i wondering if anyone out there has ever attempted to solder their blade to their hilt on their own.
i've been working on a project since about july, i made my hilt pieces fit tight enough that i didn't think i would have an issue with gaps between the guard and blade. actually, it did cause a problem. even though my guard sits well against the blade, the blade has a fuller running through the grip (this is part of my colossus knife project) which when seated together there's tons of play in the guard due to the lack of the flat surface for the guard to sit against.
so i refereed to my books - read up on soldering guards to hilts. my surfaces are clean, well polished, fluxed to the max, yet the all purpose metal is not flowing like described. this is a steel on steel joint, and i just need a little bit of it to flow in the crack but instead when heated it just sits on top of the steel like a bubble of lead. other times rolls right off, and other times sticks to the steel in the wrong place.
i got it to work once, and it must have been by accident because i can't tell you how i got it to work. but from what i've been seeing i'm now thinking its not tuff enough to hold the guard on. i bet if i drop it on the floor everything goes in pieces. i thought about using JB weld, apoxy, or actually just take some lead i have laying around and melt it into it.
so, anyone know where i'm going wrong?
I soldered the guard on my first sword. I had all sorts of trouble and just by chance eventually got it more or less right. I have decided that it is much better to just use wooden or brass wedges, glue or resin. My last guard was fixed in place with one brass wedge and it is tight as can be.
I find it easier to forge weld than to get a decent soldered joint, so I'm a little heartened to hear of someone else having similar problems.
I'm told that x-rays of historical pieces have been published showing showing the use of wedges, so I'd say there's no shame in using them.
I'm told that x-rays of historical pieces have been published showing showing the use of wedges, so I'd say there's no shame in using them.
Usually when you're soldering with silver solder you're going to want to keep the entire piece hot, not just select areas because the cooler areas in the piece will draw the heat away from the site you want soldered. Move your torch around the entire area instead of letting it stand in one place. Granted, most of my soldering has been done in a jewelry/vessel fabrication setting, so I'm not sure on the best way to approach a heat treated blade, possibly wrap a wet towel around the base of the blade and around the tang to keep the heat from spreading too far.
You might also want to clean your solder if you haven't already been doing that. When you flux your solder site, sometimes less is more.
You might also want to clean your solder if you haven't already been doing that. When you flux your solder site, sometimes less is more.
I think you might be using the wrong flux. I've soldered several stainless steel guards to blades on fixed blade hunting knives I've made. With an acid etch flux it was a piece of cake and the solder flowed beautifully.
i believe your right, my books mentioned an acid based flux which i could not find at my local lowes. i was using standard plumbing flux that you usually use to sweat copper joints.
i did also attempt a copper wedge using a strand of copper wire down the edges of the fuller, i think this is the only reason why i got the solder to stick - it stuck to the copper and wedge itself in the joint instead of flowing into it. it looks a little sloppy, but once i cleaned it up its not horrible. still an eyesore though.
i did also attempt a copper wedge using a strand of copper wire down the edges of the fuller, i think this is the only reason why i got the solder to stick - it stuck to the copper and wedge itself in the joint instead of flowing into it. it looks a little sloppy, but once i cleaned it up its not horrible. still an eyesore though.
Try placing a thin layer of solder on each piece separately (tinning). Add flux, put them together and heat. The two layers of solder will melt and bond.
Mike,
i believe that was the attempt i tried, i've got a picture below here that show how i set up before i heated the the knife. when i did my heat, i did it from the under side of the guard, hoping to pull the solder to the hottest part of the steel. but all that happened was it just rolled right off. i attempted with with both tinning solder, and an acid based solder. both acted the same.
however . . . today i went looking for an acid based flux - i did find some self cleaning flux - then i saw a paste based silver solder and flux. it was $3 so i went after it. at another hardware store i round some actual silver solder but i could not find the accompanying flux and it was much more expensive, and brazing rods!!!! but i don't have a torch to use them.
well i took the paste, and found that it worked just like it should have. i cleaned up two edges of steel, squeezed a little on the edge i wanted to join, and a little on the opposite side of the joint. heated it from the unsoldered end and it did flow correctly to the heat. let it cool and wacked it with a hammer and it remained joined.
so, i've got the sliver paste with flux to work. as it comes out of the tube it looks like shaving suspended in the flux, once it come to temp it begins to look like complete solder.
Attachment: 95.55 KB
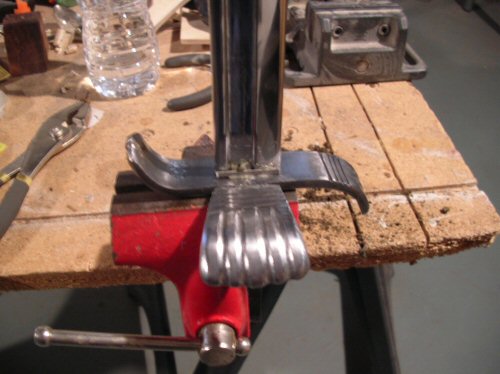
acid based solder with typical pluming flux. got an ugly result from this one.
i believe that was the attempt i tried, i've got a picture below here that show how i set up before i heated the the knife. when i did my heat, i did it from the under side of the guard, hoping to pull the solder to the hottest part of the steel. but all that happened was it just rolled right off. i attempted with with both tinning solder, and an acid based solder. both acted the same.
however . . . today i went looking for an acid based flux - i did find some self cleaning flux - then i saw a paste based silver solder and flux. it was $3 so i went after it. at another hardware store i round some actual silver solder but i could not find the accompanying flux and it was much more expensive, and brazing rods!!!! but i don't have a torch to use them.
well i took the paste, and found that it worked just like it should have. i cleaned up two edges of steel, squeezed a little on the edge i wanted to join, and a little on the opposite side of the joint. heated it from the unsoldered end and it did flow correctly to the heat. let it cool and wacked it with a hammer and it remained joined.
so, i've got the sliver paste with flux to work. as it comes out of the tube it looks like shaving suspended in the flux, once it come to temp it begins to look like complete solder.

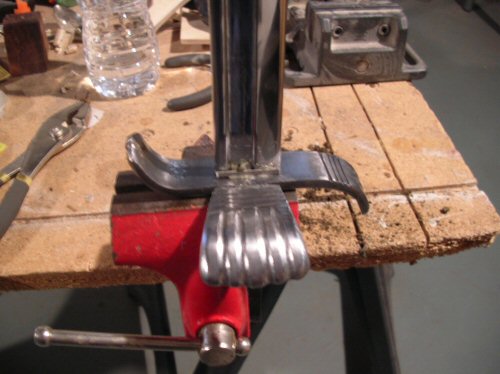
acid based solder with typical pluming flux. got an ugly result from this one.
Page 1 of 1
You cannot post new topics in this forumYou cannot reply to topics in this forum
You cannot edit your posts in this forum
You cannot delete your posts in this forum
You cannot vote in polls in this forum
You cannot attach files in this forum
You can download files in this forum
All contents © Copyright 2003-2006 myArmoury.com All rights reserved
Discussion forums powered by phpBB © The phpBB Group
Switch to the Full-featured Version of the forum
Discussion forums powered by phpBB © The phpBB Group
Switch to the Full-featured Version of the forum