Straightening the Tang
Once the swords were disassembled, the next step was to straighten the tang on the Cutlass blade. I wrapped the
blade in a wet towel and put it in the vice. The wet towel was to cool the blade and keep it from over heating and loosing
its hardness. I had my son take a propane torch (he loves to play with fire) and heat the middle section of the tang until it
was a dull red. Meanwhile I took my handy-dandy claw-hammer and tapped gently on the tang until it was straight.
Blade Shaping
I also wanted to reshape the blade a little. It seemed a little too wide at the Cop and needed a little more
distal taper. I
also wanted to soften the wedge-shaped cross section. I have a large belt sander I use for woodworking but the belt and
motor is for woodworking and does not work well on metal. So I clamped the blade to a plywood workbench and tried to
shape it with my angle grinder. Every few passes I would wet the blade to keep it cool, although I think I got the tip a little
too hot. You have to be very careful near the tip and edges. These areas can heat up really quickly. I was really careful at
first so that I did not ruin the blade. Eventually I got a little to careless and cut too deep near the edge. So I took my
bastard mill file and reshaped the edge. It really didn’t matter because I was planning on narrowing the blade at the Cop.
But it was a good lesson in how quickly you can gouge a blade while holding a heavy angle grinder. So I put the angle
grinder in my vice and held the blade against the grinding disc, taking very light passes, always keeping the tip and edge
pointed away. After several passes I would wet the blade to keep it cool and use the calipers to keep track of how much
material was being removed. Once the shape of the blade was close to where I wanted it, I used the bastard mill file
to remove most of the grinding marks.
Basket Shaping
I like the Cold Steel basket. It was a little oversized but not too much so. Also the forward guards (loops at the front of the
basket) were too wide. They were out of proportion with the bars of the basket. So I did a little cosmetic surgery. I took a
permanent marker and drew lines on the forward guards to get an idea of the shape and width I wanted. Then I took a
stone grinding wheel on my dremel tool and began to grind away the excess. I ground the forward guard down to a more
proportionate (and a little more period) size. Using the course sanding drum on the dremel, I shaped them and rounded
the edges, then polished it with medium sand paper.
Blade Aging
I put fingernail polish over the threads of the tang to keep them from rusting, covered the rest with vinegar and rock salt
and buried it in the backyard. I let it set for a week or so. When it was removed there were many shallow pits. As I
finished the blade with coarse sand paper most of the pits were removed but a few remain to give the blade a little
character.
Basket Aging
The Basket had a nice gun bluing on the surface. If you have seen my other projects, you know I like the brown look. So I
covered the basket with etchant (ferric chloride) and just let it rust for about a week. This worked to remove the blue and
give the basket very shallow pits. The pits would remain in the hard to get places and would be polished out on the outer
parts of the basket giving a nice contrast in texture.
Basket Browning
I covered the rusted basket in oil and let it set a day. Then I took fine sand paper and polished the outer and inner
surfaces of the basket until it was smooth taking out the rust pits. I then used cold browning solution to get a nice even
brown. Then steelwool was used to lighten the middle areas of the wider components of the basket bars and
shields.
Then another layer of browning solution, then lightened the center more with steel wool or very fine sand paper, then
another layer of brown… repeating until I achieved the contrast in the tone of the browning.
Engravings
I noticed that the bottom plate (main knuckle guard) and the front plate (“quillon block”) were rather plain and
undecorated compared to the other parts of the basket. It was at this point that my love for all things Celtic came into
play. (I’m half Scotch Irish. My granddad was a Duncan). I decided to do a little engraving in the plain areas. I had seen Scottish baskethilts with thistle, crowns and regimental numbers and the initials of the maker. So I took a thin permanent marker
and drew two thistles one large and one small on the main knuckle guard at the bottom of the basket. I gave them each vine
like roots that reached toward the other. On the quillon block I drew a crown similar to one I had seen on
the blade of an original. I also drew the number 45 under the crown. In my mind it stood for the desire and action taken
for Scottish liberty in 1745. Or it could simple be a regiment number. Below the blade on the quillon block I drew the
initials KS. Not sure why… just liked the look of it J. With the tip of a diamond bur on my dremel, I engraved along the lines
I had drawn. For the straight lines of the numbers and letters I took a steel 6 inch ruler and clamped it along the
straight sections of the letters and numbers I had drawn. I used it as a guide for the dremel tool. (I didn’t trust my ability
to freehand a straight line.) It worked really well. Using fine sandpaper I polished these areas again and used the layers
of cold browning as described earlier to recreate the light to dark tones in these areas.
ks
Attachment: 96.05 KB
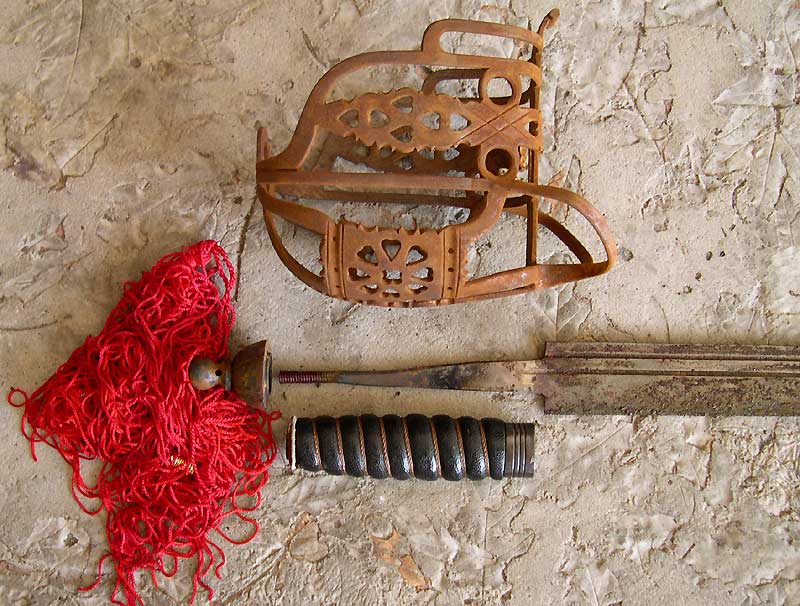
Rusted Basket and Blade Showing Straightened Tang
Attachment: 98.35 KB
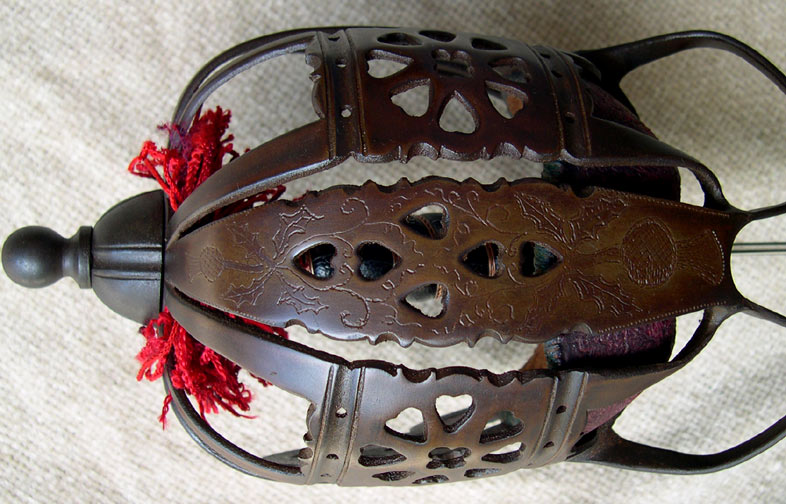
Main Knuckle Guard with Thistle Engraving
Attachment: 97.53 KB
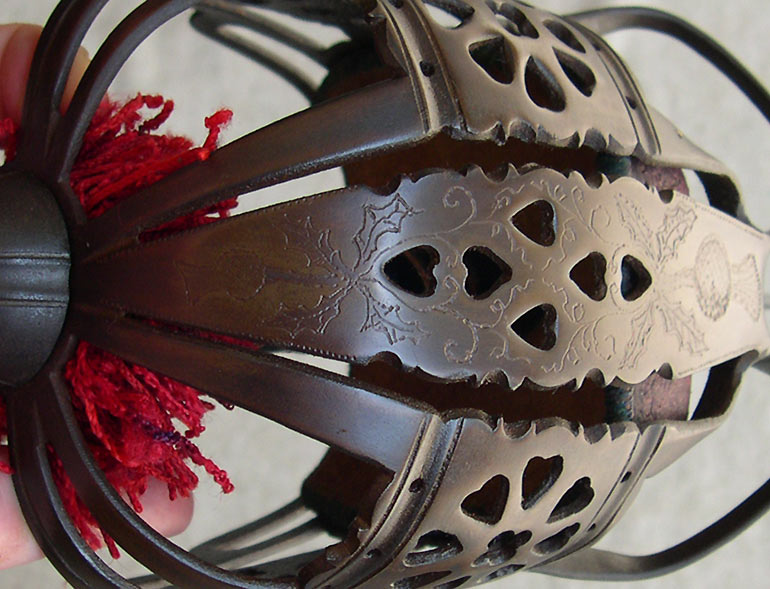
Close-Up of Thistle Engraving on Main Knuckle Guard