I have been working on a shirt of chainmaille for about 4 months now, the linking is the easy part I'm just having trouble with the cutting of links. I've been using aviation snips to cut the wire, but these have proven ineffective, the blades separating and the wire getting wedged in between them.
I'm thinking about buying some bolt cutters and then machining them down so they can fit into the coils, I'm not sure if this is the best way to go. Does anyone else have any suggestions?
The wire is about this thick ( made of coat hangers)
||
||
||
||
||
||
||
||
Hey C. My experience with aviation (sheet metal) snips is that they can be tightened to where they will cut the wire and not separate. The Maille Artisan's International League ( M.A.I.L.) is easily found on the net and they are free to join. They have many articles that deal with tools for making chain links as well as all other aspects of this craft.
Hope this helps,W
Hope this helps,W
I've tightened my snips but its the steel that bends. Thanks for the site though.
P.S. The wire thickness is about 1/16" thick
P.S. The wire thickness is about 1/16" thick
http://theringlord.com/cart/shopdisplayproduc...re+Cutters
The first ones on the list are what I used to make my mail shirt. They burned through 14 ga. steel with no difficulty. As for that, I'd recommend getting coils of steel from a hardware store. It might be easier than using coat hangers. Good luck! Making a mail shirt is a rough and time consuming hobby. If you have any other questions don't hesitate to ask. There are a number of people here who have undertaken similar projects. You may also want to search past forum posts. There were a number of posts on that subject only a few months ago.
The first ones on the list are what I used to make my mail shirt. They burned through 14 ga. steel with no difficulty. As for that, I'd recommend getting coils of steel from a hardware store. It might be easier than using coat hangers. Good luck! Making a mail shirt is a rough and time consuming hobby. If you have any other questions don't hesitate to ask. There are a number of people here who have undertaken similar projects. You may also want to search past forum posts. There were a number of posts on that subject only a few months ago.
The fastest and least authentic method is to cut a line down one side of the coiled wire with a separating or abrasive cut-off disc on a dremel or grinder. This gives you nice square ends on your links, too. For wire of 1/16th inch, I think you'll like it, bolt cutters would be slow & awkward compared to zipping them off.
If you go with that, be sure you don't use a disk that's too thick, otherwise your rings will not be shaped properly when you close them.
Jeff Pringle wrote: |
The fastest and least authentic method is to cut a line down one side of the coiled wire with a separating or abrasive cut-off disc on a dremel or grinder. This gives you nice square ends on your links, too. For wire of 1/16th inch, I think you'll like it, bolt cutters would be slow & awkward compared to zipping them off. |
The problem with using a Dremel is that it is horribly inefficient. I tried that despite being warned by a all the mail forums. Unless you use a diamond cutting wheel (very expensive) you will have to change the cutting disc every ten rings or so. It does give you very nice cuts though but the time factor and the frustration go way up. I'm told that even if you use a diamond cutting disc they must still be changed far too frequently.
Then there is the problem of heat generation. A dremel generates a lot of heat as it cuts. If you are cutting galvanized wire, tis heat will generate toxic fumes from the wire. So if you decide to go this route, please be careful and do it in a well ventilated area.
Overall, the best way to cut that I have found so far is using a good (high quality) pair of aviation snips.
I too had many problems very I first began to cut my links with aviation snips. I found that the cut rings were very distorted and the act of cutting them caused serious pain in my hand and forearm. After one extremely painful experience I got angry and slammed down my snips breaking them. I was forced to go the the local hardware store to buy new ones. This time however, I decided to buy the best I could find, since initially I went with a cheaper pair and ended up getting a name brand pair. I immediately noticed a difference. The good pair of snips cut clean and easy as long as I don't try to cut too many rings at once, about 2 -3 rings. I also learned to stretch out my coil slightly before i cut as this will lessen the distortion in the final rings.
Chris Lee
Aurora Ontario
Canada
Using hand tools, one of the best ways I've heard of for cutting links is with a jeweler's saw - set up a jig and you'll be able to cut multiple links at a time. Advantages: relatively fast, quiet compared to power tools, cheap, and you get a good square end on the cut for making very tight butted links. Another trick I've heard about using the same tool is to make the cut intentionally at an angle - the complimentary angles of the cut ends of each link butt together very nicely.
Check out www.armourarchive.org and do a search on "mail" or "maille" and the first few pages should get you in good shape.
Good luck and have fun :)
Check out www.armourarchive.org and do a search on "mail" or "maille" and the first few pages should get you in good shape.
Good luck and have fun :)
Quote: |
The problem with using a Dremel is that it is horribly inefficient. |
Ah, yes - If you are going to use this method, be sure to secure your coil, do not allow the tool bit to deviate in direction or plane as you make the cut, wear safety glasses, don't get your hands anywhere near the 'line of fire' without protection, dust mask for the dust, respirator if you are moving slow enough to generate so much heat that you volitize the zinc if you are using galvanized wire... :wtf:
You are right, Chris, that it can be a difficult method to get to work efficiently. And motorized tools are unplesant - I'll change my advice to suggest using a well-sharpened chisel, on 1/16th wire with good support, you could knock off the links one or two per hammer blow. And, it's what they did back in the day!
Jeff
If you have access to a drill press, the easiest, most efficient, and inexpensive way I found was to make a saw and chute for this. I posted the details here:
Cutting rings for butted maille
Piece of cake... cleanly cuts about 100 rings a minute.
If you don't have the tool, it isn't cost-effective to buy it just for this purpose, but I won't ever cut another ring by hand.
Cutting rings for butted maille
Piece of cake... cleanly cuts about 100 rings a minute.
If you don't have the tool, it isn't cost-effective to buy it just for this purpose, but I won't ever cut another ring by hand.
Thanks for the tips guys, but I just received some new high-carbon steel snips and a 3lb club hammer. When I strike the handle with the hammer it snaps off up to 3 rings at a time. It may be a bit slow, it may not be high tech but at least its working. :p
That's a pretty cool gizmo, Aaron..
Jesse Frank wrote: |
That's a pretty cool gizmo, Aaron.. |
Thanks, Jesse! It's amazing how hard a man can think and work towards an end of laziness. With it, though, we were able to coil up 1/2 mile of wire and cut it in an afternoon - and that's with a half-case of Bass in the mix, and taking a break here and there. Probably saved me well over 100 hours. It will come in handy for my last remaining butted maille project...
What someone needs to design is a machine for making and knitting rivetted maille :p
C. Stackhouse wrote: |
What someone needs to design is a machine for making and knitting rivetted maille :p |
While not riveted, there are machines which produce welded maille, for use in shark suits, butcher's gloves, auto convertible roof liners, and fashionwear/jewelry. Whiting & Davis is the most well known, although I believe Niroflex is also in the business. Last I had heard W&D were the only ones in the world who owned the patented machines for making the mesh, though if things have changed since I cannot say.
The attached image is a scan from a sample of Whiting &Davis maille I have, just to give you an idea of how tight this stuff is - it feels very much like fabric.
The "Machine for Making Link Mesh", patented Feb. 8, 1910 by A.C. Pratt (PN 948,615):
http://tinyurl.com/8jsok (or, if that doesn't work for you: http://mailleartisans.org/gallery/pics/5439pat.gif )
And something else which may be of interest is the RasterMesh G16-T, otherwise known as "The Turtle":
http://66.78.4.141/~selwyn/rm-work1.htm
As far as cutting rings goes, I've found the best way to get a clean edge quickly is to shear the rings, rather than cut completely through. I prefer to use end cutter pliers, which I then use 90 degrees to the coil, so actually, the side - much more comfortable than end-on with conventional cutters. I just squeeze enough to nick the ring, then grab then opposite side (again, with the cutters) and twist it off. They pop off cleanly, leaving a flush, flat edge, and it's actually quite fast.
Once you've done enough you don't even need to look at the coil anymore. :)

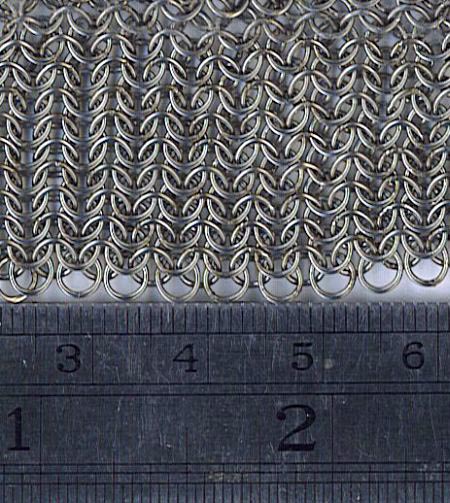
Aaron I wish you had come up with that out sooner! It would have saved me lots of time! :D
That is about the smartest low-tech thing I have seen in awhile! Much better than what I did below!
What I did to cut the rings was to place one handle of my small bolt cutters in a vise. Then tie a bungee cord to the top handle and connect it with the roof of my shop (low ceiling) I did that so it would open back up automatically. I then attached a rope to that same handle. I put a loop in the dangling end for my foot and left just enough space between my looped foot and the floor for the downward motion to close the bolt cutters. Worked great! No sore hands and it left my hands free to correctly align the coil for 45 degree cuts. I could cut pounds of rings in a fairly short time.
That is about the smartest low-tech thing I have seen in awhile! Much better than what I did below!
What I did to cut the rings was to place one handle of my small bolt cutters in a vise. Then tie a bungee cord to the top handle and connect it with the roof of my shop (low ceiling) I did that so it would open back up automatically. I then attached a rope to that same handle. I put a loop in the dangling end for my foot and left just enough space between my looped foot and the floor for the downward motion to close the bolt cutters. Worked great! No sore hands and it left my hands free to correctly align the coil for 45 degree cuts. I could cut pounds of rings in a fairly short time.
Shaun Swanner wrote: |
Aaron I wish you had come up with that out sooner! It would have saved me lots of time! :D
That is about the smartest low-tech thing I have seen in awhile! Much better than what I did below! |
Your solution was pretty good, too, for someone who doesn't have a drill press and vise.
Figured I would throw in my method(s) as well. I've been making maille for a number of years now, more as a hobby then anything else. I started out with a set of aviation snips but just never seemed to have much luck with them. From there I moved up to a set of bolt cutters that have worked well for several years. Like a few others mentioned you can make a pretty effecient setup with a table vise or by screwing one handle to a table. Slide a bar over the other handle for some added leverage and you can cut several rings at a time.
I had tried using the Dremel cut-off wheels but either burnt through a lot of wheels or removed too much material when cutting. So at a friend's suggestion he pointed me to another site where I found a picture and some information about a tool someone had created to cut rings. A Friday night of drafting and a Saturday afternoon of construction yielded me this nice jig.
The blade is a HSS Jewelers that are real cheap to pick up and replace. Currently I just wax the blade between cuts, but I'm working on (and almost finished) a slow oil-drip to keep the blade lubricated. The little basin underneath can be swapped out for a piece of angle aluminum that acts like a chute and leads off to a 5 gallon paint pail for when I'm cutting a lot of rings.
Credit for the design certainly goes to the original inventor.
~Dominic
Attachment: 23.39 KB
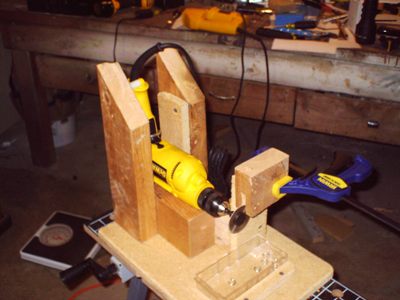
Overall picture of the jig. You can see that the block is held on by a clamp. I have blocks cut for various diamters and gauges of wire and just swap them out depending on what I'm cutting.
Attachment: 22.13 KB

Front view. The block here is for 14ga 5/16" diameter rings. You can see a clamp on the trigger which means the drill is always on. I have a control switch mounted on the back that turns the whole unit on and off. Avoids me having to reach my hand in
Attachment: 21.45 KB
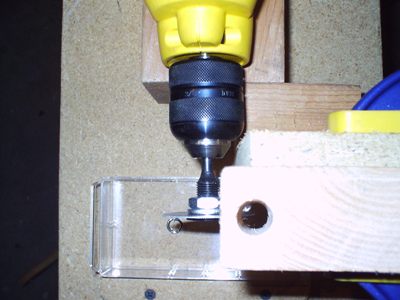
Top down view with the catch basin below. Have to make sure that the blade comes in far enough to cut fully through the ring but not the other side
I had tried using the Dremel cut-off wheels but either burnt through a lot of wheels or removed too much material when cutting. So at a friend's suggestion he pointed me to another site where I found a picture and some information about a tool someone had created to cut rings. A Friday night of drafting and a Saturday afternoon of construction yielded me this nice jig.
The blade is a HSS Jewelers that are real cheap to pick up and replace. Currently I just wax the blade between cuts, but I'm working on (and almost finished) a slow oil-drip to keep the blade lubricated. The little basin underneath can be swapped out for a piece of angle aluminum that acts like a chute and leads off to a 5 gallon paint pail for when I'm cutting a lot of rings.
Credit for the design certainly goes to the original inventor.
~Dominic

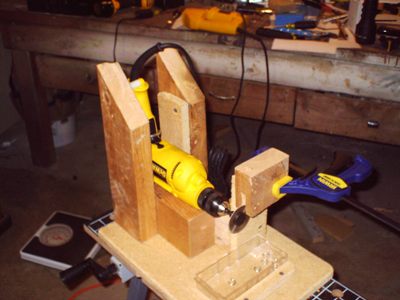
Overall picture of the jig. You can see that the block is held on by a clamp. I have blocks cut for various diamters and gauges of wire and just swap them out depending on what I'm cutting.


Front view. The block here is for 14ga 5/16" diameter rings. You can see a clamp on the trigger which means the drill is always on. I have a control switch mounted on the back that turns the whole unit on and off. Avoids me having to reach my hand in

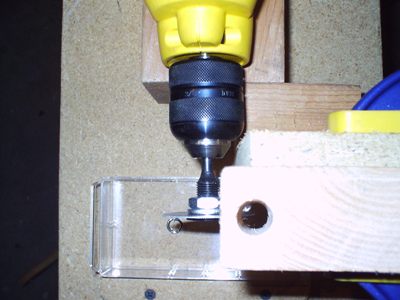
Top down view with the catch basin below. Have to make sure that the blade comes in far enough to cut fully through the ring but not the other side
an easy, safe and quiet way is to get 8 inch spring loaded bolt cutters. they have red handles and are usually black or silver in color. makes cutting coils easy :) might cost 10 bucks from lowes or walmart
My method is extremely low tech. When I was 15, that was because I had no money. After I started getting money, I found that I enjoyed the Zen simplicity of making mail with a minimum of tools.
I use a regular metal rod of the desired inside diameter with one third of the length bent so it forms an L. They're about $1.00 apiece in any hardware store. A hole is drilled on the longer segment, about ten inches from the end. The wire goes in the hole, I brace the end of the rod on the floor with my leg and I turn it using the shorter L segment as a crank handle with my left hand guiding the wire. With good bolt cutters, I can coil and cut a 100' roll of 14 ga. wire in about two hours.
There's something almost meditative about the work when there are no power tools, but I'm certain it takes longer that way.
I use a regular metal rod of the desired inside diameter with one third of the length bent so it forms an L. They're about $1.00 apiece in any hardware store. A hole is drilled on the longer segment, about ten inches from the end. The wire goes in the hole, I brace the end of the rod on the floor with my leg and I turn it using the shorter L segment as a crank handle with my left hand guiding the wire. With good bolt cutters, I can coil and cut a 100' roll of 14 ga. wire in about two hours.
There's something almost meditative about the work when there are no power tools, but I'm certain it takes longer that way.
Page 1 of 2
You cannot post new topics in this forumYou cannot reply to topics in this forum
You cannot edit your posts in this forum
You cannot delete your posts in this forum
You cannot vote in polls in this forum
You cannot attach files in this forum
You can download files in this forum
All contents © Copyright 2003-2006 myArmoury.com All rights reserved
Discussion forums powered by phpBB © The phpBB Group
Switch to the Full-featured Version of the forum
Discussion forums powered by phpBB © The phpBB Group
Switch to the Full-featured Version of the forum