a question for professional or hobbyist knifemakers.
Many Landsknecht or Bollock daggers with the strongly flaring "trumpet" shaped handles have pommels that sort of grip the handle with small triangular or decoratively shaped protrusions all around the pommel's perimeter. These protrusions are presumably crimped down to the handle's surface after the pommel is put in place.
I attached an image as an example of what I am talking about. Here the flare of the grip is actually very slight, in most others I have seen it much more pronounced.
I am working on a hobby project of a little Landsknecht style dagger, mostly using it to experiment with new techniques: wire wrapped grip and this style of pommel attachment. When I got to test-fitting the pommel, I discovered that I can't crimp the protrusions all the way down. The metal (nickel silver in my case) has some springiness to it, so no matter how hard I push they spring back a little and stay about 1/16" away from the handle wrapping.
So, is there some trick to this? I would appreciate any suggestions.
For now, my plan is to try annealing the protrusions first (will put the pommel in a shallow pan with some water to preserve the soldered joint, and use a propane torch), and then lightly hammer them in place instead of pushing.
Thanks.
Alex.

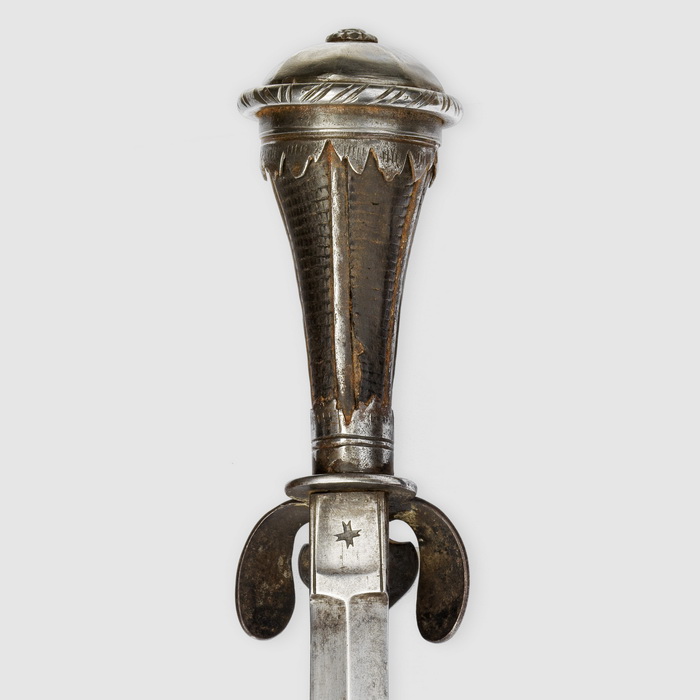