Author |
Message |
Michael Pikula
Industry Professional
|
Posted: Mon 08 Dec, 2008 8:42 am Post subject: Two pattern welded seaxes |
|
|
Hello everyone. I have two pattern welded seaxes that I finished rehilting yesterday. Both of them have Zebra wood handles, the smaller one has brass fittings, the larger one has copper fittings. Everything on these was made from scratch, even the rivets. The smaller on has an 8 7/8 inch blade, 13 1/2 over all, and I am asking for $200 for this piece. The larger one has a 13 1/2 inch blade, 18 inch over all, and I am asking for $450. As with all my work if you are not happy with the piece for any reason you can return it within the first week in like new condition for a refund and all craftsmanship is guaranteed under normal wear and tear for the life of the blade. If there are any questions, comments, or requests let me know!
Thanks
Attachment: 147.89 KB
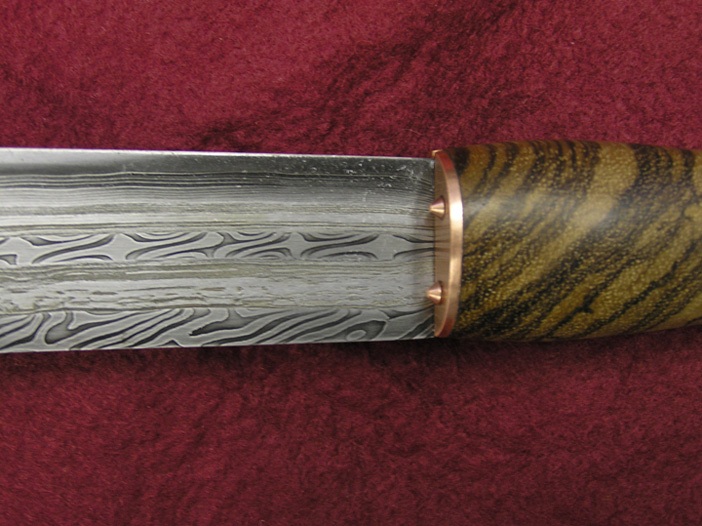
Attachment: 133.85 KB
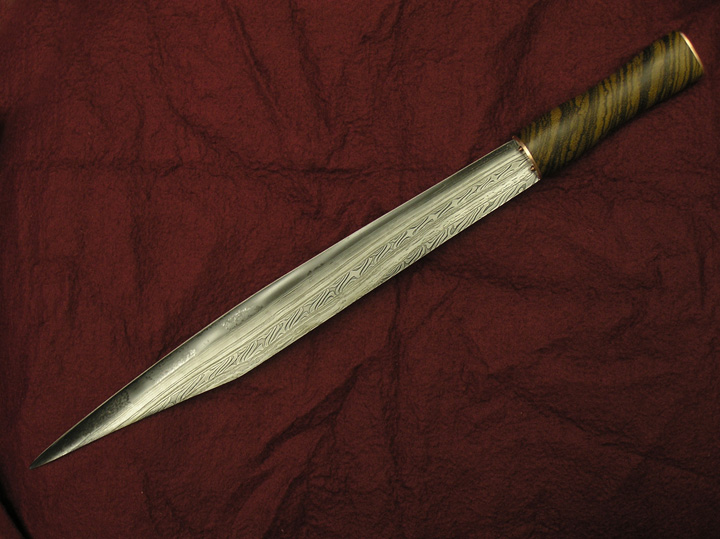
Attachment: 107.99 KB
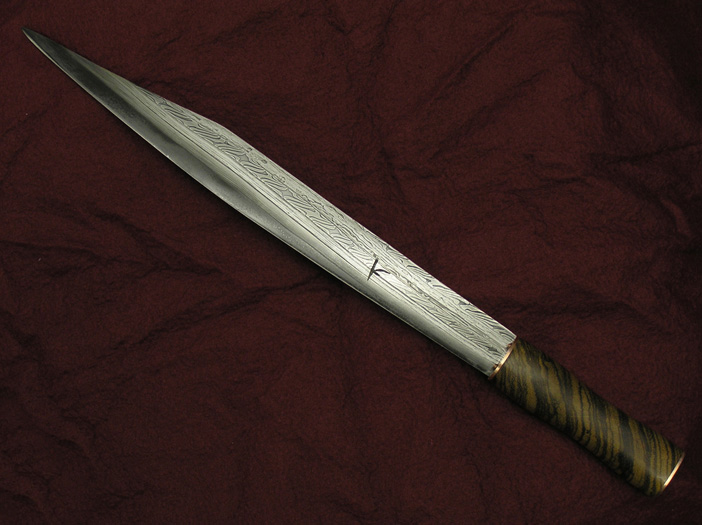
Attachment: 149.68 KB
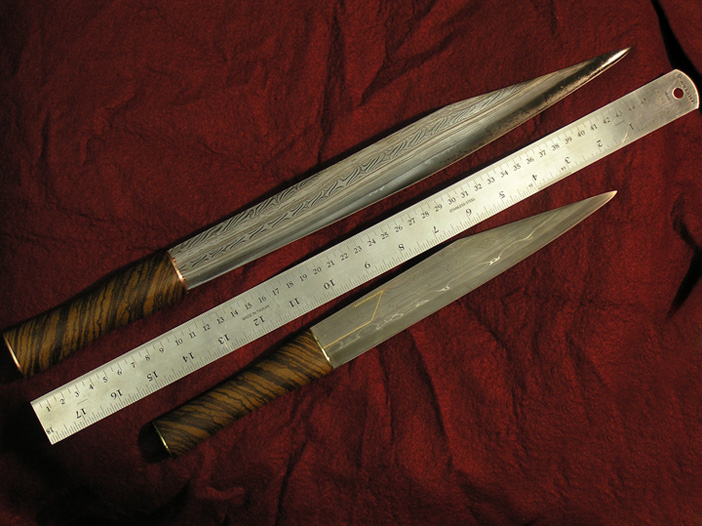
|
|
|
 |
Michael Pikula
Industry Professional
|
Posted: Mon 08 Dec, 2008 8:47 am Post subject: |
|
|
And the last 5 images since I couldn't fit all 9 in one post.
Attachment: 135.99 KB
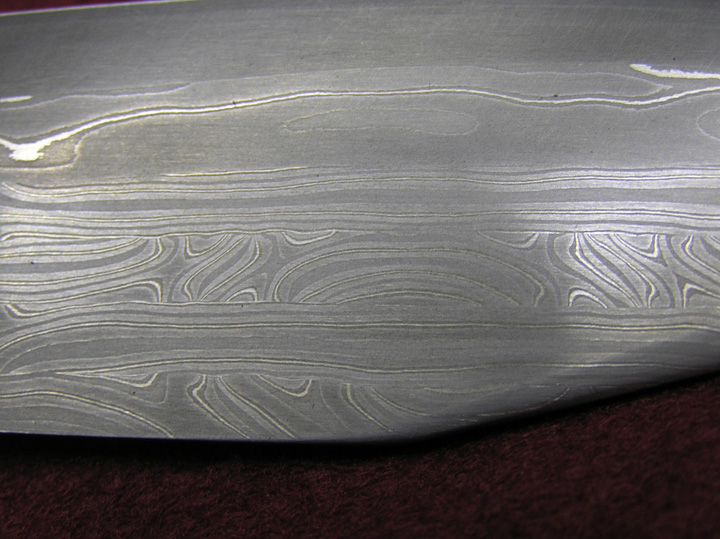
Attachment: 126.2 KB
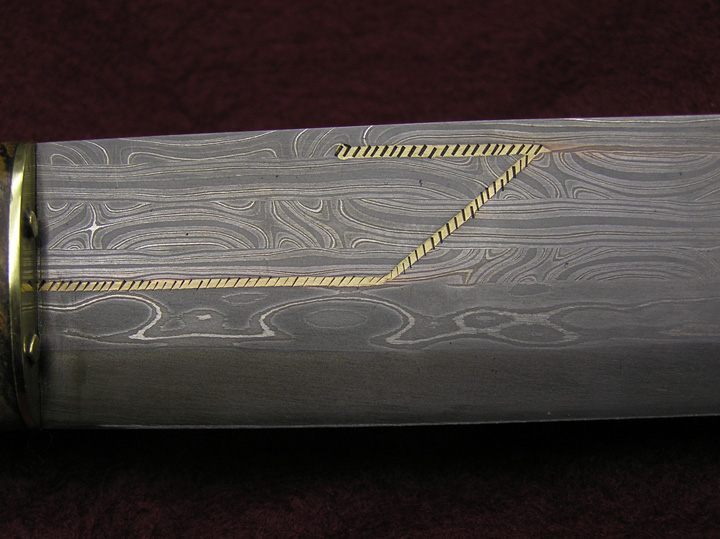
Attachment: 148.47 KB
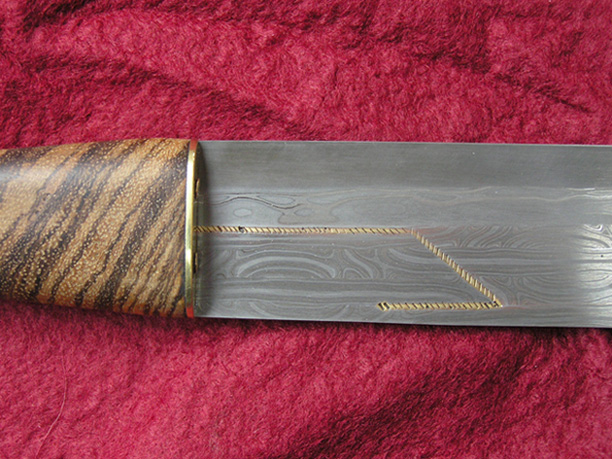
Attachment: 102.86 KB
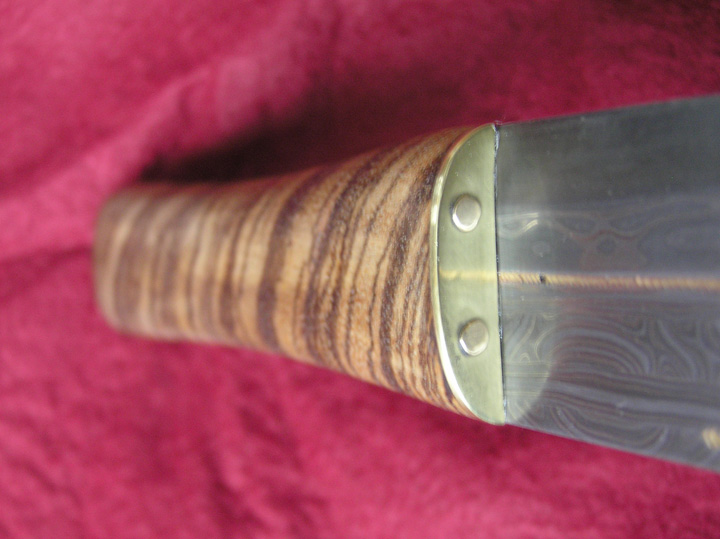
Attachment: 143.62 KB
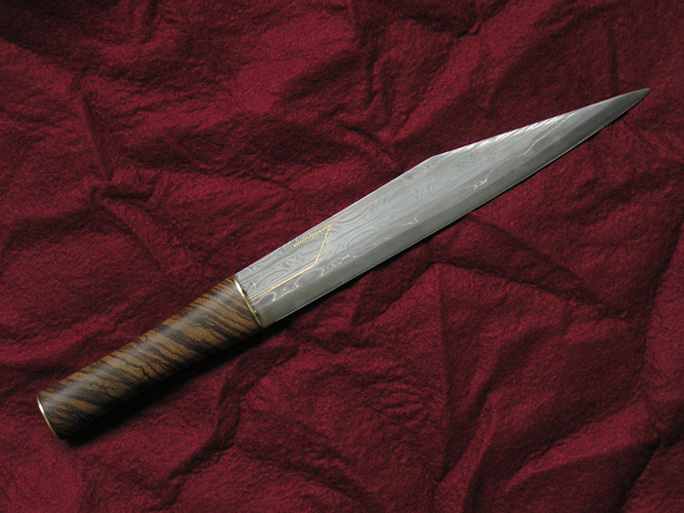
|
|
|
 |
Tim Lison
|
Posted: Mon 08 Dec, 2008 9:23 am Post subject: |
|
|
PM sent!
|
|
|
 |
Michael Pikula
Industry Professional
|
Posted: Mon 08 Dec, 2008 10:03 am Post subject: |
|
|
The big seax is sold!
|
|
|
 |
Matthew Stagmer
Industry Professional
|
Posted: Tue 09 Dec, 2008 7:37 am Post subject: |
|
|
Nice work. I have enjoyed watching your work progress. Keep it up.
Matthew Stagmer
Maker of custom and production weaponry
Youtube.com/ThatWorks
|
|
|
 |
Michael Pikula
Industry Professional
|
Posted: Tue 09 Dec, 2008 8:43 am Post subject: |
|
|
Thanks Matt I love doing what I do and I hope that it shows in my work. Postive feedback and knowing that others enjoy it as well is a good feeling!
|
|
|
 |
Jean Thibodeau

|
Posted: Tue 09 Dec, 2008 9:03 am Post subject: |
|
|
Great looking work and are you sure you didn't drop a 0 there on the price.
Looks like the kind of work that should bring a 4 figure price and not just 3 ! But, I'm glad for the buyer and if you are happy with what you are getting for it I happy for you also ....... but this kind of work is awesome !
You can easily give up your freedom. You have to fight hard to get it back!
|
|
|
 |
Michael Pikula
Industry Professional
|
Posted: Tue 09 Dec, 2008 10:02 am Post subject: |
|
|
Thanks for the complement Jean. I know I didn't drop a 0 in the price... yet! I am kind of playing to the market in that I know the economy is not the greatest and also not too many people know who I am. So I figure doing good work, offering it at a great price is my way of riding out the hard times and still being able to get my works into people’s hands so that I can make a name for myself. Plus that way if I get feedback regarding things that need improving, I can make those changes and be offering a better product as the prices rise to find that happy balancing point! At least that is the model that I have been trying to follow.
|
|
|
 |
Matthew Stagmer
Industry Professional
|
Posted: Tue 09 Dec, 2008 12:55 pm Post subject: |
|
|
Yea I was thinking the same thing. Cheap prices... I would at least be at $800 for the larger.
Matthew Stagmer
Maker of custom and production weaponry
Youtube.com/ThatWorks
|
|
|
 |
Michael Pikula
Industry Professional
|
Posted: Tue 09 Dec, 2008 2:15 pm Post subject: |
|
|
I am starting to see a common response in that my prices are a bit too cheap. I suppose that is better then being told they are too high though! Pricing my work is the hardest part of making a piece for me, and this is something I am going to have to work on... But that is going to have to wait for my next piece. Anyone want to volunteer to become a member of the official "Volund Forge Pricing committee"
|
|
|
 |
Carl W.
|
Posted: Tue 09 Dec, 2008 7:17 pm Post subject: |
|
|
I really like the shape of the large blade, including subtle curves. Gently hints at a seax to bowie evolution that seems logical & natural to me. Not sure if that was intentional, or if experts would dispute such a link, but nice!
(ps. also, I for one like your original business plan to err on side of good cash flow & to minimize inventory. :-)
|
|
|
 |
Jean Thibodeau

|
Posted: Tue 09 Dec, 2008 8:02 pm Post subject: |
|
|
Michael Pikula wrote: | I am starting to see a common response in that my prices are a bit too cheap. I suppose that is better then being told they are too high though! Pricing my work is the hardest part of making a piece for me, and this is something I am going to have to work on... But that is going to have to wait for my next piece. Anyone want to volunteer to become a member of the official "Volund Forge Pricing committee" |
Well, low prices do mean that even in a challenging economic period the knives or swords will sell quickly and the ready cash may be useful to you.
As well you are getting known and the prices can go up later if you get so much volume in orders that you can't keep up then adjusting the prices up should happen naturally.
Obviously, those lucky enough to have ready cash at the moment are not going to complain too much about getting some of your work before the demand makes your prices higher, as they should be, eventually.
If you are doing this work as a second job then the hourly rate you are getting for the work is less important: I assume that this is at least a work of love and not just a way to make a living. In any case I'm greatly impressed by the artistry of the work.
You can easily give up your freedom. You have to fight hard to get it back!
|
|
|
 |
Mike Capanelli

|
Posted: Tue 09 Dec, 2008 8:18 pm Post subject: |
|
|
Looks like I'll be a part of that committee soon.
Winter is coming
|
|
|
 |
Michael Pikula
Industry Professional
|
Posted: Tue 09 Dec, 2008 9:56 pm Post subject: |
|
|
Thanks guys! To be honest I am falling into the norm where I know how to make good product, but the whole business end meaning pricing, audience, customers, advertising, are all my weak points. I got into this thinking that if I make the best work I can then eventually everything WILL work itself out.
Carl, I don't think that it was intentional, I was working with some cut offs that I had that were very clean and the piece kind of naturally evolved as I was working on it. Some times I like to just grab some steel and start forging it, knowing what I am doing, but let the steel tell me where it wants to go and what it wants to do. I defiantly see the connection that you are talking about with the evolution to the bowie.
However, there have been some very interesting points and philosophies brought up here in the thread and through PM's that make me realize several points that I am going to have to think long and hard on with my up coming pieces. One of them being if I am selling good quality work now for $450, how easy is it going to be to sell the same level or slightly better quality of work two years from now for what it really should be worth? Also if someone knows that one of the pieces I made should have a price tag that is double or triple of what it is really worth, will they take me seriously as a custom maker that is trying hard to make a living at this? These are questions that before today I really haven't thought about, and since I have no other source of income I need to find a better balance between keeping alive and looking at how my decisions today will not only effect tomorrow but next year and 5 years from now. Make no mistake, if I have to hunt down deer and grow my own garden for food and use the money I make to pay for gas and electricity I will do it, but I am here to stay. This IS what I will be doing for the rest of my life, for not so rich and for poor.
As for the pricing committee, I wasn't totally serious about it, but if anyone is interested in getting an e-mail with pictures of new work as I finish it, before posting it online, to give feedback and suggest "what you would pay" then send me a PM! Seeing as how the two things mentioned above have been brought into focus, I may be starting to charge more, even if it means having lots of stock. I guess that means I can finally start a collection of my own!
I know this has slid off topic, I just can't justify starting a new thread titled "Pricing my work," I just don't have the ego to go there.
|
|
|
 |
Michael Pikula
Industry Professional
|
Posted: Sat 20 Dec, 2008 1:39 pm Post subject: |
|
|
Both seaxes are sold. Thanks for looking!
|
|
|
 |
Zach R
|
Posted: Tue 30 Dec, 2008 4:37 pm Post subject: |
|
|
I received the smaller of the two seax's a few days ago and have been meaning to post a review as requested( sorry for the delay Michael)
I've not done to many reviews but ill give it a shot. The blade has a composite back of 1095, nickel, A203E, 8056M, 1020 with a cutting edge of L6. The pattern is very well done and the nickle gives an amazing contrast that combines with the steels to make the overall appearance subtle yet beautiful upon close inspection. The L6 edge blends in well with the pattern of the spine and is viciously sharp.
The knife is very light and has a somewhat blade heavy feel that goes wonderfully with the overall chopper style of the seax pattern. It made short work of several soda bottles ( though i was almost loath to risk any scratches or wearing from use to this little beauty)
The striation pattern of the wood grain in the handle blend perfectly with the pattern welding and the wood feels as smooth as the blade itself.
I have always loved the seax pattern and i think that Mr. Pikula has done a wonderful job on this blade. I am glad that the first seax added to my collection is such a work of art and function and it was a pleasure to make the transaction.
|
|
|
 |
|