Author |
Message |
Joe Caswell
|
Posted: Wed 07 Jan, 2004 5:21 pm Post subject: Advice for a Sword Maker |
|
|
Hi,
This is my first visit to myArmoury.com and, while looking over past postings, was pleased to see that there are others with similar interests in historical arms, et cetera (I wonder sometimes).
I'm a full time knifemaker that focuses exclusively on pattern welded product, especially things harkening to earlier days. Like many on this forum, I've researched swords for years and am fixing to shift the bulk of my attention from the lucrative knife market to the far more specialized sword (and related) segment.
One of my big problems has been trying to establish fair pricing for this sort of thing so I can project just how soon I'll be losing my shirt. Most of my special pieces are sold before I can get them out in front of people and that doesn't help me gage true demand on the open market.
Here is a link to something I finished recently. Any insite is greatly appreciated.
http://www.caswellstudios.com/SwordPages/Body...ailey.html
Joe Caswell
|
|
|
 |
Angus Trim
|
Posted: Wed 07 Jan, 2004 6:59 pm Post subject: |
|
|
Well Mr. Caswell
Let me introduce myself. I'm Angus Trim, the NW swordfabricator, troublemaker, and Dumb Irish Country Machinist. Always willing to share an opinion.
First, let me tell you, that the "upper echelon" of the sword smiths, are very popular. And that the upper echelon of the sword market is beginning to follow the kustom knife world in valuation. In other words, guys that are real popular, are seeing the potential value of what they do grow real fast........
In the online segment of the market, Kevin Cashen, Vince Evans, and Peter Johnsson are the names. There are a couple other smiths as capable, but they are not as well known.
Right now, a collector looking to find a smith to make a custom project is going to have a heck of a time finding someone to do it. The last I heard, Kevin is out four years, Vince isn't really taking orders, and Peter's custom work is limited too. There is a large void in the current market. This void as allowed a couple of semi-production ventures to step in and fill a part of the void. However, that void is still wide open........
The thing is though, that like a lot of fields, name recognition is very important. And in this crowd, sheer two dimensional aesthetics isn't going to get you ushered into the "upper tier". The "mechanical" stuff, and the "organic" stuff is gonna have to be there.
So let me describe the three gentlemen above just a bit.
Kevin does just some really awsome pattern welding. He's a kustom maker, who has done some of the nicest migration era stuff around, but he doesn't "specialize. His stuff isn't just drop dead gorgeous, it performs on a par with its dollar valuation.
Vince' style is a bit different than Kevin's, and he also does some knock out pattern welding. His baskethilts are to die for..... and I for one have mistaken a dao and scimitar made by Vince as antiques. He's done the research, to replicate these swords three dimensionally, and he "has it", such that what you feel is as good as the finest antiques you'll handle. Having handled several antique baskethilts at Pat Tuffer's place before ever handling a Vince baskethilt, I was awed by the handling of his work. As good or better than the nicest antiques I've yet had the opportunity to handle.
Peter Johnsson is not just one of the top smiths, he's also likely the leading researcher into the Western Sword. What he does with a sword's lines is indescribeable, mainly because its not only really attractive, its subtle...... Handle a PJ sword, and its like handling a medieval sword when new........
All three of these gentlemen make swords that perform well.
So........
Looking at those photos, it looks to me like you have the two dimensional stuff down. The thing is how is the third dimension, the fourth {mechanical}, and the fifth {organic}.
As it happens, there's a couple of guys on this forum, who are fairly well thought of as "reviewers". Pat Kelly is relatively busy, but for a collector guy, he's pretty sharp on what a sword is all about. Let me clarify, he's not up to the best makers in sword knowledge, but he's certainly better than 95% of the collectors out there, and he's pretty objective.
If I was in your shoes, I'd see if I could talk Patrick into looking at that sword.
Value? If its "there", in all five dimensions, then the current market for something like that is $2000 on the low side, $4000 to $5000 on the high side. But, there is also a growing understanding, that this is underpriced for the amount of work into the project, and compared to what the more well known knife makers get.............
my $.02
Auld Dawg
swords are fun
|
|
|
 |
Russ Ellis
Industry Professional
|
Posted: Wed 07 Jan, 2004 9:05 pm Post subject: |
|
|
Hello Joe,
I'm not a swordmaker, but I do a have a small amount of experience in the area, and I can say for sure that finding the right pricing structure is darned hard to do. I've been told several times recently that I'm pricing my stuff to low, and perhaps I am but so far it has worked pretty well for me.
I think Angus Trim gave you some good advice. I'd send a piece along to a good reviewer, someone with a decent reputation for integrity and fairness and see what they have to say about it in comparison with other high quality pieces they have handled. That should give you a pretty good idea of what prices you can charge. Since Viking era pieces are Patrick's primary area of interest he seems like a natural choice for what it is worth. The guy that owns this site Nathan Robinson would also be a good pick.
Finally I have to say that the stuff on your site looks very nice. The pattern welding is certainly a tour de force. I am a bit thrown by that wheel pommel on that type X on your front page. As you say it is not unheard of but it is rather unusual. If I might ask why did you decide on it? Stunning job on the fittings to by the way if I might say so.
TRITONWORKS Custom Scabbards
|
|
|
 |
Patrick Kelly
|
Posted: Wed 07 Jan, 2004 9:28 pm Post subject: |
|
|
Hello Joe, and welcome to myArmoury.
From what I've seen on your site your work looks very nice, with a very unique signature look to it.
I particularly like this piece:
Russ is correct, my main area of interest lies with swords of the Viking age, and early middle ages. As such, I find your recent project to be thought provoking. Very nice.
Welcome.
"In valor there is hope.".................. Tacitus
|
|
|
 |
Joe Caswell
|
Posted: Wed 07 Jan, 2004 11:36 pm Post subject: Advice for a Sword Maker |
|
|
Hi and thanks for the info!
I do appreciate the kind comments regarding the "2-D" aspect of my stuff. It is regrettable that it's all you can get through the internet.
I would love to discuss the virtues that would make the perfect Type X (or similar). It would also be very helpful to inspect what is considered a very high-quality modern reproduction. This would go a long way in identifying which characteristics are prized in a sword of this type. As it is, the sword I linked in my first posting was actually designed from dimensions gleaned from originals (fuller depth at hilt, fuller depth at tip, thickest dimention at hilt, thickest dimension at point, etc, etc). I realize, however, that there is often a difference between what conforms with historical accuracy and what performs optimally.
Russ, I tend to favor the looks of either the sandwich style migration hilt or the "Tea Cozy" pomel which, as we know, are among the more typical for a pattern welded sword of this type. I chose the wheel for this blade because, when "trying on" the templates, it just jumped out at me, what can I say? It's a conceivable combination for 1st generation hilting and certainly for 2nd or 3rd. Plus it lends itself nicely to this sort of enammel work.
Patrick, thanks for sharing your favorite off my site. I like that one a lot as well. It's funny, but I just got the e-mail confirming the sale of that very knife this evening after reading through your replies (it sold for $1,000, which I feel OK about). If you'd like to see the sword, please let me know, though I'd rather send you the next one as this one is going to be traveling around a little pretty soon.
Angus, thanks for the great advice and insight. My main experience with swords is the epee. I have extensive experience with it and good track record for competitive victories, but an epee is not a type X. I haven't cut much more than straggling tree branches with this type X before it was finished. It's all medium carbon/high-carbon and austempered. I bent it under foot and between two pipes pretty acutely. It is a true spring. but pretty stiff (not floppy or "whippy" as we might say in sport fencing). What would be the hallmarks of "function" at the highest level of swordmaking? I'm not sure what you mean by "organic" though I'd certainly like to know.
Thanks for the warm welcome I hope to benefit from your additional comments,
Joe
|
|
|
 |
Geoff Wood
|
Posted: Wed 07 Jan, 2004 11:57 pm Post subject: Re: Advice for a Sword Maker |
|
|
Joe Caswell wrote: | Hi,
This is my first visit to myArmoury.com and, while looking over past postings, was pleased to see that there are others with similar interests in historical arms, et cetera (I wonder sometimes).
I'm a full time knifemaker that focuses exclusively on pattern welded product, especially things harkening to earlier days. Like many on this forum, I've researched swords for years and am fixing to shift the bulk of my attention from the lucrative knife market to the far more specialized sword (and related) segment.
One of my big problems has been trying to establish fair pricing for this sort of thing so I can project just how soon I'll be losing my shirt. Most of my special pieces are sold before I can get them out in front of people and that doesn't help me gage true demand on the open market.
Here is a link to something I finished recently. Any insite is greatly appreciated.
http://www.caswellstudios.com/SwordPages/Body...ailey.html
Joe Caswell |
Hi Mr Caswell
Gorgeous workmanship. I do have some issues with the style of the hilt components, but that may be a personal preference. There seems to me to be to be at least one axis of symmetry too many in the pommel and the crossguard. Then again, I am probably sacriligeous in my opinion of Mr Cashen's style also, so my taste counts for little. For the more historical end of pattern welding, Patrick Barta's work may give some additional pricing information (although as a Czech he may have a built in pricing advantage).
regards
Geoff Wood
|
|
|
 |
Leif Hansen
Industry Professional

|
Posted: Sat 10 Jan, 2004 5:48 pm Post subject: |
|
|
Rick Barrett also offers many pattern-welded pieces, though they're mostly "fantasy" configuration.
http://www.barrettcustomknives.com
---------------------------
Leif Hansen
Albion Armorers
|
|
|
 |
Larry Nowicki
|
Posted: Tue 02 Mar, 2004 6:59 am Post subject: |
|
|
I too am new to this forum. Like what I see so far. I've been making knives for a few years now part time.
I'm looking to do this in retirement. Swords have always facinated me and I think it would be a great addition to my work.
I would like to learn the ins and outs of fittings, profiles, tapers etc... and all the things that would make a sword authentic.
Someday to have one of my works mistaken for an antique would be great. I've been forging in 5160, D2, W2, 1040, O1,and some cable demascus. Mostly edge quenched but a few clay heat treats. This spring I will be building a new coal forge. I curently have a propane forge, Little Giant power hammer, several anvils, grinders, buffers and stuff. I figure I still have a lot to learn and plan to keep at it so that when the time comes I'll be good enough to make the grade. Any and all directions will be apreciated. The Idea of filling a nitchie until I make a name for myself sounds great but I want to go about it the right way.
Attached is a few of my recent cordwraps.
Always a student
Larry Nowicki
Attachment: 22.12 KB
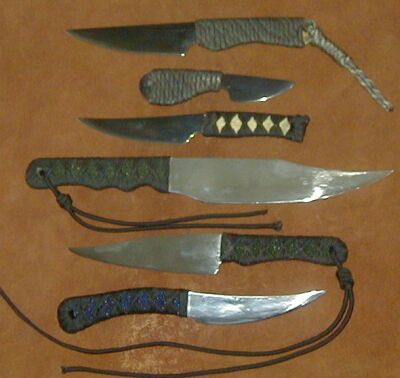
Always A Student
|
|
|
 |
|
You cannot post new topics in this forum You cannot reply to topics in this forum You cannot edit your posts in this forum You cannot delete your posts in this forum You cannot vote in polls in this forum You cannot attach files in this forum You can download files in this forum
|
All contents © Copyright 2003-2025 myArmoury.com All rights reserved
Discussion forums powered by phpBB © The phpBB Group
Switch to the Basic Low-bandwidth Version of the forum
|