I have started on a pair of swords I have wanted to make for years and have finally got the chance to reproduce the amazing A489 Swiss Sabre from the Wallace Collection.
I have been posting up pictures of the progress on Instagram, but thought I would share it here with a more expanded story with more details.
The sword was made around 1530 in the very stylish and fashionable Swiss Sabre style using a complex guard and a wickedly sharp single edged blade at a whopping 102cm/40" long. The sword looks like a beauty and when you handle it, you realise just how lovely this sword actually is - I am in love.
Like all sabres, the blade is quite complex and this simply does not show from the pictures. The whole blade is very slightly curved, thou through some trick of the eye it looks far more curved than it is, and if you set it on its spine there is less than 10mm from the surface to the back of the blade even with the stepped down section.
The first 15cm of the back of the blade is 'full height', then it steps down 2mm and goes along a further 45cm and lifts up again for the yelman. The whole blade is hollow ground and then goes into an appleseed edge so that the thickness of the peak at the transition between the fuller and the edge is significantly smaller than the back edge thickness at that point. The blade starts at 9.5mm thick but tapers down to 6mm over the first 15cm and the tapers down from there. What this all means in practice is that the blade is long but relatively light. The whole sword weighs in at 1620 grams.
I profiled the blade and the heat treated so there was some hard core grinding to get it down to 2mm by the tip. The next step was to grind a bevel in so that the transition point thickness between the fuller and bevel would be set, then the hollow went in, next the edge grind on the yelman and finally the appleseed grind to the main edge.
The guard is lovely and almost art nouveau in feel and like all complex guards must be made up piece by piece and welded and cleaned at each stage.
What is interesting is that it would be possible to make a sword with a guard like this much faster than I currently am able to. I could use this style as a target and simply bend the bars to shape, fit it in and move on. The result would be a perfectly good sword, but of course different to the original although if that was your destination it would of course be similar. When you are trying to copy a piece, the endless tweaking of shapes and checking and tweaking soaks up loads to time and so you would end up with two similar swords, but one which cost considerably more. My friend Owen Bush reckons that making a blade to dimensions takes 3 times as long as making a blade and I think he is on the right track.
Back to the story. The main guard is the first place to start and then slowly each piece is added and the whole piece is filed back, cleaned up and polished and then the next piece is added and in this way even the hard to reach areas of a finished piece should be reasonably well finished - it avoids you 'painting yourself into a corner'. Saying that though, this sword is a actually quite roughly made and a number of the guard welds are fracturing and not great and a deal of the file work has left lots of cut marks. This is not at all unusual in original pieces; we just look at them through rose tinted glasses and think they were all perfect - they weren't.
The next stage will be to make the pommel and then I will go back to finishing the bars on the guard. One is spoken for and the other will be available.
The interaction between the pommel and the guard is sensitive and so if I were to carry on with tgeuard at this stage would most likely leave the guard not quite right.
More progress next week and I hope you like it so far.
Tod


Original sword

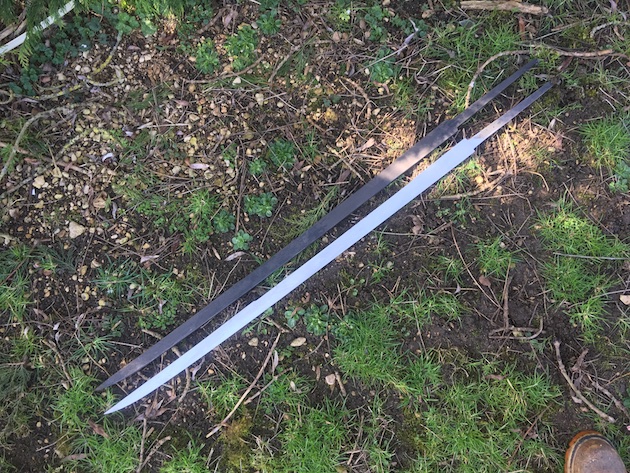
Profile cut at 10mm thick and one tapered down to correct thickness

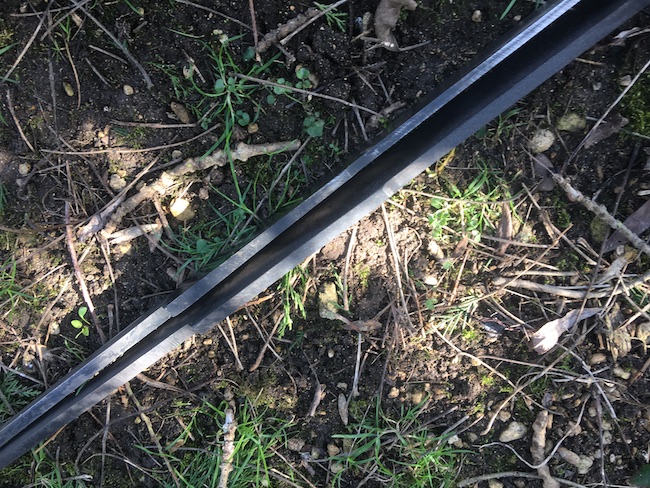
Showing the drastic thickness reduction over the first 15cm

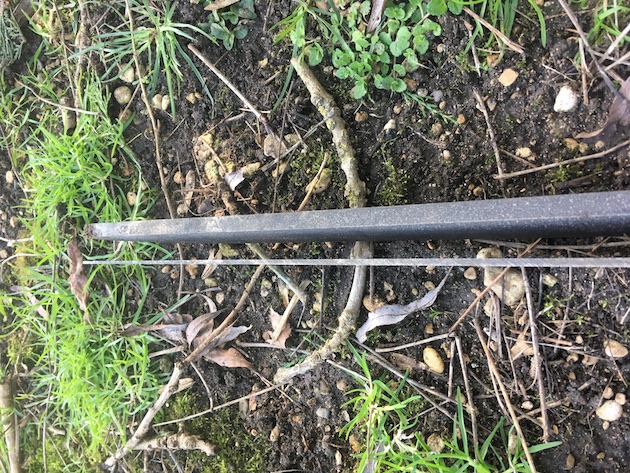
Showing the reduction of the tip thickness

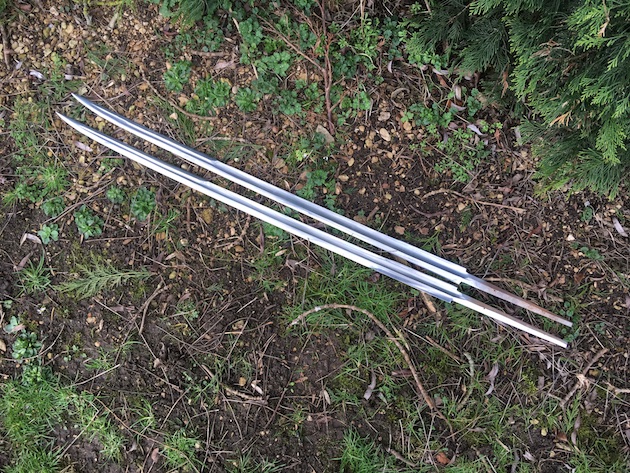
Sabre blades ground

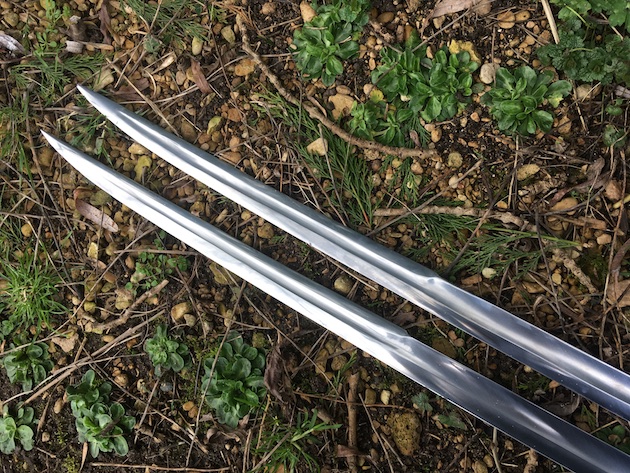
Ground tips

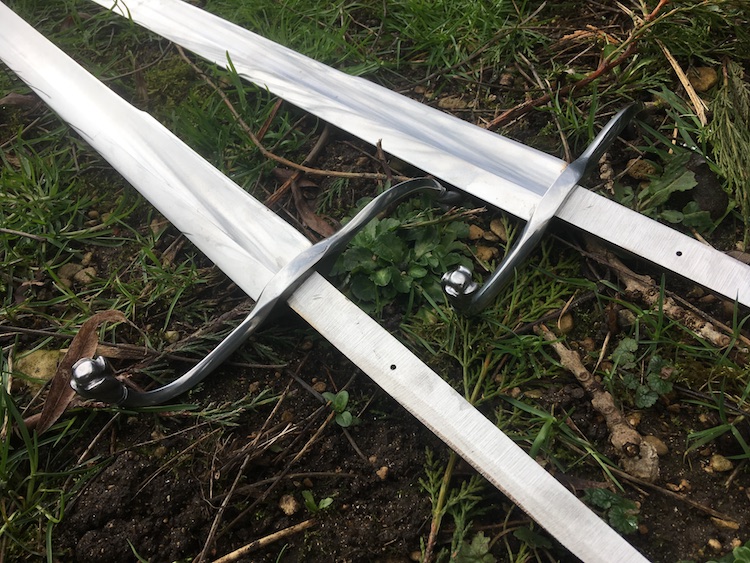
The guards start

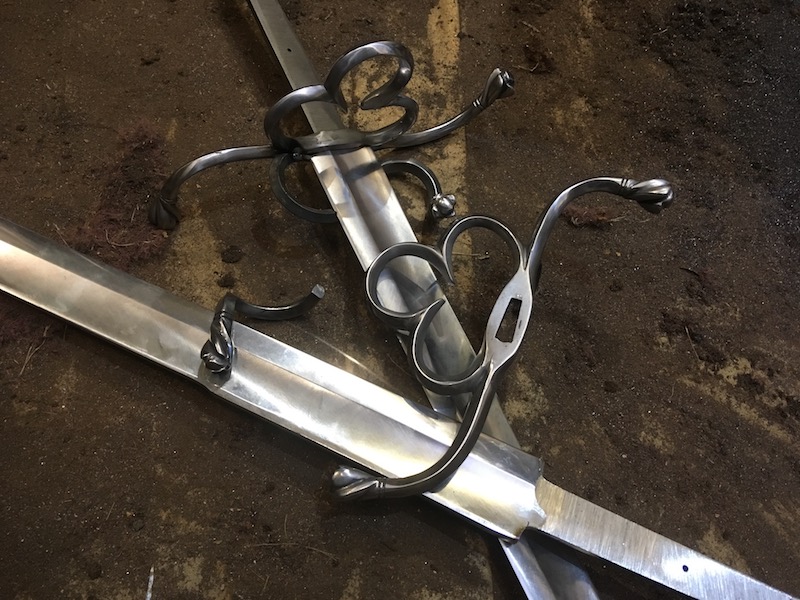
Guards piece by piece

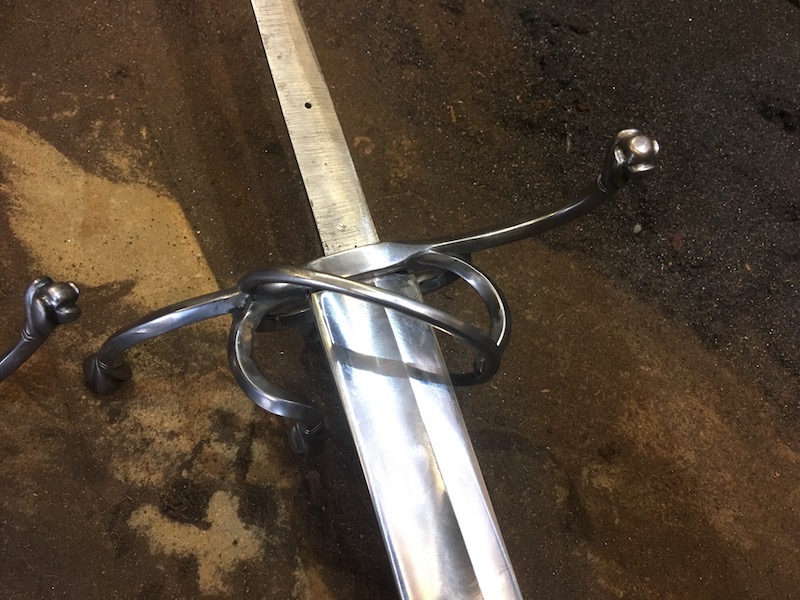

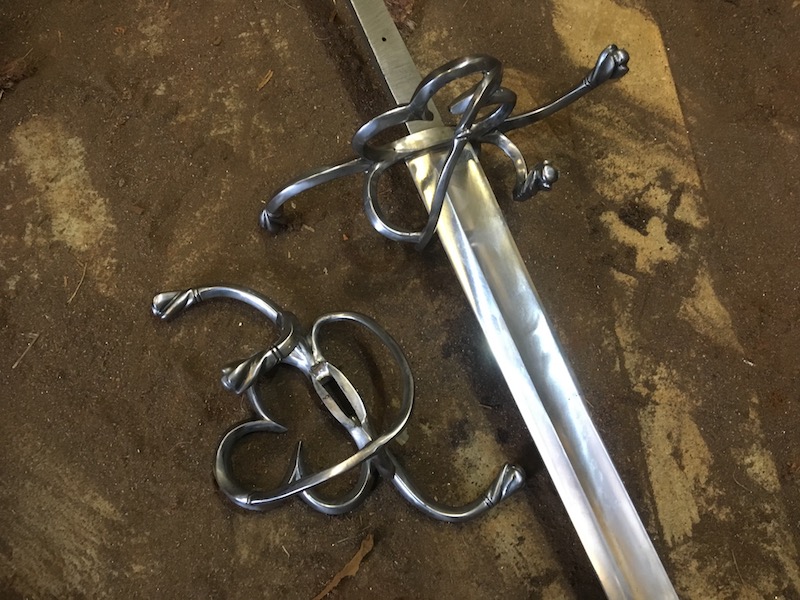
All the lower guard elements in place