After seeing Boris Bedrosov's longsword project, I get motivated and clear the dust off my grinder to start working on my first blade project.
It is based off this image, the second dagger on below:
[ Linked Image ]
Current progress:
[ Linked Image ]
[ Linked Image ]
[ Linked Image ]
Steel type: Carbon Steel 1045
Thickness: 4.5cm
As this is my first blade progress, I'd like to see what's you guys thought, or advice that I can learn from.
Last edited by Foong Chen Hong on Sat 12 Oct, 2013 11:24 am; edited 2 times in total
I don't think your pics made it. Give them another try............mcm
Mark Moore wrote: |
I don't think your pics made it. Give them another try............mcm |
I dunno why my pic doesn't work with img tag here, the link work fine with img tag in other forum though...
Don't know why they aren't showing up. Maybe try photobucket....some servers just don't seem to work on here.
Here are the direct links to the pictures above:
https://fbcdn-sphotos-d-a.akamaihd.net/hphotos-ak-frc3/1383146_10200623184653757_500865721_n.jpg
https://fbcdn-sphotos-g-a.akamaihd.net/hphotos-ak-prn1/1383874_10200623184773760_1213298357_n.jpg
https://fbcdn-sphotos-a-a.akamaihd.net/hphotos-ak-prn2/1393892_10200623184693758_1768425918_n.jpg
and the original:
https://fbcdn-sphotos-b-a.akamaihd.net/hphotos-ak-prn2/1381689_10200604015534541_1231672840_n.jpg
Keep us posted. Looking forward to seeing how this turns out.
Here are the direct links to the pictures above:
https://fbcdn-sphotos-d-a.akamaihd.net/hphotos-ak-frc3/1383146_10200623184653757_500865721_n.jpg
https://fbcdn-sphotos-g-a.akamaihd.net/hphotos-ak-prn1/1383874_10200623184773760_1213298357_n.jpg
https://fbcdn-sphotos-a-a.akamaihd.net/hphotos-ak-prn2/1393892_10200623184693758_1768425918_n.jpg
and the original:
https://fbcdn-sphotos-b-a.akamaihd.net/hphotos-ak-prn2/1381689_10200604015534541_1231672840_n.jpg
Keep us posted. Looking forward to seeing how this turns out.
Thanks, I change the host to imgur, which they work.
I also edited the first post with little more info.
I also edited the first post with little more info.
Well, not the best pictures but this doesn't matter anyway.
I would recommend you
* clamp the blank well by any means you've got - C-clamps, F-clamps, vice.... This is for your own safety first
** it's better to use thinner (1 mm) cutting disc instead of the standard 3 mm - the cutting goes faster and cleaner; the grinder works easier
*** in future avoid right angles at the blade / tang transition area, use round instead. In the past the tang was forged, not cut. I know, it's not so essential in short blades (like daggers), but in some future project you might ruin a good sword you've made just because this area is not correct
**** last but not least - wear personal protection - goggles, dust-mask, ear protection, gloves
I'm waiting to see this beauty finished.
And of course, you could ask anytime you want.
I would recommend you
* clamp the blank well by any means you've got - C-clamps, F-clamps, vice.... This is for your own safety first
** it's better to use thinner (1 mm) cutting disc instead of the standard 3 mm - the cutting goes faster and cleaner; the grinder works easier
*** in future avoid right angles at the blade / tang transition area, use round instead. In the past the tang was forged, not cut. I know, it's not so essential in short blades (like daggers), but in some future project you might ruin a good sword you've made just because this area is not correct
**** last but not least - wear personal protection - goggles, dust-mask, ear protection, gloves
I'm waiting to see this beauty finished.
And of course, you could ask anytime you want.
Foong Chen Hong wrote: |
After seeing Boris Bedrosov's longsword project, I get motivated and clear the dust off my grinder to start working on my first blade project.
It is based off this image, the second dagger on below: [ Linked Image ] Current progress: [ Linked Image ] [ Linked Image ] [ Linked Image ] Steel type: Carbon Steel 1045 Thickness: 4.5cm As this is my first blade progress, I'd like to see what's you guys thought, or advice that I can learn from. |
Maer agoreg (You have made well).... I'm also working on something of this nature - but lack the skill to actually form a blade. My approach - from commercial component offerings.... a Work in Progress (not yet wrapped)....
[ Linked Image ]
Not as authentic - I tend to do things like this :).
Boris Bedrosov wrote: |
Well, not the best pictures but this doesn't matter anyway.
I would recommend you * clamp the blank well by any means you've got - C-clamps, F-clamps, vice.... This is for your own safety first ** it's better to use thinner (1 mm) cutting disc instead of the standard 3 mm - the cutting goes faster and cleaner; the grinder works easier *** in future avoid right angles at the blade / tang transition area, use round instead. In the past the tang was forged, not cut. I know, it's not so essential in short blades (like daggers), but in some future project you might ruin a good sword you've made just because this area is not correct **** last but not least - wear personal protection - goggles, dust-mask, ear protection, gloves I'm waiting to see this beauty finished. And of course, you could ask anytime you want. |
By right angles you mean the tang is curved, right? I am trying to fix that.
Can you tell me any tip at thinning the blade at diamond grind?
Yep, I mean this (look at the bottom of the picture)
[ Linked Image ]
transitional area. It should be curved, not at right angle.
About the diamond cross-section:
* draw the center line of the blade (you should come to something like this)
[ Linked Image ]
** then comes the tricky part - you need to draw another center line, but this time over the thinner surface of your blade - where the cutting edge will be.
If you didn't make the distal taper so far, this step would be quite easy. If you did - you should take several measurement of the thickness alongside the blade and to calculate and mark the middle.
If this is the first blade you make, I personally would recommend you not to make distal taper - then the blade is fairly easy to make, but the experience you would get is invaluable.
*** then you should grind all metal between these to lines. Please, work slow and carefully; you would feel by yourself how to do this exactly. The easiest way is to hold the tool at some angle, but there are some other tricks that are very difficult to be explained - they should be exactly felt.
[ Linked Image ]
transitional area. It should be curved, not at right angle.
About the diamond cross-section:
* draw the center line of the blade (you should come to something like this)
[ Linked Image ]
** then comes the tricky part - you need to draw another center line, but this time over the thinner surface of your blade - where the cutting edge will be.
If you didn't make the distal taper so far, this step would be quite easy. If you did - you should take several measurement of the thickness alongside the blade and to calculate and mark the middle.
If this is the first blade you make, I personally would recommend you not to make distal taper - then the blade is fairly easy to make, but the experience you would get is invaluable.
*** then you should grind all metal between these to lines. Please, work slow and carefully; you would feel by yourself how to do this exactly. The easiest way is to hold the tool at some angle, but there are some other tricks that are very difficult to be explained - they should be exactly felt.
Boris Bedrosov wrote: |
If you didn't make the distal taper so far, this step would be quite easy. If you did - you should take several measurement of the thickness alongside the blade and to calculate and mark the middle. If this is the first blade you make, I personally would recommend you not to make distal taper - then the blade is fairly easy to make, but the experience you would get is invaluable. |
as a note, I learnt from a friend that its actually really simple to make a distal grind on a diamond section, without having to do any grinding to the flats beforehand
here's a little picture of what I mean - the angles are exaggerated for clarity.
what you do is you grind past the midline - so you mark your line out maybe 5-6mm off to one side, and grind that edge on each side of the blade.
then you mark the midline on the blade, and grind the other side. because you've ground past the midline, when you grind back to there, you're removing material, and the thickness is reduced - distal taper.
I love geometry - its fascinating :)

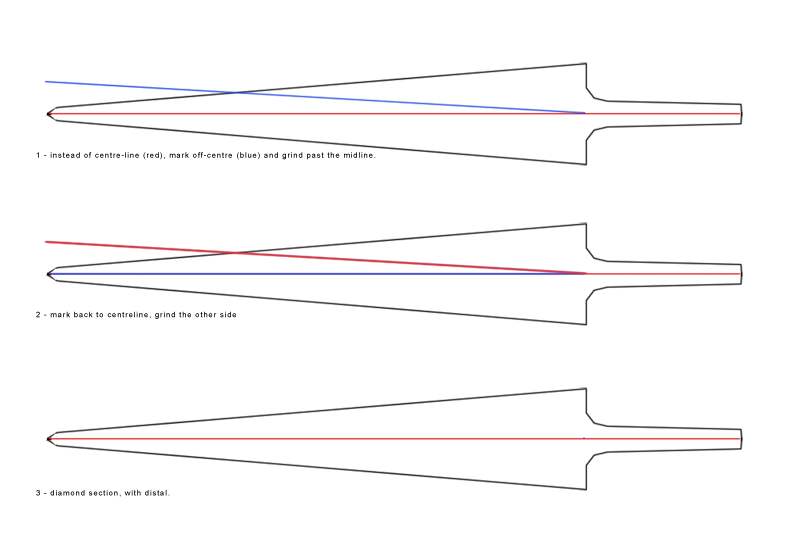
Thanks for these tips and advice, I will show the shape when I done cutting the final shape out
After hours of cutting and grinding, this is how it end up. The blade and tang is indeed curved, my grave mistake, but it is my first time doing this and nothing else I could do but move on.
[ Linked Image ]
[ Linked Image ]
[ Linked Image ]
[ Linked Image ]
[ Linked Image ]
4.5 CM thick.
(want to try out James's method but afraid failing.
[ Linked Image ]
[ Linked Image ]
[ Linked Image ]
[ Linked Image ]
[ Linked Image ]
4.5 CM thick.
(want to try out James's method but afraid failing.
Page 1 of 1
You cannot post new topics in this forumYou cannot reply to topics in this forum
You cannot edit your posts in this forum
You cannot delete your posts in this forum
You cannot vote in polls in this forum
You cannot attach files in this forum
You can download files in this forum
All contents © Copyright 2003-2006 myArmoury.com All rights reserved
Discussion forums powered by phpBB © The phpBB Group
Switch to the Full-featured Version of the forum
Discussion forums powered by phpBB © The phpBB Group
Switch to the Full-featured Version of the forum