I'm making a scabbard for my Squire line knightly. This is my second scabbard but it's the first historical one and i plan to do everything. I'll post some pictures showing what I've done so far.
I've finished the wooden core and the chape. That's about where I am now. I am extremely proud of this chape by the way, first one I've ever made. I shaped the halves out of 18 gauge steel. I really like how it turned out.
I'm getting ready to start cutting leather but I'm trying to be careful not to waste any. To that end I'm using an idea which i believe i saw somewhere on this forum. I covered the core in masking tape and then cut it off to form a perfect pattern for the leather.
I've also re-wrapped the grip on the sword. It was just a temporary experiment/practice run. I did not actually use any glue but the grip has held on really well. I wanted to try out having five risers. I'm not quite sure whether or not the final grip will have that many or not.
Questions, comments, and criticisms are welcome.
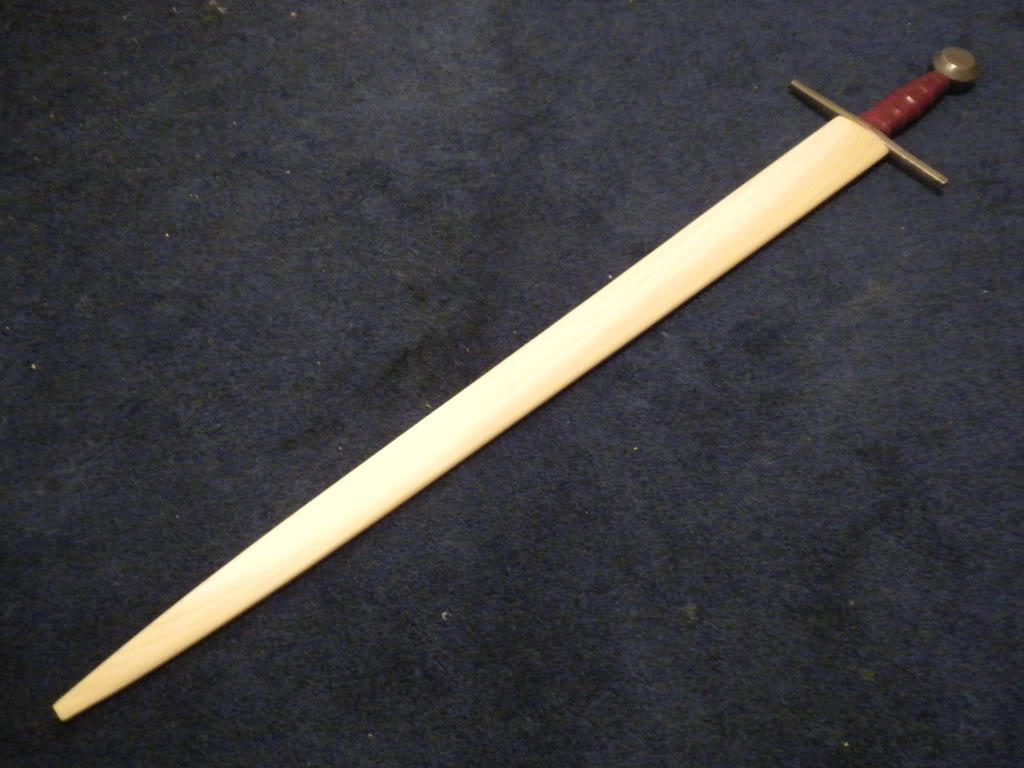
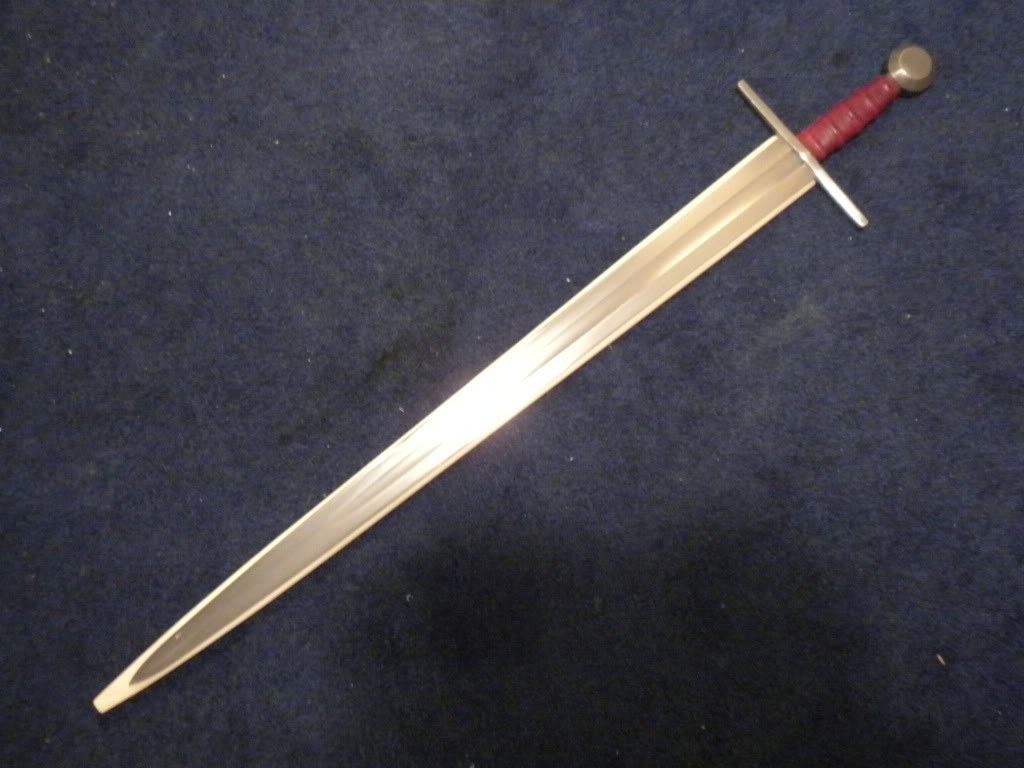

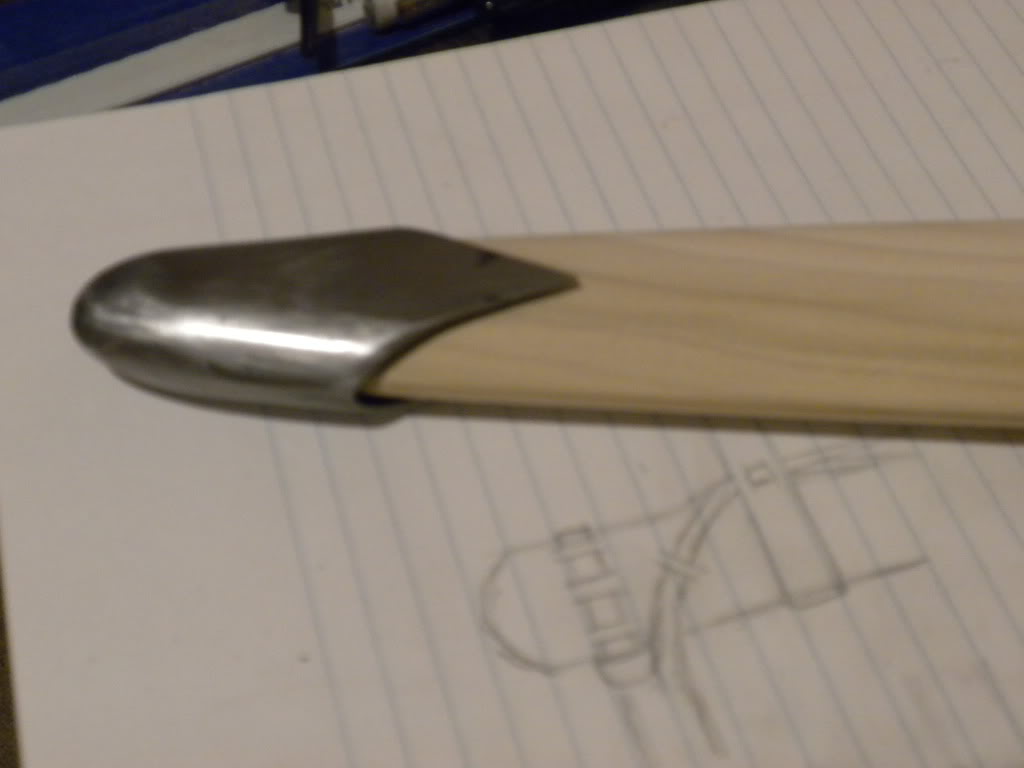
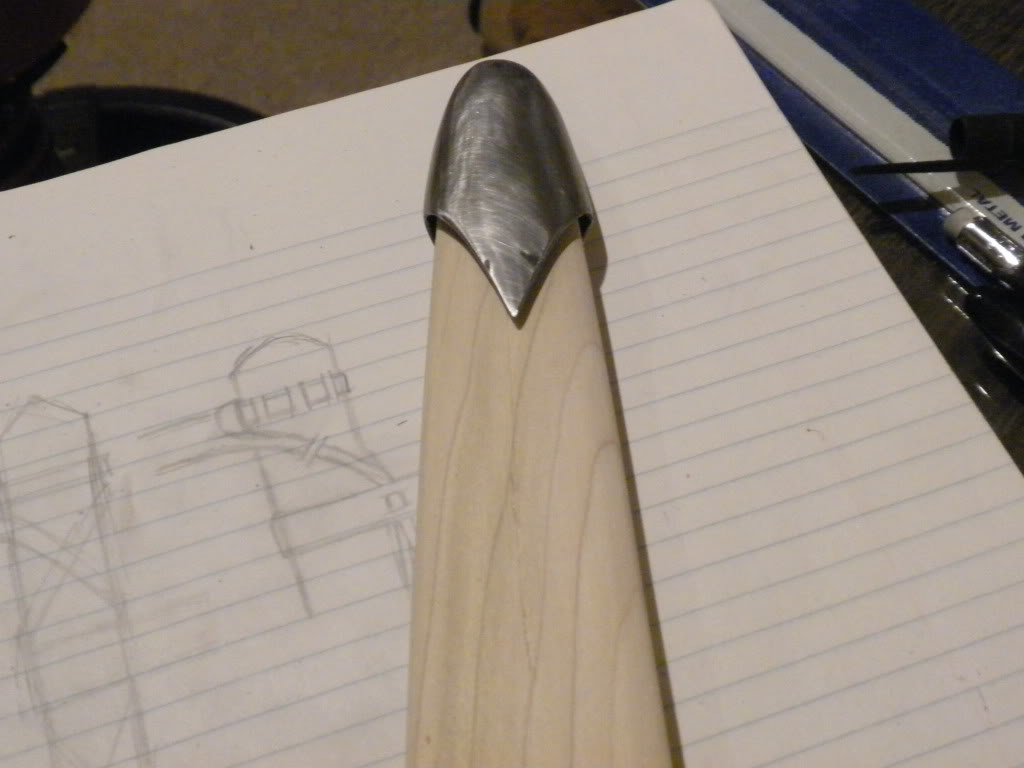