Author |
Message |
Jeff Pringle
Industry Professional
|
Posted: Tue 25 Jan, 2011 11:55 pm Post subject: Introducing Jim Austin: axe, seax and swordsmith |
|
|
I’d like to introduce my good friend Jim to the community, he’s a remarkably skilled smith who is one of my main collaborators in the recovery of obsolete technology. He is a professional smith with a lot of historically-informed forging experience, including a number of beautiful pattern-welded seax and swords.
We’ve been intensely studying Viking-age axes in the last year, and Jim has been doggedly reverse-engineering the forging processes hinted at by subtle clues in the artifacts of that era, with (of course ) the goal of truly recapturing the presence and feel of those marvelous weapons.
Here is some of what he has come up with… I think he’s got photos of his beared- and Baltic-style axes as well.
Attachment: 43.19 KB

Attachment: 37.39 KB
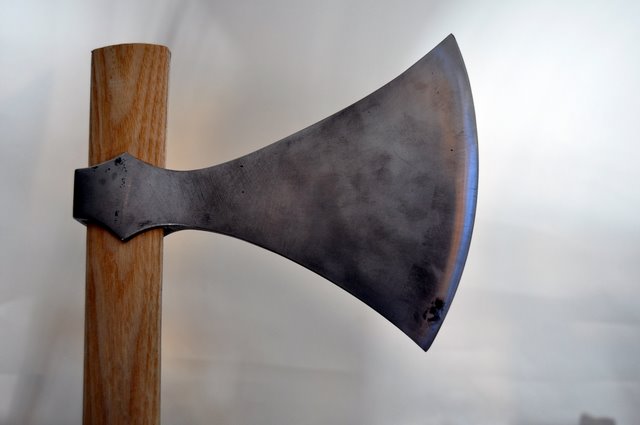
Attachment: 32.41 KB
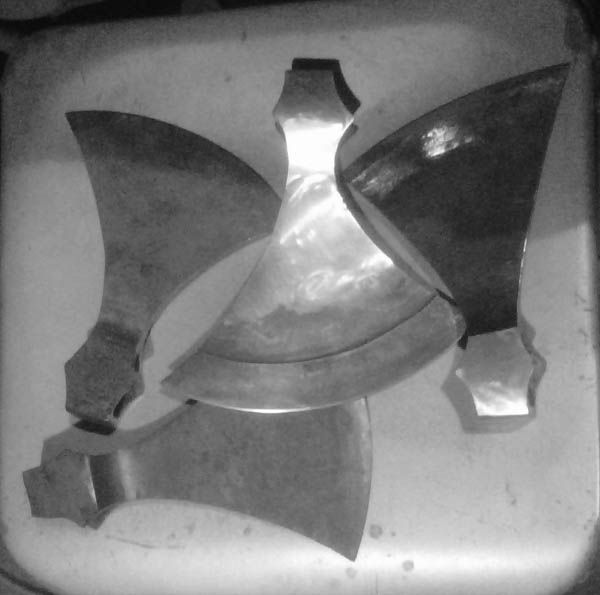
|
|
|
 |
Owen Bush
Industry Professional
|
Posted: Wed 26 Jan, 2011 12:42 am Post subject: |
|
|
It is beautiful work .
I have enjoyed watching jim and your work in this area .
Very inspirational .
The top Dane axe is a real beauty .
forging soul into steel .
www.owenbush.co.uk the home of bushfire forge school of smithing .
|
|
|
 |
Ryan Renfro

|
|
|
 |
Richard Furrer
Industry Professional

|
Posted: Wed 26 Jan, 2011 7:30 am Post subject: |
|
|
I am rather envious of what the two of you have been up to together..and separately as well.
I can see the future when they find the "Hoards of Oakland".
Will you two make a combined stamp to mark and commemorate these pieces? Some late medieval work had wonderful maker stamps.
Ric
Ric Furrer
Sturgeon Bay, WI
www.doorcountyforgeworks.com
|
|
|
 |
Ken Speed
|
Posted: Wed 26 Jan, 2011 12:45 pm Post subject: |
|
|
So Jeff, are you going to share a website address with us or just torture us with pictures of his work?
|
|
|
 |
Matthew Stagmer
Industry Professional
|
Posted: Wed 26 Jan, 2011 3:29 pm Post subject: |
|
|
I too am envious of the work you 2 are putting out. I just recently speant a day digesting your thread on Foggs.
Awesome work. Jim is very skilled with a power hammer. Im loving the axes you two are turning out. The research is key. I would have never thought that many pieces were wrapped like that. I would have assumed most were drifted.
Jim + Jeff = JJ stamp ?
Matthew Stagmer
Maker of custom and production weaponry
Youtube.com/ThatWorks
|
|
|
 |
R D Moore

|
Posted: Wed 26 Jan, 2011 5:44 pm Post subject: |
|
|
Welcome to the forum Jim! I'm surprised you've evaded us! We're very fortunate to have you both on the forum. Check that link Ryan posted folks, you wont ever be the same again!
"No man is entitled to the blessings of freedom unless he be vigilant in its preservation" ...Gen. Douglas Macarthur
|
|
|
 |
Jim Austin
Industry Professional
|
Posted: Fri 28 Jan, 2011 9:16 am Post subject: |
|
|
Thanks for the introduction, Jeff, and sorry for the delay in joining the fray. I have been getting ready to teach a 6 session course in Viking axe making at my own shop and it's been keeping me up late.
I think that Jeff neatly summarized our efforts in trying to shed some light on how some axes may have been forged back in the day. I find axes particularly fascinating as technical forging exercises because they pack so much technique into such a small and beautiful object. So far I've been sticking with one process to form the eyes of the axes (splitting the back of the axe into a Y, wrapping it on a mandrel and forge welding the eye closed at the poll). Clearly there are more common welding techniques such as the asymmetric wrap and axes which are punched and drifted. I will get to these at some point - hopefully sooner rather than later. I have been forge welding the bits (The bits are 1070 and the body is 1018) into a cleft formed by splitting the front of the blade with a chisel. The point of making numerous axe heads so far has been to explore forms and test out successively developed ideas on the forging and forge welding sequences. I have kept close notes on most of the trials (about 15 to date) and have a nice pile of axe heads to show for it. I would like to start selling these as soon as I have a makers mark to stamp them with (it's on the way). All in all it has been great fun and a great education. I have included a few pictures of various axe heads below and will try to keep the pictures coming.
Thanks for you interest.
A note about the pictures: The grid, where it appears, is 1". Some axes show temper colors on the steel bit.
Attachment: 31.31 KB
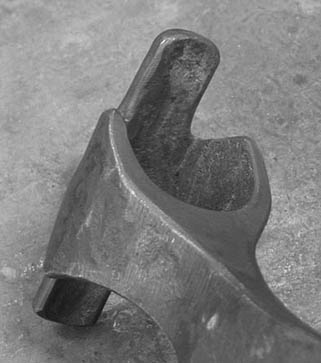
Attachment: 23.05 KB
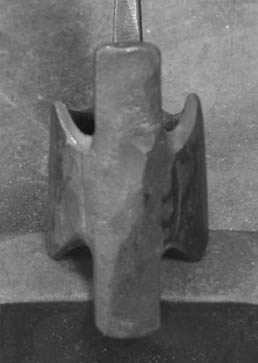
Attachment: 48.14 KB
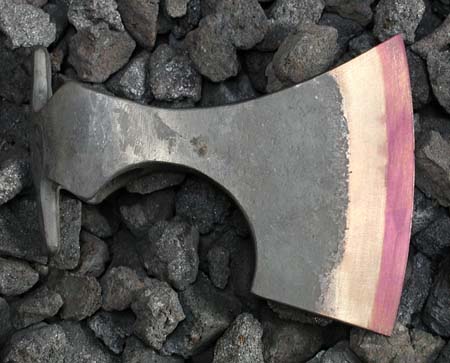
Attachment: 22.18 KB
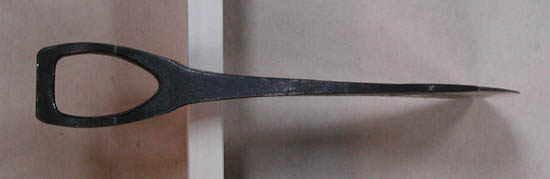
Attachment: 40.24 KB
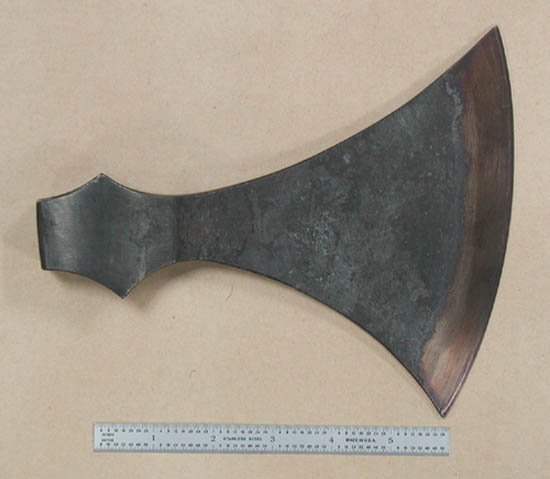
Attachment: 41.56 KB

Last edited by Jim Austin on Fri 28 Jan, 2011 10:36 am; edited 1 time in total
|
|
|
 |
Jeremy V. Krause
|
Posted: Fri 28 Jan, 2011 9:47 am Post subject: |
|
|
Hi Jim,
What are you using for the blade body of the axes- wrought?
I have read that some axes, specifically Danish axes may have been divided into a socket, blade body, and finally, edge. Do you have any plans to construct axes using this or other historical methods?
|
|
|
 |
E Sideris
|
Posted: Fri 28 Jan, 2011 6:30 pm Post subject: |
|
|
Having stood transfixed, watching Jim work his magic, I can only say that he truly knows what the hell he's doing and it's awesome.
Jim, mind if I post some pictures of you forging these axes?
|
|
|
 |
Matt Corbin

|
Posted: Sun 30 Jan, 2011 2:03 pm Post subject: |
|
|
Welcome to myArmoury Jim. It's good to have you here. And the axes are fantastic
“This was the age of heroes, some legendary, some historical . . . the misty borderland of history where fact and legend mingle.”
- R. Ewart Oakeshott
|
|
|
 |
Jeff Pringle
Industry Professional
|
Posted: Sun 30 Jan, 2011 4:07 pm Post subject: |
|
|
Jeremy V. Krause wrote: |
I have read that some axes, specifically Danish axes may have been divided into a socket, blade body, and finally, edge. Do you have any plans to construct axes using this or other historical methods? |
From the beginning, our plan has been to start with Viking-era artifacts that show traces which reveal construction details, work out the proportions & precursor forms in modern steel (1018/1070 for the most part), do a few in wrought iron and then make prime examples in bloomery iron/steel. We started with the weld on the back of the socket method because it is an elegant solution which (as far as I have found) is not mentioned in the literature on axes. We have both started thinking about & doing test forgings on what I have been calling the ‘asymmetric wrap” method, so that is probably next up. I have not run across any archaeological papers which describe this socket/body/edge method (usually the socket is formed of the same material as the body), do you have any illustrations which might further explain what they meant?
|
|
|
 |
|