Author |
Message |
Gavin Kisebach

|
Posted: Tue 15 Jan, 2008 6:38 pm Post subject: Socketed lance heads from Native Way |
|
|
I just wanted to do a quick writeup on some steel spearheads that I bought from Native Way over the holiday. The original plan was to use them as cheap viking throwing spears, but they turned out to be larger (and much cooler) than I had originally pictured.
Native Way is a primitive weapon and flintknapping supplier that I found whilst looking for images of cavalry lances. I didn't look too deeply into their website, but the majority of their products are geared towards stone and bronze age hunting tools.
http://nativeway.safewebshop.com/
Overview
Native way is selling these as "socketed lance heads" fit for a wide range of cultures and time periods. This assessment is fairly accurate; the head is a very generic elongated diamond shape with a diamond cross section, built on a large, heavy duty socket. The measurements provided were 14 inches length overall, 1 3/4 inches wide, though I measured the head at the widest point. The blade itself is 9 inches long. The socket is 5 inches long with an interior diameter of 1 1/8 inches wide. Native Way informed me that they were made in Pakistan but did not specify the manufacturer.
Fit and Finish
The heads are carbon steel and were shipped in plastic bags covered in grease. Once the grease was wiped away, some discoloration on both heads was evident, but polished out fairly easily. Of the two heads I purchased, one had the very last two millimeters of the tip broken off. Normally I would have returned the damaged head, but I wanted one for display and one for hard use anyhow. The overall construction is very stout; the socket is 2mm thick, and the blade exhibits a constant distal taper from 6mm at the socket joint down to less than 1mm at the tip. One gets the immediate impression that this was built for hard use, but retains an elegant simplicity that is very pleasing to the eye. No rivet hole was provided, but the sockets are easy enough to tap that this was not a problem.
Handling Characteristics
Off the haft, the socket seems unnaturally bulky, but one mounted on a short (6ft) haft this makes the head very agile; again the design proves to be well thought out. Thrusts are forceful but easy to recover. There is sufficient edge on the front half of the blade to slash against an unarmored target. This is a very quick and deadly sharp tool.
Conclusion
Native way is currently offering these lance heads for $20 a piece. At this price these are an excellent purchase, and I almost wish I had bought a couple more as gifts.
Attachment: 28.57 KB
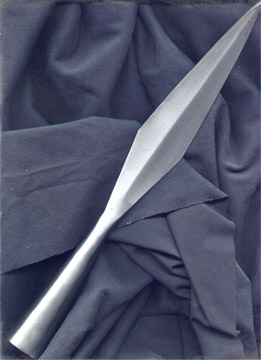
|
|
|
 |
Sean Flynt

|
|
|
 |
M. Eversberg II

|
Posted: Wed 16 Jan, 2008 7:20 am Post subject: |
|
|
Seems like a nice project.
What did you haft yours onto, and what did you rivet it with?
M.
This space for rent or lease.
|
|
|
 |
Jean Thibodeau

|
Posted: Wed 16 Jan, 2008 8:54 am Post subject: |
|
|
Interesting site and I've just bookmarked it for future reference and will have a closer look at what they offer.
With a thick walled socket and a shaft of diameter equal to the outside diameter of the socket, I would think that one could recess the socket so that the outside of the socket and the shaft are flush or close to flush: Would look good and maximize the diameter of the shaft if one wanted a very stout shaft for a mostly handheld spear that wouldn't be thrown except at very close range.
Was this done historically when mounting spears or other polearms ? I would do it anyway, but it's useful to know for those its an important thing to be strictly historically correct.
You can easily give up your freedom. You have to fight hard to get it back!
|
|
|
 |
Sean Flynt

|
Posted: Wed 16 Jan, 2008 10:15 am Post subject: |
|
|
Jean Thibodeau wrote: | Interesting site and I've just bookmarked it for future reference and will have a closer look at what they offer.
With a thick walled socket and a shaft of diameter equal to the outside diameter of the socket, I would think that one could recess the socket so that the outside of the socket and the shaft are flush or close to flush: Would look good and maximize the diameter of the shaft if one wanted a very stout shaft for a mostly handheld spear that wouldn't be thrown except at very close range.
Was this done historically when mounting spears or other polearms ? I would do it anyway, but it's useful to know for those its an important thing to be strictly historically correct. |
This is the way I haft polearms, and it's the method I've seen on most--maybe even all-- originals of the 15th/16th century. See images below for spears with original hafts or informed reconstructions. Artwork also typically shows flush mounting.
By the way, I use 1.25" diameter poplar dowels for my spear hafts and ordinary bright nails for the rivets (through both walls of the socket, cut off and peened, original head hammered to match the peen. Most (all?) modern spear heads are made like those described above, with ~ a 1 1/8 internal diameter to match the commonly available 1.25" dowels, with allowance for flush mounting.
Attachment: 113.06 KB
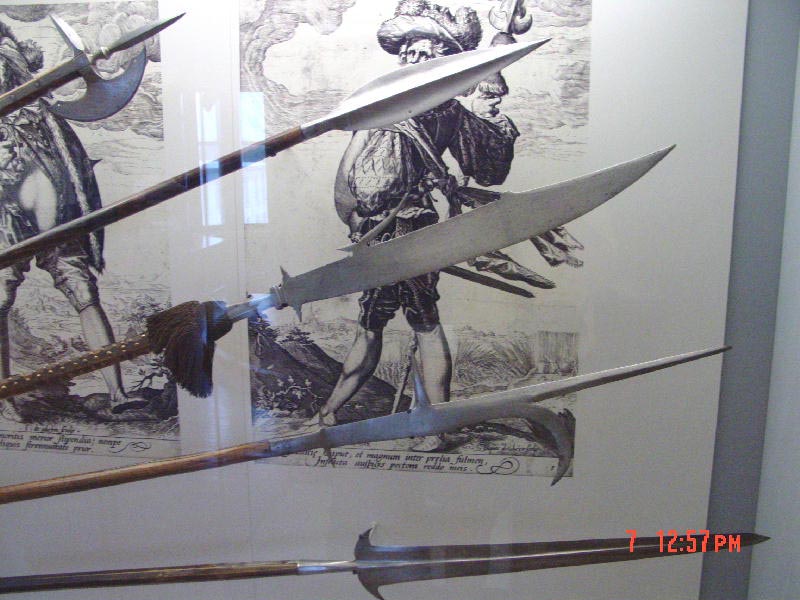
Attachment: 90.98 KB
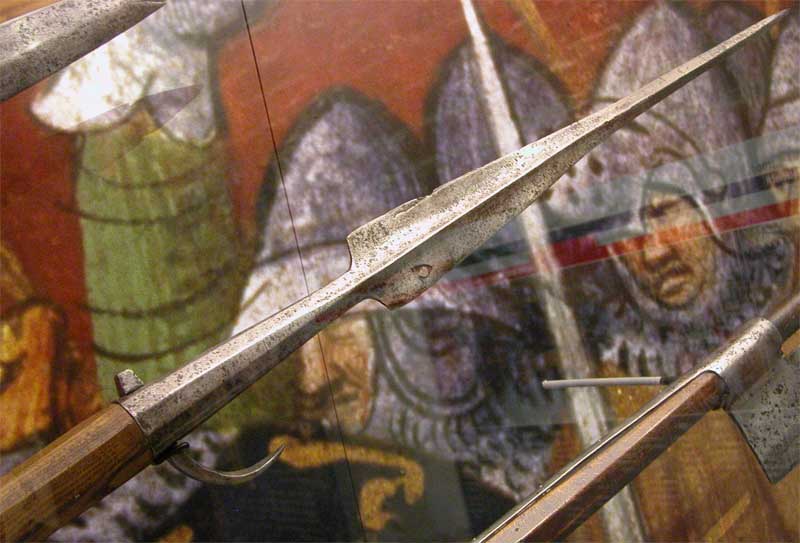
Attachment: 18.43 KB

Attachment: 48.6 KB
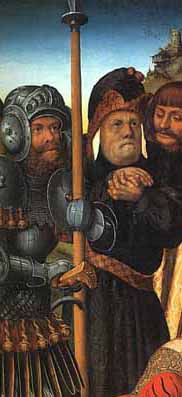
Attachment: 70.42 KB
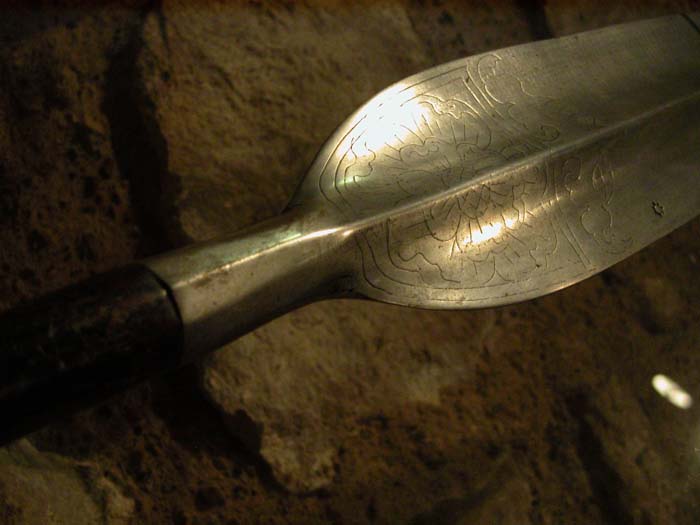
-Sean
Author of the Little Hammer novel
https://www.amazon.com/Little-Hammer-Sean-Flynt/dp/B08XN7HZ82/ref=sr_1_1?dchild=1&keywords=little+hammer+book&qid=1627482034&sr=8-1
|
|
|
 |
Gavin Kisebach

|
Posted: Wed 16 Jan, 2008 11:57 am Post subject: |
|
|
Quote: | I wish I'd known about these before I invested so much time in de-vik-ifying a Hanwei Viking Throwing Spear head. |
I liked the Hanwei spears a lot better before they started "antiquing" everything. I don't necessarily want my weapons to look like I dug them up (though I understand the sentiment) but rather like they were brought forward in time. Did you have to grind off the "patina" they put on there?
Quote: | What did you haft yours onto, and what did you rivet it with? |
1 1/4 closet rod and a section of nail peened over. It didn't seem logical at this point to put a $30 ash haft on a $20 head. I won't tell anyone if you don't.
|
|
|
 |
Sean Flynt

|
|
|
 |
James King
|
Posted: Wed 16 Jan, 2008 1:31 pm Post subject: sockets |
|
|
I purchased two of those spearheads a few years ago. I cut off the last 2 inches of socket and shaped them with a file, turned out nice.These spearheads appear to be forged from a single piece of steel.They compare very well to my Arms and Armer "viking" spear as well as my custom Mark Morrow spear.
|
|
|
 |
Jeroen Zuiderwijk
Industry Professional
|
Posted: Wed 16 Jan, 2008 2:18 pm Post subject: |
|
|
Jean Thibodeau wrote: | With a thick walled socket and a shaft of diameter equal to the outside diameter of the socket, I would think that one could recess the socket so that the outside of the socket and the shaft are flush or close to flush: Would look good and maximize the diameter of the shaft if one wanted a very stout shaft for a mostly handheld spear that wouldn't be thrown except at very close range. | A step in the wood is not recommended, as it severely weakens the shaft at that location. With a thick strong haft before the recess, and the shaft supported by the spearhead just after, the shaft would very easily snap right there. It's better to thin down the socket at the edge, so you don't need much of a recess. I know this was done in the bronze age, but I don't know about later periods.
|
|
|
 |
Jean Thibodeau

|
Posted: Wed 16 Jan, 2008 5:43 pm Post subject: |
|
|
Jeroen Zuiderwijk wrote: | Jean Thibodeau wrote: | With a thick walled socket and a shaft of diameter equal to the outside diameter of the socket, I would think that one could recess the socket so that the outside of the socket and the shaft are flush or close to flush: Would look good and maximize the diameter of the shaft if one wanted a very stout shaft for a mostly handheld spear that wouldn't be thrown except at very close range. | A step in the wood is not recommended, as it severely weakens the shaft at that location. With a thick strong haft before the recess, and the shaft supported by the spearhead just after, the shaft would very easily snap right there. It's better to thin down the socket at the edge, so you don't need much of a recess. I know this was done in the bronze age, but I don't know about later periods. |
Instead of a 90 degree step down by tapering the socket one avoids a sudden change of diameter and a weakening of the shaft, but one can still have a thicker diameter shaft: It should produce a flush looking transition but be stronger.
Sort of the same principle as the tang transition to blade should have radiused corners to avoid stress risers.
Well, this is how I interpret your comments.
You can easily give up your freedom. You have to fight hard to get it back!
|
|
|
 |
M. Eversberg II

|
Posted: Wed 16 Jan, 2008 6:31 pm Post subject: |
|
|
So I just sand down the shaft by .25" to fit?
M.
This space for rent or lease.
|
|
|
 |
Gavin Kisebach

|
Posted: Wed 16 Jan, 2008 6:39 pm Post subject: |
|
|
I'm having trouble with the physics on this. What is the difference strengthwise between a taper to 1" or a step to 1"? In either case the weakest point will be the 1" section, unless there is some interaction between the wood fibers that is not intuitive.
|
|
|
 |
Jean Thibodeau

|
Posted: Wed 16 Jan, 2008 9:12 pm Post subject: |
|
|
Gavin Kisebach wrote: | I'm having trouble with the physics on this. What is the difference strengthwise between a taper to 1" or a step to 1"? In either case the weakest point will be the 1" section, unless there is some interaction between the wood fibers that is not intuitive. |
Like I said in my previous post I'm assuming it's like a stress riser in principle were a sudden narrowing concentrates force at a specific point when a change of dimensions is a sudden 90 degree step.
If the corner is radiused or the step is done at a gradual shallow angle the change of diameter happens gradually and stress is spread over a length of tang or in this case a length of the shaft.
Although, I'm not myself sure about the actual physics and may not be explaining it accurately.
Take a hardened steel rod or a piece of glass and score the surface: Even a scratch is enough for the rod or piece of glass to break exactly in the scratch/groove. This is used all the time when cutting glass or ceramic tiles.
You can easily give up your freedom. You have to fight hard to get it back!
|
|
|
 |
Jeroen Zuiderwijk
Industry Professional
|
Posted: Thu 17 Jan, 2008 2:19 am Post subject: |
|
|
Jean Thibodeau wrote: | Gavin Kisebach wrote: | I'm having trouble with the physics on this. What is the difference strengthwise between a taper to 1" or a step to 1"? In either case the weakest point will be the 1" section, unless there is some interaction between the wood fibers that is not intuitive. |
Like I said in my previous post I'm assuming it's like a stress riser in principle were a sudden narrowing concentrates force at a specific point when a change of dimensions is a sudden 90 degree step.
If the corner is radiused or the step is done at a gradual shallow angle the change of diameter happens gradually and stress is spread over a length of tang or in this case a length of the shaft.
Although, I'm not myself sure about the actual physics and may not be explaining it accurately.
Take a hardened steel rod or a piece of glass and score the surface: Even a scratch is enough for the rod or piece of glass to break exactly in the scratch/groove. This is used all the time when cutting glass or ceramic tiles. | That's one of the effects. The other is that the edge of the spearhead is were all the non-axial loads get introduced into the already weakened area. It's basically like making a cut in the pole, and striking it at the opposite end with a localized force. It may even happen that if the shaft gets struck from the side far from the spearhead, the spearhead will snap off due to the shock traveling through the wood (particularly if the spearhead has a bit of weight to it).
You still have the latter as problem, but if the edge of the socket is thinner, the force introduced by the socket edge is on a wider section of pole. And as the step is less or non existant, you also have less stress risers there.
|
|
|
 |
Sean Flynt

|
Posted: Thu 17 Jan, 2008 7:37 am Post subject: |
|
|
I made some darts/light javelins a few years ago using large medieval swallowtail arrowheads. Instead of mounting the heads on a simple tapered haft, as one would when making arrows in historical fashion, I mounted them flush on tapered and stepped 48", .5" diameter poplar dowels. Given the taper, the haft stepped down from about 3/8" to 5/16". During throwing experiments one of these darts struck a rock and the head snapped off cleanly at the step. I decided that the step serves as a very efficient lever point for the edge of the socket when the head strikes an unyielding object at an angle. I slapped my forehead. Maybe arrowheads were mounted on simple tapered shafts for reasons other than weight savings or simplicity of manufacture. Duh! Lesson learned. I also understood why at least one contemporary writer decried the common use of poplar for arrow shafts instead of superior ash.
Polearms are different (at least in the medieval period for which there is artistic documentation and surviving weapons). Spearheads seem typically to have been flush-mounted with some kind of step, either straight or sloped, thinned edge or not. I hadn't thought of the sloped step solution, but I think that's a compelling idea, albeit one that requires a thin socket edge, which seems counterintuitive for reasons described below. I have little doubt that a straight step puts extra stress on the haft, but I also have little doubt that this matters more in the case of the narrow shafts of arrows. An 1/16" step down on an arrow shaft might prove catastrophic. I'm not yet convinced that a 1/8" step down from a 1.25" spear haft poses significant risk to the haft. I sure would love to get a close look at the sockets of unmounted historical heads now that I know what I would want to look for (a very thin edge quickly sloping up inside to a thick socket wall).
As for thinning the edge of the socket--there might be more danger in this than in a straight step because a too-thin wall could be deformed or torn around the rivet. There is also the case of the spear shown below, which clearly was intended to withstand tremendous stress in the socket walls around its rivet. Now, this is a replacement haft, but one made or at least approved by the Royal Armouries, Leeds. It's flush mounted, with what must be a very thick socket and little, if any, thinned edge.
The other photo below gives some idea of socket wall thickness. The edges of some of these sockets are straight and quite thick, just like most modern repros. We don't know if these were flush mounted, but artistic evidence suggests that they probably were.
Polearms study lags far behind sword study, but that at least leaves us to ponder such interesting technical questions!
I think all we can say with certainty is that contemporary artwork and surviving examples show flush mounting. It's also reasonable to assume that flush mounting would not have been the norm if it was known to compromise the weapon.
Attachment: 90.98 KB

Attachment: 20.09 KB
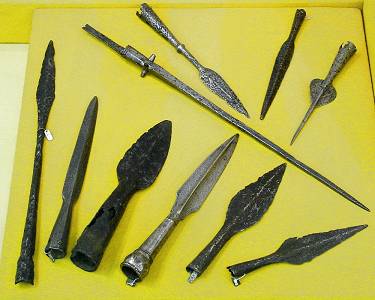
-Sean
Author of the Little Hammer novel
https://www.amazon.com/Little-Hammer-Sean-Flynt/dp/B08XN7HZ82/ref=sr_1_1?dchild=1&keywords=little+hammer+book&qid=1627482034&sr=8-1
|
|
|
 |
Sean Flynt

|
Posted: Thu 17 Jan, 2008 8:02 am Post subject: |
|
|
This is a rough diagram of my spearhead mounting method, originally posted in another thread here (the step is exaggerated for clarity). If, instead of presenting this as a how-to diagram, I were to ask, "which of these sticks would be most likely to break?," I think most of us would choose the middle image. I don't know if this perception is true. Somebody else will have to tackle the physics involved, but I'd sure like to know, through both theory and experiment, if a 1/8" step on a 1.25" diameter pole significantly weakens it at that point. I'd also like to hear speculation about why flush mounting seems to have been the common method of construction. Surely it isn't purely aesthetic....? It's a lot more trouble than a simple tapered haft.
Attachment: 8.74 KB
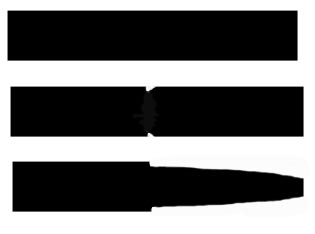
-Sean
Author of the Little Hammer novel
https://www.amazon.com/Little-Hammer-Sean-Flynt/dp/B08XN7HZ82/ref=sr_1_1?dchild=1&keywords=little+hammer+book&qid=1627482034&sr=8-1
|
|
|
 |
M. Eversberg II

|
Posted: Thu 17 Jan, 2008 8:33 am Post subject: |
|
|
My intuition says that I would sand the point end to match the interior of the socket, fit it over, and rivet it in place.
M.
This space for rent or lease.
|
|
|
 |
Sean Flynt

|
Posted: Thu 17 Jan, 2008 8:41 am Post subject: |
|
|
M. Eversberg II wrote: | My intuition says that I would sand the point end to match the interior of the socket, fit it over, and rivet it in place.
M. |
Do yourself a huge favor and pick up a Stanley "Surform" tool at your local home improvement store (you'll want the hand-size model--well under $10). It's a bit like a cheese grater, easily, quickly and evenly tapering the haft, whether or not you use a step. Sanding the haft into shape will take forever and a day.
Attachment: 13.47 KB
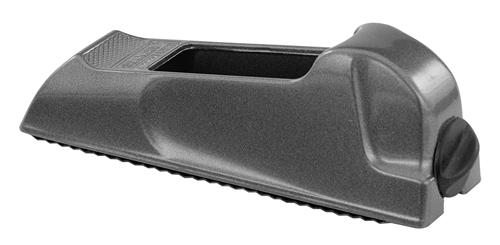
Attachment: 20.75 KB
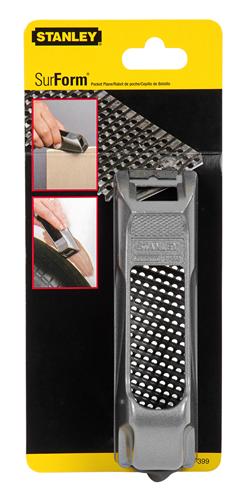
-Sean
Author of the Little Hammer novel
https://www.amazon.com/Little-Hammer-Sean-Flynt/dp/B08XN7HZ82/ref=sr_1_1?dchild=1&keywords=little+hammer+book&qid=1627482034&sr=8-1
|
|
|
 |
Jerry Knox
Location: Palm Bay, Florida, USA Joined: 12 Jun 2007
Posts: 53
|
Posted: Thu 17 Jan, 2008 9:16 am Post subject: |
|
|
Quote: | This is a rough diagram of my spearhead mounting method, originally posted in another thread here (the step is exaggerated for clarity). If, instead of presenting this as a how-to diagram, I were to ask, "which of these sticks would be most likely to break?," I think most of us would choose the middle image. I don't know if this perception is true. Somebody else will have to tackle the physics involved, but I'd sure like to know, through both theory and experiment, if a 1/8" step on a 1.25" diameter pole significantly weakens it at that point. I'd also like to hear speculation about why flush mounting seems to have been the common method of construction. Surely it isn't purely aesthetic....? It's a lot more trouble than a simple tapered haft. |
By notching the shaft to a minimum diameter of 1", you effectively create a 1" diameter rod mounted into your spearhead, and then encased in a 1/8" thick tube over the rest of its length. When you try to flex it, you're flexing a 1" diameter rod, which is significantly less stiff than a 1.25" rod. Given the relatively low ultimate strain of wood, this can drastically increase the chance of snapping the shaft.
The step will act as a stress riser proportionally to how square its internal corner is (i.e. 90 degrees is bad, 179 degrees is good), but unless you actually cut into the shaft deeper than 1/8", it will still be proportionally as strong as a 1" shaft, you'll just be certain to know where the break will be when it happens :-)
As to which of the pictures is worst, the second and third would be the same once a spearhead was mounted onto the third one, as it would more than make up for the lost stiffness of the removed wood.
Sorry I don't have numbers, but I could do a calculation later if anyone wants.
|
|
|
 |
Sean Flynt

|
Posted: Thu 17 Jan, 2008 9:39 am Post subject: |
|
|
Jerry Knox wrote: | Given the relatively low ultimate strain of wood, this can drastically increase the chance of snapping the shaft. ...unless you actually cut into the shaft deeper than 1/8", it will still be proportionally as strong as a 1" shaft, you'll just be certain to know where the break will be when it happens :-) |
Very interesting!
Decreasing the diameter of the haft increases the likelihood of damage. No surprise there. An oak 4x4 would make a much stronger shovel handle than a length of 1" diameter ash. It also would be ridiculously impractical and, in ordinary use, pointless. Ditto for polearms. It's undeniably true that a 1.25" diameter haft is stronger than a 1" haft, but the real questions are whether or not a 1" diameter haft is historically valid and, if so, is it compromised by a step.
If I understand the point made above, a haft stepped down to 1" diameter is not weaker than a simply-tapered 1" diameter haft. It just has a more predictable break point.
I think this is the heart of the concern, and the lesson may be that we're thinking about this in the reverse order of our medieval friends. They may have determined the optimal diameter for a spear shaft and then stepped up, overbuilding slightly and creating a flush surface between socket and haft (for reasons unknown). For our modern purposes, this would mean that a 1 1/8 haft is plenty strong for a spear, and we're not compromising that strength by "adding" 1/8 to create the flush surface. Does that make sense, or am I trying too hard to match the physics to the historical practice?
-Sean
Author of the Little Hammer novel
https://www.amazon.com/Little-Hammer-Sean-Flynt/dp/B08XN7HZ82/ref=sr_1_1?dchild=1&keywords=little+hammer+book&qid=1627482034&sr=8-1
|
|
|
 |
|
You cannot post new topics in this forum You cannot reply to topics in this forum You cannot edit your posts in this forum You cannot delete your posts in this forum You cannot vote in polls in this forum You cannot attach files in this forum You can download files in this forum
|
All contents © Copyright 2003-2024 myArmoury.com All rights reserved
Discussion forums powered by phpBB © The phpBB Group
Switch to the Basic Low-bandwidth Version of the forum
|