
Looks like I'm back on track thx to fieblings acrylic paints. Now I don't have the rich depth of leather dye, but it still looks pretty nice and provides the contrast I was after. Now It needs to hold and not peel away, I'm a little worried by that...time will tell. I'll apply some leather protective balm. I need no hardening of the leather. This little rain guard as soaked so much stuff that it is stiff as cardboard. Now that I'm out of trouble, I'm thinking of creating some more - I was thinking of painting the background of the grip red too...but on the grip the acrylic paint probably won't survive repeated handling. I need to make some tests. In the meantime I will decorate the overlap with a few stamps and lines, and glue it on the handle.

Last edited by Julien M on Wed 12 Oct, 2016 6:39 am; edited 1 time in total
I thought it looked great before, but it really is stunning now!
For leather, oil paints work really well. If you really want to go out on a ledge with it, you can mix your own from period correct pigments. For leather I can recommend various ochre/earth pigments. Just mix with linseed oil. Once its dry it should last much better than acrylics, since the oil interacts really well with the leather.
Thx for the suggestion Bjorn, I'll look into that at some point, just as I will try historic ways to dye the leather...as time allows.
The grip is now fully glued together with the rain guard, with light tooling on the grip overlap. I've applied generous amount of beeswax on it and let it dry for days before buffing. It really creates a nice finish.
I also made a scabbard core for it, as I needed an excuse to try the slats method vs carving method. This one is made from reclaimed wood (from a broken fence panel!), soaked for a couple of hours in hot water, then clamped onto the blade...for 5 days (it took ages to dry, I set it up on a radiator to speed things up in the end). Today I glued it together, fiddling around to make sure the fit was correct. I reopened one side before the glue was fully cured, as inserting/drawing out the blade was too hard. That way, I loosen the fit and it's perfect now.
Another way would be to wrap around with linen soaked in glue, in fact i will wrap it with that to strengthen it further.
I'm 100% sold on that technique. getting a core with such a tight fit and that thin from carving is way more labor intensive...and this can be done with minimal mess, on the side of a kitchen sink. No proper lighting so can't shoot the sword in the scabbard in full length properly...next time.
The grip is now fully glued together with the rain guard, with light tooling on the grip overlap. I've applied generous amount of beeswax on it and let it dry for days before buffing. It really creates a nice finish.
I also made a scabbard core for it, as I needed an excuse to try the slats method vs carving method. This one is made from reclaimed wood (from a broken fence panel!), soaked for a couple of hours in hot water, then clamped onto the blade...for 5 days (it took ages to dry, I set it up on a radiator to speed things up in the end). Today I glued it together, fiddling around to make sure the fit was correct. I reopened one side before the glue was fully cured, as inserting/drawing out the blade was too hard. That way, I loosen the fit and it's perfect now.
Another way would be to wrap around with linen soaked in glue, in fact i will wrap it with that to strengthen it further.
I'm 100% sold on that technique. getting a core with such a tight fit and that thin from carving is way more labor intensive...and this can be done with minimal mess, on the side of a kitchen sink. No proper lighting so can't shoot the sword in the scabbard in full length properly...next time.
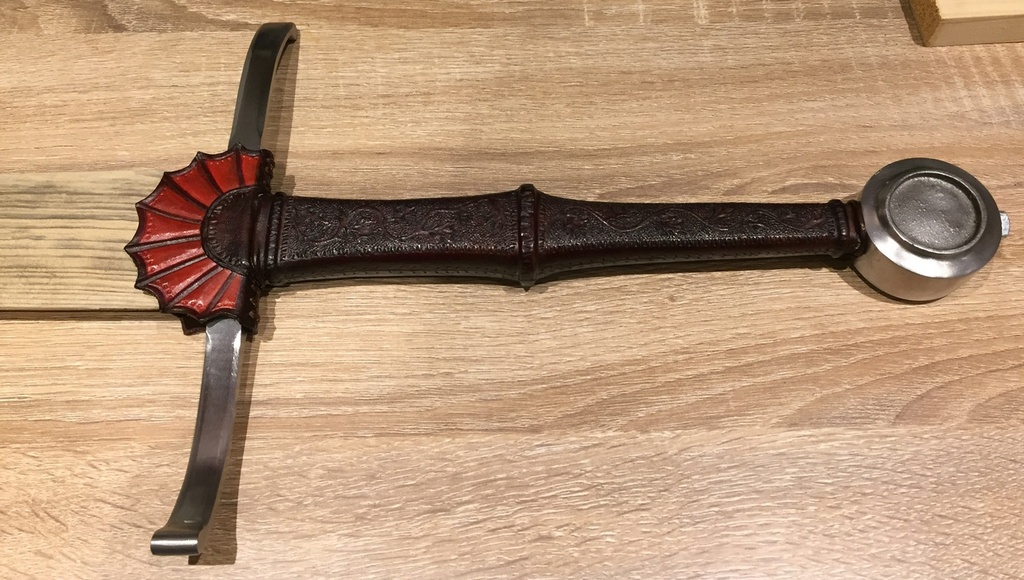


That looks fantastic! You could just put the finished hilt on a shelf and be proud of that.
Wow, with a hilt like that you should consider becoming a proffesional leatherworker ;)
No seriously, it's gorgerous
No seriously, it's gorgerous
That hilt turned out very nicely!
Very nice Julien! The coloring and tooling on the leatherwork is gorgeous. I'm also excited to hear about your scabbard method. Do you mind to share the thickness and type of wood you used? Also, did you do any cutting to match the blade taper before soaking?
Julien, I was following this this work and the result is really astonishing. Can´t wait for the scabbard. Construction of the core looks like a good idea, I have to try it soon - some swords are still waiting on the shelve.
When you say "Another way would be to wrap around with linen soaked in glue, in fact i will wrap it with that to strengthen it further" do you mean:
- 1) soaking 2 thin slats in hot water, 2) pressing them to blade & wrapping them in glue-soaked linen, 3) letting it dry;
- or do you mean the same method, without soaking the slats in hot water (presuming they are thin & flexible enough to go around the blade, without cracking), an the result would keep the shape thanks to the dried glue-soaked linen
- or do you mean that you would wrap the blade directly, let it dry, and then sand the core etc. (let´s call it "a pre-modern fiber-glass:))
Sorry for this industrial espionage, but it really sounds like an interesting method & I´ll definitely try it.
When you say "Another way would be to wrap around with linen soaked in glue, in fact i will wrap it with that to strengthen it further" do you mean:
- 1) soaking 2 thin slats in hot water, 2) pressing them to blade & wrapping them in glue-soaked linen, 3) letting it dry;
- or do you mean the same method, without soaking the slats in hot water (presuming they are thin & flexible enough to go around the blade, without cracking), an the result would keep the shape thanks to the dried glue-soaked linen
- or do you mean that you would wrap the blade directly, let it dry, and then sand the core etc. (let´s call it "a pre-modern fiber-glass:))
Sorry for this industrial espionage, but it really sounds like an interesting method & I´ll definitely try it.
Thanks for your kind words guys! Much appreciated.
The wood should be between 1mm to 3mm. The slats I have are approx 3mm thick. These are cut before soaking.
Hey Radovan - nothing wrong with asking, I do that a lot too!
Slats are mostly formed on the blade (cut to size, soak, clamp, dry). The steaming/soaking is always the core principle here, no going around it. Once the wood is fully dry, you can remote the clamps, glue both halves together. You need to cut your slats with an additional 5 mm margin around the shape of the blade, that margin will receive the (thin!) line of glue.
To my experience, this leads to failure - the fit ends up being too tight (I had to destroy a core years ago to free the blade! I never tried again as I did not protect the blade with cellophane and oil grease, it ended in disaster (no scabbard, hours of cleaning to remove the corrosion on the blade).
So you need to find a way to adjust/loosen the fit, that's what I did by reopening one side. I glued again on top of the layer of dried glue: it provided the missing space inside the core for a great fit. other way seen on historical examples: a thin band of veneer is inserted to adjust the fit on one side or both.
Another method is to cut slats to exact size (no margin. clamp and let dry. then wrap with linen soaked in glue (hide glue preferably). Let it dry, it can then be sanded as needed, cover with leather. I have not tried this yet, but seen some really nice examples by others.
I'm planning to combine the 2 techniques here. I have a solid wood core, glued. It's good enough to receive leather as it is. But I will wrap it in soaked linen to strengthen it as this stuff is tough as nails when dry. It's super thin, so I can spare a millimeter in thickness to do that.
Hope this helps.
J
Jonathan Hodge wrote: |
Do you mind to share the thickness and type of wood you used? Also, did you do any cutting to match the blade taper before soaking? |
The wood should be between 1mm to 3mm. The slats I have are approx 3mm thick. These are cut before soaking.
Radovan Geist wrote: |
When you say "Another way would be to wrap around with linen soaked in glue, in fact i will wrap it with that to strengthen it further" |
Hey Radovan - nothing wrong with asking, I do that a lot too!
Slats are mostly formed on the blade (cut to size, soak, clamp, dry). The steaming/soaking is always the core principle here, no going around it. Once the wood is fully dry, you can remote the clamps, glue both halves together. You need to cut your slats with an additional 5 mm margin around the shape of the blade, that margin will receive the (thin!) line of glue.
To my experience, this leads to failure - the fit ends up being too tight (I had to destroy a core years ago to free the blade! I never tried again as I did not protect the blade with cellophane and oil grease, it ended in disaster (no scabbard, hours of cleaning to remove the corrosion on the blade).
So you need to find a way to adjust/loosen the fit, that's what I did by reopening one side. I glued again on top of the layer of dried glue: it provided the missing space inside the core for a great fit. other way seen on historical examples: a thin band of veneer is inserted to adjust the fit on one side or both.
Another method is to cut slats to exact size (no margin. clamp and let dry. then wrap with linen soaked in glue (hide glue preferably). Let it dry, it can then be sanded as needed, cover with leather. I have not tried this yet, but seen some really nice examples by others.
I'm planning to combine the 2 techniques here. I have a solid wood core, glued. It's good enough to receive leather as it is. But I will wrap it in soaked linen to strengthen it as this stuff is tough as nails when dry. It's super thin, so I can spare a millimeter in thickness to do that.
Hope this helps.
J
Done.
First linen wrap, then leather. I've mixed wood glue with water then applied liberally on the linen (soaked) with an old brush. I will soak it in one go to save time on the next one. To be fair, I am not convinced this step is essential. Another mod would be to add felt/wool inside, an easy step with the slat method.
Leather work - I'm usually cutting to rough shape, then refine on the core. Not easy with linen on. I am also punching holes straight on the core too. I will try to measure and punch before hand. I also don't mind tooling the leather on the core. I know many pro work on the leather flat, then sew it on the scabbard. As you can see, my stitching is nothing fancy, as long as the seam is centered, I'm happy, especially when using dark dye afterwards. I could improve this by stitching into the thickness of the leather. Stitching the scabbard is long, tricky, and no fun at all. But completing this step is very satisfying.
I wrapped the rain guard with cellophane so that the humidity of the drying scabbard allowed it to shape nicely around the mouth of the scabbard. It rests on the scabbard when the sword is in, and is not in the way when drawing it back.
Again, the slat method allowed for the full thickness of the scabbard to fit nicely under the rain guard. No more carving for me, the fit is like a glove.
That's it for now. I won't be able to work on this for a few weeks. It's down to tooling, which will be extensive to match the guard. Then dye, refinish blade and hilt, peen block (or no peen block, have not decided yet) then make custom buckles and suspensions...So still some way to go.
First linen wrap, then leather. I've mixed wood glue with water then applied liberally on the linen (soaked) with an old brush. I will soak it in one go to save time on the next one. To be fair, I am not convinced this step is essential. Another mod would be to add felt/wool inside, an easy step with the slat method.
Leather work - I'm usually cutting to rough shape, then refine on the core. Not easy with linen on. I am also punching holes straight on the core too. I will try to measure and punch before hand. I also don't mind tooling the leather on the core. I know many pro work on the leather flat, then sew it on the scabbard. As you can see, my stitching is nothing fancy, as long as the seam is centered, I'm happy, especially when using dark dye afterwards. I could improve this by stitching into the thickness of the leather. Stitching the scabbard is long, tricky, and no fun at all. But completing this step is very satisfying.
I wrapped the rain guard with cellophane so that the humidity of the drying scabbard allowed it to shape nicely around the mouth of the scabbard. It rests on the scabbard when the sword is in, and is not in the way when drawing it back.
Again, the slat method allowed for the full thickness of the scabbard to fit nicely under the rain guard. No more carving for me, the fit is like a glove.
That's it for now. I won't be able to work on this for a few weeks. It's down to tooling, which will be extensive to match the guard. Then dye, refinish blade and hilt, peen block (or no peen block, have not decided yet) then make custom buckles and suspensions...So still some way to go.

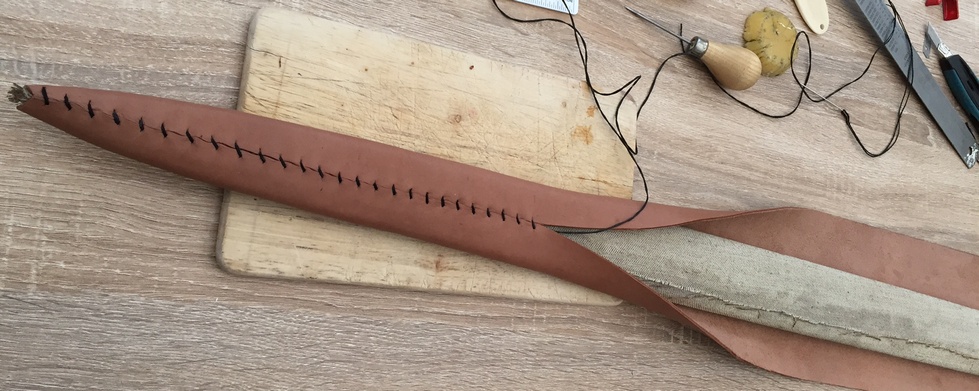



Dot dot dot dot dot - lines lines lines - bone folder - dot dot dot dot dot dot dot dot dot dot dot dot dot dot dot dot dot dot dot dot...
All work and no play makes Jack a dull boy...
You get the picture :) A scabbard is a bloody long implement...when you have to cover it with tiny dots (I use an empty mechanical pencil). This is testing my patience already...
I am also testing a technique involving line burning, which does not make the all thing any faster.
I've done 1/5 in two hours..sigh*
All work and no play makes Jack a dull boy...
You get the picture :) A scabbard is a bloody long implement...when you have to cover it with tiny dots (I use an empty mechanical pencil). This is testing my patience already...
I am also testing a technique involving line burning, which does not make the all thing any faster.
I've done 1/5 in two hours..sigh*


"Zen in the Art of the Sheather" It's certainly proving to be worth the effort--at least to the rest of us!
I've said it before Julien, you are amazingly talented. You might think it just hard work and time, but not everyone can create something this beautiful!
Thanks JD & Sean for your comments, very motivating :)
There we are. I can't shoot any decent full size shots at his time (night time at 4 pm these days in Britain) - but you can have an idea of the finished piece below. As usual, a couple of mistakes were made, few if you consider the size of the piece.
I toyed with the idea of using colors on the flowers - red - to further link with the hilt. But I did not want to take away attention from the carving. The straps will be in red, that should be good enough.
Had a weird render with the dye, way darker than the grip. So I'll be rubbing the scabbard with dark brown shoe cream until I lighten the pigment. Delicate job as I can take away some of the carving details easily. Should I've done the usual, diluted pass after diluted pass, until I get a match. It was dark already out there, could not see properly and I went overboard. I think it will be fine though. Better pics to come soon.
J
There we are. I can't shoot any decent full size shots at his time (night time at 4 pm these days in Britain) - but you can have an idea of the finished piece below. As usual, a couple of mistakes were made, few if you consider the size of the piece.
I toyed with the idea of using colors on the flowers - red - to further link with the hilt. But I did not want to take away attention from the carving. The straps will be in red, that should be good enough.
Had a weird render with the dye, way darker than the grip. So I'll be rubbing the scabbard with dark brown shoe cream until I lighten the pigment. Delicate job as I can take away some of the carving details easily. Should I've done the usual, diluted pass after diluted pass, until I get a match. It was dark already out there, could not see properly and I went overboard. I think it will be fine though. Better pics to come soon.
J


Last edited by Julien M on Sun 13 Nov, 2016 1:03 pm; edited 1 time in total
Very well done, Julien! I've watched the progress of this project and enjoyed seeing it come together. Your tooling is very well done. Cheers!
You're definitely a sword hero, Julien. This is incredible to see. I'm impatient to see the finished piece!
Vraiment du super boulot ! :D
Vraiment du super boulot ! :D
Thanks for shaering your experiance
Thanks guys/Merci messieurs! :) I have a few things in mind as next steps. A steel shape, brazed, a nut for the peen which will involve heating the thread and flatten and draw it out a little bit (the tang is threaded, but I prefer to ignore this and peen the sword), clean fittings and blade to clean satin polish, sort out the guard with brass wedges or a dab of weld inside the slot, suspensions (carved too - no choice here or it will look out of place) and buckles, strap end etc.
Started two years ago...these projects are never ending when you have a couple of hours per week to spend on them.
ps: as far as documenting the process, I could just post pics of the final piece. But seeing others post their stuff (Sean among others) prompted me to start mine so might continue to do that.
Started two years ago...these projects are never ending when you have a couple of hours per week to spend on them.
ps: as far as documenting the process, I could just post pics of the final piece. But seeing others post their stuff (Sean among others) prompted me to start mine so might continue to do that.
That is bloody good. You rock at leather work, Julien. Seriously.
No offense but the Durer is hardly deserving of that scabbard and grip. You need a better sword ;)
No offense but the Durer is hardly deserving of that scabbard and grip. You need a better sword ;)
Page 4 of 5
You cannot post new topics in this forumYou cannot reply to topics in this forum
You cannot edit your posts in this forum
You cannot delete your posts in this forum
You cannot vote in polls in this forum
You cannot attach files in this forum
You can download files in this forum
All contents © Copyright 2003-2006 myArmoury.com All rights reserved
Discussion forums powered by phpBB © The phpBB Group
Switch to the Full-featured Version of the forum
Discussion forums powered by phpBB © The phpBB Group
Switch to the Full-featured Version of the forum