Author |
Message |
Johan Gemvik

|
Posted: Sun 29 Jan, 2012 7:31 am Post subject: Pressblech toolmaking |
|
|
I've been talking to Bruce who posted that most excellent Staffordshire seax with a decoratively plated Bjärs 17 scabbard, and it's inspired me to get off my behind and finally make the effort to put together a Valsgärde seax with pressblech plates and all.
Well, actually pressblech stuff is useful for making all sorts of Anglo Saxon, Vendel and viking goodies of course, not just scabbards. Belts, helmet plates, arm bands, various other jewelry and so on. Some here like Thorkil already make these, his helmets are legendarey here, though I haven't seen what the tools might look like. It sure looks good though and is most inspiring.
To make pressblech plates I need to first be able to make my own tools for it. One could possibly laser something from the photos of the finds, but I'd want it to be as authentic as possible to show the method at demos and such.
So the questions that need answers are:
What materials were used historically?
Exactly what did they look like?
How does this work -do you need a positive and negative or can one use a single side stamp/ die?
How thin does the brass or bronze need to be for this to work?
How long will a tool like this last?
Fist off, what materials were used, how did the tools work and what did they really look like historically?
I always imagined a massive lump of tempered steel, or at least wrought iron with one face carved with the design to be pressed, like we see for coinmaking. But having searched for a few hours with friendly google I've come across several examples that are fairly thin bronze plates, kind of what we see today as cast plate belt fittings more than the large massive thing I was imagining.
Have a look at these:
Source link:
http://www.flickr.com/photos/finds/2049150461/
Source link:
http://finds.org.uk/database/artefacts/record/id/133399
Source link:
http://www.time-lines.co.uk/anglo-saxon-zoomo...692-0.html
These are listed as cast copper alloy, so bronze, brass or red metal could work good for a modern repro of them. Thickness seems to be about 2-4 mm.
Anyway, let's discuss this! I bet a lot of people here have thought about these kinds of plates and how they're made. They're the ultimate bling for ones kit after all.
"The Dwarf sees farther than the Giant when he has the giant's shoulder to mount on" -Coleridge
|
|
|
 |
Matthew Amt
|
Posted: Sun 29 Jan, 2012 8:17 am Post subject: |
|
|
Ave!
I always figured these were done in a similar way to stamped Roman belt plates, of which I have made quite a few. I use cast brass "positive" dies about 3/8" to half an inch thick, with a lead block "negative" die. The plates are .010" brass, well annealed, and the stamping is done with a 3-pound hammer. The process is briefly covered on my Legio XX page on Belts: "Dies for stamping plates begin with a mockup sculpted from modeling clay or wax, simply a flat block about a half-inch thick with the design raised on one face. This mockup is then used to cast the "positive" half of the die in brass or bronze. The "negative" half of the die is made by floating the positive half face-down in molten lead, which is allowed to cool so that it retains the impression of the positive die. (Small holes can be drilled through the edges of the positive die at the corners for wires to suspend it at the right depth in the lead.)
"Blanks for the plates are cut from .010" brass, annealed, and polished. Place one face-down in the impression in the lead negative, place the positive die on top (making sure it is properly aligned!), and give six or seven solid blows with a 3-pound hammer."
http://www.larp.com/legioxx/balteus.html
You can see some of my plates there, and here's a (not-very-good) photo of 3 of the 4 types I can make:
http://www.larp.com/legioxx/bltplts.jpg
So yes, making the die is the first step. Luckily my lovely wife is an artist, so she did the Sculpey mockups for my dies, and I just sent them to a foundry to be cast. I did try getting one negative die half cast in brass, too, but with shrinkage and warpage it's almost impossible to get a really good set of dies that way. In this case I use it after the lead die to sharpen up some details, but used alone it wouldn't give the entire design. After hundreds of belt plates, only one of my dies is showing any sign of cracking, and for all I know even that one will last for many more plates.
I would agree that the items you posted could indeed be stamps or dies. At least one Roman belt plate stamp has been found, and it is made with a thick shank, like a coin die. From what I've seen, pressblechs have a lower relief but more sharp detail than the plates I've made, and I suspect they are thinner metal, too, more like heavy foil. So it's no surprise to me that those suspected stamps are thinner than my belt plate dies. The ancient craftsmen may have stamped into a cast lead negative, like I do, or onto the smooth surface of a lead block (I do that to make the brass rosettes seen on Roman helmets and lorica segmentata), or they might have backed their work with leather, pitch, or wood. Sometimes when I'm not getting some details with a few hammerstrokes, I'll lay the plate on the positive die and go at it with the corner of a chunk of lead, just hitting the bits that need it. So it's possible that these pressblech dies were laid flat, face up, and the plate hammered down onto them. They would take a lot less abuse that way.
Oh, here's a photo of the Roman rosettes I make, along with the tools:
http://www.larp.com/legioxx/dies2.jpg
On the left is my current die, cast from brass by a friend of mine. At top is my original die, just a piece of brass rod (from a door handle) with the end rounded and grooves filed across. For that I first stamped the blank with the ring to get a nice raised edge, then the floral die. The old die was used to make the mockup for the new one, and I added the pearled rim. At right is a 1" leather punch used to punch out the brass discs. After a few rounds of stamping discs, the lead slab gets too badly marred or starts to break up, and I just remelt it.
Aha! Old die and new die:
http://www.larp.com/legioxx/dies1.jpg
Coulda sworn I had a nice photo of my belt plate dies, hmmm....
I realized years ago that doing the plates for a Sutton Hoo or Vendel helmet wouldn't be hard. All I had to do was buy a few cast plates from Raymond's Quiet Press to use as dies, and start stamping. Doing the little ridged brass strips that hold the plates down is actually what worries me more! It's a project which is definitely on my list, should I ever be able to justify the expense of those plates for dies. TEMPTING!!
Well, I hope that is helpful! Looking forward to what you come up with.
Matthew
|
|
|
 |
Mark Shier
Industry Professional
|
Posted: Sun 29 Jan, 2012 1:55 pm Post subject: pressblech |
|
|
There have been some suggestions that some things, like bracteates http://www.britishmuseum.org/explore/highligh...ate-1.aspx , were hammered into wood dies, probably endgrain hardwoods such as holly.
I usually use scrap brass for my dies, even though I do a lot of casting. I carve the dies using a flex shaft tool, but you could use engraving tools. I've used brass nut heads for bracteate dies.
If you don't like using a lead hammering pad, try thick leather.
mark
Attachment: 44.56 KB
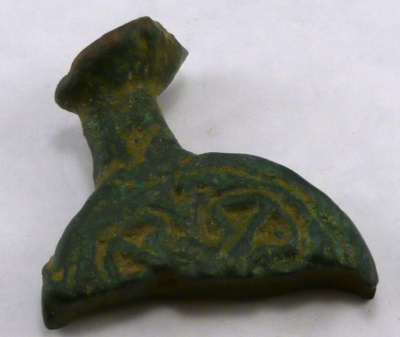
Pressblech die in my collection. A failed casting. 3.7cm wide.
Attachment: 67.2 KB
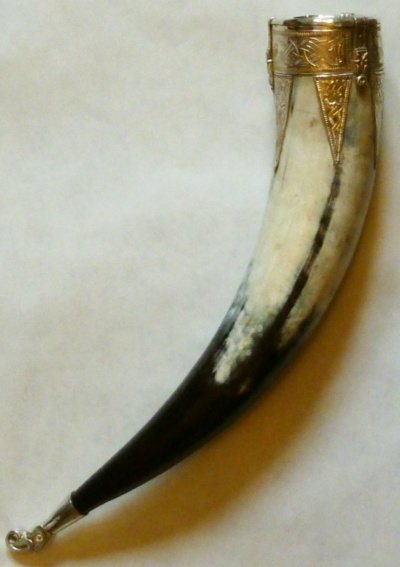
Drinking horn.
Attachment: 60.11 KB
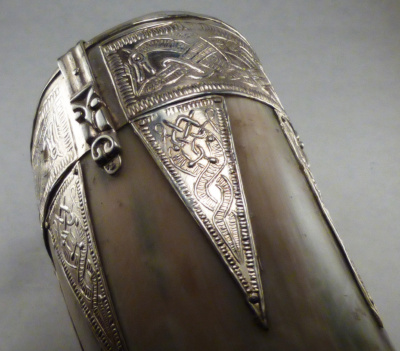
Sterling silver castings and fine silver pressblech on a drinking horn.
Attachment: 53.89 KB

Brass die for drinking horn bits.
Gaukler Medieval Wares
http://www.medievalwares.com
|
|
|
 |
Matthew Bunker

Location: Somerset UK Joined: 02 Apr 2009
Posts: 483
|
Posted: Mon 30 Jan, 2012 1:36 am Post subject: |
|
|
Matthew Amt wrote: | I suspect they are thinner metal, too, more like heavy foil. |
Correct. The average thickness of pressbleched foils in a study by Duczko was found to be 0.2mm.
With foils that thin, you don't need a negative die. I've watched Dave Roper hammering out pressblechs on site and he lays the foil over the die and then a thin sheet of lead flashing over the top of that and hammers away.
Quote: | ttle ridged brass strips that hold the plates down is actually what worries me more! |
EASY, once you figure out the tooling.
There's a fantastic set of Viking period copper alloy dies in the museum at Hedeby, found in the harbour. I bet someone regretted dropping that box as they left the ship.
http://s418.photobucket.com/albums/pp263/medi...nt=409.jpg
This is an excellent paper for anyone interested in pressblechs and any other aspect of early medeival metalwork:-
http://www.scribd.com/doc/52879626/2/Decorati...of-Surface
"If a Greek can do it, two Englishman certainly can !"
|
|
|
 |
Matthew Bunker

Location: Somerset UK Joined: 02 Apr 2009
Posts: 483
|
Posted: Mon 30 Jan, 2012 1:43 am Post subject: Re: Pressblech toolmaking |
|
|
Johan Gemvik wrote: | So the questions that need answers are:
What materials were used historically?
Exactly what did they look like?
How does this work -do you need a positive and negative or can one use a single side stamp/ die?
How thin does the brass or bronze need to be for this to work?
How long will a tool like this last?
|
1. I've seen dies made from copper alloy, bone and antler. I've also heard that dies of wood have been found.
2. Varies. See the article I posted a link to in my previous post.
3. Positive die, foil over the top, soft medium over the top of that (lead flashing for roofs seems to be ideal and easy to get hold of. Usual caveats apply when working with lead). Hit it with a mallet.
4. 0.2mm or thinner is best. you might get away with thicker if you anneal it.
5. No idea.
"If a Greek can do it, two Englishman certainly can !"
|
|
|
 |
Johan Gemvik

|
Posted: Mon 30 Jan, 2012 4:56 am Post subject: |
|
|
Thanks guys! You've all been amazingly helpful, far more than I expected on the subject even!
I'll try the lead plate. That's if they still sell it in Sweden, the europeean ROHS directive forbids all lead after all. If I can't get that I'll just try something else similar to it. Tin maybe.
0.2 plate foil is about the thickness I figured. I have some 0.5 brass plate I use for knife sceath fitting details and it seems a bit on the thick side for something like this. It's very springy and stiff. I could anneal it as suggested of course to make it softer, but since the finds show 0.2 I'd want to go with that anyway for historical accuracy reasons, with the added benefit of it being easier to form.
This is exciting! I'll make some sculpey originals for tool casting later this week. I might try the cutting/engravng method Mark showed as well.
"The Dwarf sees farther than the Giant when he has the giant's shoulder to mount on" -Coleridge
|
|
|
 |
Johan Gemvik

|
Posted: Mon 30 Jan, 2012 5:27 am Post subject: |
|
|
I see the thead was moved. Good call gentle mods!
Looking back, this obviously belongs in the OT not under weapons. Thanks.
"The Dwarf sees farther than the Giant when he has the giant's shoulder to mount on" -Coleridge
|
|
|
 |
Matthew Bunker

Location: Somerset UK Joined: 02 Apr 2009
Posts: 483
|
Posted: Mon 30 Jan, 2012 5:44 am Post subject: |
|
|
Johan Gemvik wrote: |
I'll try the lead plate. That's if they still sell it in Sweden, the europeean ROHS directive forbids all lead after all. If I can't get that I'll just try something else similar to it. Tin maybe.
|
ROHS doesn't forbid all lead at all. It can still be used for roofing for example, that's why lead flashing is a suitable material.
http://www.wickes.co.uk/lead-flashing/invt/241450/
Lead free 'pewter' sheet might do the job I suppose.
"If a Greek can do it, two Englishman certainly can !"
|
|
|
 |
E. Storesund
|
Posted: Thu 02 Feb, 2012 11:59 am Post subject: |
|
|
As mentioned above, I remember looking at bracteates figuring that they looked like negatives of woodcarving. Thank you everybody for all this useful information. I always wondered if I could give this a go some day, and given the current information I believe the answer to be yes.
|
|
|
 |
Johan Gemvik

|
Posted: Sun 05 Feb, 2012 3:31 pm Post subject: |
|
|
You and me both E. I always wanted to do this!
"The Dwarf sees farther than the Giant when he has the giant's shoulder to mount on" -Coleridge
|
|
|
 |
|
You cannot post new topics in this forum You cannot reply to topics in this forum You cannot edit your posts in this forum You cannot delete your posts in this forum You cannot vote in polls in this forum You cannot attach files in this forum You can download files in this forum
|
All contents © Copyright 2003-2025 myArmoury.com All rights reserved
Discussion forums powered by phpBB © The phpBB Group
Switch to the Basic Low-bandwidth Version of the forum
|