Overview
Sword collecting has been a hobby of mine for around 11 years now. In that time I have found many variations of the hobby that bring me enjoyment. One aspect of the hobby that I enjoy in particular is trying to identify and support “undiscovered” talent. Of course “undiscovered” is a relative thing. A particular artisan or craftsman may be very well known in some particular circles and still be an unknown quantity entirely in others. However, when I am looking for “unknown” talent I’m looking for someone who is just starting out professionally or even semi-professionally. I look for someone who has done a few pieces which demonstrate that they might possibly have some significant talent. I then contact this person and ask if they would be willing to do a commission and we go from there. This is usually mutually beneficial arrangement. The artisan has the opportunity to be paid for their work, an arrangement which is sometimes difficult for the new artisan to find. Additionally, if their work is good, I try to give them some well deserved press for their efforts. This often has the benefit of insuring that they will have more commissions in the future. This arrangement also works for me. By taking a chance on a talent that is not already a big name I am often able to have items made that are of top tier quality and workmanship without the attendant top tier pricing and wait list. Of course this does not always work out. On at least two occasions I have been burned by overly optimistic beliefs in what an artisan was capable of. However, in the main, this strategy has worked out well for me, and I hope, for the craftsman as well.
In this case I was looking for someone to make me a seax. I had been busily reading several lengthy books on knives and scabbards and the seax had captured my imagination. Seaxes of course come in all shapes and sizes from the small utility blade, to the large war knife. My imagination was fired by the idea of having a large seax of nearly short sword proportions paired en suite with a Viking style sword. It wasn’t that I believed such a thing was particularly historically accurate (although there are a few cases of such a pairing known) but I do like to have a certain symmetry in my collecting. A matched seax / sword pair seemed intriguing. I mentally ran through my checklist of seax makers that I was aware of. None of them really fit the bill. Some makers were turning out serviceable but somewhat rough pieces. I wanted a showpiece. Some were turning out elegantly finished seaxes but were charging significant prices for them. I was operating on a budget. Neither of the two top flight talents that came immediately to mind is any longer taking custom commissions. So I made up my mind to hunt down a new maker, the lesser known to me the better. I started scouring the internet and various blade publications to see who was out there and what they were producing. Finally over at Don Fogg’s blade smithing site I found a guy who had created a very interesting seax.
[ Linked Image ]
Although that particular piece wasn’t exactly my cup of tea it did appear that the gentleman had some talent. He also appeared to have some VERY reasonable prices. So I contacted the gentleman in question who turned out to be Ben Potter, a very talented craftsman indeed.
Ben Potter
Ben Potter started blade smithing when he was about 10 and was interested in out door activities but couldn't afford a good knife. He learning knife making using the stock removal method, basic woodworking, blacksmithing, leatherwork, as well as a love for traditional crafts from his father, Ben became a farrier’s apprentice and learned more about blacksmithing. He took two years of saddle making and leatherwork training and worked as a custom western style leatherworker for a year. He then had a series of different business ventures where he did everything from boomerang making to developing and testing underwater spear guns and diving equipment. In 2007 he realized that he had gained the skills needed to make knives and swords in the Celto-Norse style.
The other smiths who have had the most impact on his work are Jake Powning, David and Andy of the MAD dwarf workshop and Don Fogg. The craftsmen (and women) who have helped him on his way are, his father in law Don McKinley (a top notch violin maker) who had taught Ben to mix machines and hand tools to speed the process with out compromising on the finished product, and his mother in law Anne who taught him to be perfectionist about getting the details right. Ben says that a huge influence in his life and work comes from the scriptures and the ideals and principles therein. Of course his last but greatest influence is, Corrie, his wife and helper in all things.
Commission
Ben and I started trying to work our way towards a commission. I knew I wanted a seax of the variety known as the “broken back” seax. I knew that I wanted some sort of figural carving on the handle. I knew I wanted steel fittings and I knew that I wanted the piece to be fairly large. Other then that all I had were question marks. What should the dimensions be exactly? What should the blade profile look like? What sort of wood should be used on the handle? Did I want the fittings to be decorative as well as functional? What sort of steel did I want? What kind of carving did I want on the handle? These were all questions that Ben had to have answers for… and I hadn’t a clue. So we started working through it. Ben helpfully drew up some diagrams of potential blades and fitting combinations.
[ Linked Image ]
We soon were able to settle those questions.
[ Linked Image ]
We decided upon some simple geometric patterning on the fittings. I left the question of the steel up to him entirely. I had decided long ago that it is best to let a craftsman work in the medium that they are most familiar with. For the wood I only specified “dark” again I left the actual choice up to Ben. We decided upon dimensions for the finished piece (roughly) and finally I again scoured various resources both in print and online to find examples of Viking era wood carving. When I happened across some detailed shots of the prow of the Osberg ship currently housed in the Viking Ship Museum in Oslo, Norway I knew I had found what I was looking for. I sent the pictures to Ben and he took it from there.
[ Linked Image ]
After that my participation in the project mostly consisted of waiting. Ben did ask questions about how I wanted particular things done from time to time, but in all honesty when dealing with a craftsman I usually just give them free rein to do whatever they think is necessary to complete the project to their satisfaction. I have found through experience that this invariably leads to a finer finished product then anything I could have told them to do. This case proved to be no exception. Ben absolutely out did himself.
Here are the results:
[ Linked Image ]
[ Linked Image ]
[ Linked Image ]
[ Linked Image ]\
Weight: 1.2 pounds
Overall length: 21.25 inches
Blade length: 15.5 inches
Blade width: 2 inches at base
Grip length: 5inches
Blade thickness: 0.25 inch spine
Seax Characteristics
Like daggers it is rather difficult to characterize how a seax “handles.” There is a balance point of course but the entire piece is so short that one does not get the feeling of the piece being truly “blade heavy” or not no matter where the balance point is. In a similar manner the center of percussion is largely irrelevant. Suffice it to say that this piece does feel very good in hand and I think would be very good for its intended purpose cutting. I have to be honest and admit that I have never tried to cut anything with this seax. Like many functional pieces of art, although I have no doubt it can cut, there is no way I’m going to mess it up by actually cutting with it. However, Ben felt no such compunction and tested the blade quite rigorously to make sure that it would stand up to use and abuse.
Fit and Finish
The workmanship on this piece is simply fantastic. As you can tell from the pictures above Ben has the ability to first draw out incredibly intricate designs and then make those designs reality in wood, metal and leather. All tolerances on this piece are extremely tight. All junctures are crisp and clean, the handle assembly is rock steady. The carving is fantastic… as a wood worker myself I know what goes into making something like this grip from wood and it just makes it that much more impressive. The fittings are nearly jewel like in their clean geometry and the blade is cleanly executed. I’m sure as with every project the maker can point out flaws… but as the customer I have been unable to find them.
Conclusion
Ben Potter did a fantastic job with this piece. It is a testament to his skill set that he was able to take a complicated design and turn it into concrete reality. Additionally, Ben is an absolute pleasure to work with. He very much takes his customers desires into account and tries to be responsive to all their questions.
There are only a handful of artisans that can do the sort of things that Ben does. Most of them like Jake Powning have long ago moved into the realm of no longer wanting or needing to take custom orders. I fully expect that this will be true of Ben as well. He has the talent and does the same sort of work. In other words, if you are interested in the sort of work that Ben does you need to move now, before his backlog becomes a matter of years instead of months and before he starts commanding the sort of prices that the better known master craftsman command.
Contact Information
You can find all you need to know to contact Ben here:
http://www.seekyee.com/Bladesmithing/index/index.htm

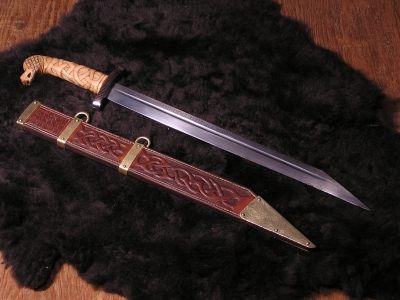

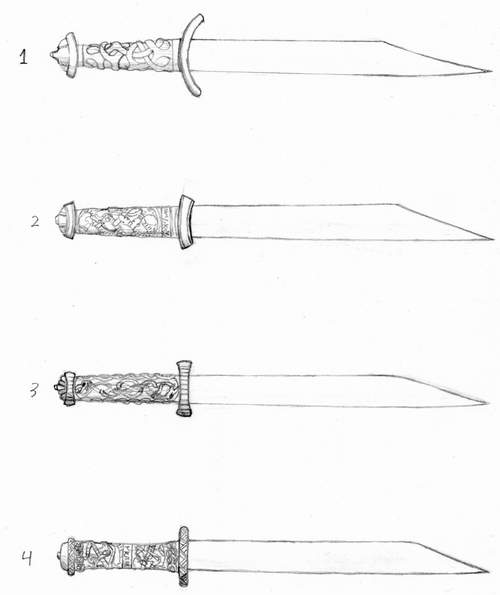

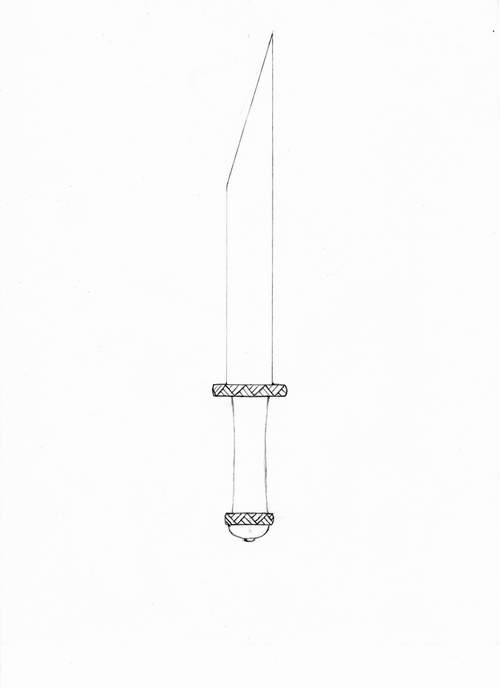

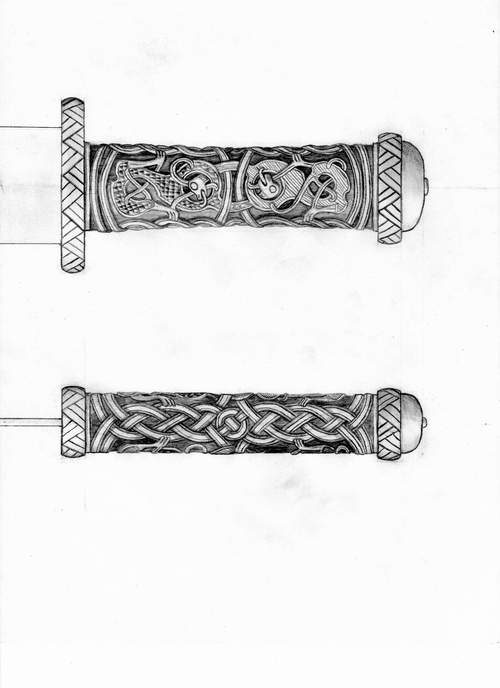

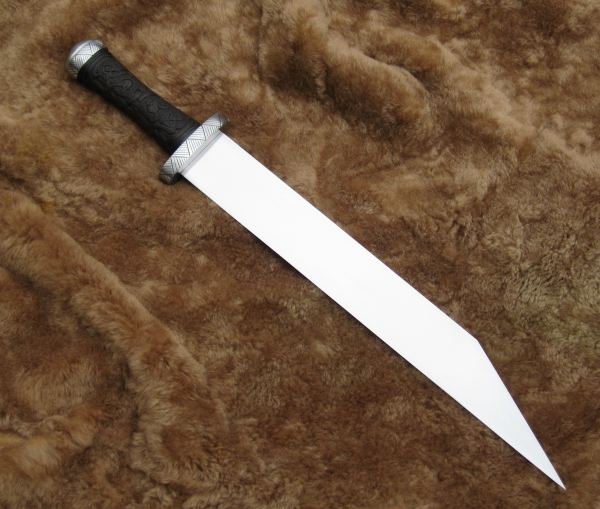

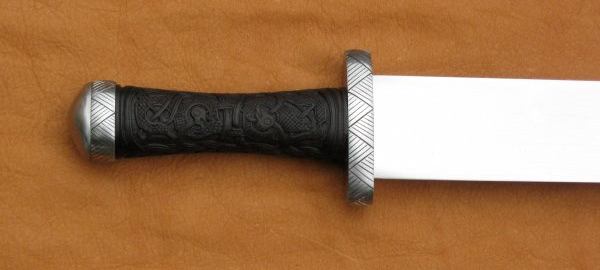

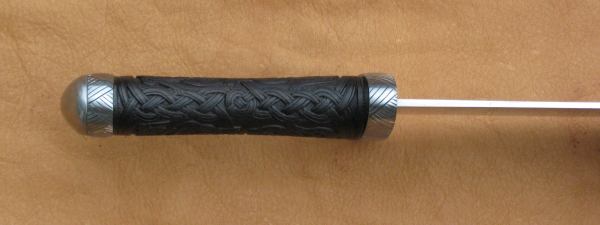

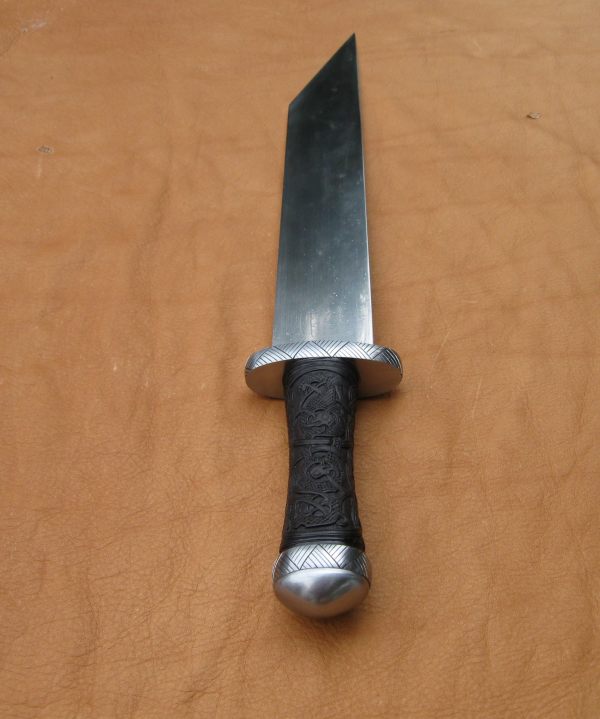