1743 is the date Sheffield plating was invented. Electroplating comes in in 1838. How was silver plating of copper, brass, and steel done before that?
Was gilding of metal all via mercury and heat?
Was mercury used in silver plating? It was used in making silvered mirrors.
How common was hot-dipping metal items into molten silver?
Goldsmith, in The Vicar of Wakefield, mentions cheap silver coating on eyeglasses. What would that have been?
I've also seen reference to silver wash, including early coins. How was that done?
Inquiring minds want to know!
Thanks in advance.
Quote: |
Was gilding of metal all via mercury and heat? |
At least for armour this is the only way I know of.
Thanks, Peter.
I left this query relatively broad to be of general interest to the readers. However, my particular focus is on the Scottish Highland targe in the Metropolitan Museum in New York.
The description says nothing about silver plating, but the visual evidence is clear:
[ Linked Image ]
Attachment: 56.15 KB
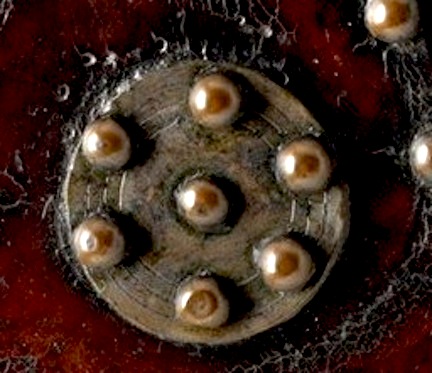
Attachment: 247.04 KB
[ Download ]
I left this query relatively broad to be of general interest to the readers. However, my particular focus is on the Scottish Highland targe in the Metropolitan Museum in New York.
The description says nothing about silver plating, but the visual evidence is clear:
[ Linked Image ]

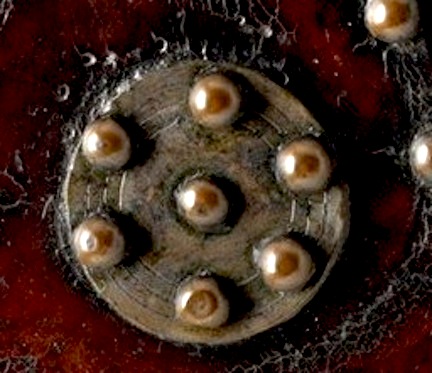

[ Download ]
G'day Richard,
I'm not an expert on this subject, but you can plate objects using acid. Such techniques well pre-date electroplating and are still used in jewelry-making today.
I came across this when mixing vinegar, iron oxide (a rusty tool) and a brass component of that tool in a bucket. The brass component took on a uniform copper appearance and it was reasonably thick. A bit of sanding took it back to brass. Of course brass is an alloy of copper.
Now I don't understand this chemical process, but others here may. Perhaps you can silver plate metals with a similar process? Hope that's useful!
Cheers.
I'm not an expert on this subject, but you can plate objects using acid. Such techniques well pre-date electroplating and are still used in jewelry-making today.
I came across this when mixing vinegar, iron oxide (a rusty tool) and a brass component of that tool in a bucket. The brass component took on a uniform copper appearance and it was reasonably thick. A bit of sanding took it back to brass. Of course brass is an alloy of copper.
Now I don't understand this chemical process, but others here may. Perhaps you can silver plate metals with a similar process? Hope that's useful!
Cheers.
Now that I look at the buckler I believe that this is not plated as you think. My guess is that the rivets and decorative plates, which now have a yellowish shine and are made of brass, as the MET says, once were tinned with a high percentage of silver. You make all the brass applications, drill the holes, create the necessary depressions, mount everything for a try, when it fits you tin all the pieces and rivet them onto the shield. That 's how I would do it. Are you certain that the white you can see on the pictures is silver?
Thanks for the replies.
After doing a bit of reading, yes, acid treatment of alloys was used by the Romans. Coin blanks with low silver content were treated in an acid bath, which removed the copper, etc. from the surface. When struck in the coin dies, the rough silver surface became a nice uniform silver colour. With wear, though, the alloy beneath showed through.
With your brass piece, the acid removed the zinc from the surface layer.
I had not considered tin or a silver-tin alloy. I think this would have to have been via a "hot dip" process. In my limited experience, this produces a thicker layer than that seen on the Met shield. But my experience is with tableware, which may purposely have a very thick coating.
After doing a bit of reading, yes, acid treatment of alloys was used by the Romans. Coin blanks with low silver content were treated in an acid bath, which removed the copper, etc. from the surface. When struck in the coin dies, the rough silver surface became a nice uniform silver colour. With wear, though, the alloy beneath showed through.
With your brass piece, the acid removed the zinc from the surface layer.
I had not considered tin or a silver-tin alloy. I think this would have to have been via a "hot dip" process. In my limited experience, this produces a thicker layer than that seen on the Met shield. But my experience is with tableware, which may purposely have a very thick coating.
There is a method for silver that is basically potato juice and powdered silver. Commercially there are a few products and one is called Silver Secret.. I have used it for various projects. The process has been around (as far as I know) way, way, back. It is the oxalic acid that etches and adds the silver in a deposition manner.
Fire gilding gold way old as well. Electroplating suggested before Roman Empire days.
Here is an example I used on an 1800 period sword hilt to add silver. The Silver Secret product needs to be rubbed in with a fair amount of determination and persistence for doing more than just touching up flatware. I basically kept adding from a small dose cup and rubbing with cotton swabs.
Cheers GC
Attachment: 50.66 KB
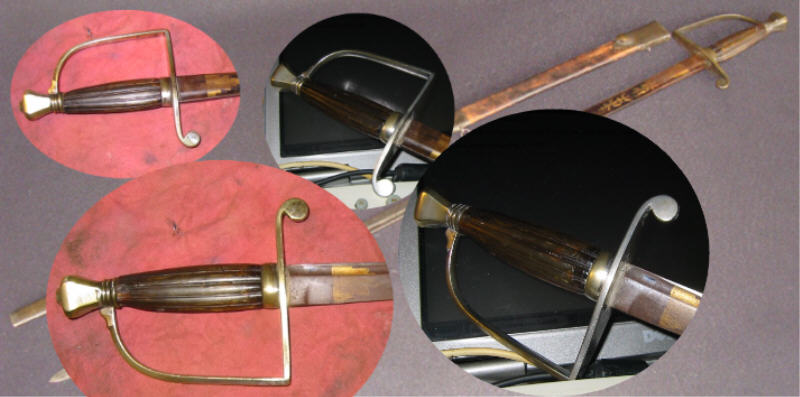
Fire gilding gold way old as well. Electroplating suggested before Roman Empire days.
Here is an example I used on an 1800 period sword hilt to add silver. The Silver Secret product needs to be rubbed in with a fair amount of determination and persistence for doing more than just touching up flatware. I basically kept adding from a small dose cup and rubbing with cotton swabs.
Cheers GC

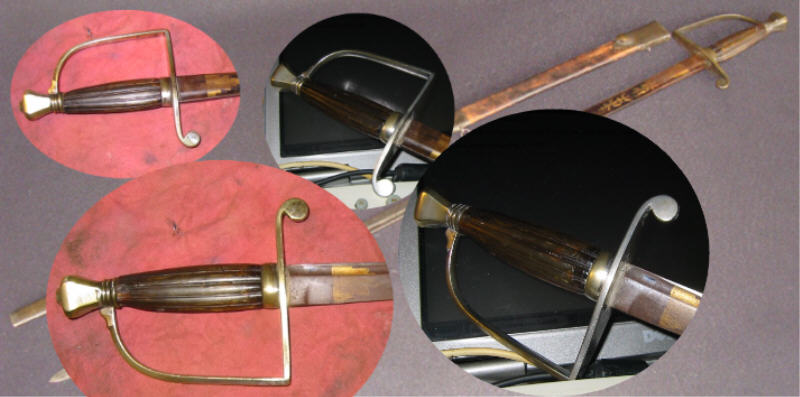
Hmm... there's obviously more to this than the standard history:
nothing, then Sheffield Plate, 1743, and Electroplate, 1838. The End
Unfortunately, most of the "how to" books were published after 1743. But I'll keep digging, and post anything worthwhile.
nothing, then Sheffield Plate, 1743, and Electroplate, 1838. The End
Unfortunately, most of the "how to" books were published after 1743. But I'll keep digging, and post anything worthwhile.
Just wild guessing, but perhaps what appears to be silver plating is in fact oil gilding and not mercury gilding? While I would assume mercury gilding would be harder wearing, perhaps oil gilding can be sealed onto the item using a lacquer or wax?
Aside from gilding techniques, perhaps pigments were created using ground gold/silver and a carrier, such as tallow, tar or beeswax? Etching the surface you apply such a thing to may increase its durability.
You might look into ochre, which the Greeks and countless indigenous peoples have used for millennia. The colours are very rich. Perhaps there are techniques for a metallic appearance there?
Cheers!
Aside from gilding techniques, perhaps pigments were created using ground gold/silver and a carrier, such as tallow, tar or beeswax? Etching the surface you apply such a thing to may increase its durability.
You might look into ochre, which the Greeks and countless indigenous peoples have used for millennia. The colours are very rich. Perhaps there are techniques for a metallic appearance there?
Cheers!
did you ask the MET already what they think about the silvered parts?
Brass caps on steel rivets for armour are connected via tinning. You punch a depression into a piece of brass, roughly cut around it, add a mixture of tin and a flux to the inside of the brass cap, place the rivet into the brass cap, the flux + tin in-between and heat it up. The tin gets liquid, cools down again and the cap holds onto the rivet. The layer produced is not very thick. As for hot dipping, I know from riding equipment which was tinned that the tin on the mouth pieces wore off at some point. I believe that the coat was not very thick as a thick tin layer is quite hard to remove. At least with a tongue and a bit of spit...
Brass caps on steel rivets for armour are connected via tinning. You punch a depression into a piece of brass, roughly cut around it, add a mixture of tin and a flux to the inside of the brass cap, place the rivet into the brass cap, the flux + tin in-between and heat it up. The tin gets liquid, cools down again and the cap holds onto the rivet. The layer produced is not very thick. As for hot dipping, I know from riding equipment which was tinned that the tin on the mouth pieces wore off at some point. I believe that the coat was not very thick as a thick tin layer is quite hard to remove. At least with a tongue and a bit of spit...
I've looked all over the Met's website for curatorial contact information, but couldn't find any.
Some museums get back to you right away, and others can't be bothered. :\
Some museums get back to you right away, and others can't be bothered. :\
Most targe nails, 1623-1745, were cast, but some are clearly domes of thin brass sheet. They are easily damaged.
Page 1 of 1
You cannot post new topics in this forumYou cannot reply to topics in this forum
You cannot edit your posts in this forum
You cannot delete your posts in this forum
You cannot vote in polls in this forum
You cannot attach files in this forum
You can download files in this forum
All contents © Copyright 2003-2006 myArmoury.com All rights reserved
Discussion forums powered by phpBB © The phpBB Group
Switch to the Full-featured Version of the forum
Discussion forums powered by phpBB © The phpBB Group
Switch to the Full-featured Version of the forum