
| myArmoury.com is now completely member-supported. Please contribute to our efforts with a donation. Your donations will go towards updating our site, modernizing it, and keeping it viable long-term. Last 10 Donors: Graham Shearlaw, Anonymous, Daniel Sullivan, Chad Arnow, Jonathan Dean, M. Oroszlany, Sam Arwas, Barry C. Hutchins, Dan Kary, Oskar Gessler (View All Donors) |
Author |
Message |
Chris Walton
Location: Cambridgeshire, England Joined: 16 Jan 2010
Posts: 3
|
Posted: Sat 16 Jan, 2010 10:35 pm Post subject: Anglo-Saxon Sword Manufacturing |
|
|
Very interested to know the details of acid etching in early pattern welding of A-S sword manufacture, such as how specifically the tanic acid was obtained? and at what point in the process does the etching occur??
On another subject. can anyone help me with the details on A-S mead brewing??
The hard-edged blade with its woven patterns quivers and trembles; grasped with terrible sureness, it flashes into changing hues.
- excerpt from the Anglo-Saxon poem Elene. Translated by H.R. Ellis Davidson
|
|
|
 |
Stephen Curtin
|
Posted: Sun 17 Jan, 2010 4:50 am Post subject: |
|
|
Hi Chris and welcome to myArmoury.
As far as I know we're not even sure if pattern welded swords were acid etched or not.
But if they were, it would probably be the very last thing done to the blade before it was sent to the cutler for hilting.
As for mead brewing, I'm sorry but someone wiser than I will have to fill you in on that one, all I can say is that I got
a couple of bottles of the stuff for christmas and it tastes really good
Éirinn go Brách
|
|
|
 |
Liam O'Malley
Location: New JErsey Joined: 17 Jan 2010
Posts: 29
|
Posted: Sun 17 Jan, 2010 1:24 pm Post subject: |
|
|
Chris Walton wrote: | Very interested to know the details of acid etching in early pattern welding of A-S sword manufacture, such as how specifically the tanic acid was obtained? and at what point in the process does the etching occur??
On another subject. can anyone help me with the details on A-S mead brewing?? |
it doesnt really make sense to do patternwelding without etching, it just looks like monosteel and the anglosaxons were certainly doing decorative patternwelding as well as functional. until you etch you cant see the contrasting steels at all unless you get right up close to it and hold it at exactly the right angle in the right light.
the etchants used can range from vinegar to tannic acid to pretty much any acid you can think of. vinegar is pretty straightforward, let wine get infected with acetobacter and voila, vinegar. tannic acid is used for any number of things from tanning leather to earlier forms of ink and dyes (most black dye in europe was tannic acid with a mordant made from iron filings) the tannic acid used in inks and dyes in later periods was oak galls, but it is possible to get tannic acid from boiling certain types of wood, especially oak, as well as from mashing and boiling animal brains, as in brain tanning leather. its really not hard stuff to come across.
as for when you etch, you generally heat treat, get the polishing done and get the edge almost sharp then etch, afterwards you do a very light draw polish, wipe it down with a cloth then stone the edge sharp and polish the edge in line with the blade. some people do it differently but that is how i was taught
as for mead anglo saxons probably weren't doing anything fancy. i'd have to dig through my sources (hopefully its not anything from before my comp crashed) but honey was a valuable commodity, so mead was probably not made from the actual honey. its a lot more likely they crushed up the combs after most of the honey had been extracted, washed them in a pot of warm or hot water, and got the honey that way, as well as a little wax which would function as a yeast nutrient. there are accounts in a few other later sources of it being done this way in both britain and the continent. its anyones guess if the saxons used spices, i tend to think they would have included fruits, grains, or grapes as i doubt the practice of hybrid booze simply stopped from late antiquity and magically restarted in the post-conquest isles. spices aren't really a stretch, pretty much anything tastes good with honey, its just a matter of what would have been available, some things you wouldnt expect to be there already were thanks to italian and viking trade routes. herbs are practically a given, gruit ales were well established as the norm by the point in the middle ages we have any real surviving documents, so the idea of the anglosaxons not using herbs in beers, wines, and meads seems a little unlikely.
yeast cultures were kept by anyone doing serious baking or brewing, but the first brew would probably have been done by simply sitting the fermentation vessel outside and letting wild yeast fall into it. they used the same yeast cultures for baking and brewing, which is why imho a few later sources advocate chucking some bread dough into mead to get it to ferment quicker.
hope that was at least slightly useful. sorry for lack of documentation, and sorry it was slightly longer than war and peace
|
|
|
 |
Hadrian Coffin
Industry Professional
Location: Oxford, England Joined: 03 Apr 2008
Posts: 404
|
Posted: Sun 17 Jan, 2010 2:20 pm Post subject: |
|
|
Quote: | it doesnt really make sense to do patternwelding without etching |
That's not exactly true, especially depending upon what century you are talking about. Pattern welding (especially if you include earlier forms such as pilling) was originally purely functional. It was difficult to create perfect mono steel, most of the time one ended up with iron or cast iron. Cast iron is very brittle, and thus unsuitable for sword manufacture. Iron is very soft, and so does not make particularly fine blades. Pattern welding and pilling were originally developed to combine steel, cast iron, and iron, in an effort to create a better blade. It was created for a functional purpose, but was soon found to create a decorative appearance. As steel became easier to produce pattern welding became rather unnecessary, and became more of a decorative function.
There is evidence to believe pattern welded blades were etched, but there is also evidence to say they were not. In all honesty, some were probably etched, and some where probably not. Without etching it is still possible to see the pattern welded structure. Especially as it gets older, because steel and iron age at different rates.
Cheers,
Hadrian
Historia magistra vitae est
|
|
|
 |
B. Stark
Industry Professional

|
Posted: Sun 17 Jan, 2010 4:16 pm Post subject: |
|
|
I doubt that they were etched. Purely from the standponit that it creates a more pourous surface that would encourage rusting and decay. A quality I'd imagine would be fowned upon for an expensive sword. Not to mention any historical or contemporary descriptions of pattern welded blades and that the pattern could be observed by breathing on the blade. I would imagine that the 'weld-grain' could be easily observed under various light conditions. Much the same way that a katana's hada is revealed. Certainly an old blade would reveal 'more' of this character, as was stated, the iron and steel would tarnish at varying rates thus creating more contrast between the metal elemnts of the weld. I doubt that conditions would be allowed to reach a state of servere 'etch' for the above reasons and the blade would be furbished back up to polish.
"Wyrd bi∂ ful aræd"
|
|
|
 |
Liam O'Malley
Location: New JErsey Joined: 17 Jan 2010
Posts: 29
|
Posted: Sun 17 Jan, 2010 5:24 pm Post subject: |
|
|
Hadrian Coffin wrote: | Quote: | it doesnt really make sense to do patternwelding without etching |
That's not exactly true, especially depending upon what century you are talking about. Pattern welding (especially if you include earlier forms such as pilling) was originally purely functional. It was difficult to create perfect mono steel, most of the time one ended up with iron or cast iron. Cast iron is very brittle, and thus unsuitable for sword manufacture. Iron is very soft, and so does not make particularly fine blades. Pattern welding and pilling were originally developed to combine steel, cast iron, and iron, in an effort to create a better blade. It was created for a functional purpose, but was soon found to create a decorative appearance. As steel became easier to produce pattern welding became rather unnecessary, and became more of a decorative function.
There is evidence to believe pattern welded blades were etched, but there is also evidence to say they were not. In all honesty, some were probably etched, and some where probably not. Without etching it is still possible to see the pattern welded structure. Especially as it gets older, because steel and iron age at different rates.
Cheers,
Hadrian |
i can see where you are coming from, but i would like to point out that the cast iron/wrought iron patternwelding was contemporary to the La Tene culture in switzerland a few hundred years BCE and that bloomed steel was prevalent by the roman iron age. carburizing wrought in a charcoal fire is not very hard, and requires no additional equipment, whereas making cast iron requires a blast furnace, you can not impart enough carbon into ferrous metal to cause it to become hypereutectoid through a cementation process, it must be dissolved in a liquid phase ala wootz or crucible steel, which based on archaeological evidence from germanic blooming sites is not how they were doing it..
I'd been replying to a question about anglo saxon patternwelding, a people who through their pattern manipulation created works of art, which while having a function, were also intended to look beautiful. this is a big step up from the 1000 years earlier "smack it together and hope it doesnt shatter or bend" approach to bladesmithing. i was not saying pattern welding in the anglo saxon world was just to look pretty.
while by breathing on it you MIGHT be able to make out a pattern (I'm doing this to an unetched blade right now, its not working very well) it seems a lot of effort to go through twisting those patterns and continually rewelding them so they don't split to make something thats only visible when it fogs up. etching seems a lot more likely than the alternative, and an etch really doesnt cause a blade to rust faster, especially when its coated in lanolin by the lambswool lined scabbard used by the vikings and anglo-saxons.
i could be wrong, but thats just what i think.
|
|
|
 |
Liam O'Malley
Location: New JErsey Joined: 17 Jan 2010
Posts: 29
|
Posted: Sun 17 Jan, 2010 5:43 pm Post subject: |
|
|
sorry i didnt include an address to this
B. Stark wrote: | I doubt that they were etched. Purely from the standponit that it creates a more pourous surface that would encourage rusting and decay. A quality I'd imagine would be fowned upon for an expensive sword. Not to mention any historical or contemporary descriptions of pattern welded blades and that the pattern could be observed by breathing on the blade. I would imagine that the 'weld-grain' could be easily observed under various light conditions. Much the same way that a katana's hada is revealed. Certainly an old blade would reveal 'more' of this character, as was stated, the iron and steel would tarnish at varying rates thus creating more contrast between the metal elemnts of the weld. I doubt that conditions would be allowed to reach a state of servere 'etch' for the above reasons and the blade would be furbished back up to polish. |
The majority of the pattern welded blades were contrasting high P and low P wrought or Carburized low P (think shear steel) and high P wrought so it still doesnt make sense. the phosphoric iron would only contrast if etched, and wouldn't really do much else as it doesnt heat treat very well. unless you're etching it there's no reason for an anglo saxon smith in england to bother phozphorizing wrought iron for it not to show up. if only the welds were showing (assuming they didn't etch) again, you have a bit of a puzzler, why use such contrasted metals if you're not going to have the contrast show?
i also doubt blades would have been allowed to rust. either they were so precious or so often used that letting a little pitting in would have been considered extremely bad form. oiling a blade daily isnt that much effort imho, and i suspect when a blade cost as much as a luxury sedan would in the modern era maintenance would have been regular and thorough. i've heard people allege that blades were kept tarnished or browned because of the whole brunecg reference in beowulf, but i think that refers more to the temper of the blade than the appearance.
|
|
|
 |
Hadrian Coffin
Industry Professional
Location: Oxford, England Joined: 03 Apr 2008
Posts: 404
|
Posted: Sun 17 Jan, 2010 6:20 pm Post subject: |
|
|
Ah I see where you where coming from...my mistake I misinterpreted what you where saying. As for the cast iron it can be created during the carbonization of wrought iron, albeit in small amounts. I think its earliest use in Europe was 1150, I don't know what I was getting at earlier. I was tired, and using the wrong terms. The reason for pattern welding was basically to preserve steel, and to mix steel into iron.
Cheers
Historia magistra vitae est
|
|
|
 |
Jeroen Zuiderwijk
Industry Professional
|
Posted: Mon 18 Jan, 2010 12:51 am Post subject: |
|
|
Patternwelding in the early medieval period was purely aesthetic. There's a couple of things you have to keep in mind: hardenable steel in those times was a lot more rare and expensive compared to plain iron. Secondly, the hardenable steel in those days was very shallow hardening, which means that only the thin edges of swords, saxes etc. would harden. The rest of the blade will stay soft, unless it's very thin (which was the case in certain swords). If the sword can be made thin enough to fully harden it, it makes no sense to include soft iron which will weaken an otherwise perfect hardened steel sword. If the sword doesn't fully harden, it makes no sense to waste perfect hardenable steel in areas that stay soft, although the higher carbon steel is a bit stronger then soft iron in unhardened conditions.
As for the appearance of patternwelding without etching, here's what simple wrought with a welded on steel edge looks like without any etching and just a simple polish:
http://forums.dfoggknives.com/uploads/monthly...260392.jpg
As you can see, the wrought already easily shows the piled structure of the wrought, and that's not even with different types of steel. So patternwelding doesn't need etching to show. However, there's a Viking period sword (of which I can't find the picture at the moment) with the original surface still mostly intact which shows a deep etch within the patternwelded fuller.
Another piece of evidence on the visibility of patternwelding, drawings in the Stuttgard Psalter (820-830AD), sometimes show the swords depicted with snakes on the blade. So it must have been something that stood out well enough to be included in the drawings, despite the relatively low detail of the drawings (relatively, there's still a wonderful wealth of detail in there to learn a great amount on the clothing, armour and weapons of the period, which is in many repects completely different from what reenactors use, but that's a different subject).
Jeroen Zuiderwijk
- Bronze age living history in the Netherlands
- Barbarian metalworking
- Museum photos
- Zip-file with information about saxes
|
|
|
 |
Peter Johnsson
Industry Professional
|
Posted: Mon 18 Jan, 2010 2:42 am Post subject: |
|
|
Below an example of a well preserved viking sword. In places the original surface survives and clearly shows the amount of etching that was done. It is not limited to color contrast, but was done so there is a topographic effect. I do not know what type of acid that may have been used. Note that you can even see some color contrast in the piled structure of the edge steel!
I´ve also attached examples of celtic swords where selective etching was done to emphasize the structure of the material At first I thought the edges were separate strips that had been welded on, but after some careful looking it came clear that the blades are forged from one sinlge length of piled material and a resist applied to the edge, while the center is exposed to acid. Pretty clever as you will want to re sharpen the blade without marring the nice etched surface: the un etched edges can be brought back to polish, while the core remains untouched.
So we can see that even with the early forms (at least 2nd & 1st C BC) of piled structure composed of material with different alloy content, there was an awareness that a strong aesthetic effect could be achieved through etching.
These are not examples of anglo axon blade work, I know, but I feel pretty sure rather similar techniques were used all over Europe where pattern welding was used. Sometimes the steel may have ben left without etching of course, but I think etching was common and possibly even the norm when patterned material was used. Probably not to bring out structure of simple wrought iron however.
Attachment: 72.7 KB
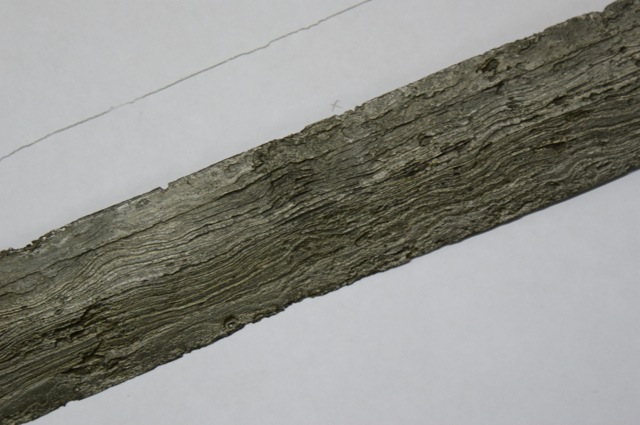
Note that the strands in the steel undulate back and forth between etched core and non etched edge zone
Attachment: 86.56 KB
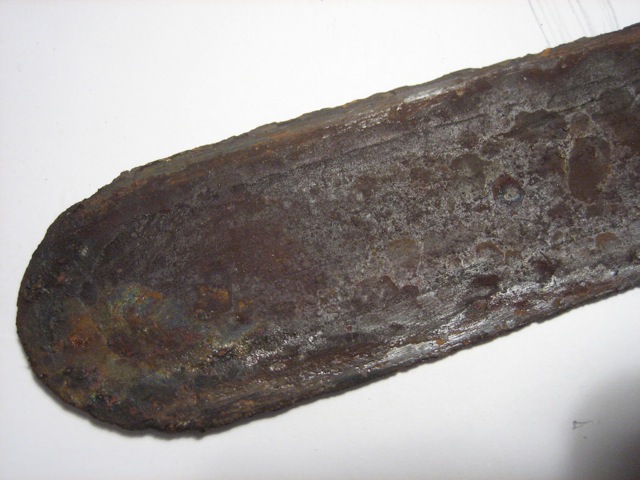
Another celtic sword with selectively etched mid panel. ...I know, it is not very clear this is so from the image posted...
Attachment: 103.39 KB
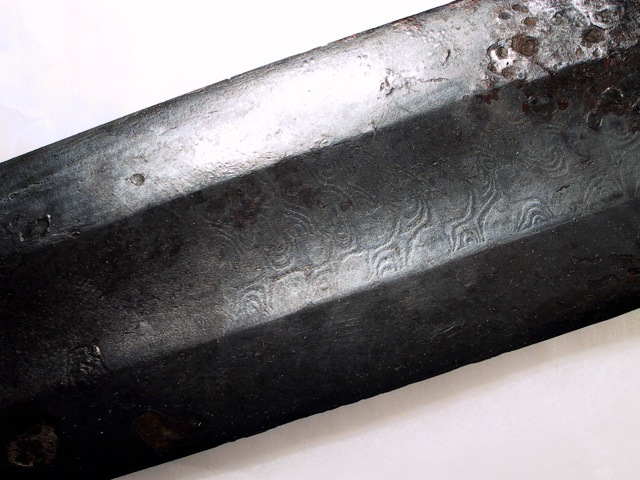
Viking sword: note how the etching is isolated to the pattern welded material in the fuller. The edges have a smooth polished surface.
Attachment: 166.81 KB

And yet another etched celt...
|
|
|
 |
Chris Walton
Location: Cambridgeshire, England Joined: 16 Jan 2010
Posts: 3
|
Posted: Tue 19 Jan, 2010 10:53 am Post subject: Mmmm |
|
|
Cheers guys some excellent food for thought, but how was the etch effectiveley applied??
The hard-edged blade with its woven patterns quivers and trembles; grasped with terrible sureness, it flashes into changing hues.
- excerpt from the Anglo-Saxon poem Elene. Translated by H.R. Ellis Davidson
|
|
|
 |
Liam O'Malley
Location: New JErsey Joined: 17 Jan 2010
Posts: 29
|
Posted: Tue 19 Jan, 2010 12:03 pm Post subject: Re: Mmmm |
|
|
Chris Walton wrote: | Cheers guys some excellent food for thought, but how was the etch effectiveley applied?? |
i just drop mine in vinegar for a few days, check em occasionally though, cause if you forget they're in there too long you'll turn a great patternwelded blade into a brown crusty toothpick.
|
|
|
 |
Jeff Pringle
Industry Professional
Location: Oakland, CA Joined: 19 Nov 2005
Posts: 145
|
Posted: Wed 20 Jan, 2010 6:36 am Post subject: |
|
|
Just to confuse matters I’ll point out this sword I made, which has about the same amount of topography as Peter’s Swedish Viking sword, was not etched. The pattern was brought out solely by differential scaling rates of the two metals during heat treating.
And that al Kindi, who was all about etching, wrote his early 9th century comparison of swords that the Frankish ones did not show their patterns until he etched them.
Also, somewhat conversely, I have found that pattern-welding (with phosphorus or carbon) shows up fairly well without etching – IF you use stones and powdered abrasives (1000-year old technology) instead of sandpaper and buffing wheels.
|
|
|
 |
Russ Ellis
Industry Professional
|
Posted: Wed 20 Jan, 2010 6:54 am Post subject: |
|
|
I appreciate the discussion gentleman, most informative all around.
TRITONWORKS Custom Scabbards
|
|
|
 |
Liam O'Malley
Location: New JErsey Joined: 17 Jan 2010
Posts: 29
|
Posted: Wed 20 Jan, 2010 6:47 pm Post subject: |
|
|
Jeff Pringle wrote: |
Also, somewhat conversely, I have found that pattern-welding (with phosphorus or carbon) shows up fairly well without etching – IF you use stones and powdered abrasives (1000-year old technology) instead of sandpaper and buffing wheels.
 |
i'm really glad i heard you say that. i'm planning to make some shear steel, further refine some wrought and phosphorize some wrought for a pattern welded blade and i probably would have ground it all on a belt sander and taken it to 500 then gotten angry that i couldnt see anything, and gone all petr and ritually killed it lol.
|
|
|
 |
Jeroen Zuiderwijk
Industry Professional
|
Posted: Thu 21 Jan, 2010 2:15 am Post subject: |
|
|
Liam O'Malley wrote: | Jeff Pringle wrote: |
Also, somewhat conversely, I have found that pattern-welding (with phosphorus or carbon) shows up fairly well without etching – IF you use stones and powdered abrasives (1000-year old technology) instead of sandpaper and buffing wheels.
 |
i'm really glad i heard you say that. i'm planning to make some shear steel, further refine some wrought and phosphorize some wrought for a pattern welded blade and i probably would have ground it all on a belt sander and taken it to 500 then gotten angry that i couldnt see anything, and gone all petr and ritually killed it lol. |
Phosporizing good wrought? I throw that on the scrap heap if I come across it. I know it can be forged as Jeff showed in some very nice examples, but to me it's only been a pain in the rear end as it cracks if you accidentally deform anything that's not around welding temperature. If you need any, I can cut off the not yet cracked parts of the wall anchors that I have. I'm actually happy at the one wall anchor in the 4 that I put in my forge is actually free of phosphorous, so it forges very nicely without any cracking.
Jeroen Zuiderwijk
- Bronze age living history in the Netherlands
- Barbarian metalworking
- Museum photos
- Zip-file with information about saxes
|
|
|
 |
Liam O'Malley
Location: New JErsey Joined: 17 Jan 2010
Posts: 29
|
Posted: Thu 21 Jan, 2010 11:27 am Post subject: |
|
|
Jeroen Zuiderwijk wrote: |
Phosporizing good wrought? I throw that on the scrap heap if I come across it. I know it can be forged as Jeff showed in some very nice examples, but to me it's only been a pain in the rear end as it cracks if you accidentally deform anything that's not around welding temperature. If you need any, I can cut off the not yet cracked parts of the wall anchors that I have. I'm actually happy at the one wall anchor in the 4 that I put in my forge is actually free of phosphorous, so it forges very nicely without any cracking. |
i'd read it was done to some wrought, or that they used high phosphorous wrought, mainly for decorative purposes on the back of pattern welded blades to contrast (kind of like high nickel steels). i know it heat treats funny, but i wasn't planning to put it on functional bits.
|
|
|
 |
Chris Walton
Location: Cambridgeshire, England Joined: 16 Jan 2010
Posts: 3
|
Posted: Thu 21 Jan, 2010 11:05 pm Post subject: |
|
|
Thanks guys, brilliantly helpful, if i have anymore questions i'll pipe up.
The hard-edged blade with its woven patterns quivers and trembles; grasped with terrible sureness, it flashes into changing hues.
- excerpt from the Anglo-Saxon poem Elene. Translated by H.R. Ellis Davidson
|
|
|
 |
M. Eversberg II

|
Posted: Fri 22 Jan, 2010 9:47 am Post subject: |
|
|
In period, would wrought with phosphorous still get used as-is (assuming the phosphorous didn't make it too hard to even work with), or would it have gone to a secondary market? Is there a way to remove the impurity using their technology? How common was this contaminated iron?
M.
This space for rent or lease.
|
|
|
 |
Liam O'Malley
Location: New JErsey Joined: 17 Jan 2010
Posts: 29
|
Posted: Fri 22 Jan, 2010 11:26 am Post subject: |
|
|
M. Eversberg II wrote: | In period, would wrought with phosphorous still get used as-is (assuming the phosphorous didn't make it too hard to even work with), or would it have gone to a secondary market? Is there a way to remove the impurity using their technology? How common was this contaminated iron?
M. |
afaik its pretty common, and it can be used, just not for certain things. steel making from phosphoric iron is difficult because high phosphorus+high carbon = shatter prone steel. i do know until the 1800s and the advent of crucible steel leading up to bessemer, most european countries imported iron bars from sweden, which had naturally phosphorus free ore.
|
|
|
 |
|
You cannot post new topics in this forum You cannot reply to topics in this forum You cannot edit your posts in this forum You cannot delete your posts in this forum You cannot vote in polls in this forum You cannot attach files in this forum You can download files in this forum
|
All contents © Copyright 2003-2025 myArmoury.com All rights reserved
Discussion forums powered by phpBB © The phpBB Group
Switch to the Basic Low-bandwidth Version of the forum
|