Author |
Message |
Luka Borscak

|
Posted: Tue 19 Oct, 2010 4:41 pm Post subject: Hanwei Saxon, full review with cutting video |
|
|
HANWEI SAXON – Reviewed by Luka
When I first saw this sword linked on the SBG (old forum) and realized it might really be pattern welded, I knew I must have it. I'm looking for a pattern welded blade i can afford for a few years now and I have owned Hanwei Godfred but its blade construction and pattern weren't historical and during the cutting it got a long shallow crack near the tip, so I got rid of it and started searching from the beginning. The Saxon ended this search, at least until I have 1000 euros to blow on a sword… This was also my frist time buying a sword online without handling it so I was quite a bit anxious. I went with Kult of Athena because they had the lowest price by far, $310,95, and I didn't regret.
Historical overview:
Hanwei is with this model trying to replicate this sword from the Yorkshire Museum:
http://www.yorkshiremuseum.org.uk/assets/coll...hi-res.jpg
http://www.yorkshiremuseum.org.uk/assets/coll...hi-res.jpg
As you will see the hilt is replicated quite well, although the original's decoration was silver I think and was surely executed much crisper and nicer when new than Hanwei's and the original didn't have iron parts of the hilt blackened like Hanwei did with theirs. Also, I'm not sure, but since the original is 9th century, it probably had two piece pommel and Hanwei of course has upper part and pommel made in one piece. All in all the hilt visually is quite similar to the original but some details are not historically accurate.
The blade of the original is of a design new for 9th century, well tapered and quite pointy, and here the original and Hanwei swords differ the most. I don't know if the original is pattern welded.
Now that differences between the original and Hanwei's sword are dealt with, I will focus on the Hanwei itself. The hilt type is Petersen type L. This type was, because of Trewhiddle style of decoration specific for Anglo Saxons, classified as a native Anglo Saxon type, but since many of the L's are found in Norway, and many without decoration, it might be that it's just a type well accepted by Anglo Saxons in their contact with Vikings so they started to replicate it and decorate it with their own style of decoration. But we can't know for sure. The dating of this variation of the type L is second half of the 9th century and early 10th, while other L variants are more typical for the first half of the 10th century (for example the famous Leuterit sword found in Witham river and replicated by Windlass and Gen2).
The blade of Hanwei Saxon is a Geibig type 1:
http://www.myArmoury.com/view.html?features/pic_geibig05.jpg
It's a blade type made until about 800AD so it is cerainly not a blade that would be made new for the type L hilt, but of course it's quite usual for the viking age sword to have much older blades rehilted with new and fashionable hilt types. So this blade might have been made anytime from 500 to 800AD and rehilted many times before finally getting the type L hilt in the second half of the 9th century with which we might unearth it somewhere in the North.
The package
I never remember to picture the box and packing before the opening so you won't see them. Standard Hanwei box inside a bigger box and padded with a lot thick, brown paper. The box and the sword inside was shipped to Croatia undamaged.
The blade
The blade is, as I already wrote, Geibig type 1, caractheristic for almost parallel edges with very little profile and distal taper. Hanwei blade also has very little distal and profile taper but is thicker and heavier than period blades which were thin and flexible. Geibig 1 blades either have no fuller or a wide shallow fuller. Hanwei blade is the second variation with wide, relatively shallow but well defined fuller. The tip is wide and short, but the tip is pointy at the end. The blade is quite thick and very stiff. In the fuller you can see the pattern welding pattern of the core. It is made of three twisted rods which are probably made of two steels already so there is probably six rods mixed in the core. The pattern is made with parts of rods being twisted or left straight to achieve the contrast between the parallel rods. You can see the weld lines and I believe the core really is pattern welded, but the darker color of one of the materials in the core can relatively easily be removed with a sand paper so I assume the steels used in the core are quite similar or the same so just etching them for a contrast is not enough and Hanwei used some kind of bluing substance to enhance the pattern. It is durable finish enough so that it won't fade away in use unless you let the sword rust so that you will have to use some aggresive abrasives to remove the rust. With that you would probably remove the contrast between the steels in the core and you would probably still see the lines between layers and you would see the blade is pattern welded, but the nice color contast would be lost and I'm not sure what would be the easiest way to return it. I would love to see a smith playing a bit with this blade and hear what he would say about the pattern and the materials of the core and in what ways the contrast between them could be achieved.
The edges are made of 1095 regular steel. I don't know what is the steel of the rods in the core. I sent an email to Hanwei and if get a reply, I will update the review. Blade length is 26 3/4" and overall length 33 7/8” according to Hanwei, but 70cm (27.5”) blade and 86cm (33 7/8”) overall. The thing is that Hanwei measured to the curved end of the guard and I measured to the real base of the blade. The sharpening of the blade varies from very nice almost apple-sead age to slight secondary bevel, but it’s not really sharp anywhere. But it shouldn’t be problem to sharpen it.
Fittings
The fittings are well shaped and quite accurate in shape to the original, decoration is not bad, but the original would be much more glorious looking, so I would prefer non decorated and well shaped fittings, but that's just me. Black finish on undecorated parts look a lot like a black paint like on their Cromwell backsword and I would prefer naked steel like on the original. Grip is leather with five metal bands and 4“ long. The tang is peened and didn't loosen after the cutting.
Look at this Barta hilt for an example of what decoration should look like. But I don't know why Patrick Barta too used black finish on undecorated hilt parts. When I think about it, Hanwei probably used the black paint because they saw black finish on the Barta sword.
http://www.templ.net/pics-weapons/128-sword/128-hilt-v.jpg
|
|
|
 |
Luka Borscak

|
Posted: Tue 19 Oct, 2010 4:41 pm Post subject: |
|
|
Scabbard
Scabbard fits the blade very well, it won't fall out when turned upside down, and the blade doesn't scratch against the metal of the throat, there is wood there. I think the scabbard is wooden core with leather covering, not fiberglass like Hanwei/Tinker line scabbards. Fittings are in the same style as hilt fittings.
Handling
Well, this sword is heavy. I don't have anything to weigh it, but Hanwei says it's 3lb and it's probably true. 3lb for a 34“ is a lot, comparable with DSA swords. The PoB is also quite far out at about 6“. All this is result of a rather thick blade with very little distal taper. The sword is wieldale because it is short, but it's definitely not an agile sword. But it would be a powerful shield cracker in a shieldwall and a strong warrior might appreciate the power of it.
Test cutting
Cutting wasn't bad, this sword has a lot of cutting potential, but relative bluntness prevented it from being really good cutter, at least out of the box. But even out of the box I managed a few nice cuts and these are the ones I posted. The rest were half cuts where I cut into the bottle, but not through it so it got batted away. But these were only thick and really hard to cut bottles so it was a combination of that, the edge and my inexperience in cutting resulting in half cut and batted bottles. Even with not really sharp edge this sword cuts normal bottles well if you get the edge alignment right and produce enough speed in a cut. I got the sword additionally sharpened, but had no time for cutting since than. I will update the review when I manage to cut again.
http://www.youtube.com/watch?v=zTrwneKFkZs
http://www.youtube.com/watch?v=nKnAiR-V124
http://www.youtube.com/watch?v=cVDqdIJFLWI
http://www.youtube.com/watch?v=_1LINQ5PR2M
Pros:
Very nice looking, quite historically accurate, quite durable it seems (at least it wasn't damaged with all the batted bottles or the cut through ones, and if it is decently heat treated it would be hard to damage this blade if nothing else because it's overbuilt. ) beautiful pattern in the pattern welded core, low price for what this sword is.
Cons:
Overbuilt (not a con for some people), heavy, not really well balanced, no distal taper, slight inaccuracies about the hilt, possible problems if the contrast in the pattern fades away and the steels used are not different enough to show contrast with etching the core, not really sharp.
Conclusion
For the KoA's price of $310.95 plus $43.60, that is total of $354.55 this really is a good buy, although I had to pay 33% of taxes on these $354.55 so the total for me was about $470. Even for $470 it is still lower than Hanwei's recommended price and a steal for a reall pattern welded blade. If you want an excellent performer cutter, for that money you can do a lot better. But if you want a quite historically accuurate sword with a real pattern welded blade that is functional and not so expensive that you would be afraid of using it, this is it.
|
|
|
 |
Jean Thibodeau

|
Posted: Tue 19 Oct, 2010 6:24 pm Post subject: |
|
|
Thanks for the great review that is very informative about the historical background of the sword and your opinion about it's handling qualities that give one a good idea what to expect if one buys one.
The great blade presence as you say may be a question of personal preferences and some might not find it agile enough but others might like the overbuilt nature of this sword.
You certainly put a great deal of effort in writing a long and detailed review and it is much appreciated.
You can easily give up your freedom. You have to fight hard to get it back!
|
|
|
 |
J. Kari
Location: Estonia Joined: 17 Sep 2010
Posts: 21
|
Posted: Wed 20 Oct, 2010 3:14 am Post subject: |
|
|
Is it possible to order a replacement blade or blade only for doing own custom hilt-pommel- crossguard?
|
|
|
 |
Luka Borscak

|
Posted: Wed 20 Oct, 2010 4:42 am Post subject: |
|
|
J. Kari wrote: | Is it possible to order a replacement blade or blade only for doing own custom hilt-pommel- crossguard? |
I don't know, but that would be an interesting option. If you are interested, you could e-mail Hanwei about that... I ordered from KoA and they certainly don't have replacement blades as Hanwei don't have them as a standard offering.
|
|
|
 |
Douglas S

|
Posted: Wed 20 Oct, 2010 10:13 am Post subject: Re: Hanwei Saxon, full review with cutting video |
|
|
Luka Borscak wrote: |
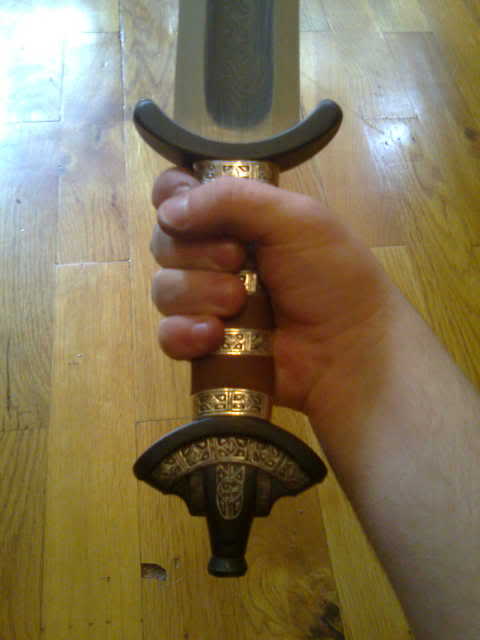 |
The hilt seems very large considering the tendency for swords of that period to be much smaller.
|
|
|
 |
Luka Borscak

|
Posted: Wed 20 Oct, 2010 10:39 am Post subject: Re: Hanwei Saxon, full review with cutting video |
|
|
Douglas S wrote: | The hilt seems very large considering the tendency for swords of that period to be much smaller. |
No, it's a standard 4" grip. My hands are very small.
|
|
|
 |
Gregory J. Liebau
Location: Dinuba, CA Joined: 27 Nov 2004
Posts: 669
|
Posted: Wed 20 Oct, 2010 1:07 pm Post subject: |
|
|
Excellent review. I'd still stay 4" for the handle is a bit much, but I don't know a lot about swords in this era. I'm used to 3.5" or so, creating a snug fit between hilt and pommel for most adult men's hands. It also creates a more appealing aesthetic balance between the components to have it be at least a bit smaller than this one appears to be, methinks.
-Gregory
|
|
|
 |
Harry J. Fletcher
|
Posted: Wed 20 Oct, 2010 10:58 pm Post subject: |
|
|
Very nice sword Luka, very nice indeed. Kult of Athena has great deals. Sorry you had to pay so much tax on yours. Your country's import tax I presume? I bieve you mentioned several times you wanted a pattern welded blade in other posts. thanks for uploading the cutting videos on Youtube and adding the link for us to watch. Maybe we can figure out a way to bypass those taxes you have to pay in an import like this. Have you double checked with any dealers in your country that maybe can order the the sword you want from Hanwei and you might be able to pay less when the taxes are computed?
Keep us informed about how the sword does for you. I for one would really like to know.
Regards,
Harry
To Study The Edge of History
|
|
|
 |
Luka Borscak

|
Posted: Thu 21 Oct, 2010 5:16 am Post subject: |
|
|
Unfortunately there is no way to bypass these taxes. And I payed less than I would going through local sword shops, so I couldn't get a better deal living where I live. I'm very happy and not bothered with price at all since I already thought that if I wanted a pattern welded blade, I would have to give at least $1000...
|
|
|
 |
Jean Thibodeau

|
Posted: Thu 21 Oct, 2010 12:44 pm Post subject: |
|
|
Luka Borscak wrote: | Unfortunately there is no way to bypass these taxes. And I payed less than I would going through local sword shops, so I couldn't get a better deal living where I live. I'm very happy and not bothered with price at all since I already thought that if I wanted a pattern welded blade, I would have to give at least $1000... |
Same thing here in Canada as we have to pay sales taxes both federal and provincial but there are no import duties from the U.S.A. as such. ( There used to be before the Free trade agreement ).
Now, not all packages get stopped and assessed taxes just because of volume not everything gets stopped so at times I have not had to pay taxes, but this is completely up to chance.
But even when I do have to pay taxes many things I order from Kult of Athena end up costing less than if I bought from a local shop that seems to charge a lot more for most things ? I do try to buy locally if the price is close to the same since I can see the product up close before I buy and I do also want to support local business but if the local business charges 30% to 50% more I sort of think they are overpricing or their costs/overhead are somehow too high if they are not " gouging " the local buyers.
Anyway, I also buy a lot from Kult of Athena out of customer loyalty due to such great customer service and as in this post I never miss an opportunity to give them a good and deserved plug. I'm also happy to hear that International customers can find KoA price competitive and also get good customer service.
You can easily give up your freedom. You have to fight hard to get it back!
|
|
|
 |
Donald L
|
Posted: Thu 04 Nov, 2010 12:26 am Post subject: |
|
|
Hi guys, I usually lurk, but decided to add a bit to this review. I got my Saxon today. Overall, I'm satisfied, with some small niggling complaints.
My calipers are saying I've got a 5.5 mm base at the thickest part of the ricasso. The blade doesn't seem to distally taper until about halfway down. Before the point I've got 4.5 mm. Then, of course, the tip shape causes an abrupt change in thickness. Tip seems stout enough, enough meat on the very point for me. Unless the temper is bad, or you hit concrete/tree trunk this should be enough stability for anyone. I flexed the blade just enough to witness it springing back to true. Normally I would flex something out of line several inches at least once, but as the reviewer said, this is a thick blade. I have confidence in what I saw enough to say it has minimum spring- at this point I'm not going to push it. Give me a couple of weeks until the novelty wears off!
It does seem to be pattern welded. Initial impression upon seeing it was a good one, but it does try and trick you into thinking the whole pattern is painted/silk-screened on at some point. My wife ran her fingernail over it and was convinced it was a paint-job. No. She was detecting the difference between relatively smooth bright steel and the much rougher dark patterning. It is possible they etched it and then applied bluing to it which adhered primarily to the rougher "mystery metal".
I am thankful that the grip is constructed the way they did it. Instead of affixing the metal bands OVER a full leather wrap, the bands seem to be glued directly to bare handle beneath, and there are unstitched leather bands glued in between them. These bands might hold in place, and if I want/need to replace the leather parts of the grip it should be easy.
Now for my slight gripes:
The patterning is dark, which is nice, but there is a dark wash-out over the bright metal of the fullering too. It looks dirty, even though the patterning is crisply darkened. Lord knows what Hanwei used to etch this, it seems like some quite formidable acid. In a strange way it reminds me of the same aesthetic they employ in treating their katana hamons. Very heavy handed and quickly done.
The blackened hilt pieces have some scuffs, though minor. I am wondering how long the blackening will last in use. The silver decorative bits on the pommel seem to be molded in to it, so it appears that the paint has been sanded away from the relief to make it silvery.
Minor glue visible at chape and throat of scabbard. Excusable and easily remedied.
The scabbard's harness furnishings are historically inaccurate. This should have a single belt retainer attached to the flat/front of the scabbard right below the throat. The metal pieces they have seem easily removable. The top strap-loop band seems to be a separate piece from the metal throat piece, so it should be removable without scarring the throat piece (or requiring the throat to be tossed also). This is all excusable in my eyes, and a nice little improvement project in the future.
Scabbard seem to have a core of plastic. Honestly it sounds like plastic, and it looks like wood grained plastic like they use on their Practical "hand and a half" Blunt line. [EDIT] I've got better light now and just checked the inside of the scabbard again. It is indeed wood, but there is a plastic faux wood liner at the throat. This is good, it will keep wood shavings and chips from being taken out of the scabbard core by the blade's point.
Chape parts look a bit dirty from excess black paint.
Scabbard fit is good though I wish it was lined.
The blade is *sigh* as rough as the Tinker line of weapons I've seen. No one seems to mind the finish on the HT line, but this is a different creature altogether. However, once again this is easily remedied.
The peening is strange. A peen block that is essentially a donut of metal has been slipped down over the tang-end, and then it was peened, but as far as I can tell there isn't a peened "plug" or mass/button built up over the end of the peen block made of hammered tang-metal. I see the tang flush with the peen block and I see hammer marks. It's as if the hilting is glued together internally, but for looks they added a peen block and smacked it a few times. I've never see a set up like this. However the hilt seems sturdy... time will tell.
POB is alright, based on what I know about period examples and good reproductions of the weapon type. Weight is surprisingly acceptable to me, though it is perhaps a pound heavier than it could be. I am 6'4' and have been practicing WMA for 9 years now, so what others consider point-heavy I consider to be something capable of allowing me to put my effort/footwork behind and see a good result. Dark age period N. European swords generally ARE a bit awkward. I like to think of them as having an "axe feel" to them-in a good way. So I consider this 3 Lbs making up for a relatively diminutive length with some hitting power. The reviewer is right however on all handling characteristics, but, yes, it's a 500-800 AD blade in a new hilt. A very accurate description of Typology and general handling characteristics.
So what's left? Here is my tentative plan for it:
Clean it up. Test the ricasso between the fuller termination and cross with vinegar to see if in fact I can etch it with household/hybrid-polishing chemicals. If so, polish the @^!@* out of the blade and re-etch. Also test one side of the point's cutting edge with vinegar- I want to check to see if it is a 1095 homogeneous steel edge WRAPPED around a pattern welded core, or if it has two 1095 edges that do not wrap and the tip is in fact pattern welded material sticking out of the center mass.
Perhaps redo scabbard, or build another one entirely.
All in all I think this was a decent buy for me. I've always wanted an example of pattern welding technique, and even if this ends up as a wall hanger in the future, it sure is a pretty one. But for now I'm going to cut with it and treat it like any of my other swords.
Thanks for reading!
|
|
|
 |
Luka Borscak

|
Posted: Thu 04 Nov, 2010 9:39 am Post subject: |
|
|
Please report what you will find out when you try to etch the forte and the tip!
|
|
|
 |
Glen A Cleeton

|
Posted: Thu 04 Nov, 2010 11:14 am Post subject: |
|
|
Forumnaut Aaron Justice had polished out and etched one of the Godfred blades. The result was actually fairly pleasing and a less harsh presentation of the folded steels. I am forgetting whether it was a saga or monk recollection of the sword's pattern being only visible when caught by the light in a certain way. Serpent in the blade stuff.
The harsh contrast shown in etched pattern welding is usually a matter of the polish itself revealing the shiny while leaving the softer darker.
Cheers
GC
Attachment: 83.42 KB
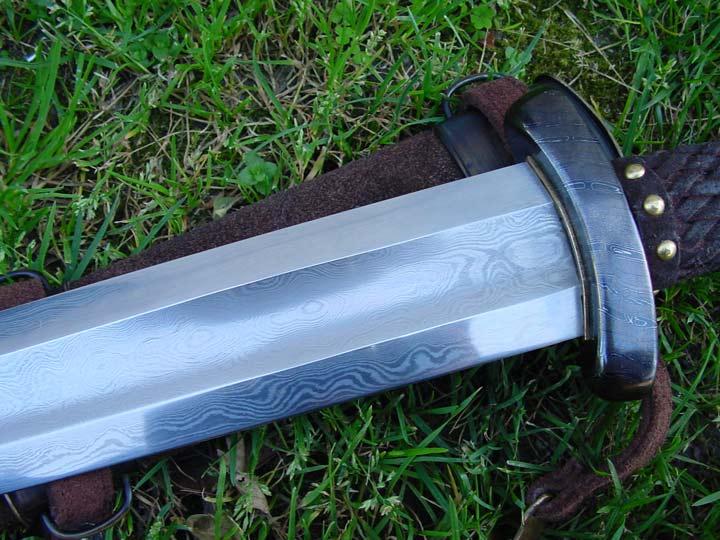
Aaron Justice polished and re-etched Godfred
|
|
|
 |
Johan Gemvik

|
Posted: Thu 04 Nov, 2010 8:16 pm Post subject: |
|
|
Excellent review on a very nice sword.
I especially like the blade and the scabbard.
Hold on a minute, I just re-read the first post... $310 something? That's an amazing sword for that money.
Anyway, if you want to re-line the scabbard with lambs' skin I'm sure one could simply open the seam, remove the fittings, grind the inside further and glue some in and re-stitch. If you need any tips on how to lambs pelt line a scabbard just PM me, I've done it a few times by now.
"The Dwarf sees farther than the Giant when he has the giant's shoulder to mount on" -Coleridge
|
|
|
 |
Donald L
|
Posted: Thu 04 Nov, 2010 11:30 pm Post subject: |
|
|
@ Glen:
I'm a bit confused about the appearance of pattern welded blades like this. From what I've read it seems like there are two versions... one is a heavily etched fuller, the other seems to be a highly polished "ghostly" patterning, the "little snake" of the saga recollection. Davidson quotes Arabic writers in "The Sword in Anglo-Saxon England" writing that some Saxon or Viking (cannot remember which right now) blades had "red backgrounds" behind the patterns.
So, I've got to figure out how to proceed with this, but I guess it would be safe/sensible enough to test if I can etch and then polish it up... that route seems like a good base to build upon later once I decide.
I hope Hanwei answers Luka's request to know the metals combined in the PW twists.
|
|
|
 |
Luka Borscak

|
Posted: Fri 05 Nov, 2010 3:42 am Post subject: |
|
|
Donald L wrote: | @ Glen:
I'm a bit confused about the appearance of pattern welded blades like this. From what I've read it seems like there are two versions... one is a heavily etched fuller, the other seems to be a highly polished "ghostly" patterning, the "little snake" of the saga recollection. Davidson quotes Arabic writers in "The Sword in Anglo-Saxon England" writing that some Saxon or Viking (cannot remember which right now) blades had "red backgrounds" behind the patterns.
So, I've got to figure out how to proceed with this, but I guess it would be safe/sensible enough to test if I can etch and then polish it up... that route seems like a good base to build upon later once I decide.
I hope Hanwei answers Luka's request to know the metals combined in the PW twists. |
They didn't answered me yet, and I doubt they will, although they replied me before when I was asking about this sword before I bought it. But than they didn't knew waht the core is made of and now they don't answer. We'll have to find out for ourselves.
|
|
|
 |
Kirk Lee Spencer

|
Posted: Sat 06 Nov, 2010 12:08 pm Post subject: |
|
|
Hey Luka…
I wanted to thank you for taking the time to review this new sword… It is certain worthy of a good reviewing. And Donald… thanks for your addition to the review. I also have one of the new Hanwei Saxon Swords and I am in agreement with all of your observations. Like Donald I bent the blade a little and observed that is springs back… so I suspect it has some level of tempering.
Now I would like to add a few of my own observations.
Hanwei has been doing production torsion pattern-welded blades for awhile. (I’m not sure if anyone else is). I have one of their pattern-welded William Marshall swords. I got at a very good price second hand. Even without etching the flats along the edges, it is clear that the torsion pattern-welded “core” billets go to the edges. In other words, it is all core, so to speak, the edge flats beyond the fuller were just left unetched.. There are no monosteel edges welded to the core… In the picture you can see the different steels of the torsion pattern welding peaking through near the ink marks outside the fuller.
ks
Attachment: 121.2 KB
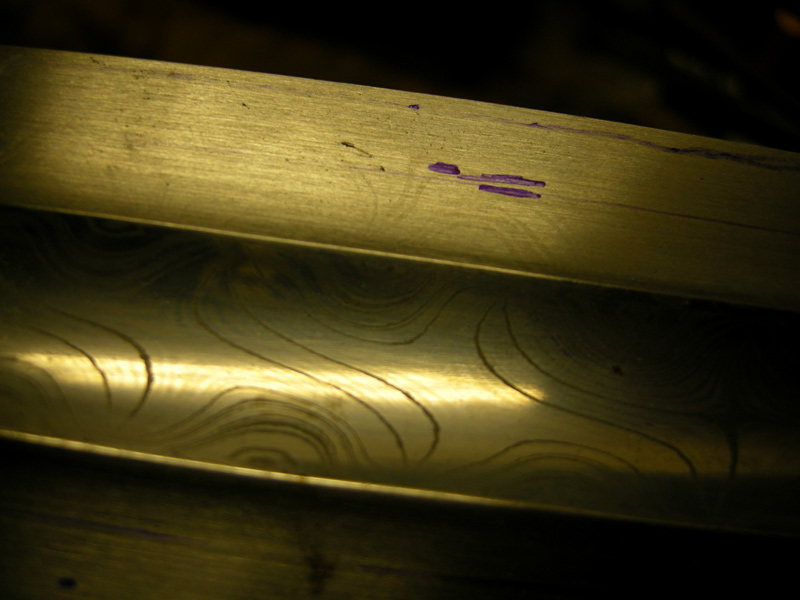
Two swords
Lit in Eden’s flame
One of iron and one of ink
To place within a bloody hand
One of God or one of man
Our souls to one of
Two eternities
|
|
|
 |
Kirk Lee Spencer

|
Posted: Sat 06 Nov, 2010 12:14 pm Post subject: |
|
|
On first seeing the Hanwei Saxon Sword, it was clear to me that the core was truly three billets of torsion pattern-welding alternating straight and twisted sections offset from each other across the blade. It was not just selective etching of the surface. The twist patterns match on both sides of the blade and are in reversed angles. Also slight undulations in the weld seams between billets appear on both sides of the blade in the same positions.
I was curious if the new Hanwei Saxon Sword was the same as the William Marshall in the edge treatment. I was not sure if it edges were monosteel or like the William Marshall Sword, just left unetched. So, like Donald, I decided to etch the forte with ferric chloride. And the etching shows it does have monosteel edges welded onto the core.
ks
Attachment: 142.59 KB
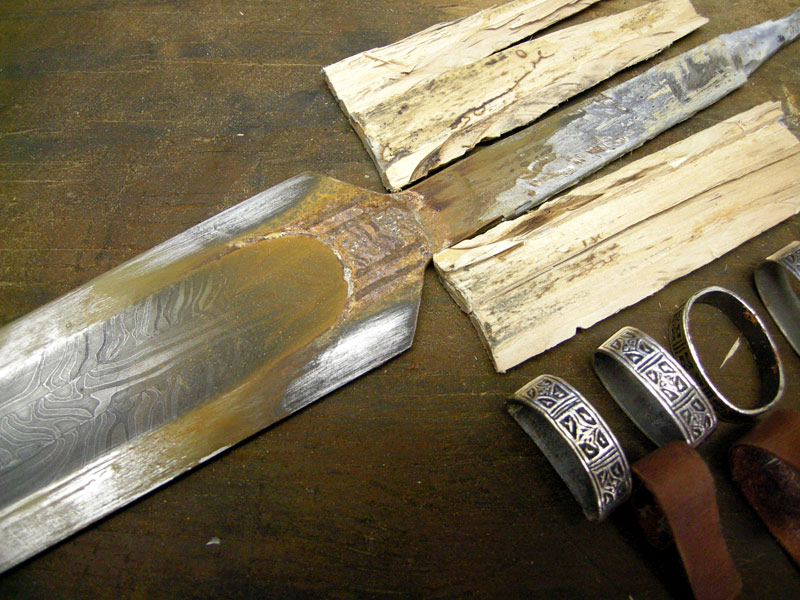
Attachment: 134.32 KB
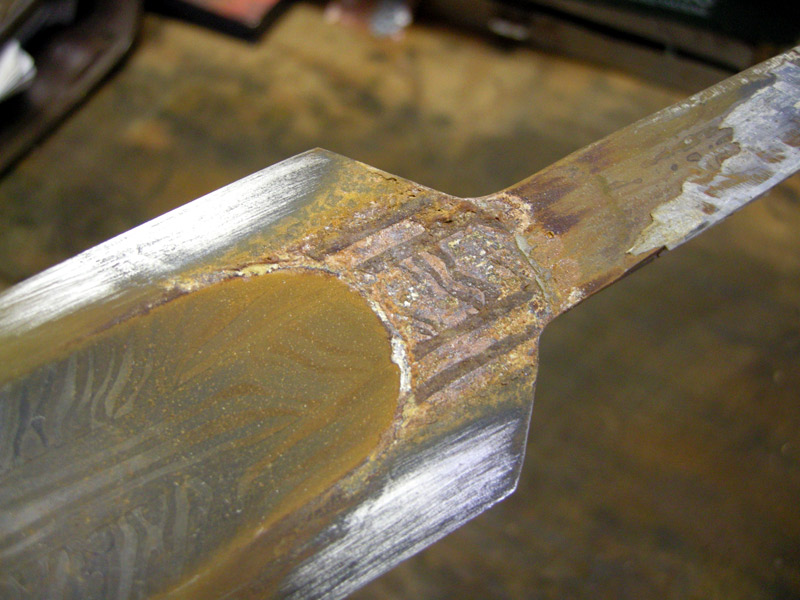
Two swords
Lit in Eden’s flame
One of iron and one of ink
To place within a bloody hand
One of God or one of man
Our souls to one of
Two eternities
|
|
|
 |
Kirk Lee Spencer

|
Posted: Sat 06 Nov, 2010 12:21 pm Post subject: |
|
|
Also like Donald, I wanted to see if the core ran out the end of the sword and it just looked like the edge wrapped around because they left the tip outside the fuller unetched or if it really did have welded on monosteel edges that wrapped around the point. So I also etched the tip. It is clear that the monosteel edge does NOT wrap around the tip. Rather the torsion pattern-weld runs out of the tip.
You can see in the pictures I posted of the etched tip that the dark coloring is something that occurs in the etching process. So I don’t think it is a paint or even a bluing substance.
With just one etch in 28% ferric chloride (Radioshack circuit board etchant) at room temperature for about 15 minutes you can see a little bit of topography on the surface (see oblique image of the tip etch). So I suspect that if the etchant was warm you could get a better cut and more topography, especially with a longer etch.
I also noticed that the core is the same width at the forte as it is at the tip (1 inch). So it appears that the elements are welded together as a long bar which is cut off in sections and ground to shape with no forging and drawing out. A much faster and cheaper process than making each blade separately and welding the edges around the tip.
If this is the process they use and if enough people purchase the Saxon Sword then Hanwei may be encouraged to make longer blades (just cut the blades longer to begin with). And maybe even different patterns. And that would provide more kit material for me
ks
Attachment: 132.89 KB
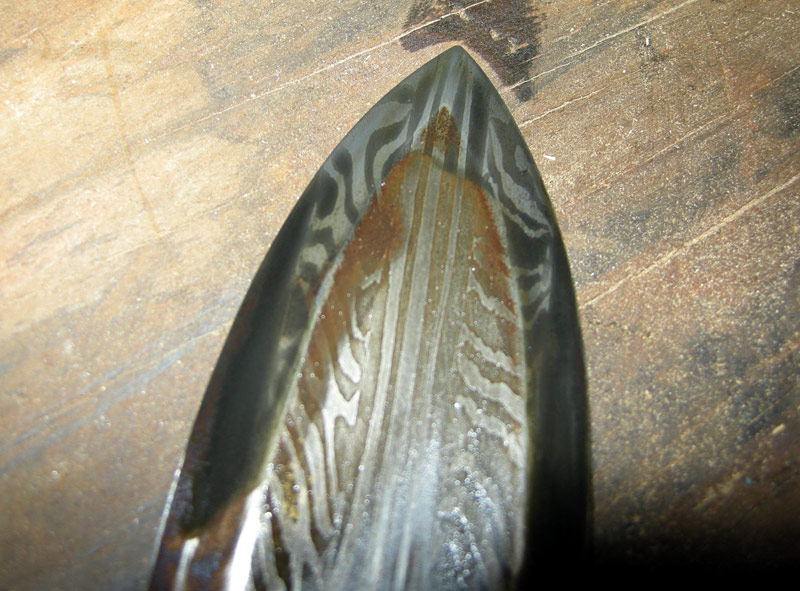
Attachment: 141.66 KB
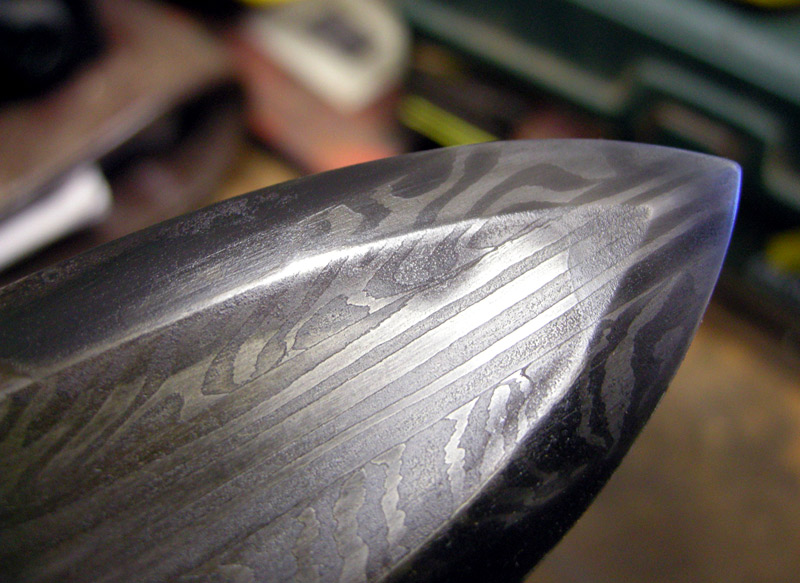
Two swords
Lit in Eden’s flame
One of iron and one of ink
To place within a bloody hand
One of God or one of man
Our souls to one of
Two eternities
|
|
|
 |
|
You cannot post new topics in this forum You cannot reply to topics in this forum You cannot edit your posts in this forum You cannot delete your posts in this forum You cannot vote in polls in this forum You cannot attach files in this forum You can download files in this forum
|
All contents © Copyright 2003-2025 myArmoury.com All rights reserved
Discussion forums powered by phpBB © The phpBB Group
Switch to the Basic Low-bandwidth Version of the forum
|