Author |
Message |
Tim Lison
|
Posted: Tue 14 Dec, 2010 4:41 pm Post subject: |
|
|
Wow! Well done Kirk! This looks terrific. I'm curious to know why you stuck with the wire grip, wouldn't leather wrapped be more accurate?
|
|
|
 |
Felix Dale

Location: wales (only studying here) Joined: 16 Sep 2009
Posts: 23
|
Posted: Tue 14 Dec, 2010 4:48 pm Post subject: |
|
|
It is beautyful! *wipes away tear*
Thats what being a gentleman is all about!
|
|
|
 |
Hadrian Coffin
Industry Professional
Location: Oxford, England Joined: 03 Apr 2008
Posts: 404
|
Posted: Tue 14 Dec, 2010 4:57 pm Post subject: |
|
|
Hello,
I personally cannot comment as to why Mr. Spencer choose to use the wire wrap, but it does have historical basis. There are several wire bound grips from the Viking period. Other grips and coverings seem to be more common, but a configuration such as this is not wrong.
I think the artificial pattern welding looks perfect. It is a bit unnerving; I could see this being exploited by con artists. Nonetheless I think it is a very clever idea, and definitely improved the sword.
Cheers,
Hadrian
Historia magistra vitae est
|
|
|
 |
Tim Lison
|
Posted: Tue 14 Dec, 2010 6:34 pm Post subject: |
|
|
Hadrian-
Oh. Thanks, I didn't know that Vikings used wire wrap grips. It looks great!
|
|
|
 |
Carl W.
|
Posted: Wed 15 Dec, 2010 6:48 am Post subject: |
|
|
Kirk - Thanks! I had read etching can be pretty fragile, but your cut & cleanup is some opposite evidence.
You painted etchant on gladius, a side at a time. Appears you gave this viking a bath - twice? If so how did you protect the (finished) reverse side during the 2nd bath?
Its your hobby, the results are beautiful, & you are not trying to fool anyone. Plus, considered original smith's work. Very well done.
|
|
|
 |
Johan Gemvik

|
Posted: Wed 15 Dec, 2010 7:53 am Post subject: |
|
|
Well done!
I've been thinking about how something like this could be done. Hot mustard indeed!
"The Dwarf sees farther than the Giant when he has the giant's shoulder to mount on" -Coleridge
Last edited by Johan Gemvik on Wed 15 Dec, 2010 8:27 am; edited 1 time in total
|
|
|
 |
Johan Gemvik

|
Posted: Wed 15 Dec, 2010 8:13 am Post subject: |
|
|
Hadrian Coffin wrote: | Hello,
I personally cannot comment as to why Mr. Spencer choose to use the wire wrap, but it does have historical basis. There are several wire bound grips from the Viking period. Other grips and coverings seem to be more common, but a configuration such as this is not wrong.
I think the artificial pattern welding looks perfect. It is a bit unnerving; I could see this being exploited by con artists. Nonetheless I think it is a very clever idea, and definitely improved the sword.
Cheers,
Hadrian |
Wire wraps from viking times are indeed pretty common on finds, usually silver or gold single thread non-twisted thread, but some have dual or multiple wires twisted together. Single thread wrap can be seen in quite a few finds, a few good examples are Icelandic finds from Kaldárhöfða and Hafurbjarnarstöðum, as well as the swedish "Dybeck" sword. Some Norwegian finds have twisted multiple thread wrap, and this one had an original from Norway so it's plausible it had such a wrap.
The type of wide flat pattern Spencer removed was too modern though and a good call. Overall he's done a fine and brave job of making an already impressive sword even more authentic.
I too feel that if it's possible by such simple means to reproduce a pattern weld look one might question the authenticity of some swords being sold as such today. Especially those with lower pricetags. But then perhaps some swords back then were also faked this way, they may be as authentic in their own way as anything else. And it's always much better that we know about it, that it can be done and how. Today quality monosteel that's differentially heat treated properly are often stronger than pattern welded swords, so for safety in demonstration cutters this optoion may even be preferable.
Perhaps this method is something for companies like Albion to look into, I mean selling it not as true pattern weld but stated as simulated pattern weld, as an option for their Anglo Saxon and Viking sword models.
"The Dwarf sees farther than the Giant when he has the giant's shoulder to mount on" -Coleridge
|
|
|
 |
Jeff Pringle
Industry Professional
Location: Oakland, CA Joined: 19 Nov 2005
Posts: 145
|
Posted: Wed 15 Dec, 2010 9:13 am Post subject: |
|
|
That looks great, Kirk!
Looks like it may have been more work than pattern-welding a blade, too
|
|
|
 |
Kirk Lee Spencer

|
Posted: Wed 15 Dec, 2010 10:53 am Post subject: |
|
|
Jean, Matt, David, Michael and Felix...
You guys are great!
Thanks so much for the encouragement
I knew I was taking a chance on such a fine sword, but I had Vlad Cervenka make it for me this this in mind... However, this technique could be used on any steel blade.
take care
ks
Two swords
Lit in Eden’s flame
One of iron and one of ink
To place within a bloody hand
One of God or one of man
Our souls to one of
Two eternities
|
|
|
 |
Kirk Lee Spencer

|
Posted: Wed 15 Dec, 2010 11:08 am Post subject: |
|
|
Nils Anderssen wrote: | That is a fantastic piece of work
I realy like that you put so much time into making it look realistic, with all its imperfections... done the right way
It is something that is realy hard to do, and most people don't get it right...
Also... it means to go against our modern symetrical and "perfect" visual rules/guidelines... which needs some guts
For a better picture of the Arhus sword (15mb):
http://www.vikverir.no/ressurser/extreme_hd_swords/sword_5.jpg
This was original ment to be for a later update of Vikverirs museum gallery, and I am sorry that I did not post it earlier. I gues the sword ha been cleaned by the musem since it does not have any rust on it.
Also thanks for the in depth description of your experience with it
I realy have to try that out one day (a blunt wma/re-enactment sword?)...
Nils |
Hey Nils...
It is great to hear from you. I have been wanting to thank you for your part in the VIKVERIR website. That is one fantastic resource! Those close shots of the ornamentation details are mesmerizing... something I have been waiting to see for a long time.
Also thanks for the link to the over-sized image of the whole Arhus Farm find. If I had this image when I started this process, I probably would have tried to do a more exacting recreation of the blade pattern. It really shows the details of the pattern, far better than anything I have ever seen.
I'm glad you can appreciate the imperfect-worn look. I like the bright and pristine look on swords also , but, to me, they just don't seem to have much "life" to them. With the imperfections and the wear, the object just seems to be connected visually to events. For instance where the wires on the grip have been worn through, most might see this as a flaw. To me, it recalls the warriors hand that used the sword. I guess it is only an aesthetic thing at this point, but I like it.
take care
ks
Two swords
Lit in Eden’s flame
One of iron and one of ink
To place within a bloody hand
One of God or one of man
Our souls to one of
Two eternities
|
|
|
 |
Kirk Lee Spencer

|
Posted: Wed 15 Dec, 2010 11:13 am Post subject: |
|
|
Tim Lison wrote: | Wow! Well done Kirk! This looks terrific. I'm curious to know why you stuck with the wire grip, wouldn't leather wrapped be more accurate? |
Hi Tim...
Thanks.
Hadrian and Johan are exactly right. Wire wrap grips have been found on Viking swords. This is especially true of the Baltic area. Most of the time the wires are untwisted, but twisted wires have been found. Here is a link to a thread on Viking Grips which shows a couple of the better ones.
http://www.myArmoury.com/talk/viewtopic.php?t...mp;start=0
If I can find time, I'll try to update this thread with more.
take care
ks
Two swords
Lit in Eden’s flame
One of iron and one of ink
To place within a bloody hand
One of God or one of man
Our souls to one of
Two eternities
|
|
|
 |
Kirk Lee Spencer

|
Posted: Wed 15 Dec, 2010 11:29 am Post subject: |
|
|
Hadrian Coffin wrote: | Hello,
I personally cannot comment as to why Mr. Spencer choose to use the wire wrap, but it does have historical basis. There are several wire bound grips from the Viking period. Other grips and coverings seem to be more common, but a configuration such as this is not wrong.
I think the artificial pattern welding looks perfect. It is a bit unnerving; I could see this being exploited by con artists. Nonetheless I think it is a very clever idea, and definitely improved the sword.
Cheers,
Hadrian |
Hi Hadrian,
Thanks...
I often get such a reaction when I artificially age swords... There are certainly persons of ill repute who can try to deceive with artificially ages blades... especially with the rise of Ebay. I would hope that before anyone spent tens of thousands of dollars on an orginal pattern welded blade they would have it x-rayed. I think there are portable X-ray machines now.
It is interesting to me to see swords for sale as original finds which are finer than anything in the museums. In almost every case, there is one or more aspects of the sword which I have never seen on any sword from that particular era. This usually involves minimal but fancy engraving on the blade.
take care
ks
Two swords
Lit in Eden’s flame
One of iron and one of ink
To place within a bloody hand
One of God or one of man
Our souls to one of
Two eternities
|
|
|
 |
Kirk Lee Spencer

|
Posted: Wed 15 Dec, 2010 11:46 am Post subject: |
|
|
Carl W. wrote: | Kirk - Thanks! I had read etching can be pretty fragile, but your cut & cleanup is some opposite evidence.
You painted etchant on gladius, a side at a time. Appears you gave this viking a bath - twice? If so how did you protect the (finished) reverse side during the 2nd bath?
Its your hobby, the results are beautiful, & you are not trying to fool anyone. Plus, considered original smith's work. Very well done. |
Hi Carl...
Once you get topography (raised and lower areas) from the etch on a hardened, modern, mono steel blade, it is not fragile. I should know, I've sanded it off several times. It takes quite a bit of sanding to get it all smooth again.
It does look like I am painting, however, on the gladius, I am not painting the etchant on the blade. A painted layer would not have enough etchant to cut. I am using an eye-dropper and creating a long pool of etchant. The surface tension will allow it to pool, held in place by the edges of the Scotch Tape. You have to be careful and not bump it too hard or it will spill over the tape and you will need to add more. Then... it can get really messy. This is one more reason the duct tape reservoir method works better. Beyond, more etchant, whole fuller etched at the same time, less obvious "weld" line, deeper cut, beyond this it is much less messy). Also with the duct tape reservoir you can rock it back and forth a little to help the etchant move which I believe gives a better cut.
As for the other side to the blade... again the duct tape reservoir is great in that a layer of duct tape can be applied to the other side of the blade. When I was doing the Scotch Tape method, I coated the other side with Scotch Tape to keep any etchant that spilled from getting on the other side of the blade. This was a big mistake. It was extremely difficult to get it all off.
Hope this helps... and thanks for the interest.
If there are any other questions, just let me know.
take care
ks
Two swords
Lit in Eden’s flame
One of iron and one of ink
To place within a bloody hand
One of God or one of man
Our souls to one of
Two eternities
|
|
|
 |
Kirk Lee Spencer

|
Posted: Wed 15 Dec, 2010 12:22 pm Post subject: |
|
|
Johan Gemvik wrote: | Hadrian Coffin wrote: | Hello,
I personally cannot comment as to why Mr. Spencer choose to use the wire wrap, but it does have historical basis. There are several wire bound grips from the Viking period. Other grips and coverings seem to be more common, but a configuration such as this is not wrong.
I think the artificial pattern welding looks perfect. It is a bit unnerving; I could see this being exploited by con artists. Nonetheless I think it is a very clever idea, and definitely improved the sword.
Cheers,
Hadrian |
...I too feel that if it's possible by such simple means to reproduce a pattern weld look one might question the authenticity of some swords being sold as such today. Especially those with lower pricetags. But then perhaps some swords back then were also faked this way, they may be as authentic in their own way as anything else. And it's always much better that we know about it, that it can be done and how. Today quality monosteel that's differentially heat treated properly are often stronger than pattern welded swords, so for safety in demonstration cutters this optoion may even be preferable.
Perhaps this method is something for companies like Albion to look into, I mean selling it not as true pattern weld but stated as simulated pattern weld, as an option for their Anglo Saxon and Viking sword models. |
Hi Johan...
Thanks for your thoughts on this.
yeah.. Hot mustard. For some reason I kept wanted to eat hot dogs with this technique. Just needed some pickle relish. Ah.... Pickle Relish.... I wonder what that would do to a high carbon steel blade.
I know what you mean about ancient fakes. I have often wondered if some of the decoration you see was not an attempt at mimicking pattern welding.
[I have often thought it strange that of all the pattern welded blades I have seen none of them have had reverse twists stacked evenly... The reason I mention this is that, if done right, it would produce this pattern on the blade. XOXOXOXOXO.
No not hugs and kisses... Circles and Xs are very common design elements and it could be done with pattern welding with reverse twists of pilled layers every inch or so and then staking them evenly in two billets. This is one of the reasons that the lower billet of the Arhus Farm find is of interest, because near the forte it appears that the twist is reversed.]
And then there is that Type X blade found in the Nene River near Raven's Willow England which has VLFBERHT inlayed on one side and INGELRII on the other. This "faker" was certainly hedging his bets.
take care
ks
Attachment: 115.12 KB
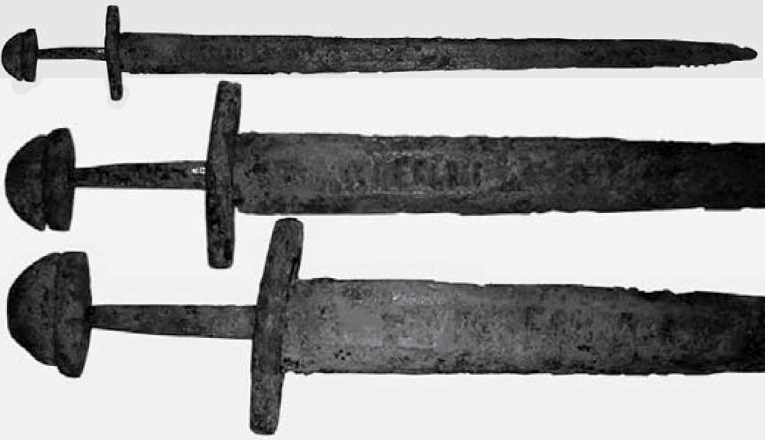
Image from "A METALLURGICAL STUDY OF SOME VIKING SWORDS," by Alan Williams from GladiusXXIX (2009) Great Reading
Two swords
Lit in Eden’s flame
One of iron and one of ink
To place within a bloody hand
One of God or one of man
Our souls to one of
Two eternities
|
|
|
 |
Kirk Lee Spencer

|
Posted: Wed 15 Dec, 2010 12:31 pm Post subject: |
|
|
Jeff Pringle wrote: | That looks great, Kirk!
Looks like it may have been more work than pattern-welding a blade, too  |
Wow!!!
Jeff Pringle thinks it looks great... What a compliment!
I am certain you could have done it for real faster than my fakery... but if I had tried to hammer it out myself, I would still be hammering away (or more likely be in the hospital with third degree burns.) Though I do go out in my garage sometimes and heat some steel with my propane torch and hammer on it. Especially in fall, when the air is cool and the iron is hot and the ring of the hammer... just something primordial about it all.
I do have great respect for your work and knowledge on the matter. As a matter of fact, the idea of the reverse twist (X and O) posted above comes from seeing a blade where you did this... I think it was on the BladeSmith's Forum Board.
Have a great Holiday and
Take care...
ks
Two swords
Lit in Eden’s flame
One of iron and one of ink
To place within a bloody hand
One of God or one of man
Our souls to one of
Two eternities
|
|
|
 |
Tim Lison
|
Posted: Wed 15 Dec, 2010 5:25 pm Post subject: |
|
|
Kirk Lee Spencer wrote: | Tim Lison wrote: | Wow! Well done Kirk! This looks terrific. I'm curious to know why you stuck with the wire grip, wouldn't leather wrapped be more accurate? |
Hi Tim...
Thanks.
Hadrian and Johan are exactly right. Wire wrap grips have been found on Viking swords. This is especially true of the Baltic area. Most of the time the wires are untwisted, but twisted wires have been found. Here is a link to a thread on Viking Grips which shows a couple of the better ones.
http://www.myArmoury.com/talk/viewtopic.php?t...mp;start=0
If I can find time, I'll try to update this thread with more.
take care
ks |
Kirk-
Thanks for the link to that thread about wire wrapped viking grips. I don't know how I missed that one. The sword looks great, I'm sure you'll enjoy it! I sure enjoyed seeing it.
|
|
|
 |
Owen Bush
Industry Professional
|
Posted: Fri 17 Dec, 2010 9:08 am Post subject: |
|
|
that is an amazing job .
I was amazed at the evenness of the patternwelding the way the lines from the two twists line up is amazing looks like snakes running down the blade......
there is only one bit of it all where you have a scroll in the back edge bar that does not look real .
you have it nailed . I must ask how long it all took , as it looks like an awfull lot of work and I think that patternwelding could actually be easier .
very good work , not sure If i should be congratulating someone for making fake patternweld but i think you have done a wonderfull job .
All the best Owen
forging soul into steel .
www.owenbush.co.uk the home of bushfire forge school of smithing .
|
|
|
 |
Tom Carr

|
Posted: Sat 18 Dec, 2010 12:23 pm Post subject: |
|
|
Good grief! Kirk! This is stuning work! Its not even the same sword anymore. I remeber when you first got it. It handled so well. I cant imagine how it handles now with all the work done to it. Bravo!
|
|
|
 |
Jeremy V. Krause
|
Posted: Sat 18 Dec, 2010 4:56 pm Post subject: |
|
|
Thanks for sharing kirk!
You are really an artist with these projects. I gave up on antiquing my Del Tin because I couldn't get off all of that *&^% lacqquer!! ARGH!!
|
|
|
 |
Jean Thibodeau

|
Posted: Sat 18 Dec, 2010 5:24 pm Post subject: |
|
|
Jeremy V. Krause wrote: | Thanks for sharing kirk!
You are really an artist with these projects. I gave up on antiquing my Del Tin because I couldn't get off all of that *&^% lacqquer!! ARGH!! |
Finger nail polish remover works like magic removing the lacquer. ( Got that this from Nathan Robinson a while back ).
You can easily give up your freedom. You have to fight hard to get it back!
|
|
|
 |
|