I must be the only person on the board that actually liked the hex nut design which was for me, a blend of new and old. :D
I like the hex nut to some degree but I still prefer either mechanical or hot peen. people who like the hex nut seem to be pretty rare while people who dislike or hate it are common. usually the best we get is neutral. a few years ago it seemed to be that the nut wasn't a big deal.
Hex nut construction is still available we are just offering plenty of options so that we can have something for everyone.
Hex nut construction is still available we are just offering plenty of options so that we can have something for everyone.
I too like the hex nut assembly and am a bit amused at the "it's not historical" flogging the hex nut design gets. Everybody seems to be happy with modern bar stock steels, CNC machining, castings, belt sanding,machine made symmetry, etc. for their "historical" reproduction swords. The hex nut is just too anti-historical for a reproduction? Really? I've been playing with hex-nut assembled swords for over tens years with no failures. Maybe I'm just easy to please and my toys don't need to be "perfect."
Maybe someone out there can make a peened cap that fits into the hex to cap it off making it look like it is peened... :p
Or, if the sword owners get really worked up about it, they could cut a nail or large thumbtack to size and glue it over the end, maybe even get fancy and whack it a few times with a hammer to give it more of a peened look...
Ken Jay wrote: |
I too like the hex nut assembly and am a bit amused at the "it's not historical" flogging the hex nut design gets. Everybody seems to be happy with modern bar stock steels, CNC machining, castings, belt sanding,machine made symmetry, etc. for their "historical" reproduction swords. The hex nut is just too anti-historical for a reproduction? Really? I've been playing with hex-nut assembled swords for over tens years with no failures. Maybe I'm just easy to please and my toys don't need to be "perfect." |
Well-done CNC machining, castings, belt sanding, modern steels, etc. don't create an ahistoric look as easily and obviously as a hex nut hole in the pommel's end. All these constructional things are indeed deviations from the way historical swords were made. However, you can make cast and parts made with electricity-assisted grinding look more period than a hex shaped hole in a pommel. The hole is harder to hide. Consider that when you wear a sword and walk straight up to someone, the bottom end of the pommel is what people will see first. A modern shaped recess is not the first impression I want to convey.
Failures or lack of failures, our ancestors didn't do it that way (apart from an odd mention or two in a fechtbuch or two). For me, it's a non-starter. Mileage and opinion on this do vary which a lot is why this method persists and has its ardent fans in the marketplace. It's just not for me. :)
For me the hex nut just doesn't seem right, not to say it doesn't work or its completely un-historical...I just don't like it! I like to feel the peen, to seen the peen..plus who really wants to have to add 'lock tight' to the thread to stop the darn thing from comming loose!
Really if its for changing blades, on the likes of sparring swords then yea its all good, but even then...as one of our members has a Tinker/Hanwei blunt bastard which she uses for the art of learning longsword, but the hex comes loose often even after having 'lock tight' added [lock tight for those who may call it something else is that plastic type glue that you put on threads to lock the nut] and after awhile the hex on the nut has stripped somewhat, lucky though as Hanwei are sending our supplyer some spare nuts for us. Maybe a nut with an eye hook type hole protruding from the pommel would be a better tighting system other than the hex? I can't say if this happens to all the hex locked hilts though, maybe only Hanweis' issue?
Anyway ATrim swords look cool and seem to be a good price, espcially for the likes of us in New Zealand with the exchange rates and all so new extras like scent stoppers and hot peens as standard will be great.
cheers.
Really if its for changing blades, on the likes of sparring swords then yea its all good, but even then...as one of our members has a Tinker/Hanwei blunt bastard which she uses for the art of learning longsword, but the hex comes loose often even after having 'lock tight' added [lock tight for those who may call it something else is that plastic type glue that you put on threads to lock the nut] and after awhile the hex on the nut has stripped somewhat, lucky though as Hanwei are sending our supplyer some spare nuts for us. Maybe a nut with an eye hook type hole protruding from the pommel would be a better tighting system other than the hex? I can't say if this happens to all the hex locked hilts though, maybe only Hanweis' issue?
Anyway ATrim swords look cool and seem to be a good price, espcially for the likes of us in New Zealand with the exchange rates and all so new extras like scent stoppers and hot peens as standard will be great.
cheers.
Chad Arnow wrote: | ||
Well-done CNC machining, castings, belt sanding, modern steels, etc. don't create an ahistoric look as easily and obviously as a hex nut hole in the pommel's end. All these constructional things are indeed deviations from the way historical swords were made. However, you can make cast and parts made with electricity-assisted grinding look more period than a hex shaped hole in a pommel. The hole is harder to hide. Consider that when you wear a sword and walk straight up to someone, the bottom end of the pommel is what people will see first. A modern shaped recess is not the first impression I want to convey. Failures or lack of failures, our ancestors didn't do it that way (apart from an odd mention or two in a fechtbuch or two). For me, it's a non-starter. Mileage and opinion on this do vary which a lot is why this method persists and has its ardent fans in the marketplace. It's just not for me. :) |
Perfectly understandable and no argument from me on the aesthetics. But I've never worn any of my swords and for my purposes (a bit of Walter Mitty and cutting/piercing targets) the lesser historically correct hex nut works just fine. My targets never seem to notice the hole in the pommel. ;) As an aside even with solid use, my ATrim handles stay tight. I guess we should be happy the various methods of assembly are available for our varying tastes. :D
Ralph Grinly wrote: |
While flush ground peens are historically correct, I feel that if used..there'll always be questions on just how much of a countersink there is on the pommel? If the peen is NOT ground flush..one can always tell if there is a decent amount of metal holding everything together ? I know all reputable makers would ensure there was a decent countersink, but still feel they'll always be questioned ? |
Personally I don't really see this as an issue - if you don't trust a maker enough to properly flush peen the pommel maybe you shouldn't be buying from them in the first place ;)
As to the the topic at hand - I sort of like the head of the peen showing just because it seems like most of the swords I've seen have the peen ground flush. Either way, having both options available is nice.
Ken Jay wrote: | ||||
Perfectly understandable and no argument from me on the aesthetics. But I've never worn any of my swords and for my purposes (a bit of Walter Mitty and cutting/piercing targets) the lesser historically correct hex nut works just fine. My targets never seem to notice the hole in the pommel. ;) As an aside even with solid use, my ATrim handles stay tight. I guess we should be happy the various methods of assembly are available for our varying tastes. :D |
For folks who are more collectors than WMA practitioners or even "cutters" the hex nut assembly can be a turn off.
I have been collecting for years and have quite a few high-end production and custom swords and have almost never cut with any of them. Indeed, I have some pieces which I will likely never cut with at all as I couldn't imagine marring them. I am most interested in the handling and aesthetics, and for my collection I want pieces as close to historical pieces as possible.
I do agree that some high end production swords can look a bit "perfect" but representing period irregularities in a production setting would be really problematic.
If I were really interested in cutting targets and performance oriented swords then I would be totally fine with hex nuts or threaded tangs.
Ken Jay wrote: |
I too like the hex nut assembly and am a bit amused at the "it's not historical" flogging the hex nut design gets. Everybody seems to be happy with modern bar stock steels, CNC machining, castings, belt sanding,machine made symmetry, etc. for their "historical" reproduction swords. The hex nut is just too anti-historical for a reproduction? Really? I've been playing with hex-nut assembled swords for over tens years with no failures. Maybe I'm just easy to please and my toys don't need to be "perfect." |
To me, Atrim swords always represented the "modern" sword, new and improved. As opposed to the other end of the scale where ultimate historical accuracy is the goal, with many makers either compromising on looks and handling, others on materials and production methods.
Atrims incorporate the good things about modern sword making: reasonably affordable through use of CNC milling, good steels, good heat treatment and easy to disassemble for maintenance. The downside is that they don't always look like accurate reproductions of historical swords, but then again, there are more than enough makers to fill that niche.
Chad Arnow wrote: |
Failures or lack of failures, our ancestors didn't do it that way (apart from an odd mention or two in a fechtbuch or two). |
Gus' typologies and evolutions ;)
IIRC back in the Tinker Toy builds, the plain capscrew was getting sent out at times with a crosswise hole through it to employ a rod for tightening. Then most often just the plain smooth nuts which are on my two (only) Gus swords that have never really been an issue and both got some serious pounding in many hands for a few years. Once settled and seldom dismounted, they have not had a problem with coming undone if the threads have been respected. The smooth nuts almost a fail safe to help some from overdoing what should never see more than about ten ft pounds max of torque (less is sometimes more).
Page after page of feedback to Gus back then and most did ok with the smooth nuts. The advance of the allens really kind of cool but an immediate invitation to offer a pretty serious learning curve for the less mechanically inclined. Even a short l type allen wrench can go way over tight on those.
The peened over nut is something A&A has done for a long long time and a couple of quick pictures of my BP that came apart because the pommel wedged fit bottoms on the tang taper with some grip and guard slop (from the get go, must have been a Friday sword ;)) Of the compression fit type of fitment, I like the A&A method as it has what does look like a simple peen block but has adjustment. I'll attach another shot of a couple of different A&A that show the end result better.
As to decorative nuts that could look like a peen, there is some room for possibility there but I was probably mostly joking a decade ago when I said 'Gus, winged eagle nuts". In that vein, here is a decorative cap that very well may be a nut, as I don't have it in hand to look more closely. Ironically on an eagle ;)
Anyway, I like the square somewhat pyramidal peen blocks (threaded or not) but can appreciate the other looks. A real advantage to peen blocks (even when incorporated into 18th-19th century swords) will let a grip repair/refurb remain the same length with tang to spare. Once you trim a flush peened tang, it all gets shorter. Shave the block to gain more for the next peen.
My thoughts
GC
PS/off topic
Does anyone know whatever happened to Claudio and his sword pages/interests?
Attachment: 77.87 KB
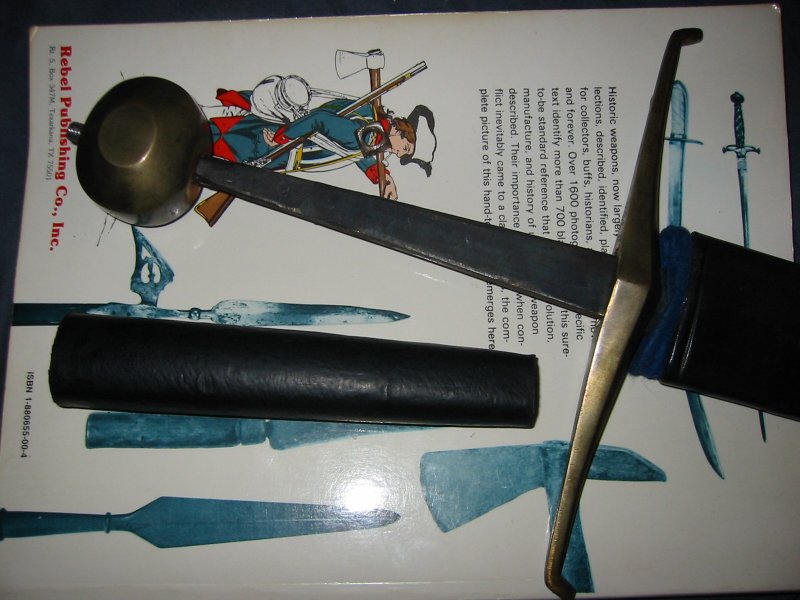
Attachment: 81.68 KB
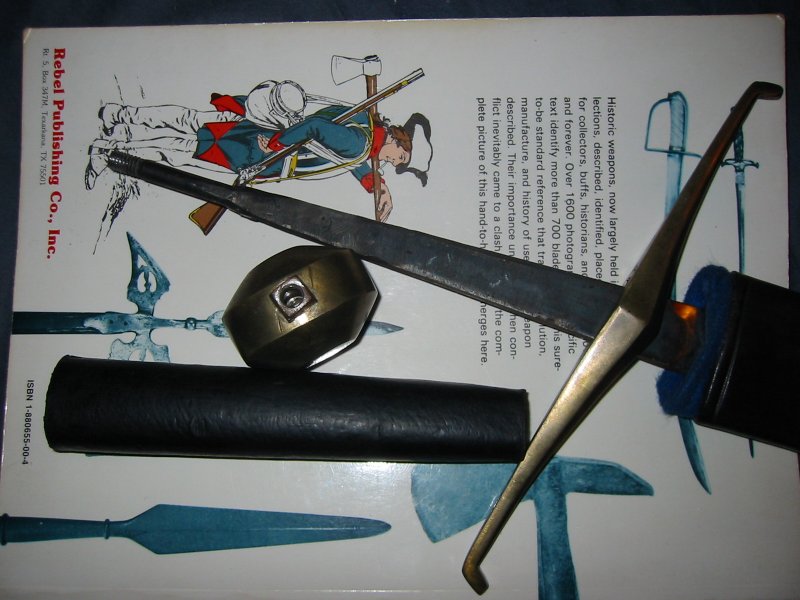
Attachment: 63.51 KB
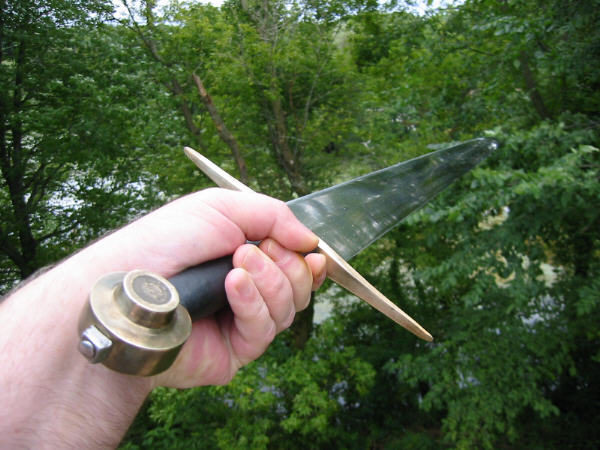
Attachment: 37.04 KB
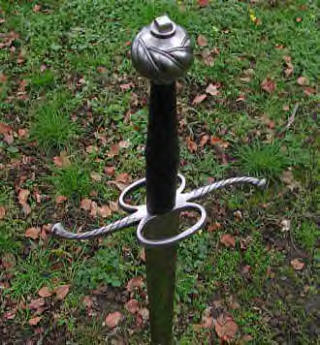
Attachment: 58.2 KB
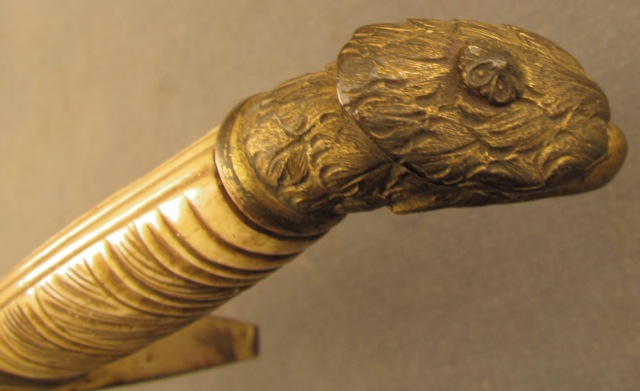
IIRC back in the Tinker Toy builds, the plain capscrew was getting sent out at times with a crosswise hole through it to employ a rod for tightening. Then most often just the plain smooth nuts which are on my two (only) Gus swords that have never really been an issue and both got some serious pounding in many hands for a few years. Once settled and seldom dismounted, they have not had a problem with coming undone if the threads have been respected. The smooth nuts almost a fail safe to help some from overdoing what should never see more than about ten ft pounds max of torque (less is sometimes more).
Page after page of feedback to Gus back then and most did ok with the smooth nuts. The advance of the allens really kind of cool but an immediate invitation to offer a pretty serious learning curve for the less mechanically inclined. Even a short l type allen wrench can go way over tight on those.
The peened over nut is something A&A has done for a long long time and a couple of quick pictures of my BP that came apart because the pommel wedged fit bottoms on the tang taper with some grip and guard slop (from the get go, must have been a Friday sword ;)) Of the compression fit type of fitment, I like the A&A method as it has what does look like a simple peen block but has adjustment. I'll attach another shot of a couple of different A&A that show the end result better.
As to decorative nuts that could look like a peen, there is some room for possibility there but I was probably mostly joking a decade ago when I said 'Gus, winged eagle nuts". In that vein, here is a decorative cap that very well may be a nut, as I don't have it in hand to look more closely. Ironically on an eagle ;)
Anyway, I like the square somewhat pyramidal peen blocks (threaded or not) but can appreciate the other looks. A real advantage to peen blocks (even when incorporated into 18th-19th century swords) will let a grip repair/refurb remain the same length with tang to spare. Once you trim a flush peened tang, it all gets shorter. Shave the block to gain more for the next peen.
My thoughts
GC
PS/off topic
Does anyone know whatever happened to Claudio and his sword pages/interests?

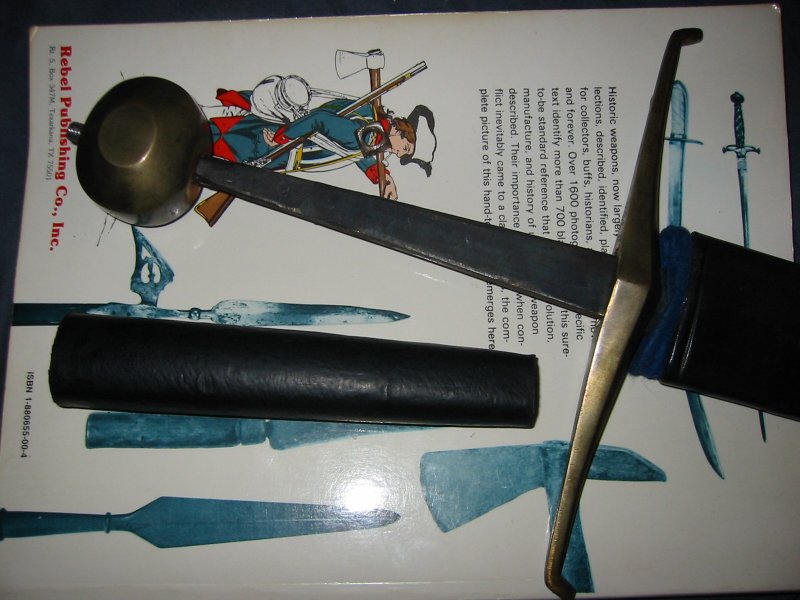

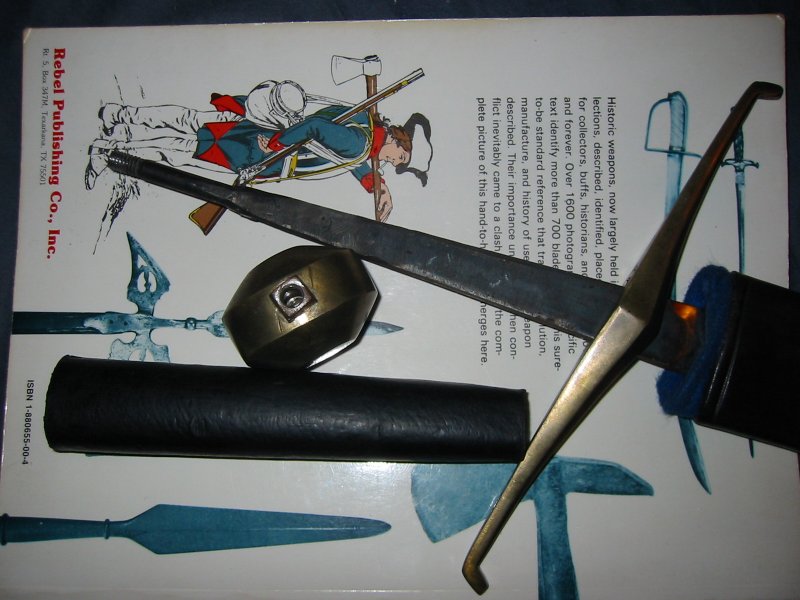

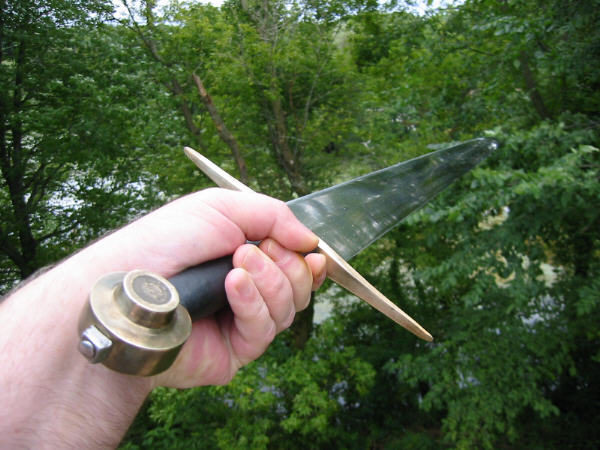

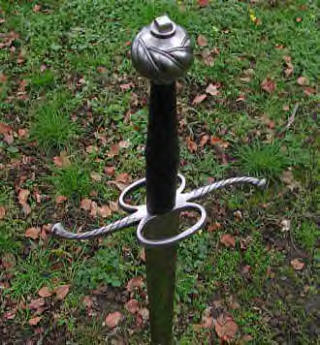

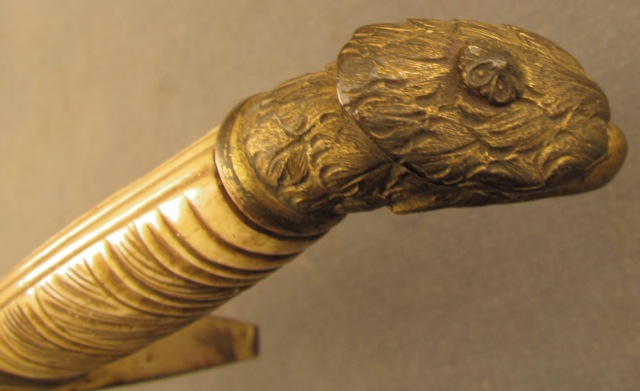
Paul Hansen wrote: |
Although, as you probably know, the threaded tang was employed from the 15th-16th C. onwards. Just not with a hex nut, which is technically superior, in my opinion. |
Please post pics of 15th century swords with threaded tangs. The bulk of Gus's lineup on the Tried and True Armory site predate 16th century styles, so my comments should be seen in light of what's common for 15th century and earlier swords.
Chad Arnow wrote: |
Please post pics of 15th century swords with threaded tangs. The bulk of Gus's lineup on the Tried and True Armory site predate 16th century styles, so my comments should be seen in light of what's common for 15th century and earlier swords. |
The sword I'm referring to is in the Real Armeria in Madrid. It was a transitional / early rapier of the late 15th / early 16th C. and was shown disassembled when I visited, I think in 2003 or so. The sword had a threaded tang and a screw-on pommel, like you find on a cheap wallhanger. Unfortunately, the Real Armeria did not allow pictures to be taken and the sword is not shown in the catalogue that I bought at the time. So I'm afraid I can't prove this observation...
But anyway I'm not defending the historical accuracy of Gus' hilt construction. :)
Page 2 of 2
You cannot post new topics in this forumYou cannot reply to topics in this forum
You cannot edit your posts in this forum
You cannot delete your posts in this forum
You cannot vote in polls in this forum
You cannot attach files in this forum
You can download files in this forum
All contents © Copyright 2003-2006 myArmoury.com All rights reserved
Discussion forums powered by phpBB © The phpBB Group
Switch to the Full-featured Version of the forum
Discussion forums powered by phpBB © The phpBB Group
Switch to the Full-featured Version of the forum