Construction:
The SKS bayonet was stripped down and cleaned, the parkerizing sanded off, and the tip re-ground to create a tapered point rather than the original "chisel" end. It was then sanded and polished with OOO steel wool. The end of an antler palm was cut off and discs cut from it using a hole saw. The discs were then drilled for appropriate center-holes, the bottom disc matching the diameter of the bayonet's tang (it has a convienent "step" already in it for the disc to sit against). A tine of antler was cut to size for a grip and bored through and stepped up to fit precisely over the bayonet tang. The pieces were sanded and finished with a 50/50 mix of turpentine and boiled linseed oil to bring them back to "life".
In order to piece everything together, I intended to run a bolt through the hilt and thread it into the end of the tang of the bayonet, so I drilled and tapped a 1/4"-20 hole for a carriage bolt. The head of the bolt was then ground to a "pyramidal" shape, leaving just enough of a square base so that I could later tighten it with a wrench. Everything was test fitted several times, the hilt pieces dremeled and sanded until they fit together snugly, matching all their natural curves. Once everything was in place, along with a metal hardware "widget" that I used as a washer under the bolt head, I set the components aside.
Each hilt piece was masked, and a batch of epoxy resin mixed up, adding enough Cab-O-Sil (a thixotropic) to keep it from running everywhere. I then coated the tang and the inside of the discs and grip with resin, filled the grip with a balance of resin to take up the space not occupied by the tang and bolt (which is not much), and put everything in place. The bolt was then tightened down, the fit checked, and given a final torqueing before wiping off the little excess resin which had escaped. Once all had set, the masking was removed and I was left with something I find a joy to hold and behold.
Stats:
Overall length: 17 1/2"
Blade length: 12 3/8"
Overall hilt: 5 1/8"
Grip: 4"
Upper (pommel end) disc diameter: 2 1/4"
Lower (blade end) disc diameter: 1 3/4"

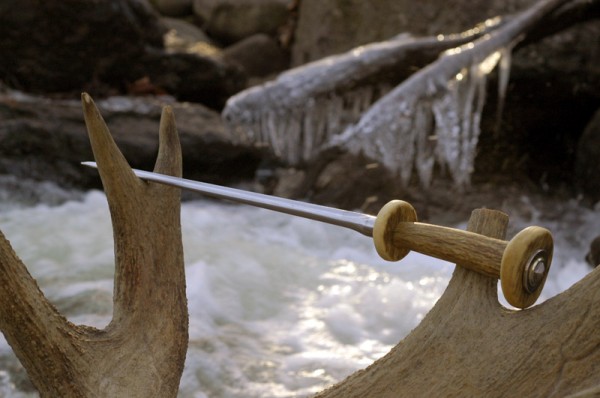

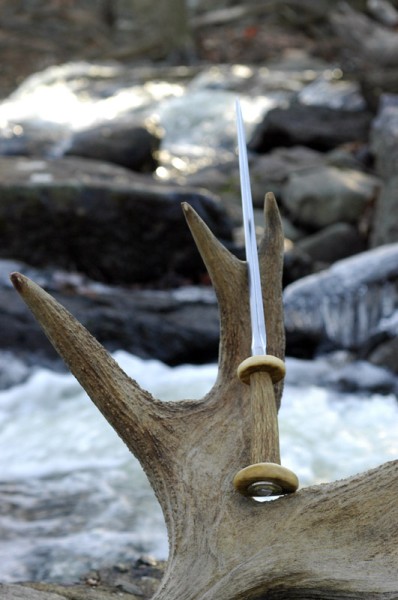

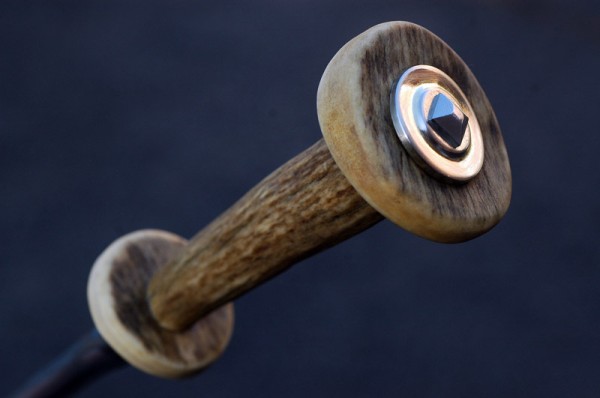

