Just finished another lockdown project which I thought I would share, following on from the bauernwehr a few weeks back, though took some process pictures this time.
This is my interpretation of a 15th/16th century messer. I really like the Breughal inspired pieces that Tod and others have replicated and so this was the main influence. The Wakefield falchions were another, though these are bigger and a little earlier, but smash those two designs together and you get something a bit like this maybe. Hopefully it looks historically plausable...
This looks bigger in the photos than reality I think, only 43cm long, but looking at the knives in 'Peasant Wedding' they don't seem to be much different. I was mostly limited by the size of the quench tank and what could fit in the oven really. The blade is forged from 1075+cr, tapering from 6mm at the guard down to 3ish at the tip. fittings are all mild steel, and the handle is walnut.
Anyway I hope you like it! I'll follow this with a couple of WIP replies if anyone is interested in how it was made. I have a photo of 9 year old me at a reenactment event holding one of these and it's stuck with me since. 15 years later and I finally have my own, so quite a special project for me, and a nice big tick on the bucket list.
Any comments or critiques welcome, lots of you are much better at this stuff than me so always happy to learn something new
Cheers!
Alex

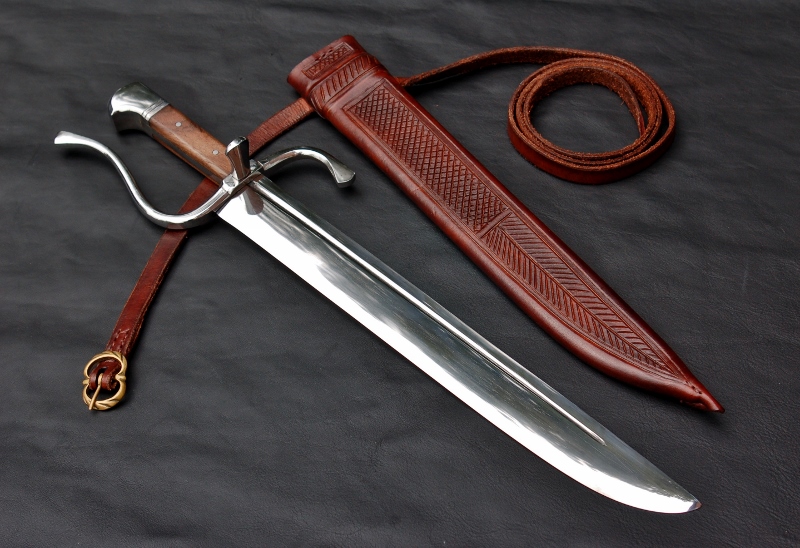

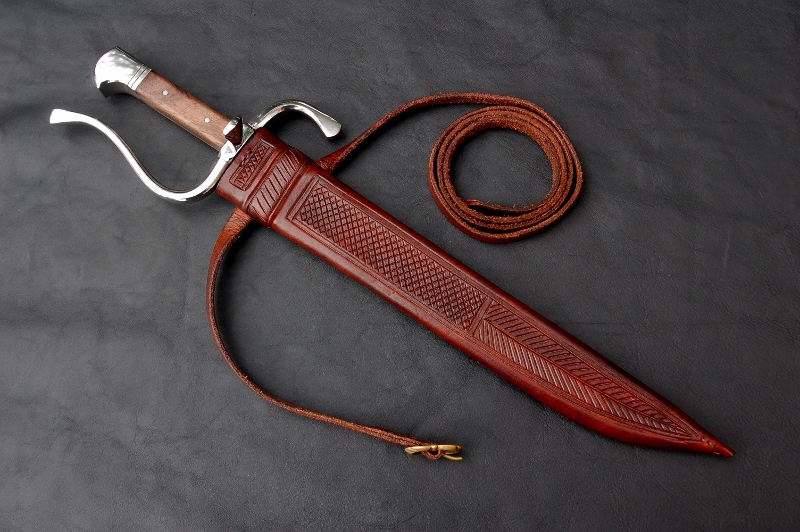



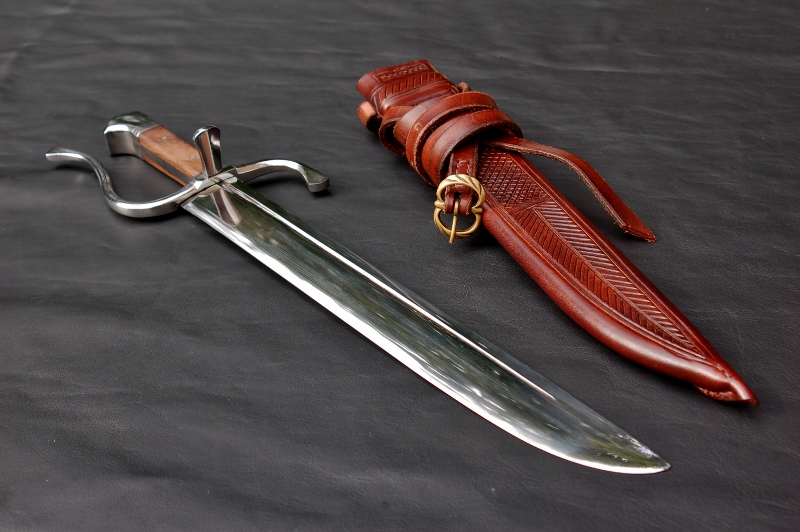

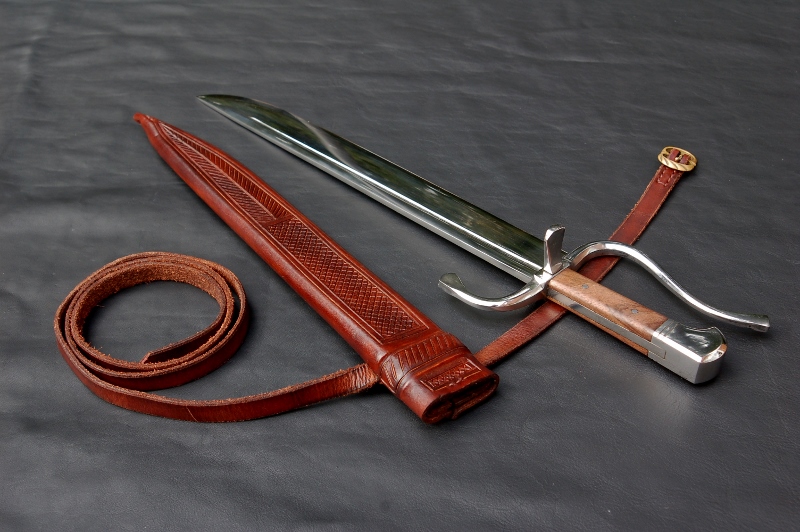

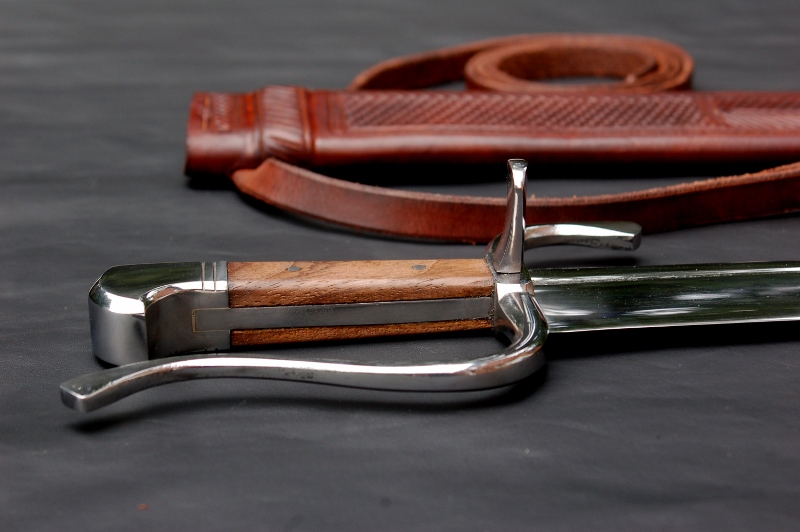

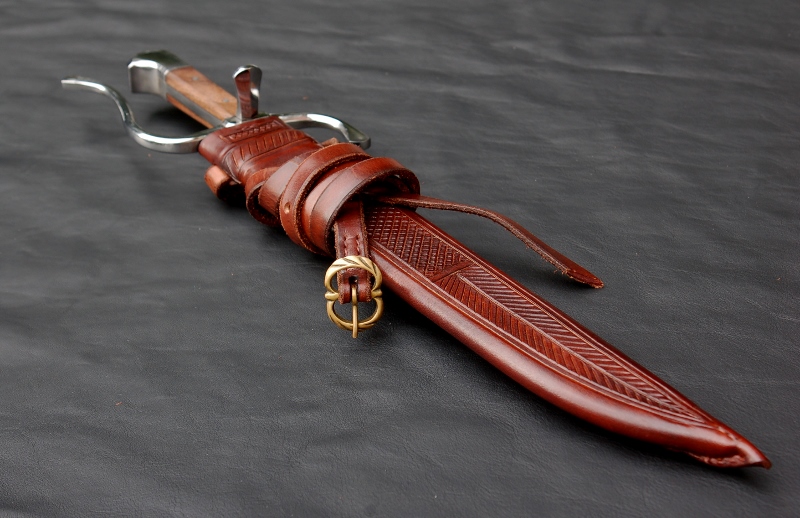

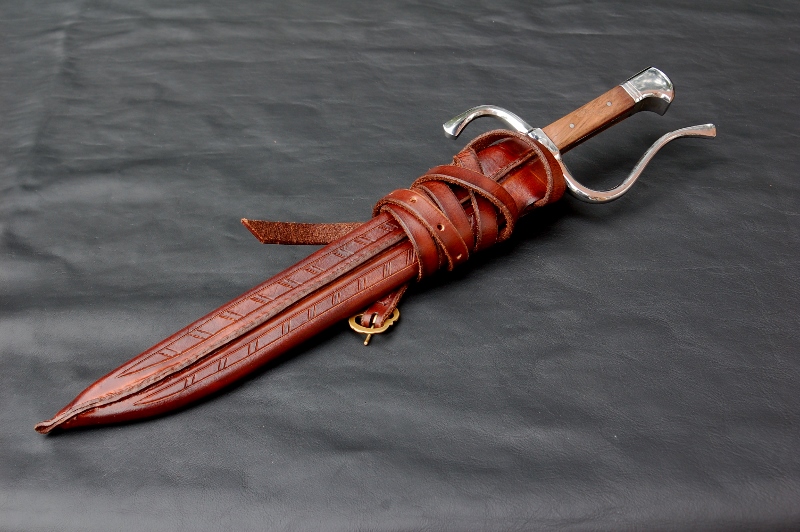