Author |
Message |
Jeremy V. Krause
|
Posted: Wed 26 May, 2010 10:22 am Post subject: Appearance of modern mono-steel vs. historical steels |
|
|
Hello everyone,
In my never ending quest to increase the historical accuracy- or to decrease the blatant non-historical aspects of my collection; I have began thinking about the appearance and sheen of the steel used on my reproductions.
I know that the wrought iron used on period pieces does indeed look quite different than the modern tool steel utilized on hilts and such. For this reason I am going to opt for wrought whenever I can on my pieces.
I also opt for fine silver instead of sterling as I feel it's sheen and degree of patination are qualitatively different.
So what about the steel used on the blade of our beautiful reproductions by the higher end makers? What was the steel used following the era of pattern-welding? Previously I thought that it was a fairly homogenous material and that the steels used on our pieces really , pretty much looks the same. Am I wrong? Was there some degree of "folding" of different materials creating a "texture" to the steel that is missing from our reproductions?
I am interested in this possible difference. For instance, I am going to order an eating knife from Tod incorporating shear steel as it is felt to be a better representative of a historic example. I am eager to see the difference between this material and the modern steel which we usually see.
I realize this post touches an ENORMOUS multitude of factors and multitudes of possible angles. I am looking at the era 1100-1500, although I am sure that there may have been huge changes in the methodology and production of steels.
Perhaps there was a tendency of steels appearance changing over this period- I don't know.
What do folks think?
Last edited by Jeremy V. Krause on Wed 26 May, 2010 9:31 pm; edited 1 time in total
|
|
|
 |
Craig Johnson
Industry Professional

|
Posted: Wed 26 May, 2010 8:01 pm Post subject: Visuals |
|
|
Hi Jeremy
You are right it is a huge subject. I would say it is much dependent on the period you chose and the type of item you are wishing to depict.
In the case of a knife from the early medieval period I would probably go with a welded on edge of shear steel or carburized iron edge on an iron blade. As you get closer to the 1500's you could start to do some layering or inset edges or steel blades with the edge heat treated.
It is a very diverse group of options for a knife through this period and each region and time period would have a favored method and some options.
It is important to remember that there where many answers to what a knife should be like and to embrace them as they where is to understand the depth and diversity of the Medieval smith.
I would expect Tod could do an excellent job of incorporating a shear steel into a blade in a period way and give you a great result as a knife and as something that has the visuals of the period blade.
Best
Craig
|
|
|
 |
Jeremy V. Krause
|
Posted: Wed 26 May, 2010 9:59 pm Post subject: Re: Visuals |
|
|
Craig Johnson wrote: | Hi Jeremy
You are right it is a huge subject. I would say it is much dependent on the period you chose and the type of item you are wishing to depict.
In the case of a knife from the early medieval period I would probably go with a welded on edge of shear steel or carburized iron edge on an iron blade. As you get closer to the 1500's you could start to do some layering or inset edges or steel blades with the edge heat treated.
It is a very diverse group of options for a knife through this period and each region and time period would have a favored method and some options.
It is important to remember that there where many answers to what a knife should be like and to embrace them as they where is to understand the depth and diversity of the Medieval smith.
I would expect Tod could do an excellent job of incorporating a shear steel into a blade in a period way and give you a great result as a knife and as something that has the visuals of the period blade.
Best
Craig |
Thanks Craig,
Oh I know that Tod will do a great job- I was just bringing up my little project to illustrate how my pondering about the appearance of historic steel led me to make such a commission choice. Given that an eating knife is obviously less expensive than a sword or even a quillon dagger made this type of project appealing.
I own a fine seax with a wrought blade and laminated steel edge which would look really quite different in the mono-steel used more commonly by smiths.
I want to focus my musings on the issue of military knives and swords from the high middle ages. Did the types of blade construction utilized historically on these weapons give a "textured" appearance to the steel that would differ from that which we see on the mono-steel weapons made by our favorite amorers such as A&A, Albion, and any others who use a modern homogenous steel.
This issue interests me not only because of my desire for a more historical appearing collection but because apparently I have had either grossly misunderstood or grossly simplified understanding of steel development in weapons. I thought, incorrectly, that after about 1100 or so western europe gained the ability to make homogenous steel knives and swords. I knew that many knives and spears were not really steel but mostly iron with a partially carburized edge but I thought that homogenous steel was being used- no more folding of iron and steel.
SOOOO, even after pattern-welding; smiths still folded different materials to arrive at a more homogenous structure? Could someone help me flesh this out a bit as smithing and steel making are not my area of expertise regarding historical arms and armor- clearly.
Also- and this is the primary thrust of my thread. Does the steel of our homogenous reproductions look nearly identical, very similar, merely similar, or quite different from historical examples when new.
If I were looking at my seax as an example (late period 11thc.) I would see that a homogenous steel blade looks grossly different than the historical method of construction used. BUT on my seax there are two distinct materials next to each other, thus showing a real contrast.
Clear as mud eh?
Last edited by Jeremy V. Krause on Thu 27 May, 2010 12:17 pm; edited 1 time in total
|
|
|
 |
C Bosh
Location: France Joined: 10 Aug 2009
Posts: 15
|
Posted: Thu 27 May, 2010 1:24 am Post subject: |
|
|
I am not too sure on the appearance of the iron and steel used in knives, but I have two swords made from more traditionally mediaeval style smeltings. And what is obvious in affecting some of their appearance is the polishing style, hand polished or muscle / water powered polishing gives a different result in appearance to an electric machine with revolutions of over 8000 per minute .
One of the blades has had a sister peace of its material tested, is not of a uniform carbon percentage through the blade varying from between around .6 -.7, percent, then taken with the forging process, which will again affect the carbon content in the steel, it is not of a modern homogenous standard, although well within the acceptable limits for a good quality sword blade, properly heat-treated.
This blade has been hand polished/ ground with a wheel etc and varying stones, this has given the blade a wonderful cloudy grey, rich velvety colour. This colour is incredibly hard to capture on camera, due to reflections, and mainly my lack of skill.
Other things to be considered would be, even in the Middle Ages, although pattern welding as we know it, is supposed to be non-existent , tests have shown that numerous swords were made of composite construction,-softcore, hard outer skin, and vice versa, numerous combinations may have been tried. Indeed the Mary Rose sword is said to have two hard steel edges welded to a softer core. Maybe some of these transition lines would be visible on the blades with different polishing techniques ? After all Damascene pattern almost disappears with modern machine polishing, and has to be chemically enhanced afterwards.[/b]
|
|
|
 |
Peter Johnsson
Industry Professional
|
Posted: Thu 27 May, 2010 3:24 am Post subject: |
|
|
As has already been said before, the look of steel & iron would have varied greatly.
Both methods and degree of polish would have varied in weapons and tools as would have the material itself.
Sometimes the subtle shading and irregularities of the material would have been readily apparent and sometimes the surface would have been indestinguishable from modern steel.
With well preserved swords this is obvious. A polished surface can be uniform and without any obvious traces of the heterogenous nature of the steel.
I have seen other blades where the structure of the steel has been more visible, but that is normally only if there is some corrosion or patination.
It takes a very high polish or corrosion/etching for the colors or shadings to come out.
We may also today use less refined steel when we smelt it for use in reproductions of historical blades. As we take the trouble to manufacture a material with some character we want this to show. In historical times they wanted a material that was as even as possible.
This is a little bit like the aesthetic ideal that is common today: we appreciate marks from the hammer and forging scale in the finished object, since this is a sign it was indeed forged. In ancient times they wanted a nicely finished object, since that is a mark of quality and skill.
The polish on blades was often accomplished with rotating wheels where a surface of leather was loaded with a abrasive compound of increasing fineness. Very fine grit was used to reach final finish (and not always very healthy materials, like arsenic). These polishing methods does not differ much from what can be done with fine grit belts or felt wheels: in essence it is the same process. Greatest difference is the power source: electric motor instead of hand crank or water wheel.
Interesting questions as it puts a perspective on what we appreciate and look for in both historical and contemporary craft.
|
|
|
 |
Jeremy V. Krause
|
Posted: Thu 27 May, 2010 4:11 pm Post subject: |
|
|
Peter Johnsson wrote: |
Interesting questions as it puts a perspective on what we appreciate and look for in both historical and contemporary craft. |
Well, I appreciate and look for modern reproductions that match historical examples as close as possible. Indeed, I recognize, and dislike the faux-historical "rustic" aesthetic taken on some modern examples. That's not the distinction I was looking to examine.
I am glad to hear that our finer reproductions can share the sheen evident on some historic pieces.
I was not aware that using a refined polishing process with abrasives and such could really diminish the textures of heterogenous steels to the extent to which their appearance would be nearly uniform.
Would finishes be fairly similar or quite different between, utility and military blades in a given time period?
|
|
|
 |
Maurizio D'Angelo

|
Posted: Thu 27 May, 2010 5:15 pm Post subject: |
|
|
Before the battle, their don't show weapons, could reflect the sun. (V century - Procopius)
The blades were finished well (VI century. Imperator Maurizius)
An Italian author, tells us that the blades were forged with a subsequent first grinding. (XIII century- Boccia) There were specialized workshops for grinding finish.
We think that the degree of finish was nice enough. Material differences tend to disappear with a good finish. (I say this, no author.)
Ciao
Maurizio
|
|
|
 |
Jared Smith

|
Posted: Thu 27 May, 2010 5:27 pm Post subject: |
|
|
There was a new brazil nut type sword posted very recently that was stated to be made from "bloomery steel" if I remember it right. At least in the photo, it was indistinguishable from a modern homogeneous blade. I suspect this is because it was very well done, fluxed, and kept clean throughout the process. Then, polished to nearly perfect finish that it seems a majority of buyers now expect in replicas.
Some custom offerings have stated that 1018 mild steel was used for furniture, and depending upon finishing, it can have a lot of character even though it is just homogeneous iron with low carbon. You might like some hand forged furniture that is hand forged and not polished to perfection. I have heat blued some non-weapon items (rail spike knife, bottle opener, hook, etc.) made from 1018 and cooled them with WD-40. They actually resist rust fairly well and have gray to blue to black final appearance depending upon cleanliness, and temperature. (Have not mastered control of color yet.)
If thinking of pattern welded items, the more elaborate and complex composite patterns I have seen seems to be on spear heads as opposed to knives and blades. For knives, I actually greatly prefer non-historic patterns that bring twisted layers into the cutting edge. (This is from a performance point of view in slicing for knives.)
Absence of evidence is not necessarily evidence of absence!
|
|
|
 |
Peter Johnsson
Industry Professional
|
Posted: Fri 28 May, 2010 12:18 am Post subject: |
|
|
Jeremy V. Krause wrote: | [
Would finishes be fairly similar or quite different between, utility and military blades in a given time period? |
As blade production was a large scale operation, I think that finishes were pretty standard to some degree. Some blades would stand out as obvious high quality work. In some areas the standard issue would be of comparatively higher quality than blades from other production centers. Even in high quality blades that survive in pristine condition, you can sometimes find scratch marks from file, scraper or coarse stone remaining in patches. This is not the norm, but it happens.
It is a varied picture that is made up from numerous types of variations as a result from many different causes. Still if we take one step back, the overall impression is that blades as a rule were finished pretty well.
If you focus on small details like the sharpness of the edge, larger scale features tend to follow suit. But it can also mean that if the blade has good shape and is sharpened well, small blemishes or irregularities were not cause to discard the blade.
You do see weld lines at times. Sometimes the steel has a variegated "color" or sheen. Not always and mostly a very subtle effect. Strands heterogenous character of the material often comes out with heavy corrosion, but at times it can show after a certain type of grinding/polish has been done.
EDIT: comments to the photos were shortened.
The polish on the war sword would not, I think, be typical or representational for the work done originally. It is an interesting experiment done today that reveal tat the steel used for European blades have at least some features of the fabled japanese swords. Especially the steel is very similar in some ways. Not surprising, since it was a heterogenous material refined by folding and forging.
The Later blade is a wide hollow ground blade. Between dark pits of corrosion, the surface seems to be original. The edge is still almost sharp. Color shifts you see in the surface are result of oil or wax catching the light. Note the coarse marks in the blade. The hilt was of highest quality and must have demanded 100´s of work hours to complete. In all a sword of stunning quality both artistically, crafts wise and as a weapon.
With many abrasive polishing methods (used today and in ancient times), there is still a slight smearing effect. This will tend to even out any irregularities in hue and structure of the steel. It takes dedicated and special grinding/polishing to bring these out to full effect.
Perhaps this illustrates why it is so difficult to say anything general about finish and standards?
I attach some photos as example:
Attachment: 60.1 KB
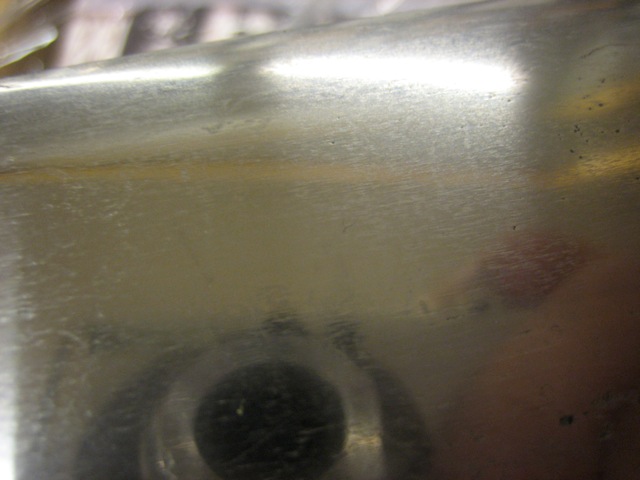
This is a 13th c or early 14th c great war sword that has been brought to a high sheen with japanese type polish. You can see a subtle "hada" but this is only since the polsh is very fine and of a special type. I do not think this is the typical polish of
Attachment: 48.4 KB
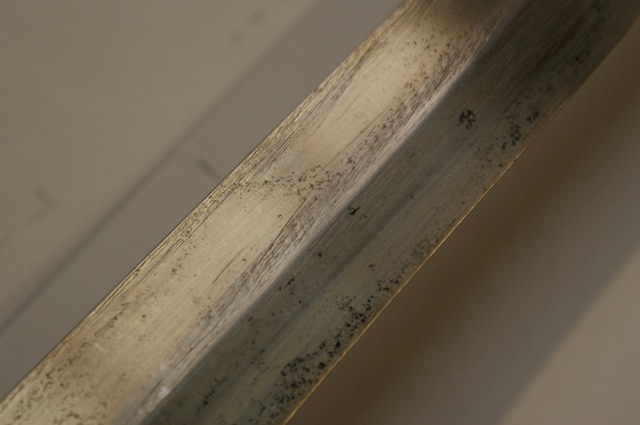
This is a very fine quality C&T sword of the late 16th C or early 17th C. The surface is more or less original, possibly with a light restoration. We can see how some scratch marks from a scraping tool still remains in the surface of the finely hollow gr
|
|
|
 |
Peter Johnsson
Industry Professional
|
Posted: Fri 28 May, 2010 12:38 am Post subject: |
|
|
And another example, just to underline the complexity of the topic. An original sax blade and some roman spathae were recently polished with japanese techniques showing a very fine hada and a nice hamon. The undulating line of the hamon on the sax blade suggests this may have been an intended feature. Something was done to get the wavy line and not just a line following the thickness of the blade as a result of cooling. If this was an appreciated feature of the blade, they must have been finished much like japanese blades...
...and we are talking about "simple" sax blades.
That you see dark pits and lines in these blades that have been given a high polish in modern times, is since black oxide still remains in rust "scars". Originally irregularities in structure would have been much more subtle in look. Mostly.
Attachment: 55.23 KB

Sax blade below, roman spatha above
Attachment: 48.51 KB
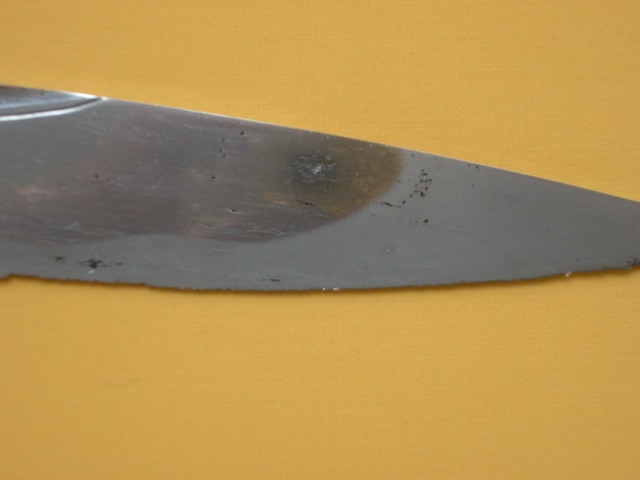
Note the nice curve and slight undulation of the hardening line at the point.
|
|
|
 |
Maurizio D'Angelo

|
Posted: Fri 28 May, 2010 4:18 pm Post subject: |
|
|
Peter,
thanks for these photos.
Clarification. Gender differences in the materials tend to be confused with a good finish, to use a template, let's say a little 'less finishing Albion. If the finish is driven at high levels, these differences tend to reappear. It is no coincidence that some analysis of the material, the specimens used in the metallurgical industry (not for swords, but for mechanical components) the finish is like a mirror, (the next test with Nital acid for microscopic analysis) differences of color or foreign inclusions, are also evident by eye. We can assume that the swords in Europe, in generally, had a good finish, but not a super-finishing.
Ciao
Maurizio
Last edited by Maurizio D'Angelo on Fri 28 May, 2010 4:20 pm; edited 1 time in total
|
|
|
 |
David Sutton
|
Posted: Fri 28 May, 2010 4:19 pm Post subject: |
|
|
This essay might be of interest.
Its by Stefan Maeder and concerns the use of Japanese sword polishing techniques to reveal the surface structure of period European swords, which Peter mentions above. Theres some interesting info on the appearance of period swords and sword polishing in Europe. There is also this brilliant quote from a letter sent by the Ostrogothic King Theodoric to a king of the Varni in the late 5th Century which gives some indication of the level of finish on Dark Age swords:
“Together with black trunks (of moor-oak) and indigenous blond
boys your fraternity has chosen swords for us, that are able even to cut
through armour, and which I praise more for the quality of their iron than
for the gold on them. Their polished clarity is shining so strong, that they
reflect with utmost clearness the faces of those who look at them. Their
edges run so regularly towards the point, that one is tempted to assume
that they were not shaped by files, but formed in the smelting-furnace.
Their midsection, skillfully wrought with hollows, appears to be covered
with swirling worms, and there are so manyfold shadows, that one might
believe the shining metal to be interwoven with many colours. This metal is
ground on your grindstone and polished with your most famous powder so
diligently, until its´ steely shine becomes a mirror for men. This powder is
provided to you by the natural treasures of your country and may its´
possession bring singular fame upon you. Regarding their beauty such
swords may appear as the work of Vulcanus, who is said to have ennobled
his craft with such skill, that everything he crafted appeared to have been
made not by human but by divine power.”
Japanese Sword-Appraisal/刀剣の鑑定
Its´ Significance for Archaeo-metallurgical Research within International
Archaeology and Materials Science
Stefan Maeder, Kokugakuin University, Tokyo 2006
www.schwertbruecken.de/pdf/sigjapswocu.pdf
'Reserve your right to think, for even to think wrongly is better than not to think at all'
'To teach superstitions as truth is a most terrible thing'
Hypatia of Alexandria, c400AD
|
|
|
 |
Maurizio D'Angelo

|
Posted: Fri 28 May, 2010 6:03 pm Post subject: |
|
|
A letter of gratitude. If it was common because show gratitude?
Maybe you can interpret that it was not the norm mirror polished sword?
Perhaps a taste of the owner, but perhaps not manufacturing, apart from these specific swords, of course.
another thought, why, today, we use acids to highlight the texture of damask? No, it is less evident, probably.
just my thought
Ciao
Maurizio
|
|
|
 |
Timo Nieminen
|
Posted: Fri 28 May, 2010 10:00 pm Post subject: |
|
|
Note the "polished with your most famous powder". The region these gift-swords were from was famous for sword-polishing, or at least, as a source of an abrasive for sword-polishing.
Al-Kindi on Frankish swords: "Their structure resembles the character of the foreign Tabari clothes [1] and the structure of the rings of armour; they are white of ornamentation [2], red of ground [3] after throwing [4], and before throwing nothing of it appears."
[1] Tabaristan was famous for embroidery.
[2] Probably high-phosphorus portions in the pattern-welded blade.
[3] The rest of the blade. "Ground" suggests that the "ornamentation" appears as patches in a continuous "ground", but he uses the same terms for crucible steel blades, so these might just carry over from that. "Red" appears to be a mystery - darker, yes, but red? Hoyland and Gilmour [5] suggest this might be a characteristic colour while the etchant is still there.
[4] "Throwiing" as in throwing on the etchant.
[5] R. G. Hoyland, B. Gilmour, "Medieval Islamic swords and swordmaking", Gibb, 2006. Translation of al-Kindi, commentaries, etc.
"In addition to being efficient, all pole arms were quite nice to look at." - Cherney Berg, A hideous history of weapons, Collier 1963.
|
|
|
 |
Michael Edelson

|
Posted: Sat 29 May, 2010 12:34 am Post subject: |
|
|
Peter,
Thank you for posting those great pictures and the accompanying explanations. It's rare to see a photo with that much small detail.
I too have some photos to share of swords from the Metropolitain Museum of Art. This is the display as it appeared in 2008:
The first is the sword in the middle:
This is the sword on the left:
This is their famous and often reproduced type XIV:
You can see all kinds of nastiness in the fuller.
Any comments you would care to make on these photos would be appreciated.
New York Historical Fencing Association
www.newyorklongsword.com
Byakkokan Dojo
http://newyorkbattodo.com/
Last edited by Michael Edelson on Sat 29 May, 2010 11:42 pm; edited 1 time in total
|
|
|
 |
Maurizio D'Angelo

|
Posted: Sat 29 May, 2010 3:55 am Post subject: |
|
|
Michael you are great.
Here some details of an original sword used by the emperors. The sword never fought.
Michael, how do you post pictures so big? I had to reduce the resolution of my much. is a mystery.
Attachment: 149.55 KB
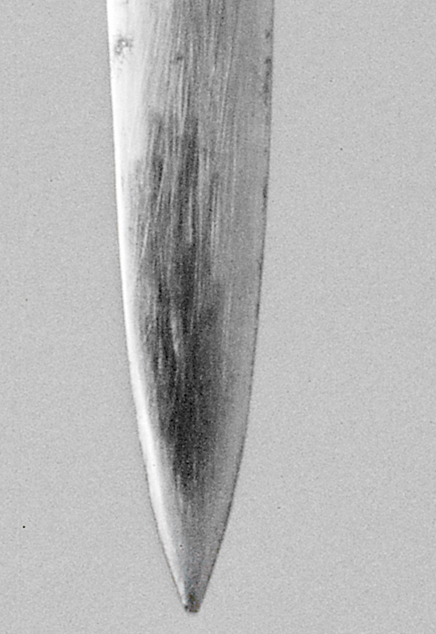
Attachment: 182.32 KB
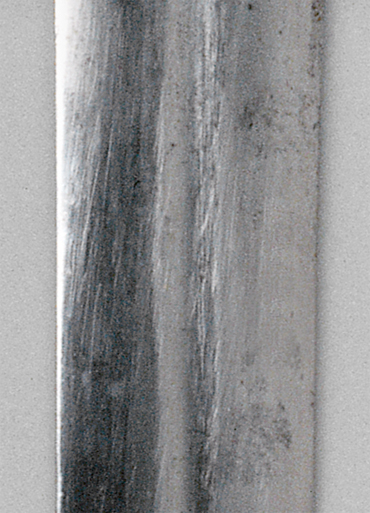
Ciao
Maurizio
|
|
|
 |
Michael Edelson

|
Posted: Sat 29 May, 2010 9:10 am Post subject: |
|
|
Well the size restriction is supposedly 1200 by 1600, but it wouldn't let me do that even though the images fit within that limit, so I kept reducing them in tiny steps until it went through. The system is glitchy...it let me post it, but I can't edit it.
So what sword is that in your pics? Do you have a picture of the whole thing? If not, what kind is it? Longsword, arming sword sword, etc?
Nathan, Chad, all you admin types...please lift the size restriction on linked images. It's a huge pain in the buttocks.
New York Historical Fencing Association
www.newyorklongsword.com
Byakkokan Dojo
http://newyorkbattodo.com/
|
|
|
 |
Chad Arnow
myArmoury Team


|
Posted: Sat 29 May, 2010 9:51 am Post subject: |
|
|
Michael Edelson wrote: | Nathan, Chad, all you admin types...please lift the size restriction on linked images. It's a huge pain in the buttocks.  |
Well, Nathan is the only one who can do that and there are better ways of suggesting this to him than what you're doing....
For Attachments:
In the Add attachment section of a new topic or reply, there is always a link called "Allowed Extensions and Sizes." That will show you exactly what the limit is in terms of size. For the Off-topic Talk forum, the size limit is 220 KB. Anything under that size will post just fine. If it measures more than 800 pixels wide in any direction, it will display as a link rather than as an image. This lets people on slower connection decide if they want to spend the time downloading it.
For images found elsewhere on the net:
Yes, there is a size limit. If you exceed it, the forum software will tell you.
I realize some people don't like these restrictions. Oh well. They're put in place to make sure users with slower connections don't have to wait inordinate amounts of time for a page to load. They're put in place to make sure the database size (for attached images) does not expand beyond what it should. Or that downloads don't start eating up more bandwidth than is allotted. They're there to make sure people don't go over their personal attachment limit.
The sizes are perfectly viewable in plenty of detail if cropped/edited correctly. The FAQ pages and its attachment guide even give some advice on how to do it.
The size limits were not done willy-nilly. They're for very valid reasons. We've placed info about these sizes in obvious places and have provided tips on how to re-size things to fit.
ChadA
http://chadarnow.com/
|
|
|
 |
Jared Smith

|
Posted: Sat 29 May, 2010 10:22 am Post subject: |
|
|
Michael Edelson wrote: |
I too have some photos to share of swords from the Metropolitain Museum of Art. This is the display as it appeared in 2008. |
Thanks from me as well Michael. The cruciform sword on the left with a remaining grip and lower close ups has several aspects of what I was trying to describe earlier. The look of the furniture is emulated in replicas fairly well with 1018 if it is heated to a few hundred degrees and cooled with some light oil burning onto it. The blade looks "mono-steel" to me other than genuine antique wear effects. A puzzling aspect of it is that there are some small metal (or epoxy?) shapes between the guard and the blade shoulder corners. I wonder if these may be something the curator did to hold the restored assembly together?
Absence of evidence is not necessarily evidence of absence!
|
|
|
 |
Maurizio D'Angelo

|
Posted: Sat 29 May, 2010 10:42 am Post subject: |
|
|
Michael Edelson wrote: |
So what sword is that in your pics? Do you have a picture of the whole thing?
|
Is the famous sword of Vienna, S. Mauritius. Only with high magnification is more than 9000 pixels, so you can see the scrape.
With a normal resolution, these scratches are not visible, so.
Almost a contradiction: your photos are better quality than mine.
The continued reduction of the resolution gave a poor overall result, but the idea of the finish seems to have remained.
P.S.
No claim to post on this resolution.
Ciao
Maurizio
|
|
|
 |
|
You cannot post new topics in this forum You cannot reply to topics in this forum You cannot edit your posts in this forum You cannot delete your posts in this forum You cannot vote in polls in this forum You cannot attach files in this forum You can download files in this forum
|
All contents © Copyright 2003-2025 myArmoury.com All rights reserved
Discussion forums powered by phpBB © The phpBB Group
Switch to the Basic Low-bandwidth Version of the forum
|