Author |
Message |
Joe Fults
|
Posted: Mon 30 May, 2005 9:16 pm Post subject: Discussion: Sword Maker Quality Control Practices |
|
|
I am starting this thread to see if anybody else is interested in how different vendors handle quality control.
Some vendors seem to enjoy consistent reputations for quality. Others seem to have reputations for ongoing quality control issues. However, these should be easy to fix since QC is a process issue. The issues that cause QC problems may be more difficult to solve though. That said I know from experience in other industries, that sometimes quality control, and effectively quality, goes out the door for the mother of all business necessity, cash flow. So at some point continued quality control problems just reflect conscious acceptance of poor quality on the part of the vendor.
So how do sword makers generally approach quality control? Does anybody have a formal QC process or it all by instinct/experience? Does anybody have a general process? If so, what gets checked? Are there any generally accepted best practices for quality in this industry? Who follows them? Are there industry benchmarks? Who sets them?
I'm in a service industry, which is a very different beast, but we send an electronic satisfaction survey out with each transaction we process as part of our QC. In theory we QC 100% of the work we do and we have meaningful performance criteria we can benchmark against.
My wife works for an auto maker. She has assembly and QC tasks she is expected to perform on every vehicle (of prior work). In turn somebody down-line is supposed to check her work based on a documented set of criteria.
Thank in advance to any who chose to participate.
"The goal shouldn’t be to avoid being evil; it should be to actively do good." - Danah Boyd
|
|
|
 |
Glen A Cleeton

|
Posted: Tue 31 May, 2005 1:37 am Post subject: |
|
|
My concern is that if a manufacturer is advertising a good as functional, then a reasonable level of expectation should be met.
If a company is pumping out product to meet demand and is being driven by profit, quality/durability may be taking a back seat. Volume can create problems.
When reports surface of several swords failing, in our small sector of the market, it should be a wake up call to a business that continues to diversify. One, in particular comes to mind. I know they listen, so I wish Paul the best. He has listened to my case.
Another company clearly states that they don't warranty most of their swords to act as a sword should. They continue to be popular with reenactors and are introducing a functional line. They appear to have always erred on the side of caution.
Every American maker I know will back up their product to perform within reasonable parameters. Most will go out of their way to make things right.
We, as the consumers, have to accept what the realistic expectations are.
Cheers
GC
|
|
|
 |
Craig Johnson
Industry Professional

|
Posted: Tue 31 May, 2005 7:24 am Post subject: Quality |
|
|
Hey Joe
Good questions. We just had a discussion about this last week as several of us in the shop had recently dealt with defective products in our homes, TV, disposal, that kind of stuff and we were amazed at the poor response from the makers. One was the old "Oh your warranty expired two months ago." If you buy electronics in this day and age its almost to the point where you have to buy the extended service plan if you ever want to get help with the thing. If we acted this way with our customers we would get creamed.
In the shop its not very scientific for us the basic rule is if you would not pull the money from your own pocket to buy the product its not good enough to send out the door. I think the difficulties in the handmade objects we deal with add an xfactor into the process for sword makers as not everything is slide together and move it down the line. It often takes some tweaking to get it all just right and we often will pull something apart and redo it to make it right.
The amount of energy that goes into this is one of the biggest draws on domestic makers bottom lines. If you want to have the expectations of the customers satisfied then you need to do it but at the same time the price pressure from over seas is down down down. It gets to be a balancing act with some pieces as they are just not profitable to make in that enviroment. The expectations that customers have of the domestic producers is very high and it creates challenges for us to meet and exceed their anticipation. In a way I guess we have to combine service and production. In our shop the goal is to make great stuff but also to produce an experience for the customer that makes them feel they got more than they paid for when they open the box. In a real way our job is to make them happy at the end of the process more than anything else.
Sorry rambled there a bit
Best
Craig
|
|
|
 |
Aaron Schnatterly
|
Posted: Tue 31 May, 2005 8:03 am Post subject: Re: Quality |
|
|
Craig Johnson wrote: | Sorry rambled there a bit |
Actually, Craig, you didn't. I read your post... twice. It's great for me to know how you and your crew view your business.
Your customer base is a special bunch. Typically, I would think, it's either the person looking for that special piece or two, or it's a serious collector (and by "serious" I mean in number, breadth, and depth of collection - I think we're all serious about our interests). Either way, we really both appreciate and depend upon quality and craftsmanship.
You mentioned being between hammer and anvil by mass producers and lower-quality or lower-priced overseas stuff. I know this is the case - seen a person tell a true craftsman they were insane for asking what I thought to be a rock-bottom price on a beautiful piece, because "so and so website has one like it for $xx.xx!" and then went on to tell him he must not know what he is doing, or that he thinks "we the customer" are idiots. You know what? That's ok. Speaking for myself, I appreciate the high degree of skill and craftsmanship that goes into pieces that enter my collection. For that, I accept (gladly) that I will pay for it. I have, and I will again. And again.
Keep after it as you have been... I'll be knocking on your door soon. You have a couple of things I think I just might need.
-Aaron Schnatterly
_______________
Fortior Qui Se Vincit
(He is stronger who conquers himself.)
|
|
|
 |
Joe Fults
|
Posted: Tue 31 May, 2005 8:26 am Post subject: |
|
|
Craig,
A valid criteria but it seems somewhat subjective.
It seems clear to me that many of the overseas makers do not deliver the quality of the US makers. Many appear to compete almost purely on price. To a certain segment of the market, that is all that will ever matter. However, to others quality will matter. Right now I'm not sure consumers have clear quality expectations.
Would objective and measurable quality expectations might help consumers make decisions on more than just price?
"The goal shouldn’t be to avoid being evil; it should be to actively do good." - Danah Boyd
|
|
|
 |
Lancelot Chan
Industry Professional

|
Posted: Tue 31 May, 2005 8:27 am Post subject: |
|
|
I want to commend about A&A shipping package improvement along the time. When my friend Ben first got his GBS in gun case, the sword knocked against the rim of the box and dented the tip a lil' bit. Then years later I recommended another friend of mine to buy a GBS from A&A without special mention other than "shipped in gun case". A&A crews improved the packing so much that the tip of the sword never got to touch anything but foam. Here're some photos. Craig and guys at A&A have my high recommendation:
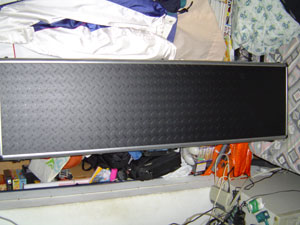 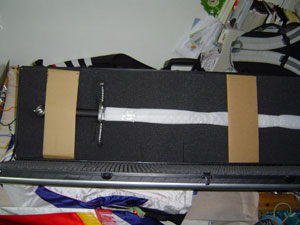
Ancient Combat Association —http://www.acahk.org
Realistic Sparring Weapons — http://www.rsw.com.hk
Nightstalkers — http://www.nightstalkers.com.hk
|
|
|
 |
Angus Trim
|
Posted: Tue 31 May, 2005 9:33 am Post subject: Re: Discussion: Sword Maker Quality Control Practices |
|
|
Joe Fults wrote: | I am starting this thread to see if anybody else is interested in how different vendors handle quality control.
Some vendors seem to enjoy consistent reputations for quality. Others seem to have reputations for ongoing quality control issues. However, these should be easy to fix since QC is a process issue. The issues that cause QC problems may be more difficult to solve though. That said I know from experience in other industries, that sometimes quality control, and effectively quality, goes out the door for the mother of all business necessity, cash flow. So at some point continued quality control problems just reflect conscious acceptance of poor quality on the part of the vendor.
So how do sword makers generally approach quality control? Does anybody have a formal QC process or it all by instinct/experience? Does anybody have a general process? If so, what gets checked? Are there any generally accepted best practices for quality in this industry? Who follows them? Are there industry benchmarks? Who sets them?
I'm in a service industry, which is a very different beast, but we send an electronic satisfaction survey out with each transaction we process as part of our QC. In theory we QC 100% of the work we do and we have meaningful performance criteria we can benchmark against.
My wife works for an auto maker. She has assembly and QC tasks she is expected to perform on every vehicle (of prior work). In turn somebody down-line is supposed to check her work based on a documented set of criteria.
Thank in advance to any who chose to participate. |
Hi Joe
We have two things here to consider. Expectations, and quality control. Two different things......I'm sure you remember a couple of celebrated events from a couple of years ago, involving swords and helmets on poles. In both instances, the swords were very good swords, there was just something wrong with the expectations....... expecting a quality, very sharp sword's edge to hold up to a steel helmet on the one case, and on the other, lightweight real swords to hold up like much heavier crowbars..........
There's nothing a swordmaker or swordmaking firm can do about a potential customer's expectations, except education of the public, and honesty about one's products.......
Speaking just for myself, and what I check..........
I check hardness, I want a fairly uniform hardness from the base of the blade to the tip, numerically speaking. I don't want it to vary more than 3rc..... 52 at the base, say, 55 at the tip or edge........
I guarantee hardness to be between 51 and 53rc, so that has to be checked......
I check the edges...... my swords, on a percentage of swords shipped, are used more often for cutting than any other maker's............
I check blade flex......the more flexible blades I check by holding by the handle next to the cross, and pull the blade by the tip 40 to 45 degrees......... {the stiffer blades can't be pulled that far, so they don't get pulled as far}......
I check assembly.........
I check visually for an aesthetic flaw or oxidation....... {if I miss something though, its something here that I miss}......
If I have a special request, or a customer with special needs, I will check one more time. I recently made an AT1562 for shipment to Hong Kong knowing it was going to be used a lot cutting pork shoulders, so I made the edge just a bit thicker than normal to reduce wear.........
swords are fun
|
|
|
 |
Joe Fults
|
Posted: Tue 31 May, 2005 10:55 am Post subject: |
|
|
Angus,
Thanks for that post.
It is very informative (to me) from the process perspective since it expalins in just enough detial, what your QC process is and why you check what you check. I understand the part about expectations too. Sometimes having known and measurable QC standards helps manage expectations. At least in my radically different field.
Do your quality practices represent a norm for the industry in any way, or is it something you brought to your operation from your pre-sword fabricator days?
Basically, I'm trying to get a feeling for is what is common (best) quality practice in this industry because I think it could help manage expectations (at least mine).
Are there things people generally check on each piece before it goes out the door?
Do most makers use a less defined criteria like Craig outlined?
Are there any generally agreed upon best practices?
Regards,
"The goal shouldn’t be to avoid being evil; it should be to actively do good." - Danah Boyd
|
|
|
 |
Thomas McDonald
myArmoury Alumni


|
Posted: Tue 31 May, 2005 12:53 pm Post subject: |
|
|
A few random pages pulled from -
'British Military Swords; From 1800 To The Present Day' by John Wilkinson Latham (1966).
Mac
Attachment: 63.29 KB
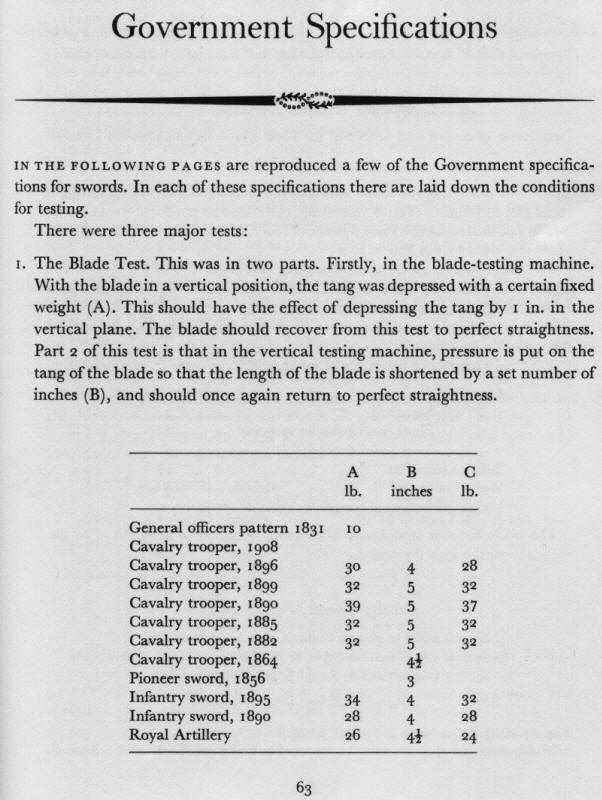
'Gott Bewahr Die Oprechte Schotten'
XX ANDRIA XX FARARA XX
Mac's PictureTrail
|
|
|
 |
Lance K.
|
Posted: Tue 31 May, 2005 1:42 pm Post subject: |
|
|
Whatever you do don't buy a "practice" sword from this guy.
http://www.killsometime.com/Video/video.asp?v...ork-Katana
I actually saw this happen on live tv, It was hilarious. I was just flippin through channels and magically stumbled upon this as it happened. It was great. I laughed so hard.
Lance
|
|
|
 |
Craig Johnson
Industry Professional

|
Posted: Tue 31 May, 2005 6:37 pm Post subject: QC List |
|
|
I see what you mean Joe as far as specifics and subjective. I guess I personally have a tendency to be tougher on the items than just the specs. Its got to look right and feel right. It can often be something very minor as far as what I don't like but it bugs me so I fix it.
As a process I will check all the specs as the piece is in progress and take notes on issues if it is a piece we have not been producing for a good length of time. The blade is checked a couple of times for different details as it is taken from the stock to a finished blade. The parts and such are usually gone over by more than one person to check for flaws. As far as fine adjustments these I try to stay consistent to the original if known or the design goal and variations are usually done only at customer request.
Finally once all the elements are together and fit, the whole shebang is gone over and tweaked to satisfaction. This is were one will find the odd little things that can be difficult to adjust but are the things that can really matter when someone opens the box.
I guess if the system was codified it would be described as integrated into the construction process. If something is found to be wanting its fixed at that point and not later in the flow.
I guess the quantifying of things for customers to refer to is possible but I would not want to work to just that spec. To me getting the integrated whole as close as our hand and eye can do with the talents and skill we have is a big part of what makes us Arms & Armor. Hope that does not sound to atmospheric.
Not sure if that clarifies or muddies the issue.
Best
Craig
|
|
|
 |
Angus Trim
|
Posted: Tue 31 May, 2005 7:05 pm Post subject: |
|
|
Joe Fults wrote: | Angus,
Thanks for that post.
It is very informative (to me) from the process perspective since it expalins in just enough detial, what your QC process is and why you check what you check. I understand the part about expectations too. Sometimes having known and measurable QC standards helps manage expectations. At least in my radically different field.
Do your quality practices represent a norm for the industry in any way, or is it something you brought to your operation from your pre-sword fabricator days?
Basically, I'm trying to get a feeling for is what is common (best) quality practice in this industry because I think it could help manage expectations (at least mine).
Are there things people generally check on each piece before it goes out the door?
Do most makers use a less defined criteria like Craig outlined?
Are there any generally agreed upon best practices?
Regards, |
Hi Joe
Jamie and I just shut down everything but the one mill, machining a couple blades.....and before getting ready to go fencing and checkin' the gals out, we did a little "qc" work..... ie making sure that the new bastard sabers would cut better than the katanas that have left here.....*g*
Handling issues too.......
what do I check.........
It depends on the sword and sword type to some degree...........
And some blades get scrapped. Just two weeks ago, a 1433 blade was scrapped due to a problem with one shoulder..... hated to do it because it was already late, but that blade's not going to "get out there"......
Like Craig, I check things like handling..... sometimes something just doesn't feel right, though frankly, 99% of what I put together is very, very consistent, one blade of the same model to another blade, one pommel of the same model to another, etc......
Its my background, aircraft machining. I can dig one of a kind swords, but with a "model", in my view one should be as consistent as possible, so a customer can depend on what they're going to get.......
I like to use the same material all the time for guards and pommels too. I used to experiment, I've used 1018, 4130, 4340, and 303 for pommel material. I finally settled on 1143, because it finishes easier and better, is consistent stuff to work with, and as delivered is approx 30rc. I use 1018 for the guards, because sometimes the guards need to be tweaked a bit into shape, or welded onto for compound hilts, and the 1018 I get is very consistent.......
The same with the 5160 I use. Pretty consistent stuff........though not perfect. A year and a half ago, I made a splash on the manufacturers forum, mentioning that the 5160 I used never had any material issues with it. Since then, I've had two blades have some carbon banding show up as I was finish grinding them...... both blades had to be junked.......
Even with the machining and consistency, there still is a lot of handwork and hand finishing. So consequently, things like handle fit can be unique to a sword at times, as organic materials don't always cooperate........
Then I try and improve the process, and the qc as time goes on. If you were to look at the average sword that leaves here now, and an average sword that left here three/ four years ago, you'd probably notice one heck of a difference......
swords are fun
|
|
|
 |
Angus Trim
|
Posted: Tue 31 May, 2005 8:21 pm Post subject: |
|
|
Joe Fults wrote: | Angus,
Thanks for that post.
It is very informative (to me) from the process perspective since it expalins in just enough detial, what your QC process is and why you check what you check. I understand the part about expectations too. Sometimes having known and measurable QC standards helps manage expectations. At least in my radically different field.
Do your quality practices represent a norm for the industry in any way, or is it something you brought to your operation from your pre-sword fabricator days?
Basically, I'm trying to get a feeling for is what is common (best) quality practice in this industry because I think it could help manage expectations (at least mine).
Are there things people generally check on each piece before it goes out the door?
Do most makers use a less defined criteria like Craig outlined?
Are there any generally agreed upon best practices?
Regards, |
Hi Joe
I think I got a little wordy, and didn't actually answer what you asked.....
My aircraft background probably has more to do with how I see things, production or qc, than it being a norm for the industry. I don't think there is a norm for the industry.......
Yes.........
I really don't know how most makers do things, there's ussually more important things to discuss when we get together, things like the gals, good beer, where we're going for dinner and beer, etc.......
It would be nice if there were some agreed upon practices, but communication between makers is limited......
*g*
swords are fun
|
|
|
 |
Michael Pearce
Industry Professional
Location: Seattle, Wa. Joined: 21 Feb 2004
Posts: 365
|
Posted: Tue 31 May, 2005 10:56 pm Post subject: |
|
|
Being a 'custom' rather than 'production' maker I tend to work on one sword at a time from start to finish until it's done. I would have thought that this might lead to differences in the way we QC things, but apparently not... My process (if I can call it that) includes a lot of the same things as Gus's and A&A's. I am continually looking at and adjusting things as I go along like Craig- and I test like Gus throughout the process. I generally then spend some 'quality time' with the finished peice, playing with it and examining it closely. I was doing this last night with a piece that was finished and noticed that one of the features was off by about .04-.05 inches- nothing for it- had to go right back into the shop to fix it. My wife teases me about 'fondling' my blades, but sometimes it allows me to catch minor things and fix them before the piece goes out the door.
I get certicication on heat treat for each batch of blades- Gus and I use the same heat treat facility and they are quite good.
Specific tests- once a blade is ground out and the differential tempering is completed I flex test the blade. Some blades are too stiff to flex a full 45 degrees, so I just do what I can. Blades that are only normally rigid get flexed to 45-90 degrees depending on the swords type. Then I whack the un-sharpened edge into a nice solid piece of wood several times on different parts of the blade- I've found that if any tiny fractures have occured in heat treat this shows them up pretty quickly! This is a very infrequent occurence, but it only has to happen once in a customer's hand for a serious injury to occur... Between the flex and the bashing around they don't get out of the shop with microfractures.
Once it's all together I smack things with it again to make sure it all stays tight and check the harmonics- I used to check this more as I went along but experience seems to have rendered this unecessary... I also 'ring' the blade. Not really a test- I just like to hear it., and it does tell you if anything is at all loose.
Finally, after the sword has a scabbard, I sharpen and test the cutting edges (if the sword is a 'sharp') I typically test the edge by holding a scrap of 7-8 oz. leather in my left hand and slicing (not slashing) ...it with the sword- it has to shear cleanly and evenly along all cutting edgees
I use the same sort of 5160 as Gus from the same source (not surprising if you think about it...) For fittings I use 1018 for guards and pommels- lately I have been using a 'free-machining' steel for some pommels- I think it's the same one that Gus uses... we have a lot of the same suppliers, being from the same town. Not to mention having dinner at least once a week and comparing notes...
Another aspect of QC- sort of- is that Gus and I both work with martial artists who use our swords to fine tune them on handling issues, so that a given type of sword, as nearly as we can determine, has appropriate handling and dynamic characteristics for the arts they were used with. I imagine that other makers do this too, but it hadn't been mentioned yet.
That's all I can think of at the moment- it's getting late...
Michael 'Tinker' Pearce
-------------
Then one night, as my car was going backwards through a cornfield at 90mph, I had an epiphany...
|
|
|
 |
George Hill
Location: Atlanta Ga Joined: 16 May 2005
Posts: 614
|
Posted: Tue 31 May, 2005 11:26 pm Post subject: |
|
|
Tinker, Where can I get a good look at your swords? I've been to blade art, but it seems to be very limited in way of pictures.
To abandon your shield is the basest of crimes. - --Tacitus on Germania
|
|
|
 |
Nathan Robinson
myArmoury Admin


|
|
|
 |
Gordon Clark

|
Posted: Wed 01 Jun, 2005 5:59 am Post subject: |
|
|
Michael 'Tinker' Pearce wrote: | Being a 'custom' rather than 'production' maker I tend to work on one sword at a time from start to finish until it's done. I would have thought that this might lead to differences in the way we QC things, but apparently not... |
That is an interesting point - sounds like the "production" guys, at least these 2 examples, really still have more of a "custom" philosophy. The "holistic" approach to quality control sounds appealing in some ways but I wonder about the process involved - is it completely repeatable? By different individuals? Do results vary depending on who is doing the testing?
In software development (and other industries) there is a system called the Capability Maturity Model that describes how "mature" and maybe standardized your organization is. Level 1 (the lowest) is characterized by success depending on heroic effort on the part of individuals. I wonder if production sword makers in the US share much with custom makers because they are still relatively small and may not have seen the need to develop a set of documented "practices" that they always conform to for every product they produce - rather they may rely on individuals following an approach that combines "art" and "science".
I'm not saying this is bad - but it does suggest that there may be little difference between what we call "production" makers and "custom" ones in ways that are critical to discussions of process and quality control. For instance - what would happened if key personnel at A&A or Albon were out for a few months at their respective companies? Would the production level fall dramatically, would quality drop, ... or would the products look pretty much the same? If the products would not suffer, then it indicates that there is process in place and established, and enough redundancy and training to provide an organization that is more than a collection of individuals putting in heroic efforts...
Some rambling thoughts here - take them for what they are worth :-)
Gordon
|
|
|
 |
Angus Trim
|
Posted: Wed 01 Jun, 2005 7:15 pm Post subject: |
|
|
Gordon Clark wrote: | Michael 'Tinker' Pearce wrote: | Being a 'custom' rather than 'production' maker I tend to work on one sword at a time from start to finish until it's done. I would have thought that this might lead to differences in the way we QC things, but apparently not... |
That is an interesting point - sounds like the "production" guys, at least these 2 examples, really still have more of a "custom" philosophy. The "holistic" approach to quality control sounds appealing in some ways but I wonder about the process involved - is it completely repeatable? By different individuals? Do results vary depending on who is doing the testing?
In software development (and other industries) there is a system called the Capability Maturity Model that describes how "mature" and maybe standardized your organization is. Level 1 (the lowest) is characterized by success depending on heroic effort on the part of individuals. I wonder if production sword makers in the US share much with custom makers because they are still relatively small and may not have seen the need to develop a set of documented "practices" that they always conform to for every product they produce - rather they may rely on individuals following an approach that combines "art" and "science".
I'm not saying this is bad - but it does suggest that there may be little difference between what we call "production" makers and "custom" ones in ways that are critical to discussions of process and quality control. For instance - what would happened if key personnel at A&A or Albon were out for a few months at their respective companies? Would the production level fall dramatically, would quality drop, ... or would the products look pretty much the same? If the products would not suffer, then it indicates that there is process in place and established, and enough redundancy and training to provide an organization that is more than a collection of individuals putting in heroic efforts...
Some rambling thoughts here - take them for what they are worth :-)
Gordon |
HI Gordon
You ask some thought provoking things. My thoughts on this is that somethings can be expected to conform nearly exactly, up until you shove the part against either the slack belt, or the contact wheel. At that point, the human element becomes more involved, and things get tougher to quantify exactly.....
The same with the leather and wood we use. This stuff makes things more interesting, a slot in the handle can be machined, fit to a tang. Wrap cord, then leather, and damn, now the handle doesn't fit..... something has to be adjusted....
Those of us in the US, the custom makers, the small fabricator, the larger firms like A&A and Albion, aren't really production outfits. Yeah, even the ATrims, the A&A's, the Albion's aren't true production outfits, but more semi-custom/ semi-production. ISO kinda quality control won't work here.......
Some stuff can be done real well. Quality of the steel, the heat treat, the final balance can be held real close. But other things, just are going to have some leeway in them.......
swords are fun
|
|
|
 |
Joe Fults
|
Posted: Wed 01 Jun, 2005 8:56 pm Post subject: |
|
|
This may be an important thing many of us miss. We get caught up in classifying vendors as custom or production for ease of discussion and perhaps lose some perspective on what really is going on. Maybe because the experience and craftsman factors are pretty hard to quantify in terms most of use really understand.
Interestingly I always had the feeling that A&A, Tinker, and to a degree Atrim were less assembly line oriented. However, I had the impression that Albion was essentially running an assembly line process with multiple specialists involved. From 50,000 feet this would seem to lend itself to a production process with a ISO-ish QC. Now I think I'm hearing that is not really the case for them either.
Are any of the players like Windlass and Hanwei more truly production shops?
If they are, maybe we should stop calling the American vendors production or semi-production shops. Not sure what else we would call them in conversation, but I wonder if it may be blurring some key differences to the uninitiated.
Could this differentiation be played up more to the favor of some of our favorites?
For example, when I did some browsing on the A&A site, I see that they collectively have over 100 years experience in the shop. Its there on the news and updates page, and on another page it gives quite a bit of background information on what A&A is, how it does things, and why. But its not linked on the main page (that I could see) and its really not marketed very much. This could be a very important part of the marketing message or an entire statement on quality by itself. Its really great content, but I've overlooked it before because it does not stand out. When I rally started reading, I even found a section saying "We will not ship it if we would not be proud to own it". So A&A does have a published quality policy, just not a published process and you have to dig a bit to find it. Another little note on the same page talks about working directly from originals instead of just from books, and how it impacts quality.
Could this be a differentiator for the US folks?
IMO from reading and thought, A&A may be a little short-changed when we refer to them as a production shop.
Edit to add: Sorry if I'm straying from topic here. Not really sure.
"The goal shouldn’t be to avoid being evil; it should be to actively do good." - Danah Boyd
|
|
|
 |
Craig Johnson
Industry Professional

|
Posted: Thu 02 Jun, 2005 3:59 pm Post subject: QC |
|
|
I would have to say we are definitely in the heroic effort category. Though some days it feels more like the French Foreign Legion kind of heroic than the Henry the Vth type
In our process I would say the largest group of items that move through our assembly process on average is about 3 or 4. It just seems to give us the best result. Often individual swords are done start to finish due to scheduling and sometimes they are just bastards to get together right. We have a sneaky suspicion that they do have personalities.
Interesting points on the maturity level of companies. It is one of those things that one does not spend much time considering on a daily basis but it is crucial to long term success. Though I often think success in the sword business is equivalent to survival.
Yes Joe I should have that linked from the front page. Need to spiff the website a bit.
Best
Craig
|
|
|
 |
|
You cannot post new topics in this forum You cannot reply to topics in this forum You cannot edit your posts in this forum You cannot delete your posts in this forum You cannot vote in polls in this forum You cannot attach files in this forum You can download files in this forum
|
All contents © Copyright 2003-2025 myArmoury.com All rights reserved
Discussion forums powered by phpBB © The phpBB Group
Switch to the Basic Low-bandwidth Version of the forum
|