Anyway.. for those who are not.. I just returned from Ric Furrer's 'Shear Madness' workshop where I learned to make shear steel. In case you are not informed on this.. it is basically a way of making high carbon steel by carburizing wrought iron by bathing it in a carbon rich media under high temperatures. This type of steel goes back into the depths of time and was an important type of steel for the making of swords, knives and tools up until the development of the modern Bessemer process. So it is a very 'period correct' steel for many of the weapons on this forum. I'm sure there are many, many of you that are much better informed on this subject.. but if I didn't put it... somebody would ask anyway!
So here are some pictures of us working in Ric's shop in Sturgeon Bay. The other students in the class were Michael Pikula, Jason Mather and Jared Stiers (did I get that spelling right?).
The process basically comprises putting pieces of wrought iron into a welded can with charcoal and placing the whole thing in a forge for a long time. The wrought iron then becomes 'blister steel' which is then stacked, forge welded together, drawn out, cut, stacked, drawn out, etc.. this is done three times to get 'triple refined' shear steel. The whole process refines the slag and other impurities as well getting the carbon evenly distributed.

These are now blister steel:
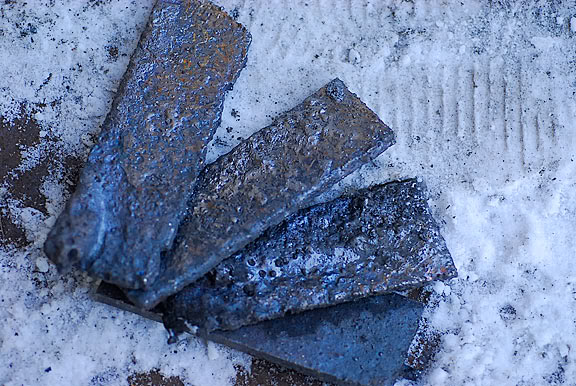
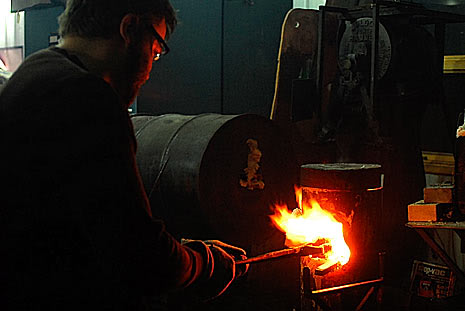
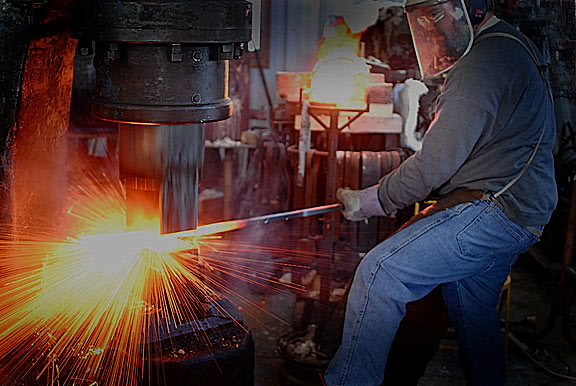
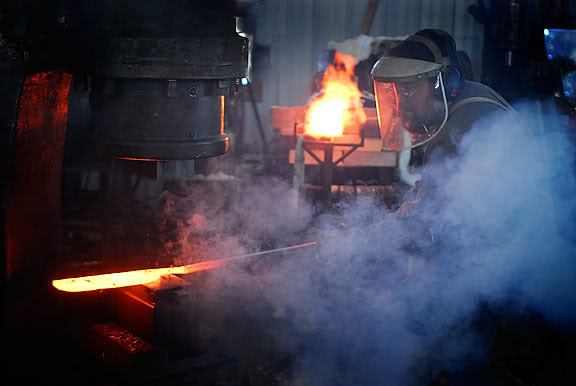
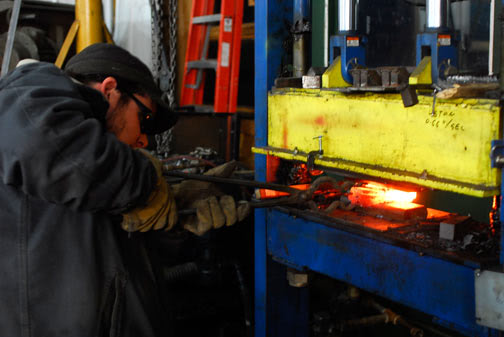
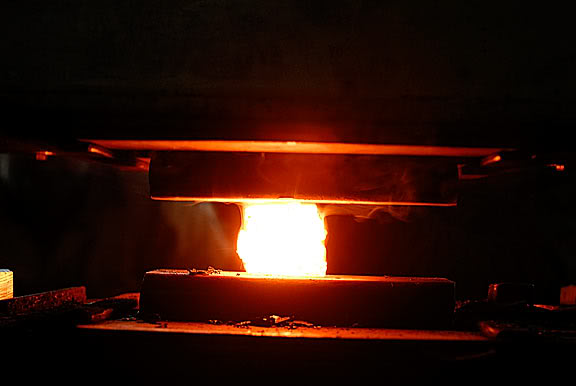
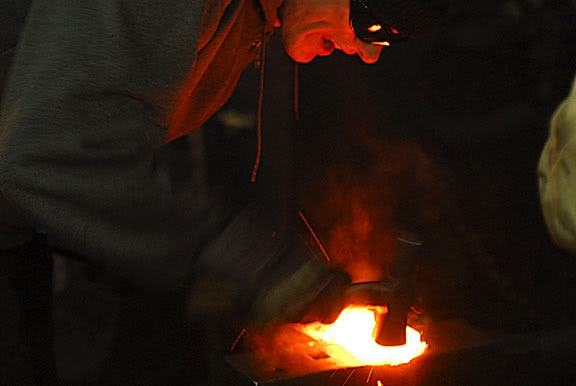
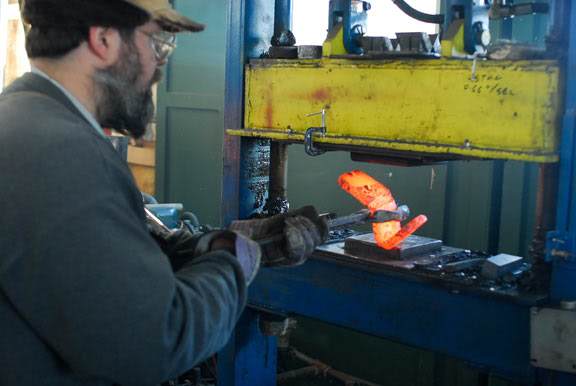
These pictures show my work with the billet I brought home from Ric's... and are in my shop...
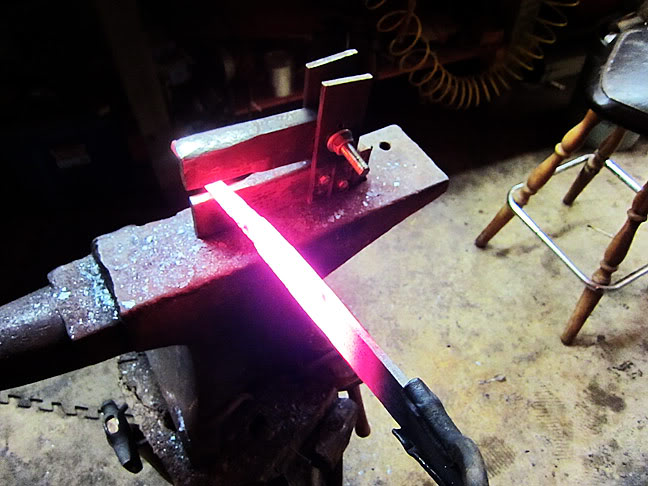
This is the blade and some conceptual ideas... Since I'm new to the history of these things I decided it would be best to pick and choose elements from different periods.. but the blade is 14". I've since greatly changed the scabbard idea.. as it didn't make sense to do it 'riding style'....
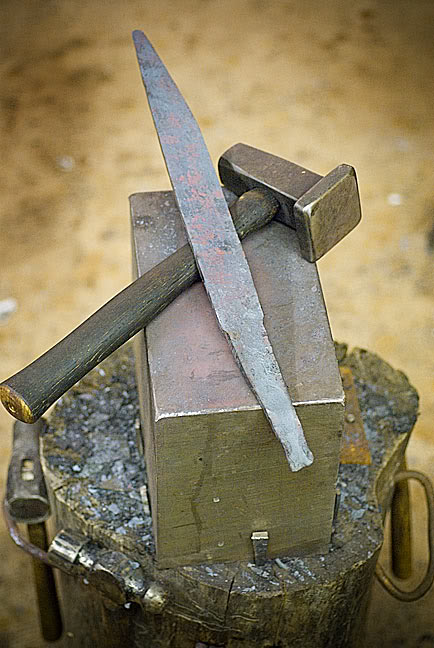
This is blade before the quench and some 'pre-etching' to see what kind of pattering was going on...
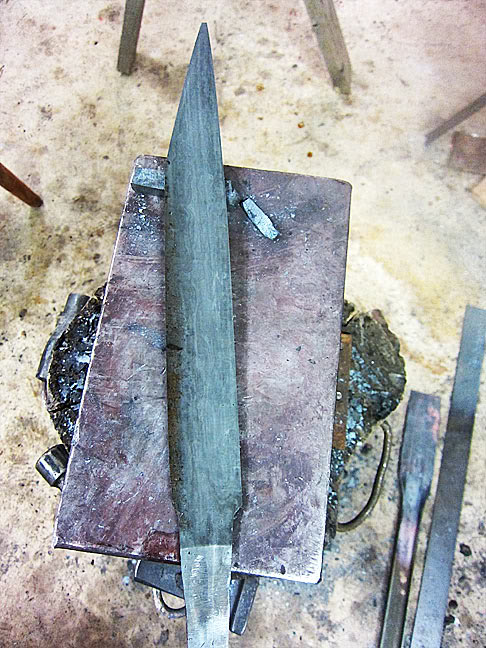
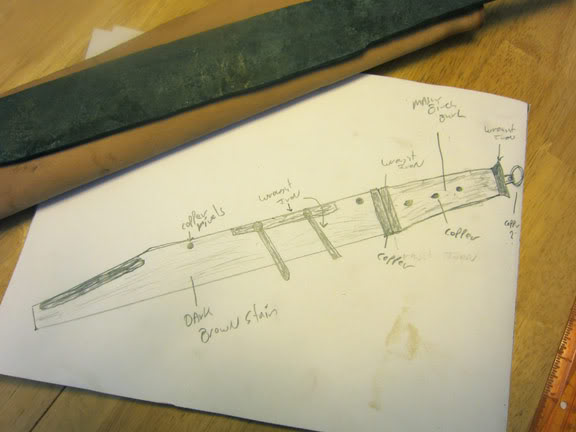
This a test blade I did to determine heat treat parameters before quenching the big one.... it ended up hardening nicely after a few false starts (and will be made available for purchase as well!)
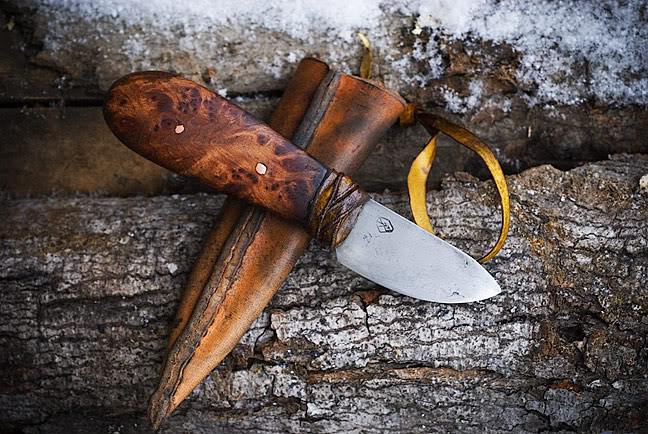
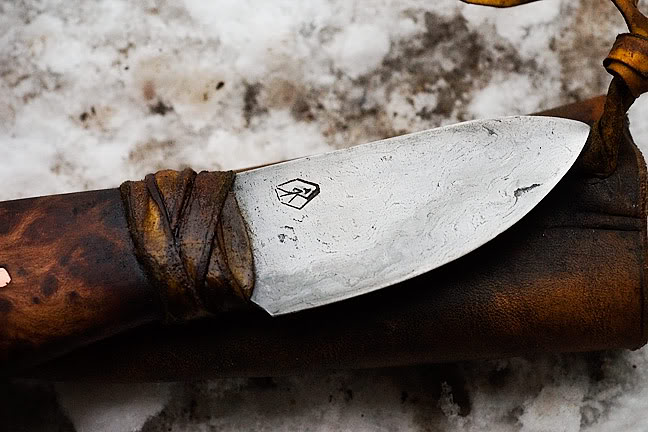
Anyway.. I hope this is interesting and I will post more a bit later.