Author |
Message |
Luka Borscak

|
Posted: Fri 30 Nov, 2012 8:43 am Post subject: Adding distal taper to Hanwei Saxon? |
|
|
Hi people. Some of you may already be familiar with my customized Hanwei Saxon (it doesn't really look Saxon any more. ). The ting is, it doesn't feel natural to me that such a short, viking age sword is so thick and almost "katana stiff" so I thought I might give it to someone to add it some distal taper to get some flexibility and lose some weight. Should I be afraid of weakening it? Hanwei heat treatment is usually good enough but since there are welds involved here, I wonder if they made it overbuilt on purpose if they didn't have much faith in their heat treatment of a pattern welded blade?
|
|
|
 |
Glen A Cleeton

|
Posted: Fri 30 Nov, 2012 9:50 am Post subject: |
|
|
You need to get in there with a pair of calipers (not vernier type) and determine the thickness of the blade at the depth of the fullers. You could probably get away with some grinding on the bevels without a real issue re the structure but it may become pretty fragile in a blow.
No doubt Hanwei has come some way since my badly heattreated Godfred blade but they probably did take thickness into consideration for your blade type. As I did later put a replacement blade in the fittings, I can say that the Godfred was a nice feeling blade even without fittings and if your sword feels like a dog now, it probably felt less than wonderful to begin with. I suspect the blades on the newer Hanwei patternwelded swords are overbuilt, just to save some from being overused.
Consider the blade thickness in this shot.
Cheers
GC
Attachment: 23.94 KB
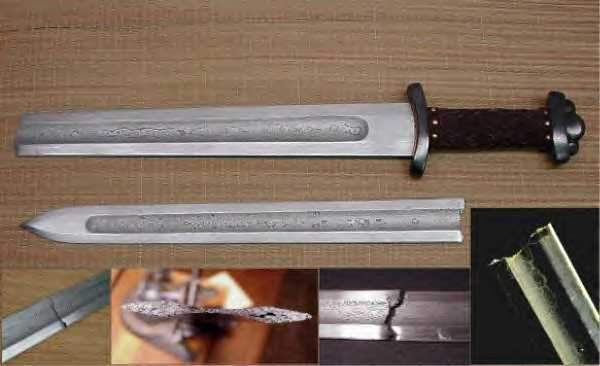
|
|
|
 |
Jack Savante

|
Posted: Fri 30 Nov, 2012 10:54 am Post subject: |
|
|
I've put distal taper into swords carefully by running the last 2/3 of the blade on the 'table' part of a belt grinder / sander. This takes time, but the beauty is it removes material slowly enough that you won't end up with a floppy sword. Another advantage is that it keeps the grain straight, meaning polishing and sanding back to the final grit is not as difficult.
You want the tip to be thinnest, and the remainder of the sword to get progressively thicker. Don't over thin the tip as it needs to be fairly rigid to ensure excellent cutting and thrusting performance. You'd be amazed how much it will improve the handling of the sword, even if you remove only the smallest amount of material (ie. you do this very conservatively). I'd advise you to take it slow. It's better to have a sword that is too stiff than too thin, and once it is too thin there is no going back. Ignore the fuller (it is much more diffcult to polish the fuller) and just work on the flat of the sword. If you proceed with caution, and do each side for an equal amount of time, you will be pleased with the results. If the sword is lenticular or beveled either side of the fuller ensure you run the sword across the belt grinder at an appropriate angle with each pass.
I like the length of your Viking sword! Lots of viking swords were on the short side (one need only look at the stats in Ian Pearce's Swords of the Viking Age to see this is true, but today's reproductions overwhelming lean to the long side. Personally I prefer a shorter sword as it allows for greater maneuverability and improved technique.
|
|
|
 |
Robin Smith

|
Posted: Fri 30 Nov, 2012 11:41 am Post subject: |
|
|
Have you read that article recently posted on the myArmoury facebook page? Apparently stiffness may be a trait inherent to pattern welding, and may have infact been one of the reasons that pattern welding was done.
This was on MA's facebook a few days ago:
http://www.medievalists.net/2010/10/04/weapon...0-1100-ad/
Its worth noting that the pattern welded sword was significantly stiffer than the "mono-steel" (misnomer that I hate) sword of the same dimensions. It was harder to get it to flex, however once flexed it took a set faster.
Anyway, my point being is that being stiff may be a trait of pattern welded steel. Also, I would measure the distal taper before I started messing around with stuff.
Also remember that PoB of 17, 18, even up to 20+ cm is perfectly normal for swords from this period.
A furore Normannorum libera nos, Domine
|
|
|
 |
Kjell Magnusson
|
Posted: Fri 30 Nov, 2012 12:34 pm Post subject: |
|
|
Considering how little the bulk modulus (stiffness by and large) of steel tends to change with composition and heat treatment relative to the umbers mentioned in the thesis, could it perhaps be that what is seen as stiffness here is deformation hardening kicking in? Especially since the heat treatment was apparently not entirely successful.
Now they do report the amount of follow down to the mm, and I'm not sure if I find it plausible (but gut feeling only though) that a single mm of deformation would allow for enough work hardening to make a significant difference in the amount of force necessary. On the other hand, the table with the result isn't consistent with the number of significant figures used, so the fact that they report their data to the mm might not mean that they actually have that kind of precision in their measurements.
So while the pattern welded blade might at first seem stiffer, in the end it could simply be weaker, and as far as I can tell would then fail much quicker as work hardening accumulates.
|
|
|
 |
Timo Nieminen
|
Posted: Fri 30 Nov, 2012 12:55 pm Post subject: |
|
|
Robin Smith wrote: | Have you read that article recently posted on the myArmoury facebook page? Apparently stiffness may be a trait inherent to pattern welding, and may have infact been one of the reasons that pattern welding was done.
This was on MA's facebook a few days ago:
http://www.medievalists.net/2010/10/04/weapon...0-1100-ad/
Its worth noting that the pattern welded sword was significantly stiffer than the "mono-steel" (misnomer that I hate) sword of the same dimensions. It was harder to get it to flex, however once flexed it took a set faster.
Anyway, my point being is that being stiff may be a trait of pattern welded steel. |
The difference in stiffness was about a factor of 2.
That difference in stiffness won't result from a difference between the steels. The far more likely explanation is that it results from a difference in thickness. The variation of thickness along the lengths of the swords isn't the same, even if the pattern-welded blade was thinned so that it's maximum thickness was the same as the non-PW sword. Small thickness differences translate into big stiffness differences (it's cubic). The difference in thickness alone shouldn't give a factor of 2 (though the original thickness difference before the final grinding/sanding/polishing of almost 20% would go close); the variation in thickness along the length must contribute.
If it results from a difference in the steels themselves, it would need a difference in the Young's modulus (Y). The variation in Y of steels is typically less than 10%, even included stainless steels, moly steels, etc. Mild steel and high carbon steel (like 1095) have very close to the same Y. Wrought iron has Y close to that of steel, too, within 10% or much closer, depending on whose values one looks at.
(There is a factor 2 difference between steel and copper (and typical bronzes).)
The difference in taking a set will be a difference in steels and heat treatment (and blade geometry will contribute).
Luka Borscak wrote: |
Should I be afraid of weakening it? Hanwei heat treatment is usually good enough but since there are welds involved here, I wonder if they made it overbuilt on purpose if they didn't have much faith in their heat treatment of a pattern welded blade? |
You might be right in why it's overbuilt. It's quite reasonable to worry about weakening. (You broke a Godfred, yes?). The Hanwei Trondheim was a little thinner, but I don't know of anybody doing any serious cutting with one.
If I had a Hanwei Saxon, and thinned the blade a lot, I don't think I'd cut with it. YMMV. If it breaks, you might be able to make a nice pattern-welded spearhead and/or seax.
"In addition to being efficient, all pole arms were quite nice to look at." - Cherney Berg, A hideous history of weapons, Collier 1963.
|
|
|
 |
Robin Smith

|
Posted: Fri 30 Nov, 2012 2:49 pm Post subject: |
|
|
Timo Nieminen wrote: | Robin Smith wrote: | Have you read that article recently posted on the myArmoury facebook page? Apparently stiffness may be a trait inherent to pattern welding, and may have infact been one of the reasons that pattern welding was done.
This was on MA's facebook a few days ago:
http://www.medievalists.net/2010/10/04/weapon...0-1100-ad/
Its worth noting that the pattern welded sword was significantly stiffer than the "mono-steel" (misnomer that I hate) sword of the same dimensions. It was harder to get it to flex, however once flexed it took a set faster.
Anyway, my point being is that being stiff may be a trait of pattern welded steel. |
The difference in stiffness was about a factor of 2.
That difference in stiffness won't result from a difference between the steels. The far more likely explanation is that it results from a difference in thickness. The variation of thickness along the lengths of the swords isn't the same, even if the pattern-welded blade was thinned so that it's maximum thickness was the same as the non-PW sword. Small thickness differences translate into big stiffness differences (it's cubic). The difference in thickness alone shouldn't give a factor of 2 (though the original thickness difference before the final grinding/sanding/polishing of almost 20% would go close); the variation in thickness along the length must contribute.. |
I'm no metallurgist, so I'm just going by what was published. They state that the difference in blade thickness was about 0.5mm
The author of the article draws the conclusion that stiffness in PW may have been a feature. This is his masters thesis so I would assume its undergone some review.
A furore Normannorum libera nos, Domine
|
|
|
 |
Timo Nieminen
|
Posted: Fri 30 Nov, 2012 4:12 pm Post subject: |
|
|
Robin Smith wrote: |
I'm no metallurgist, so I'm just going by what was published. They state that the difference in blade thickness was about 0.5mm
The author of the article draws the conclusion that stiffness in PW may have been a feature. This is his masters thesis so I would assume its undergone some review. |
People do tend to go by what they read in papers and thesis, and reputable looking books. Errors in them tend to be carried on, which is why criticism of such things matters.
The 0.5mm was after the pre-heat-treatment grinding, and was reduced in the final grinding. 0.5mm would have given a difference in stiffness of about 45%, if the swords were otherwise uniform, and the 0.5mm difference was at the maximum thickness.
Better by far would have been to give some samples to metallurgists who regularly measure such things (like elastic moduli). And hardness, and fracture toughness, and tensile strengths.
The biggest methodological problem is to simply ignore the effect of blade geometry on stiffness, when it was known that the two blades had different geometries.
Other than that, given that there tends to be variation in hand-made samples, anything stated as a somewhat definitive conclusion based on a sample size of 1 looks rather premature. http://www.phdcomics.com/comics/archive.php?comicid=1539
Depending on the kind of masters thesis, there aren't necessarily any corrections made after examiners read it. Even if there are, 2 examiners is normal, and I'd expect the ones for this thesis to have been archaeologists, who may not have been familiar enough with metallurgy. It's not at all rare to see people who do a lot with swords mix up things like elastic moduli, hardness, and strengths.
One of the important points of experimental archaeology is to discover when expectations and preconceptions are wrong; it's bad to create new ones in the process.
"In addition to being efficient, all pole arms were quite nice to look at." - Cherney Berg, A hideous history of weapons, Collier 1963.
|
|
|
 |
Luka Borscak

|
Posted: Sun 02 Dec, 2012 4:28 am Post subject: |
|
|
Interesting replies guys, thank you. But I'm now more confused than before about what to do. I doubt that stiffness of my sword has much to do with the fact it is pattern welded. I don't have caliper but it is obvious it has no distal taper until the last few centimeters of the blade. So, it is about 4mm-5mm thick along the almost entire blade length. If it was a long blade it might be whippy because of the lack of distal taper but since it's a short blade and so thick, it's as stiff as a bar. Since the edges are not pattern welded but just regular 1095 carbon steel, I might be able to add distal taper without messing with pattern welded parts, maybe just edges of pattern welded core...
|
|
|
 |
Jack Savante

|
Posted: Sun 02 Dec, 2012 5:02 am Post subject: |
|
|
Hi,
Just bring the edges down to about 2mm close to the tip and work the remainder getting slightly thicker. For example 2mm thick 5cm up, 2.5mm 10cm up, 3cm 15cm up and so on. No need to mess with the core.
This should give you a lively feeling sword that is still nice and stiff. It has been my experience that less flex is better than more flex.
|
|
|
 |
Luka Borscak

|
Posted: Sun 02 Dec, 2012 5:30 am Post subject: |
|
|
I agree. I have nothing against stiff if it is a result of proper geometry and taper. Stiff swords perform better if they are stiff for right reasons...
|
|
|
 |
Glen A Cleeton

|
Posted: Sun 02 Dec, 2012 5:36 am Post subject: |
|
|
Hi Luka
I mention the thickness in the fuller not because of taper for the beveled area but that the section of the fuller may be pretty thin to begin with and removing material from the beveled area is simply going to weaken the sword. Mentioned by yourself, my other reply and others, that removing material at all will make for a less sturdy sword. You may find other mentions of grinding through fullers while making swords but the point here is that it is still structure and if very thin, the "hard" of the beveled edge will be weakened some in grinding.
Indeed, Hanwei may have over built it to begin with. HAs anyone proved it os actually of complex make with separate steel for the edges?
http://www.swordforum.com/forums/showthread.p...res-added)
If you are having someone else doing the grinding, I imagine they will have an idea of how thin will then be too thin. A friend has reground a number of swords and the differences apparent but the point here is whether you are looking for a sword that will flourish nicely, or remain sturdy enough for regular cutting.
FWIW, even though my old Godfred broke doing stupid human tricks and the blade was hriibly overheated in heat treat, I had put a slice though both sides of a hollow core door the first day I had it.
Cheers
GC
|
|
|
 |
Luka Borscak

|
Posted: Sun 02 Dec, 2012 5:59 am Post subject: |
|
|
I wouldn't do it myself, definitely someone who knows his job would do it. It really is a real pattern welded core and monosteel edges, Alojz and me played with it with acid and polishing.
|
|
|
 |
|
You cannot post new topics in this forum You cannot reply to topics in this forum You cannot edit your posts in this forum You cannot delete your posts in this forum You cannot vote in polls in this forum You cannot attach files in this forum You can download files in this forum
|
All contents © Copyright 2003-2025 myArmoury.com All rights reserved
Discussion forums powered by phpBB © The phpBB Group
Switch to the Basic Low-bandwidth Version of the forum
|