Author |
Message |
Stephanie Maks

|
Posted: Fri 18 Jul, 2008 6:56 am Post subject: Some projects I've started... feedback, comments welcome! |
|
|
I've been interested in edged weapons for as long as I can remember, and have been collecting a few pieces on-and-off for about 20 years. I've also been very eager to make my own knives / swords, but have been limited to just doing cutlery work - buying knife blades and doing my own handles / guards, and buying (dirt cheap decorative) replica swords and replacing the nasty plastic handles and garbage parts with my own designs.
Inspired by the folks here at myArmoury.com I've decided to undertake a trio of projects that are a lot more intensive.
I purchased an antique Katana blade about 4 or 5 years ago as a project piece - the blade was damaged (which is how I was able to afford it), but I had hopes I could fix it somehow. It had a nasty chip on the edge as well as a bend, in addition to some minor pitting. After some research and asking around, the conclusion I came to was that there was no cheap and easy way to fix it back into a straight and workable Katana. The bend and chip were both 8 or 9 inches from the tip, and one suggestion I was given was to cut it at that point, and fashion it into both a small tanto and a wakizashi. It's taken 4 or 5 years but I've finally returned to that project blade, and decided to proceed with that suggestion.
It felt kind of sacreligious to cut it - even though it was more or less 'trashed' already... it was also an interesting process, as I used a hacksaw and cut the blade in from one side then the other. I could feel the softer metal on the sides and across the back, but when I got in to where the temper line was, the hacksaw just simply stopped working - it could no longer bite as it reached the hardened steel.
I now had about an 8" tip and a 'wakizashi' with a 17.5" blade and no tip. I've been gradually grinding the top end, it is shaping into a knife with a 4" blade and 4" tang. At the same time, I'm working on putting a new tip on the wakizashi end. It's been slow going, as I've never used a grinder before - I just bought a 6" bench grinder for these projects. It's also a good lesson in patience.
My plan is to finish the wakizashi in a "more or less traditional" shape and style - I have an old tsuba I picked up some years ago, and the katana blade came with its original habaki so once the tip is finished I will just have to make my own version of tsuka.
The tanto / knife, I have not yet decided what style it will be. I don't think it will be quite traditional, at the moment I'm leaning to making something that 'feels right' to me, without being constrained by historical accuracies.
The third project, which is separate from the two aforementioned, will be a sword that is inspired by the celtic weapons. I grabbed a "Del Tin Orcrist" blade from Albion's moat sale, and intend to grind off the fanciful ricasso on there and essentially shorten the blade by 4" while adding 4" to the tang -- I enjoy longer handles on shorter blades, and want to make sort of a Type XIII kind of sword, but with the hilt taking more inspiration from celtic / migration eras -- i.e. more wood and organic shapes (but not anthropomorphic.)
I'll add some photos shortly - the knife will probably be the first to completion as I have the tang nearly ready, and the wak will be next I think, as the hard work is confined to just the tip. The Del Tin blade project is going to be the slowest / last one finished, I think. With all three of these projects, I expect some setbacks and problems, as this really is my first crack at working with steel.
Cheers!
-Stephanie
|
|
|
 |
Sean Flynt

|
Posted: Fri 18 Jul, 2008 7:09 am Post subject: |
|
|
Wow! I love to see folks jump in the deep end! Good for you and good luck on these projects. Don't hesitate to ask folks here for advice, as they've certainly been of great help to me. Even when I've just had to figure out something on my own, the support of this community has been inspiring. Also, publicly posting one's intentions here also serves as a prod to keep working. There have been a few times when that public (but nonbinding) commitment has pushed me over rough patches in projects when I might otherwise have have "taken a break" or abandoned a project altogether.
-Sean
Author of the Little Hammer novel
https://www.amazon.com/Little-Hammer-Sean-Flynt/dp/B08XN7HZ82/ref=sr_1_1?dchild=1&keywords=little+hammer+book&qid=1627482034&sr=8-1
|
|
|
 |
Thom R.

|
Posted: Fri 18 Jul, 2008 10:45 am Post subject: cool |
|
|
Welcome. I am a hacker and love these kinds of projects - taking blades from the "Island of lost steel" and making something useful out of them. Half the fun for me is working in the shop. I similarly bought a broken katana (shinto- mumei) which Pierre Cayla had run on ebay for months on end with no takers. Only the hilt end was left and I ground the end down, gave it a simple hilt and turned it into a kitchen knife for my brother who is a chef. He loves it although because of the type of steel it requires careful upkeep when used in that context. Please share pictures when you get the inclination to do so and can't wait to see how the del tin blade turns out. TR
ps not to steer you away from here but on SFI (www.swordfurm.com) there is a whole board dedicated to "home improvement projects" which is always worth searching thru if you have a specific issue or question that needs answering
pps Don Fogg's website http://forums.dfoggknives.com/ is another great place to go for info on various issues of blademaking.
Last edited by Thom R. on Fri 18 Jul, 2008 12:53 pm; edited 1 time in total
|
|
|
 |
Anders Backlund
|
Posted: Fri 18 Jul, 2008 12:02 pm Post subject: |
|
|
Well, damn. And here I thought shortening my saber was scary, and you go and cut an antique katana in half. You've got guts, I'll give you that. Hope it all turns out well.
Also, I request pictures of these projects.
The sword is an ode to the strife of mankind.
"This doesn't look easy... but I bet it is!"
-Homer Simpson.
|
|
|
 |
Stephanie Maks

|
Posted: Fri 18 Jul, 2008 1:39 pm Post subject: |
|
|
Thanks for the words of encouragement! I have a couple of pictures but I have to apologize for the quality... I need to invest in some adequate lighting, or wait for a day with a bit more sunlight.
I have just about finished grinding a tang onto the tanto / katana-tip. I may need to work a bit more on tapering it thinner - Can you call it a 'distal taper' on the tang? The tang's profile is where I want it, and I managed to get a peg hole into it. I will probably go for epoxy & a rivet, rather than a traditional grip, though. It is a pretty beefy blade for a knife - it is 1/4" thick and weighs 4 1/2 ounces as-is. The tang is 4 1/4 inches long and the blade also about 4 1/4 inches. Apologies for the black tape but the blade is like a straight-edge razor and scares me a bit. There is a faint hamon, and when I have finished the handle and removed the tape, I will try and get a good photo to show the hamon. The sketch below the blade is one of the ideas I am considering for the handle - it will be brass at either end, and wood in between.
I've got a tip outline ground onto the wakizushi / rest of the katana, but haven't started working on beveling it into a rough edge. I imagine that will be difficult. Like with the tanto, the tape is there while I'm working with it, so I keep all my fingers - and also like the tanto, there is a faint but visible hamon. I don't know what to do about hardening / tempering the tip when it is done - I imagine I will just leave the tip unhardened, while the edge remains hard.
For the Del Tin blade, I've only got as far as figuring out what I want to cut away. I have some ideas in mind for the hilt but haven't got anything sketched out yet. The green indicates where I wish to cut at the shoulders and extend the tang. This will reduce the blade length from 32" to 28".
Cheers!
-Stephanie
Attachment: 58.8 KB
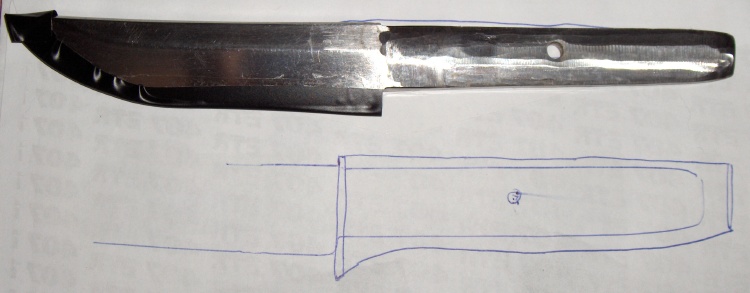
The katana-tip / tanto project, with a tang almost ready.
Attachment: 70.32 KB
The rest of the katana as a wakizushi, tip profiled but not bevelled. [ Download ]
Attachment: 53.42 KB
Planned changes to the Del Tin Orcrist blade. [ Download ]
|
|
|
 |
Stephanie Maks

|
Posted: Fri 18 Jul, 2008 9:29 pm Post subject: |
|
|
I have finished the grinding on the tanto / katana tip. One thing's for sure - I need more practice with the grinding wheel!
I've also got a grip roughed out, it's clamped at the moment while the two halves get glued together. I'll try and get the grip shape finished tomorrow. Finally, I have made a guard-plate out of 1/16" brass. It still needs to be polished but that will wait till the assembly stage.
The hamon is visible but very faint - in person, you need to tilt the blade to the light to see it. I think it's just barely visible in the attached picture, mainly around the light-bloom from the camera flash.
-Stephanie
Attachment: 133.21 KB
Grinding complete, guard plate fabricated. [ Download ]
|
|
|
 |
Justin King
Industry Professional
|
Posted: Sat 19 Jul, 2008 7:06 am Post subject: |
|
|
Good work, Stephanie! It looks like you have some pretty ambitious projects going. There is someting very personally satisfying about having your own handiwork in your collection. A warning, though, once you know you can do this kind of project you may start eyeing every sword you come across with the idea of dimounting it and working it over yourself. I have never handled a Del Tin without thinking of taking it to the grinder, and the only swords I have that have not been "improved" are Albions. I may need more practice before I can improve much on those...
The tape is a good idea to keep from cutting yourself and bleeding all over the workshop, and also to keep a polished blade safe from incidental scratches. I use 2 or 3 layers of masking tape, it seems to leave the least amount of adhesive residue when removed.
There is a lot to learn when you do things of this nature, some of it can be told or taught but much of it is learned by trial and error. There are a number of folks here and on other forums who can and will offer tips and advice for problems or questions that you may come across so if you get stuck don't forget to ask. Best of luck with your projects, I hope to see more pictures as your work progresses.
|
|
|
 |
Anders Backlund
|
Posted: Sat 19 Jul, 2008 1:10 pm Post subject: |
|
|
Neat stuff, to be sure.
I like what you're doing with the Orcrist blade - it looks quite similar to my own project. Good luck.
The sword is an ode to the strife of mankind.
"This doesn't look easy... but I bet it is!"
-Homer Simpson.
|
|
|
 |
Jean Thibodeau

|
Posted: Sat 19 Jul, 2008 4:25 pm Post subject: |
|
|
Looking forward to seeing these projects as they progress.
You can easily give up your freedom. You have to fight hard to get it back!
|
|
|
 |
Stephanie Maks

|
Posted: Sun 20 Jul, 2008 11:24 am Post subject: |
|
|
Thanks again for the suggestions & comments!
I have 'finished' the tanto... for now at least. I'm not happy with the outcome, and that's mostly because I got impatient and rushed my way through the handle work. The only positive I have is that it turned out to be a tight-enough fit that I was able to use a wood peg (mekugi?) to hold it together. I think my biggest problem was a lack of planning. I had a number of ideas and rather than settling on something I just 'winged it' and ended up with something that doesn't please me. My biggest complaint is that the handle is 'off-centre'. It's centred on the tang rather than the blade. The knife does feel pretty good - it feels a tad blade-heavy but the centre of balance is actually just inside the handle, about 1/4" inside, giving it a very quick feel.
I think what I will do is, when I have finished grinding a point onto the wakizushi, I will try and come up with a design that uses both the tanto and the wakizushi as a pair. I think that makes good sense as they came from the same blade originally, they should be treated as a set?
For the orcrist blade, I have been doodling designs for a while. Actually I kind of like the last sword-handle I made, although it was for a rather worthless blade. The blade was a cheap soft-steel decorative Toledo piece that I've had for years. The rat-tail tang broke off long ago, but I cut the shoulders down to give me a nice long tang. The Orcrist will probably get a handle similar to this -- but a little more carefully-done, and with a nicer pommel:
Cheers!
-Stephanie
|
|
|
 |
Justin King
Industry Professional
|
Posted: Sun 20 Jul, 2008 12:31 pm Post subject: |
|
|
The tanto looks good, the thingy about the handle is one of those trial and error things I mentioned. It helps to have the tang centered on most types of blades, even if they are not symmetrical. Some blade types lend themselves to this better than others but an offset tang is something that should be accounted for in the design from the beginning. The grip material often becomes very thin near the guard end , which limits how much you can adjust for problems like this. I have learned that tang design is often critical to achieve the desired strength and still get the proportions right on some pieces.
It does help to have at least an idea of how the whole thing will come together in the end. I find more and more that drawing even a rudimentary sketch of what you have in mind can save hours of labor and lots of disappointment when something dosen't turn out as hoped. Fine tuning proportions is much easier on paper than in wood and steel. Not that you can't or won't vary from your sketch in the actual working process, but it gives you a solid starting point and allows you to address design issues before they arise in the actual workpiece.
It is very easy to get excited and rush a piece to completion but some ideas need time to ripen and for the details to form in your mind. I will sit on projects for months sometimes until a particular detail or problem clarifies itself in my head, or sometimes just to give my eyes time to absorb the proportions of a piece, and decide what needs a little more work. Especially when a project is assembled with all the parts for the first time I try to just study it for a day or two, and make any changes or adjustments gradually. Even if you spot a problem or mistake immediately, the "best" solution may be longer in coming so patience is key.
|
|
|
 |
Jean Thibodeau

|
Posted: Sun 20 Jul, 2008 12:50 pm Post subject: |
|
|
If the material of the handle is robust enough the top of the handle could be flush with the tang and this would " fix " the uncentered look of the handle: This may be a problem with wood as the bottom might not be strong enough and split along the grain.
Now this would be for an non-Japanese styled handle and one could also drill small pin holes along the tang and have a slab handle pinned and glued in place.
A micarta handle could be made with an open " U " shaped slot and have an open top showing the tang.
A new symmetrical handle might be possible by thinning the top of the handle as much as possible while still keeping it thick enough for structural integrity but then the handle might have to be extended in width to compensate: The tang being offset into the handle. Visually this might make the handle look and be too wide ?
Oh, grinding away 1/8" from the top of tang might also work at long as the tang isn't narrowed too much.
Just giving you all the options I can think of off the top of my head.
You can easily give up your freedom. You have to fight hard to get it back!
|
|
|
 |
Carlo Giuseppe Tacchini

Location: Magenta, east of Milano, northern Italy Joined: 16 Jul 2005
Posts: 2
|
Posted: Sun 20 Jul, 2008 1:23 pm Post subject: Re: Some projects I've started... feedback, comments welcome |
|
|
Stephanie Maks wrote: | I purchased an antique Katana blade about 4 or 5 years ago as a project piece - the blade was damaged (which is how I was able to afford it), but I had hopes I could fix it somehow. It had a nasty chip on the edge as well as a bend, in addition to some minor pitting. After some research and asking around, the conclusion I came to was that there was no cheap and easy way to fix it back into a straight and workable Katana. The bend and chip were both 8 or 9 inches from the tip, and one suggestion I was given was to cut it at that point, and fashion it into both a small tanto and a wakizashi. It's taken 4 or 5 years but I've finally returned to that project blade, and decided to proceed with that suggestion. |
Hope you've asked to a professional (aka "Togishi") about the value and situation of this sword.
Otherwise you could have made the most silly thing in your life.
As I see in this thread a potential danger for antiques, hereby I *deeply* suggest to not mess up with ancient NihonTo
without having showed them to professionals.
No offense meant to anybody, of course. Just a "better safe then sorry" matter.
Please forgive my english
|
|
|
 |
L.S. Lawrence
|
Posted: Sun 20 Jul, 2008 1:33 pm Post subject: |
|
|
Stephanie,
Hi. I am posting here because someone has to.
First off, I’m sure you are an excellent person, who means well.
As I say the following, I am not criticizing you personally, but someone has to call a spade a spade and state if not for you then for other readers that what has been done here to this antique Japanese sword is a grave, heartbreaking loss.
OK. It was chipped and bent, and you showed it to some people who said the cost of fixing it would be high. But chipped where? Bent how? Who did you show it to? What do they know about antique Japanese swords and their maintenance and repair. How long have they studied? Under whom? “High cost” relative to what? Your income? A Japanese museum’s acquisitions budget?
There is an excellent chance this sword could have been repaired, and lived to see another day.
Was it a great sword? A mediocre sword? A true piece of junk (yes, there are some)? We will never know. But it may shock you to learn that there were many fantastic, truly culturally significant Japanese swords picked up by allied soldiers on the beaches and battlefields of WWII, brought back to North America and left in damp basements, used as machetes, etc. etc. that today would look like complete trash to you and me.
The fact is that a blade that is rusted, bent, chipped, will be almost impossible for all but the most highly educated Americans to recognize and deal with appropriately.
The great American swordsmith Howard Clark has his Japanese-style blades polished by two men. One of whom, Keith Larman, has terrific skill. Even Keith Larman will not touch a nihonto because he freely admits he doesn’t have the knowledge or the training, and absent those things, the likelihood is he will do far more harm than good if he tries to work on one.
If Keith Larman is not qualified, none of the rest of us are. It’s as simple as that.
We –you and I and anyone who enjoys this sort of thing- should stick to Paul Chens and Kris Cutlery blades to learn on and have fun with. Never, ever, ever antiques.
A person in your position might reply, “It’s my blade. I’ll do what I want to.”
Yes. It’s your blade. You own it.
But let’s put the shoe on the other foot. How would Europeans feel if in a war with Africa the great remaining rusted and corroded Viking era blades ended up in Africa, being ground down and used for cooking spatulas? Or how would we Americans feel if in a war with New Guinea, our great early long rifles from Pennsylvania and Virginia and Kentucky ended up being used as blow guns back in the rain forest?
That is what a rusted garage-sale nihonto represents to Japanese eyes. And one that has been badly polished, put on a grinder, or worse yet cut in half, is just a sad, sad loss. A loss of history. A loss of artistic skill. A loss of something that is never coming back.
I don’t know if this will change your mind or not. But other people will pass through myArmoury and see this thread. They have to know that what happened here should never happen.
And to those forum members who have congratulated you on your project…wanting to encourage your development as a craftsperson is very different than encouraging the desecration of centuries old antiques. No matter how well intentioned.
They should be saying –as kindly as possible- “Do not repeat this.” “Here’s why…”
Barring Carlo (who was posting while I was writing) they haven’t, so I have gone ahead. I hope I have been polite enough, while still communicating what needs to be communicated.
Once again, I wish you well. Take care.
|
|
|
 |
Jean Thibodeau

|
Posted: Sun 20 Jul, 2008 1:51 pm Post subject: |
|
|
L.S. Lawrence wrote: | Stephanie,
And to those forum members who have congratulated you on your project…wanting to encourage your development as a craftsperson is very different than encouraging the desecration of centuries old antiques. No matter how well intentioned.
They should be saying –as kindly as possible- “Do not repeat this.” “Here’s why…”
Barring Carlo (who was posting while I was writing) they haven’t, so I have gone ahead. I hope I have been polite enough, while still communicating what needs to be communicated.
Once again, I wish you well. Take care. |
Very good points and I will admit that I was focussed more on the " positive " DIY aspect than the " negative " possibly destroying something valuable ! ( And I don't mean just $$$$ ).
Glad that this aspect was mentioned for the sake of other old swords out there that shouldn't be used for DIY without being very sure what they are !
On the other hand: It's too late now for this sword, and it's just crying over spilt milk or trying to unscramble eggs ! So although it might be useful to continue discussing this, it might be better starting a new Topic about being very careful when dealing with what seems like an already ruined sword that might still be worth restoring or at least not making worse !
Sometimes it's just not knowing any better or assuming that something is already beyond salvage !
Oh, and I think the subject was brought up in a polite and respectful way.
You can easily give up your freedom. You have to fight hard to get it back!
|
|
|
 |
Stephanie Maks

|
Posted: Sun 20 Jul, 2008 2:49 pm Post subject: |
|
|
L.S., Carlo, you bring up very good points. I did consult a smith who has a lot of experience both in making blades and in antique weapons and techniques. He has worked with museums, and although his expertise is not specific to nihontos, I do trust his judgement. The two options I was looking at were either do nothing with it and keep it stored away somewhere as a damaged blade that I could not do much with, or to proceed as I have done and try and make something of it. I suppose a third option would have been to try and sell it on to someone with more knowledge or in a position to invest more in exploring the restorative options, but that's not why I bought it.
I only spent about $100 on the blade, and it was not prepared to invest further in it to have it appraised, much less fixed. Cutting it was not something I did lightly -- it did take me 3 or 4 years to act on the advise, after all. Maybe some ancient Japanese smith has turned over in his grave. On the other hand, perhaps he'd be happy that his work, albeit not in its original form, is once again going to be seen and appreciated.
As Jean has suggested, maybe this discussion deserves its own thread. I agree, the subject was brought up quite politely.
Re. the handle work, there is enough wood along the top that I could bring it down about 1/8" or so. Actually the idea of a U shaped grip did occur to me, but not soon enough - if I'd thought of that earlier, I wouldn't have done any grinding on the back of the tang at all; I think it would have looked very smart. I really should have known better, about rushing. I've been doing knife / sword handles on and off for several years... but just getting back into cutlering again after a 3 year break, so I was eager to finish something.
-Stephanie
|
|
|
 |
Gabriel Lebec
myArmoury Team


|
Posted: Thu 24 Jul, 2008 7:01 pm Post subject: |
|
|
This thread was just recently brought to my attention.
To any new enthusiasts, I would caution that doing anything to an antique is usually inadvisable. That even includes "cleaning" (which can irrevocably ruin nihonto – Japanese blades – if not done by trained professionals). Dr. Stein's Japanese Sword Index has two articles on proper sword care.
On the other hand, it is not unheard of for some nihonto to be considered near-worthless due to extensive damage or other reasons, and to be used (by knowledgeable people) to train apprentices in togi – Japanese sword polishing. The expectation is that the student will likely make errors on the blade. Of course, the benefit is that the professionalism of licensed togishi is maintained at a very high level, resulting in better preservation for the other 99.9% of antiques; i.e., the "junk" blade is not sacrificed to just an arbitrary end, but to a directly related cause. Usagiya actually has a dedication section for such blades. (Modern example).
Nihonto (like many highly specialized fields, both arms & armour related and otherwise) is associated with a substantial academic discipline. Therefore, even an excellent smith with experience in general antiques may not be considered by many to be authoritative in gauging if a Japanese blade is unsalvageable. As has been noted, that is kind of moot at this point, and I can easily imagine cases where a blade's prospects are unmistakably nil. But it is something to consider for the future.
Also, one man's "junk" is often another's treasure. Items from a specific era, even junk, only become rarer with time. But people will disagree on precisely where the divide is between the preservation of art and history, and the freedom to experiment and learn. That is poorly phrased (the two are not mutually exclusive!) - my point is simply that stagnation can be harmful as well.
The details of this specific case have already been discussed – fairly and cordially, I am happy to note – and I will not address most of them directly. However, Stephanie, I do wish to point one functional concern with your pseudo-wakizashi, as the hamon will run off of the tip without a proper boshi. Normally this is considered a fatal flaw in a Japanese sword. Not that such a blade is necessarily more likely to break; I just figured I might as well mention it.
Thank you to all involved parties for the tenor (and substance) of this discussion to date.
Regards,
-GLL
"The most beautiful experience we can have is the mysterious. It is the fundamental emotion that stands at the cradle of true art and true science." - Albert Einstein
________
|
|
|
 |
Jeff Ellis
|
Posted: Thu 24 Jul, 2008 9:53 pm Post subject: |
|
|
Stephanie,
Would it be possible for you to get a few clear pictures of the tang (nakago) of the longer part of the sword? There should be some nice brown rust and a signature (mei), unless it was a mumei (unsigned) blade. Get any markings on the nakago into the pictures as well if you could.
It is too late to say "Don't do this!" but I want to point out a few things...
The edge of the sword you have was and is harder than the body of the blade, this means that the edge that rolls up to the spine at the tip is hardened. The tip of your wakizashi sized blade is no longer hardened like this and is going to be very soft.
At this point, the best way to fix this issue with the wakizashi blade (as both pieces are now worthless) is to cut the tip at an angle such that it would look like a seax tip, as this will keep a good hardened area there, while "pulling" the soft steel away from the tip. (see picture)
The hard portion of the blade is called the "hamon," literally "edge pattern."
You may not be able to see it on this old blade, but it is there if it is a true Japanese sword.
Be very careful to not turn any portion of the blade blue in grinding, in fact, you will want to take a nice big bucket of cold water and dip that blade in it after every two to five seconds of grinding. If the hamon gets too hot, it will start to anneal and no longer be hard. Dip often, and when the water gets warm, get new water. Better yet, use a hacksaw and cut it.
It's been said by the other guys, but i want to repeat it...
To anyone on this forum; please do not ever take an antique Japanese sword and do this unless you are absolutely 100% sure that it is 100% worthless.
It is akin to taking one of those nice migration era blades that may have survived and turning it into a floor scraper or taking a highly decorated breastplate and hammering it out into a door decoration.
Attachment: 7.74 KB
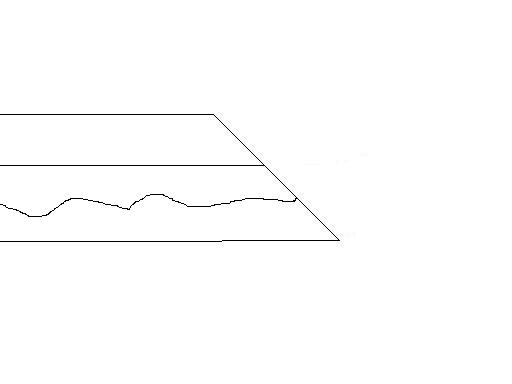
"i like swords"
|
|
|
 |
Stephanie Maks

|
Posted: Thu 24 Jul, 2008 11:32 pm Post subject: |
|
|
Well, I had no idea people would be so shocked, upset, dismayed, etc. about the old katana blade. I'm sorry I've got folks upset, but I stand by my 'project' decision - whether it was fixable/repairable/salvagable, the two key points were, I bought it specifically as a project piece, and it was not fixable by me nor could I afford to have it fixed by a professional. I know the hamon is not going to follow the new point, I know the new point will not be hardened, and considering these are my first projects involving working on the steel, I know that odds are it's not going to turn out so great regardless.
I'll get some pictures of the nakago when I get the chance. There is no mei, but it does have a layer of brown rust / patination.
I've been working this past week with the Del Tin blade rather than the nihonto; cutting new shoulders to shorten the blade and lengthen the tang was fairly easy with a dremel and heavy-duty cutting disc. The hard part was putting some holes in the tang for the rivets I want to use. (Rivets might not be historically accurate... but they give me a nice feeling of security, that the handle's not going to come off!) 3/16" holes, through 1/4" of hardened steel... I have managed to do it, and without wrecking it - slow going, with damp cloths wrapped around to keep the temperature down, using cobalt-steel bits (I did manage to kill 2 bits). I have a bit more grinding to get the tang shape smoothed out from the dremel cuts, and then the steelwork will be finished and I can focus on the design and construction of the hilt.
Will get pics of the Del Tin tang as well as the nihonto, over the weekend.
-Stephanie
|
|
|
 |
Anders Backlund
|
Posted: Fri 25 Jul, 2008 6:08 am Post subject: |
|
|
To those who thougth cutting the katana in half was a poor decition; you all make some very good points.
Still, think of it like this: in just a mere 100 years or so, Stephanie's tanto and wakisashi will be antiques again.
The sword is an ode to the strife of mankind.
"This doesn't look easy... but I bet it is!"
-Homer Simpson.
|
|
|
 |
|
You cannot post new topics in this forum You cannot reply to topics in this forum You cannot edit your posts in this forum You cannot delete your posts in this forum You cannot vote in polls in this forum You cannot attach files in this forum You can download files in this forum
|
All contents © Copyright 2003-2025 myArmoury.com All rights reserved
Discussion forums powered by phpBB © The phpBB Group
Switch to the Basic Low-bandwidth Version of the forum
|