I have just finished this sword breaker based on a composite of pieces from around 1600 and I hope you like the result.
This style of knife came in at the end of the 16thC and lasted perhaps as late as the mid 17th and were used defensively to trap an opponents blade and take control of it and they do this very well. When a blade enters the void between the teeth, a pull or a twist will catch the and hold the blade. Whether they truly did 'break blades' I am not so sure, but they certainly do work.
They were not a very common form of knife and perhaps this was ether because they were bulky or expensive to make or indeed deemed to not be very useful however they are certainly very striking. The teeth were either fixed like this example or were articulated and must have been very much more expensive. They do look inherently weak, but this is partially offset by a thick blade with very little distal taper.
This example has a 6.5mm/ 1/4" thick blade, 275mm long/11.5" and has a steel guard and pommel with a steel and bronze wrapped grip with steel turks heads top and bottom.
Tod

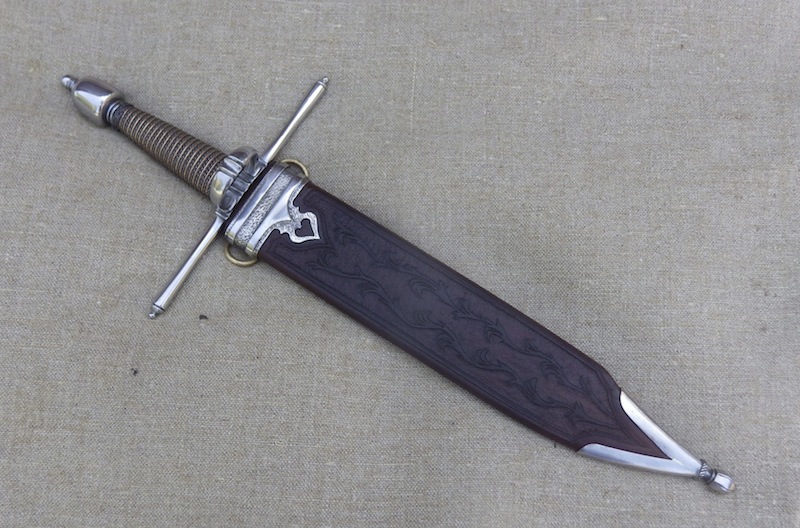

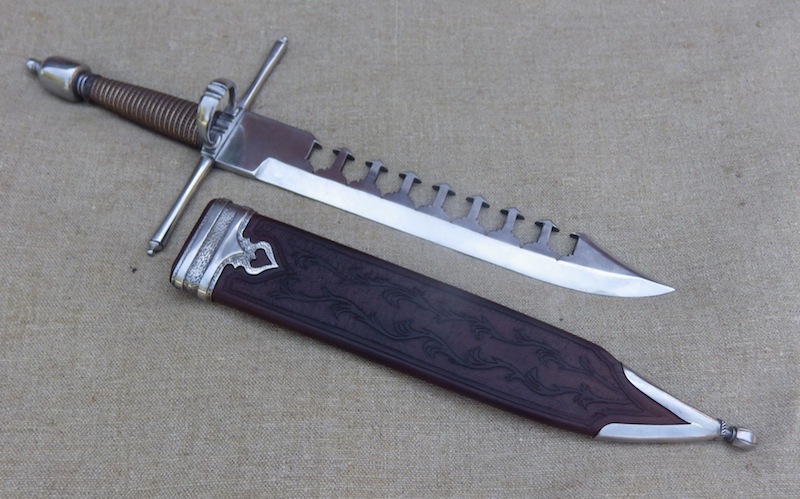

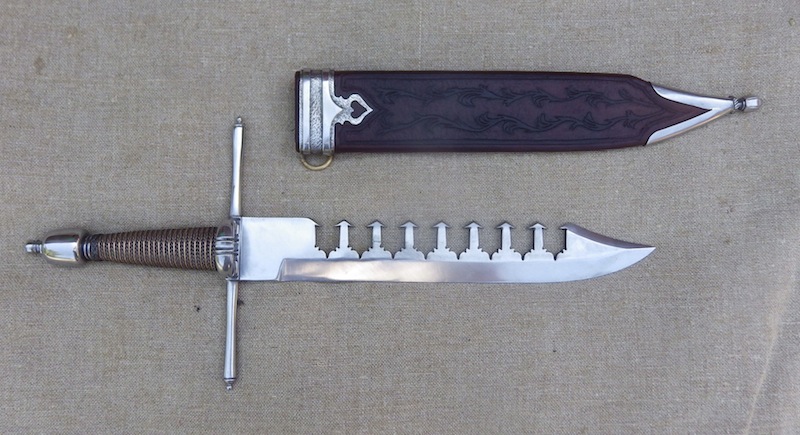

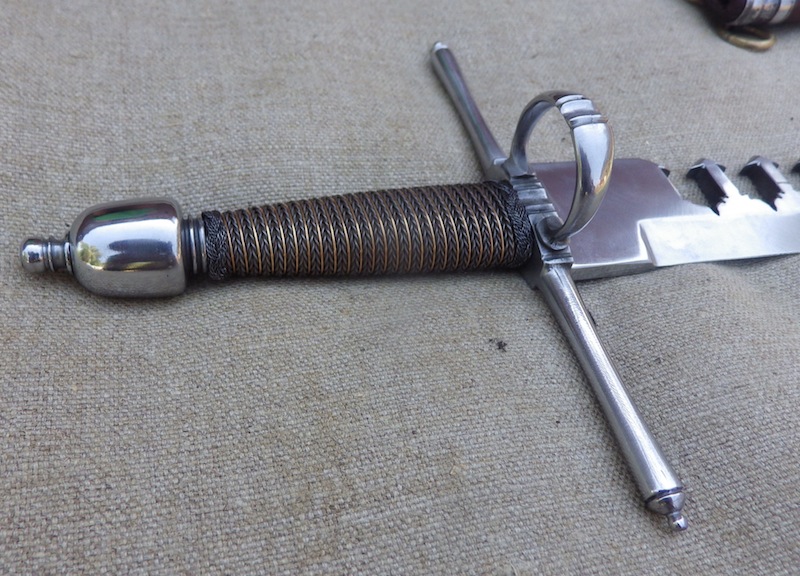

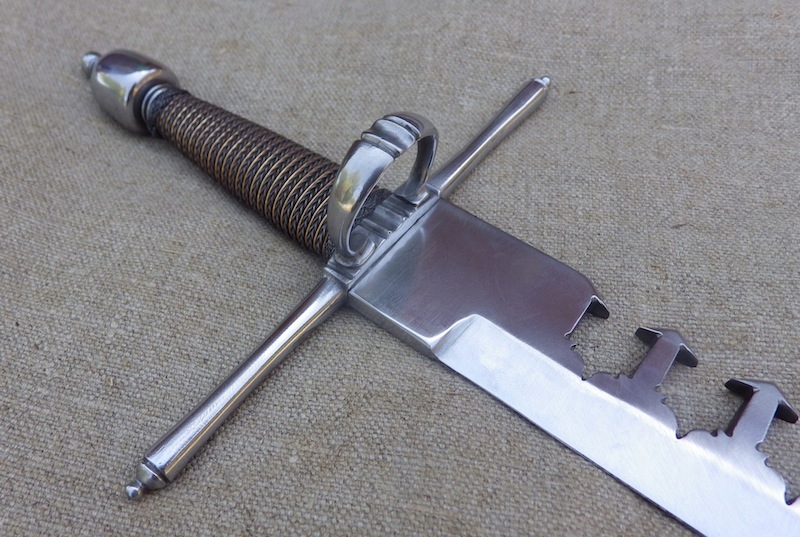

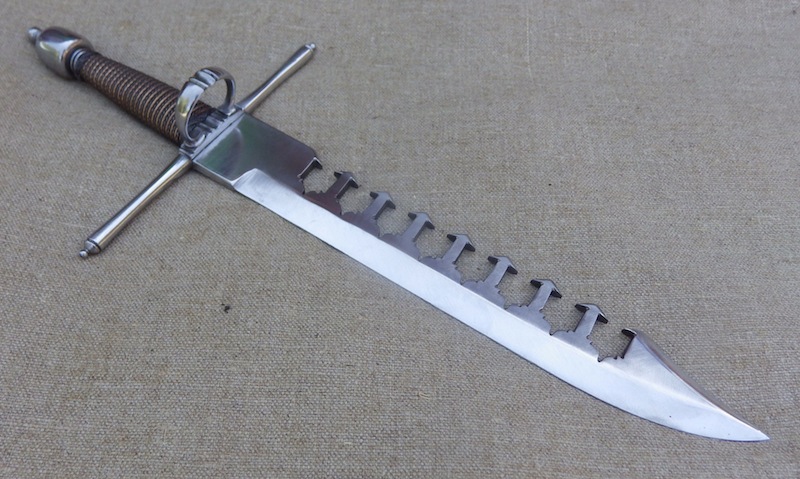