Author |
Message |
Dan D'Silva
|
Posted: Sun 13 Mar, 2016 1:54 pm Post subject: Adding flanges to a steel tang |
|
|
I've been pondering how one would recreate a certain dagger from Deve Huyuk (yes, I'm still going on about that). It's an iron continuation of older bronze styles with a flanged slab tang. My questions are from two angles:
1. When forging, would it have been more feasible to forge the flanges as one piece with the tang or to weld them on afterward? Would the latter leave them prone to delaminating?
2. If one made a replica by cutting and grinding a blank from steel plate, would it make sense, again, to weld flanges on? Or, even assuming such construction would be strong enough, would doing so bring the cost up so dramatically that you might as well have it hand-forged?
Attachment: 13.7 KB
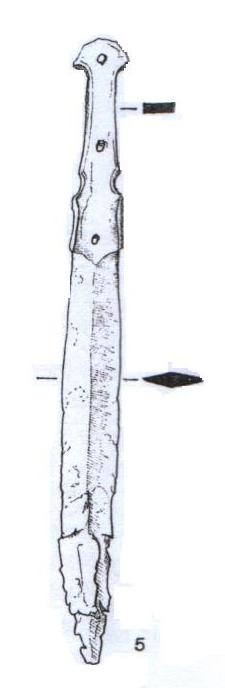
|
|
|
 |
Matthew Amt
|
Posted: Sun 13 Mar, 2016 2:53 pm Post subject: |
|
|
I used to wonder about flanges on iron hilts, too, but they're a piece of cake. Here's what I did on my own Naue II hilt, with only one brief experiment for practice, inadequate tools, and no training:
I think that took 15 or 20 minutes. A little filing and sanding gave me this:
This is scrap mild steel, 1/4" thick to begin with but I had presumably thinned the hilt area somewhat already. I just left it a little extra wide when I cut it out to allow for the flanges. And I'm sure a trained smith could do it much better and faster than I could! My flanges are not as wide as some originals.
Trying to weld the flanges on will be a HUGE amount of fuss and work, by comparison. Grab a hammer and go for it!
Matthew
|
|
|
 |
Timo Nieminen
|
Posted: Sun 13 Mar, 2016 3:32 pm Post subject: |
|
|
I have an unmounted Khyber knife blade where the flange appear to be brazed or soldered on. If the grip is held on by rivets, then the flange isn't going to have to resist much force, so brazing/soldering should be easily strong enough. Given that the T-spine of the blade is forged, I'm sure that the maker would have been able to forge the tang flange as well if it was desired.
That's a 19th century solution, and doesn't necessarily say much about solutions of more than 2000 years earlier, but it shows that it's a functional solution, and would work for a replica.
"In addition to being efficient, all pole arms were quite nice to look at." - Cherney Berg, A hideous history of weapons, Collier 1963.
|
|
|
 |
Dan D'Silva
|
Posted: Mon 14 Mar, 2016 4:38 am Post subject: |
|
|
Okay. Thanks!
|
|
|
 |
James Gibson
Location: Mobile Alabama Joined: 24 Jan 2016
Posts: 7
|
Posted: Mon 14 Mar, 2016 5:35 pm Post subject: |
|
|
Dan. If you have a proper forge take the time to forge the flange in with a hammer. It will be stronger and it will look better. Either way go for it. Even if you mess up you still learn. I have learned a hell of a lot from my mistakes over the years.
Occam's razor was a bastard sword
|
|
|
 |
Dan D'Silva
|
Posted: Tue 15 Mar, 2016 4:42 am Post subject: |
|
|
To be perfectly honest, I'm not planning on making one in the foreseeable future, nor do I have a forge. I'd certainly like one someday, but I'd prefer it in bronze. Right now this is more theoretical planning for people interested in historical reenactment.
|
|
|
 |
Matthew Amt
|
Posted: Tue 15 Mar, 2016 5:51 am Post subject: |
|
|
Rats, now we're all disappointed, ha!
I did mine cold, for the most part. Actually I had left too much metal for the job so the whole thing was too wide, so I ground off the first flange and re-hammered it. But at that point I was worried about cracks, so I tried annealing with my little MAPP gas torch. I don't think I got any glow, really, or if it made any real difference, but it didn't crack!
There was quite a bit of hammering and other finishing work done on some types of bronze weapons. The complex flanges on a Mycenaean Type G hilt that actually enclose the ends of the guard were hammered shut after casting. So those tips are hollow, not solid cast like most repros.
Matthew
|
|
|
 |
Dan D'Silva
|
Posted: Wed 16 Mar, 2016 10:35 am Post subject: |
|
|
Matthew Amt wrote: | I did mine cold, for the most part. Actually I had left too much metal for the job so the whole thing was too wide, so I ground off the first flange and re-hammered it. But at that point I was worried about cracks, so I tried annealing with my little MAPP gas torch. I don't think I got any glow, really, or if it made any real difference, but it didn't crack! |
That's good to know. I had been thinking of asking you about that. I think that some annealing can take place at least on the surface without any visible glow; I'm pretty sure I've managed to do so while trying to cut threads on a tang.
I almost want to consider applying the same process to bronze... but between buying the equipment and learning to do it well, it probably wouldn't be cheaper than having it cast unless I were doing lots of them.
|
|
|
 |
Dan D'Silva
|
Posted: Mon 28 Mar, 2016 4:42 am Post subject: |
|
|
Actually, I think I'm gonna go for it.
Whaddya think, 1/4-inch stock? 3/16?
Attachment: 163.12 KB
[ Download ]
|
|
|
 |
Matthew Amt
|
Posted: Mon 28 Mar, 2016 6:31 am Post subject: |
|
|
Dan D'Silva wrote: | Actually, I think I'm gonna go for it. |
Yay!
Quote: | Whaddya think, 1/4-inch stock? 3/16? |
Those work for the blade, but apparently for Greek and Western weapons the hilt area was more like 1/8", so you have to grind it thinner. THEN flange the edges.
Obviously if you were forging this all from a piece of stock, thinning and flanging would be part of the same process. We grinders have to start with something that's the wrong shape, make it into another wrong shape, then make it into the right shape!
Well, it wouldn't be fun otherwise, eh?
Matthew
|
|
|
 |
|
You cannot post new topics in this forum You cannot reply to topics in this forum You cannot edit your posts in this forum You cannot delete your posts in this forum You cannot vote in polls in this forum You cannot attach files in this forum You can download files in this forum
|
All contents © Copyright 2003-2025 myArmoury.com All rights reserved
Discussion forums powered by phpBB © The phpBB Group
Switch to the Basic Low-bandwidth Version of the forum
|