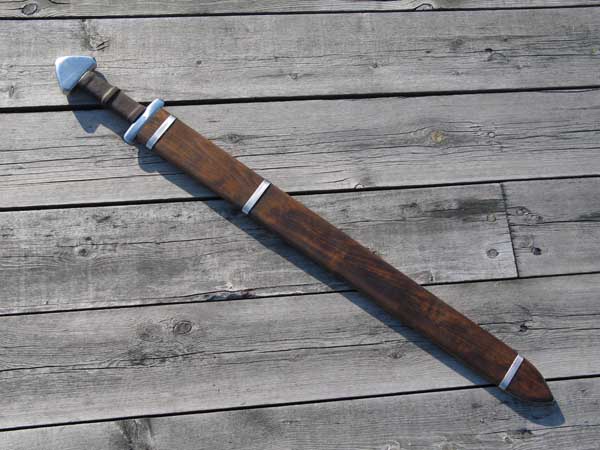
Attachment: 102.51 KB

Hakkaa päälle!
|
|
|
 |
Shawn Shaw
Location: Boston, MA USA Joined: 07 Jan 2006
Posts: 115
|
Posted: Fri 28 Apr, 2006 5:15 am Post subject: |
|
|
How did you assemble your guards? Any chance of some close up pics?
|
|
|
 |
Mikko Remes
Location: Finland Joined: 04 Apr 2006
Posts: 23
|
Posted: Fri 28 Apr, 2006 11:46 am Post subject: |
|
|
Shawn Shaw wrote: | How did you assemble your guards? Any chance of some close up pics?
 |
The guard was made from a 16mmx16mm square bar. The opening for the tang was then machined to it. I filed the hole to a tight fit. After I was happy with the fit I ground the guard to a shape with a belt sander and polished it. The pommel was made from 20mm thick steel. I used an angle grinder to saw off the rough shape. Next I drilled a hole for the tang and machined it roughly to fit the tang. After I got the grip fitted I peened the tang to secure the grip and pommel. It came out pretty good. No rattle nor movement what so ever.
-mr
Attachment: 51.89 KB

Hakkaa päälle!
|
|
|
 |
Edward Hitchens
|
Posted: Fri 28 Apr, 2006 12:42 pm Post subject: |
|
|
Welcome Mikko! Those are very fine swords you've created there, especially that katzbalger.
"The whole art of government consists in the art of being honest." Thomas Jefferson
|
|
|
 |
Don Calcote
|
Posted: Wed 03 May, 2006 6:40 pm Post subject: |
|
|
Edward Hitchens wrote: | Welcome Mikko! Those are very fine swords you've created there, especially that katzbalger.  |
I agree completely. I think I need to start looking for some truck springs.
|
|
|
 |
Shawn Shaw
Location: Boston, MA USA Joined: 07 Jan 2006
Posts: 115
|
Posted: Thu 04 May, 2006 4:22 am Post subject: |
|
|
A belt sander, you say? Hmmm.....
I've heard that a belt sander is really nice for sword-making. Personally, I've got a disc grinder. Do you (or does anyone) have any comparative comments about belt vs. disc grinders?
One thing I've already noticed is that it's really hard to get a long bevel with a disc grinder....
Thanks!
|
|
|
 |
Mikko Remes
Location: Finland Joined: 04 Apr 2006
Posts: 23
|
Posted: Wed 12 Jul, 2006 2:41 am Post subject: |
|
|
Here's a couple of pics of me cutting with the katz and couple of other toys I made.
Enjoy.
-mr
Attachment: 103.42 KB
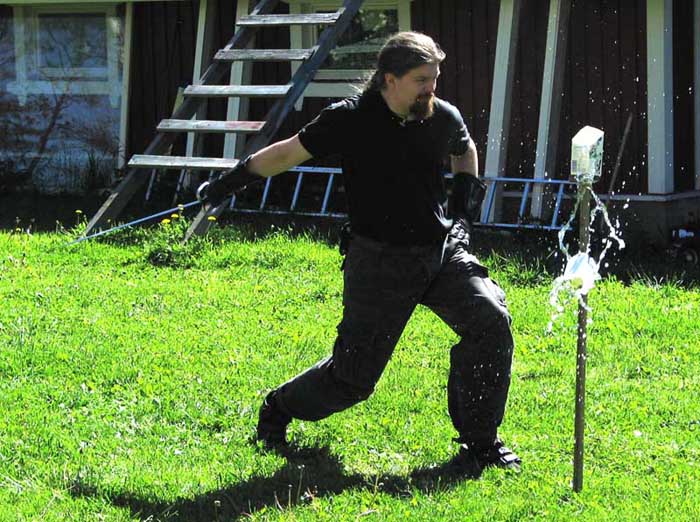
Katzbalger
Attachment: 123.84 KB
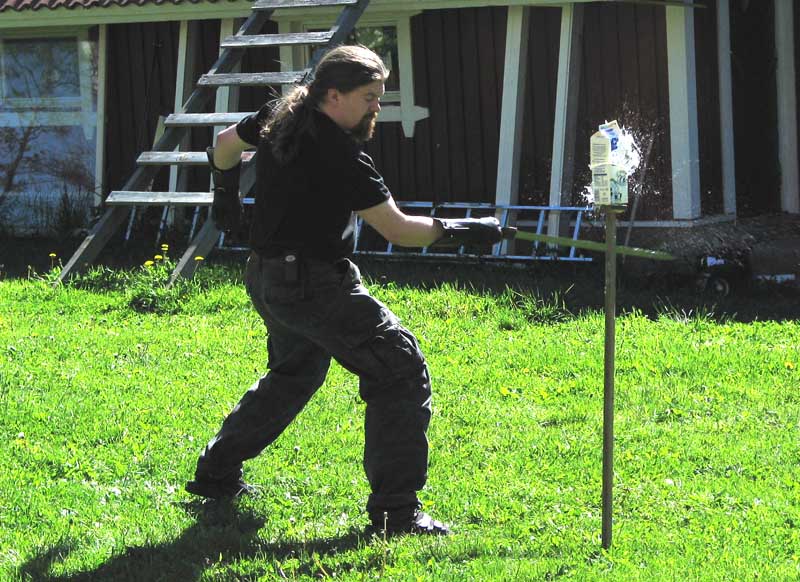
Cutting with spatha...
Attachment: 103.66 KB
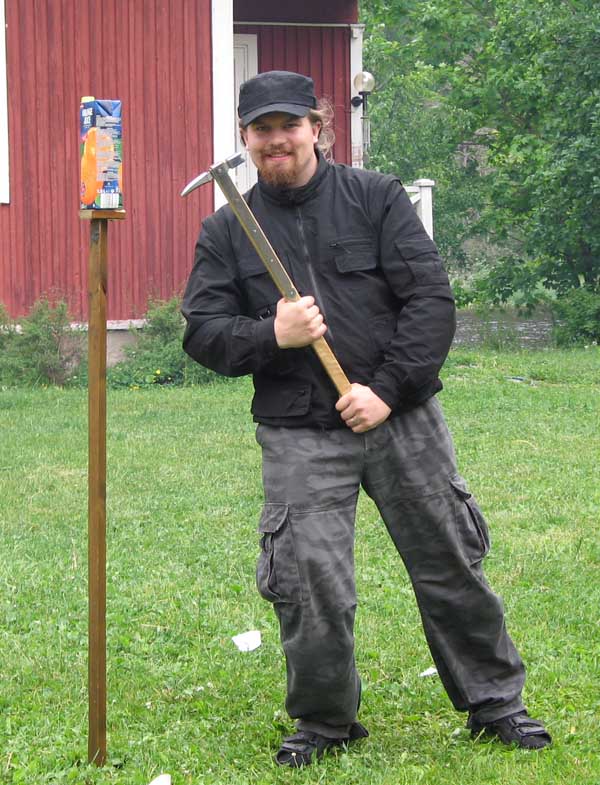
Attachment: 104.03 KB
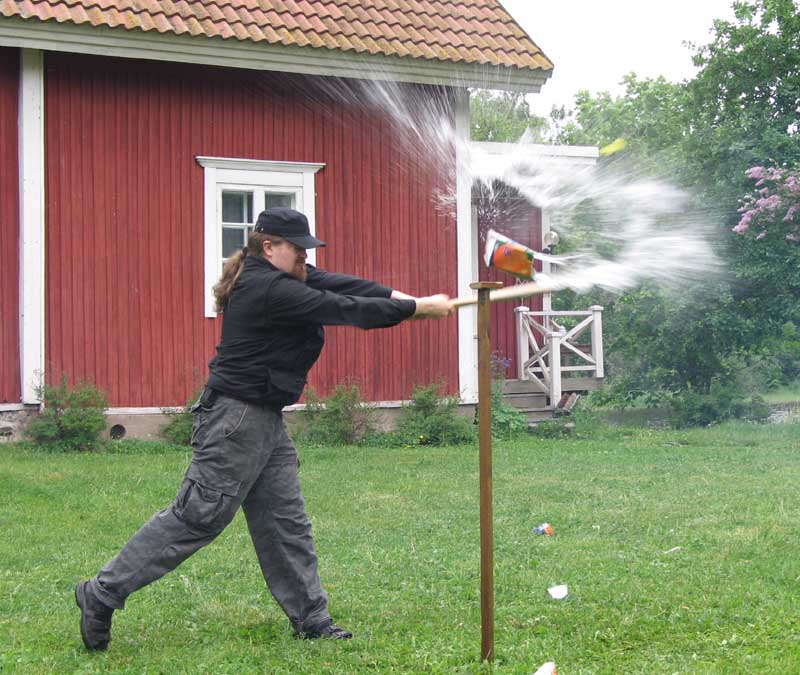
Effects of the hammer...
Attachment: 108 KB
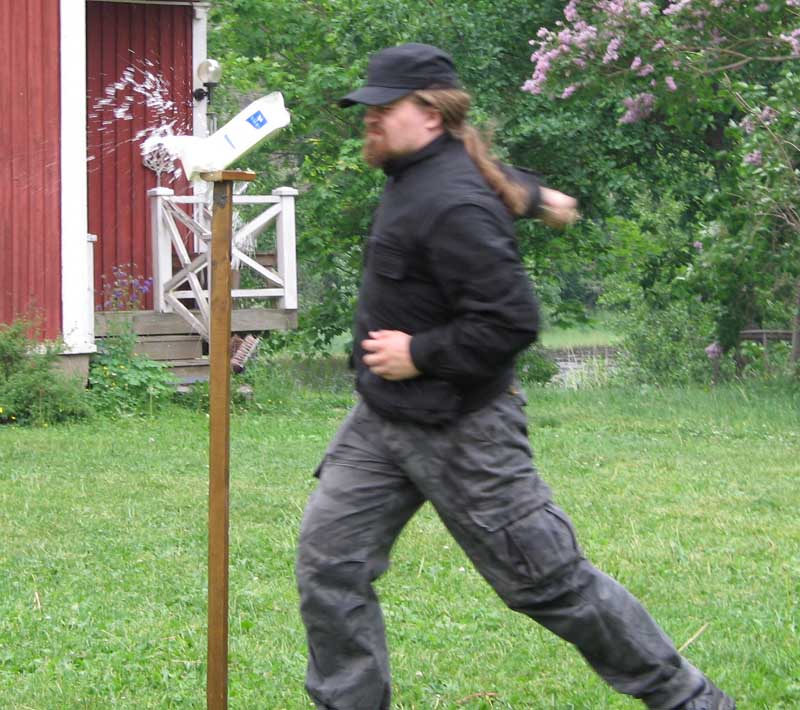
Cutting witha seax
Attachment: 119.43 KB
Yours truly with the spatha [ Download ]
Attachment: 106.51 KB
Yours truly and the seax [ Download ]
Hakkaa päälle!
|
|
|
 |
Joe Fults
|
Posted: Wed 12 Jul, 2006 9:38 am Post subject: |
|
|
Its always interesting to see what people who don't make these things to pay the bills manage to create.
"The goal shouldn’t be to avoid being evil; it should be to actively do good." - Danah Boyd
|
|
|
 |
|