Author |
Message |
Leo Todeschini
Industry Professional

|
Posted: Thu 13 Aug, 2020 1:47 am Post subject: Seax of Beagnoth repro again |
|
|
Hi All,
A few years ago I made a reproduction if the Seax of Beagnoth from the British Museum and it was time to revisit this piece and here we are.
The seax is almost certainly 10thC Anglo Saxon in origin and was found in the Thames in the mid 19thC.
The blade is constructed from wrought iron and shear steel and heavily inlaid with different coloured wires on both faces. One face has exclusively geometric patterning in a fairly regular layout and the other side is far more mixed up.....
The released photos and the description do not highlight at all the mixed up nature of the inlays. The 'rune' face has the Futorc alphabet laid out in full, although slightly in the wrong order, some geometric inlay and then the Saxon name 'Beagnoth'. Whether the name is the owner, maker or the blade name is unknown.
Why a warrior of status requires a spelling primer laid out on a blade is of course a mystery, but that is not the end of it.....The description and the photos make it sound like the inlay is of one twisted wire set and is reasonably coherent, but in fact some of the letters have 2 different wire sets within the same letter and from letter to letter the wire sets are different. There is no rhyme or reason to it. Similarly the twisted wire sets that border the lettering and geometry on both sides face in different directions and are of different lengths. Basically the whole thing is a mess.
Which leaves the question of what is going on? To cut the grooves and lay out the piece and prepare this very high status piece for the work is 99.9% of the job and yet they didn't care to pick up the right wire? This mess was deliberate - but why? Perhaps it looks like a mess but there is method in it that we just can't see.
You may also see that this blade is a different shape to the 'original'. This is simply because the original has broken near the angle change on the back and created a very distinctive 'broken back' shape that in fact the original never had. Blade forging was by James Woods.
Anyway I hope you like it.
Tod
I have made a reproduction with a full 'making of process' of this seax before and posted up full threads on this site and you can find both of those here
http://myArmoury.com/talk/viewtopic.php?t=321...t=beagnoth
http://myArmoury.com/talk/viewtopic.php?t=335...t=beagnoth
Attachment: 184.2 KB
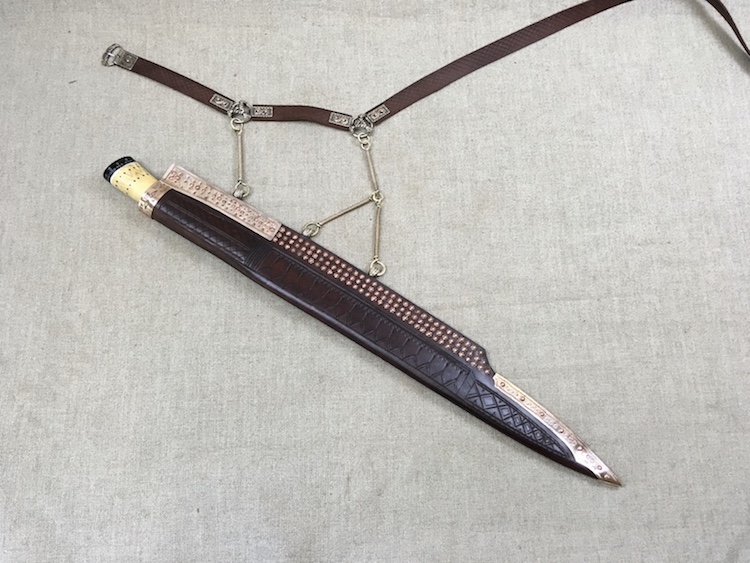
Attachment: 172.26 KB
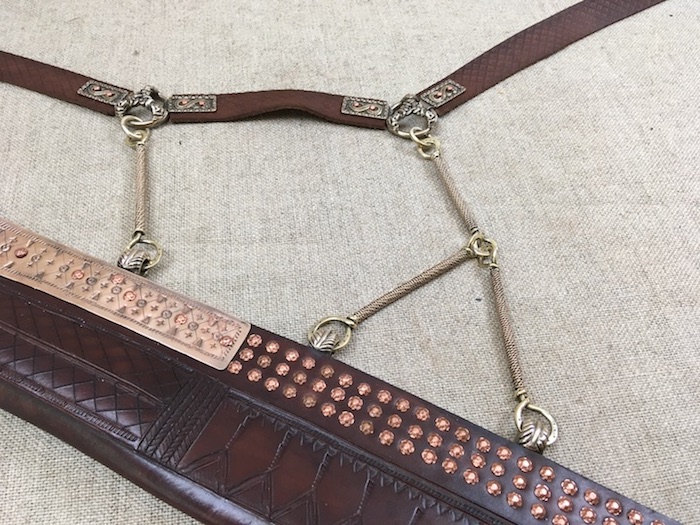
Attachment: 173.14 KB
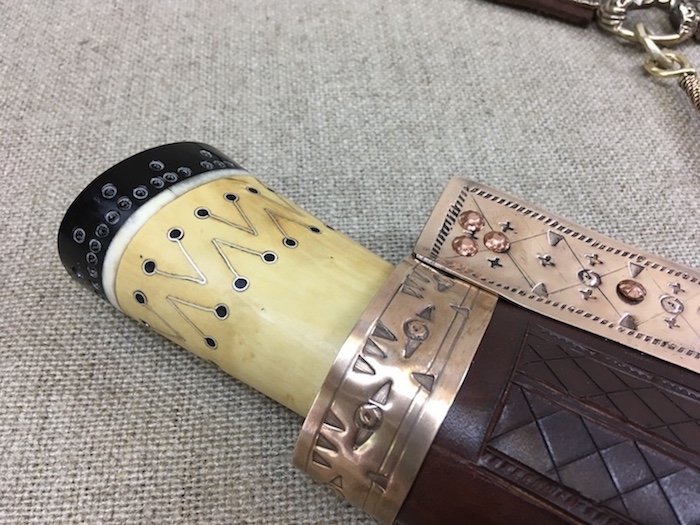
Attachment: 171.19 KB
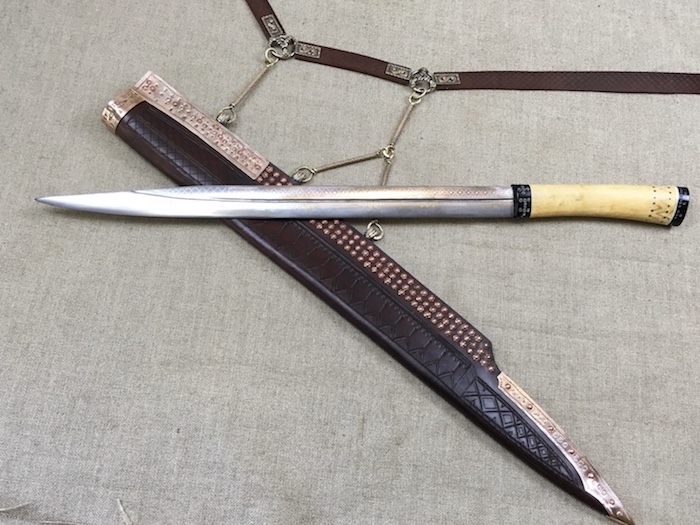
Attachment: 164.69 KB
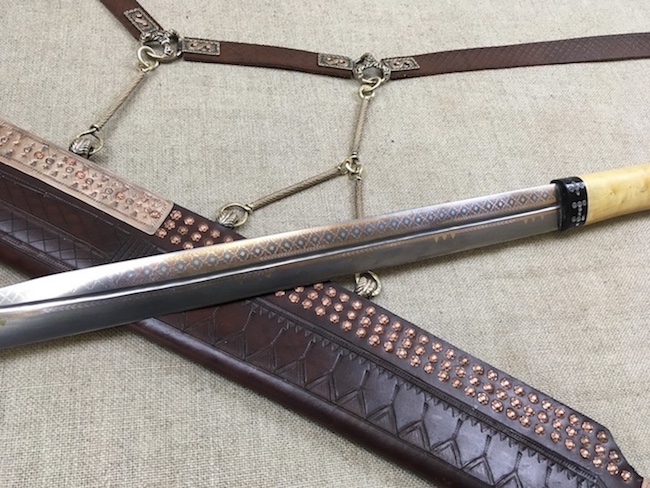
Attachment: 163.86 KB
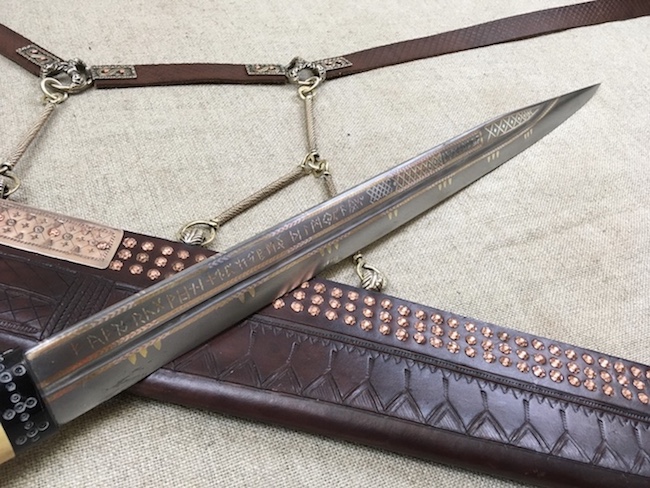
Attachment: 137.78 KB
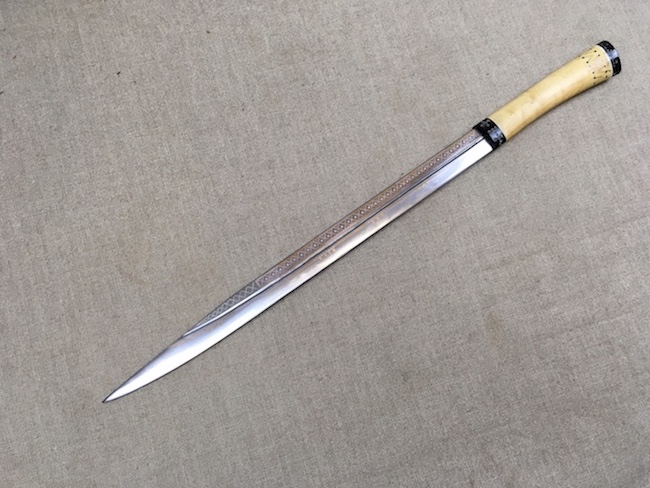
Attachment: 172.4 KB
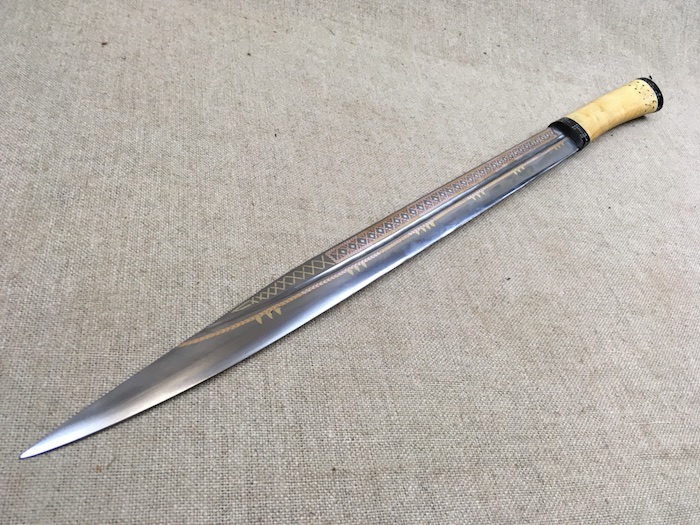
Attachment: 165.3 KB

www.todsworkshop.com
www.todcutler.com
www.instagram.com/todsworkshop
https://www.facebook.com/TodsWorkshop
www.youtube.com/user/todsstuff1
Last edited by Leo Todeschini on Thu 13 Aug, 2020 12:21 pm; edited 1 time in total
|
|
|
 |
Nathan Robinson
myArmoury Admin


|
|
|
 |
Greyson Brown

|
Posted: Thu 13 Aug, 2020 7:13 am Post subject: |
|
|
I have a blacksmith friend who has a bar with several different types of twists on it as a demo piece. Your description of the inlay kind of makes me think of that. I can image a salesman* with this seax talking to a potential customer: "So you want wire inlay, huh? Well, my smith can do something like this, or if the wire faces the other way it looks like this. Here is an example of what it could look like with the whole pattern in a single wire, but if you are looking for something with more variety, here is an example of a rune with different wires for different sections. If he switches the wire direction in the middle, you get this effect. So take a moment to look at these examples on my seax, and we'll get you set up with something that reflects your personal taste."
I have no clue if that idea is even close to the real explanation, but that is the mental image I got from reading your post.
-- Greyson
*In reality, the smith and the salesman would probably be the same person (or the salesman would be the apprentice - I'd make my apprentice deal with the customers), but a salesman is what I think of in this scenario even if it isn't necessarily historical.
"So long as I can keep the path of honor I am well content."
-Sir Arthur Conan Doyle, The White Company
|
|
|
 |
Jeremy V. Krause
|
Posted: Thu 13 Aug, 2020 7:49 am Post subject: |
|
|
It's nice to see this seax reproduced again. The blades on the two are really pretty similar but it's cool to see Tod's artistic take on the the grip and scabbards. Similar but still striking in their own character.
|
|
|
 |
Mikko Kuusirati

|
Posted: Thu 13 Aug, 2020 8:32 am Post subject: |
|
|
Oh my, that is gorgeous!
Speaking of the blade shape, the break and deformation of the original item are fairly clearly shown in this photo.
The Wikipedia article has pretty good close-ups of the inlays, too, with a clear view of the at least seemingly haphazard wire patterns. I have to wonder if parts of it aren't actually repairs made piecemeal during its working life?
(I had to use TinyURL because the forum keeps converting the word "seax" into a hyperlink to the corresponding article even when it's part of a URL.)
"And sin, young man, is when you treat people like things. Including yourself. That's what sin is."
— Terry Pratchett, Carpe Jugulum
|
|
|
 |
Paul Hansen

|
Posted: Sat 15 Aug, 2020 12:25 am Post subject: |
|
|
That's beautiful Tod!
Maybe even more importantly, it somehow looks "real", like the original may have looked once.
Great stuff!
|
|
|
 |
Brian S.
|
Posted: Sat 22 Aug, 2020 1:32 am Post subject: |
|
|
Man, you keep knocking it out of the park. I’m about ready to let my sword-brain take over and convince myself that my savings were just never really there
Jokes aside your exacting detail and choice of projects consistently leaves me stunned. It’s a strange quality that you seem to capture where things look historical and hand-made yet somehow flawless. Can’t wait to see what you do next.
|
|
|
 |
Leo Todeschini
Industry Professional

|
Posted: Tue 01 Dec, 2020 2:28 am Post subject: |
|
|
Nathan Robinson wrote Quote: | I saw this on Instagram just a few moments ago. It's one of the most amazing pieces I've seen. Wow, Tod, your game has soared to new heights!! I only wish I had the money to invest in your amazing offerings now days. You've really grown as a maker and artist. I'm super impressed, my friend.
Cheers. |
Thank you and that may be the case and I am flattered that you say it, but I can also tell you it is absolutely in large part to the presence of MA in my life for the last 14 years and what you see would not have been possible without you setting it up, the hard work of the moderators and the towering presence of the members.
Thank you all.
Tod
www.todsworkshop.com
www.todcutler.com
www.instagram.com/todsworkshop
https://www.facebook.com/TodsWorkshop
www.youtube.com/user/todsstuff1
|
|
|
 |
|