I started out with a fairly popular piece, a Windlass Type XIV. I acquired the sword from the Museum Replicas showroom on the discounted rack for only $100. The only problems with the sword were a loose crossguard and some slight rust. This sword has been around for several years now, and it's a great little blade for the money. One on the things which I have always found to be a bother on the Windlass Type XIV is how acute the angles are on the piece. The edges are far too sharp, which is a problem with many inexpensive production blades. These 90 degree edges give the sword a mechanical stamped appearance, whereas many quality hand-crafted swords bear edges which are every so slighlty rounded.
First, let's look at a standard Windlass Type XIV below with no alterations to the angles:
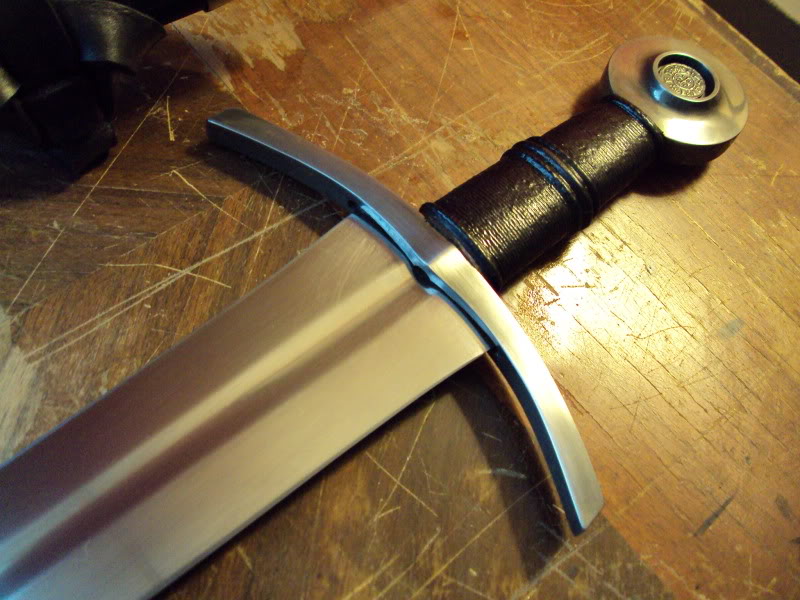
Now, onto changing the product...
On the melt job sword, I tightened the guard, removed the stock grip, and reprofiled the grip core to a smoother shape. I then worked with a file to reprofile all of the hard edges on the sword, giving them a slight bevel. This bevel is more pronounced at the ends of the cross to make it look a bit more dramatic. I then finished the edges with various grits of sanding, until I had worked the finish to an even 600 grit. The blade surface and all of the flat surfaces on the sword were also finished to 600 grit.
The grip was given two central oversized risers to enhance the whole theme of the sword, which is a gently, slightly noticable melted look. Even though the difference is slight, the overall aesthetic of the sword has been greatly improved to give it a look of much higher quality. This is my personal Windlass Type XIV, and I really like the overall results.
I look forward on being able to try melt jobs on some other swords in the near future! :)
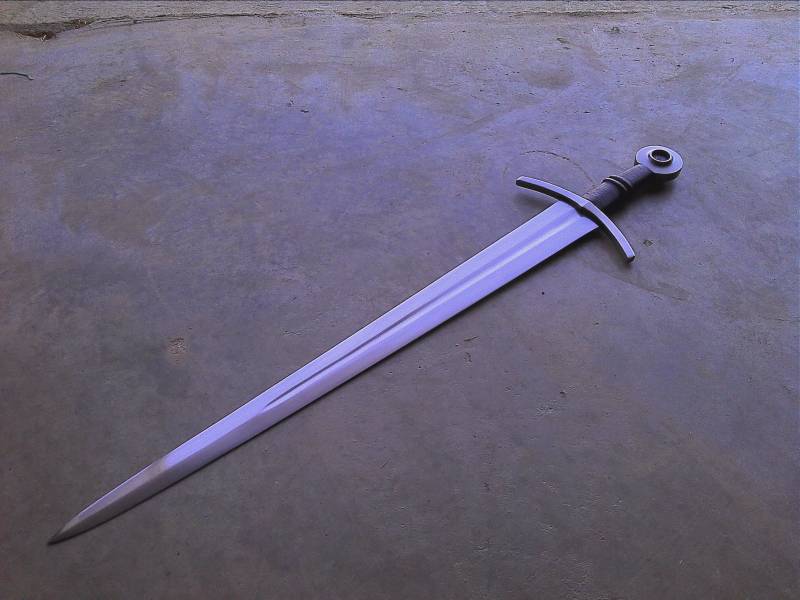
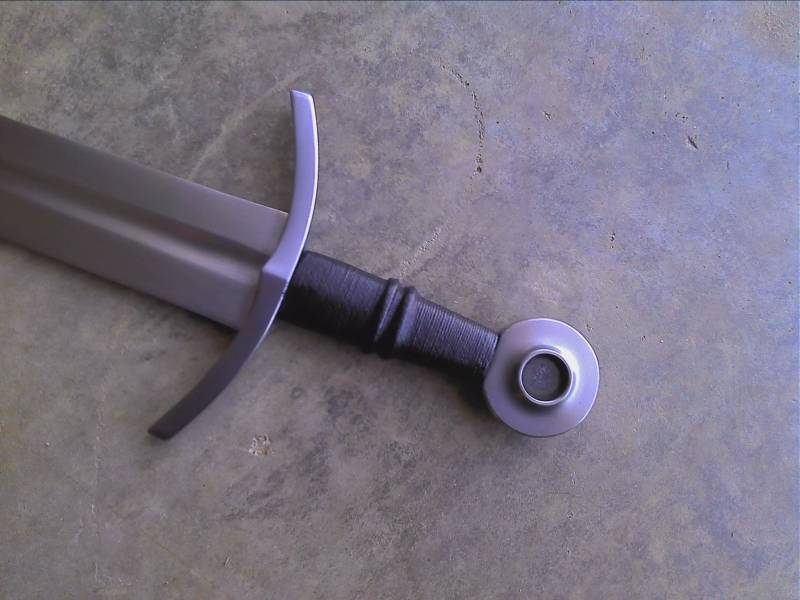
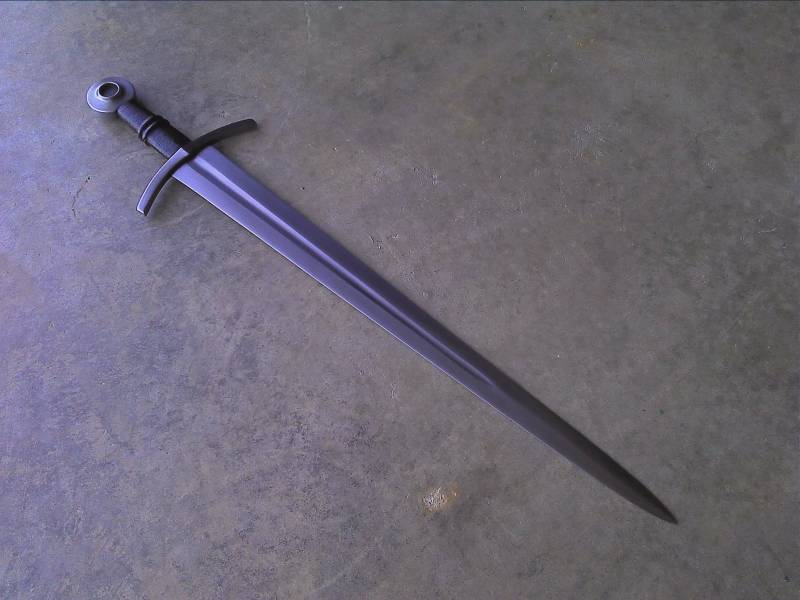
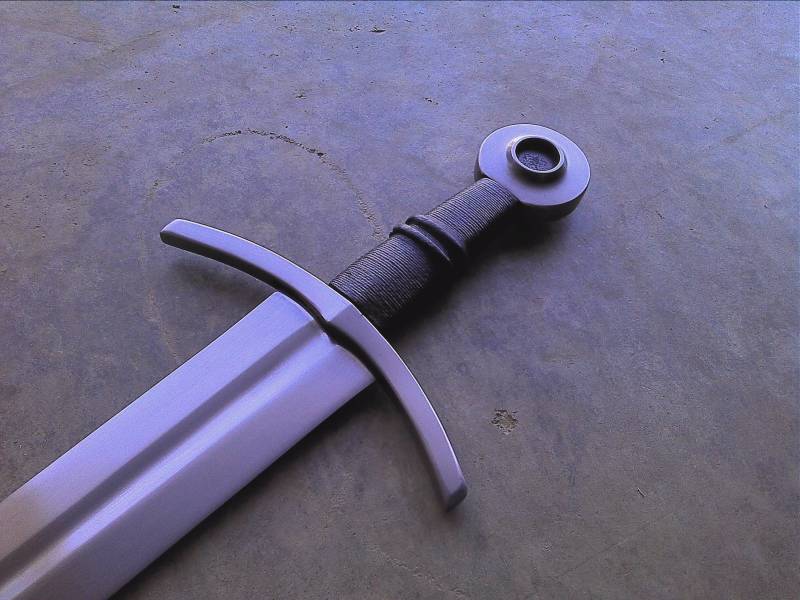
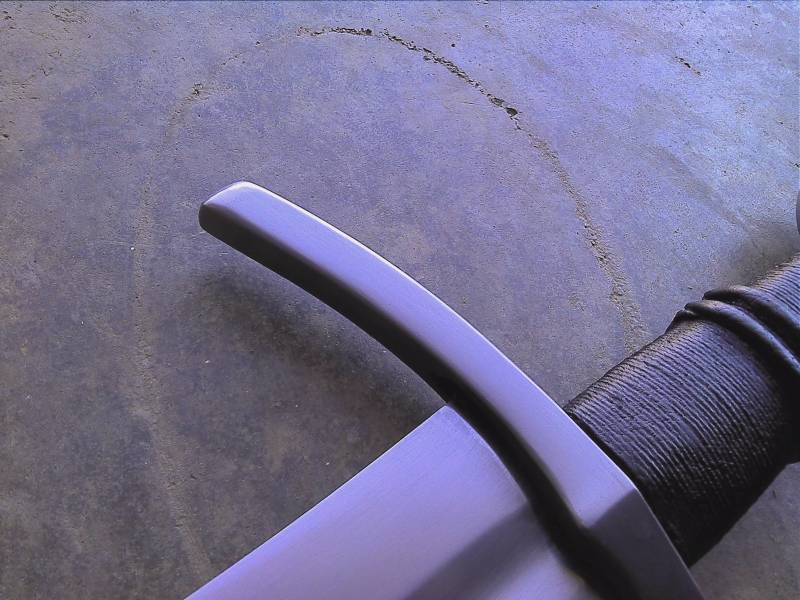
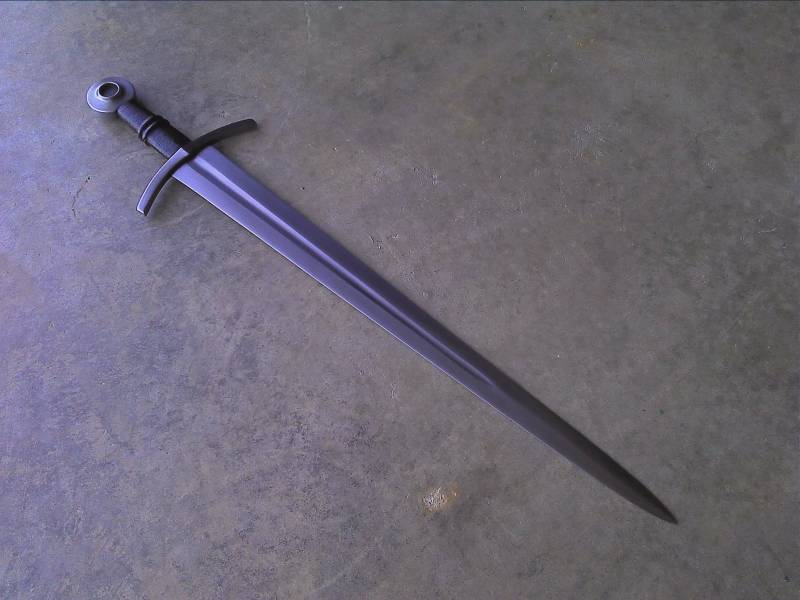
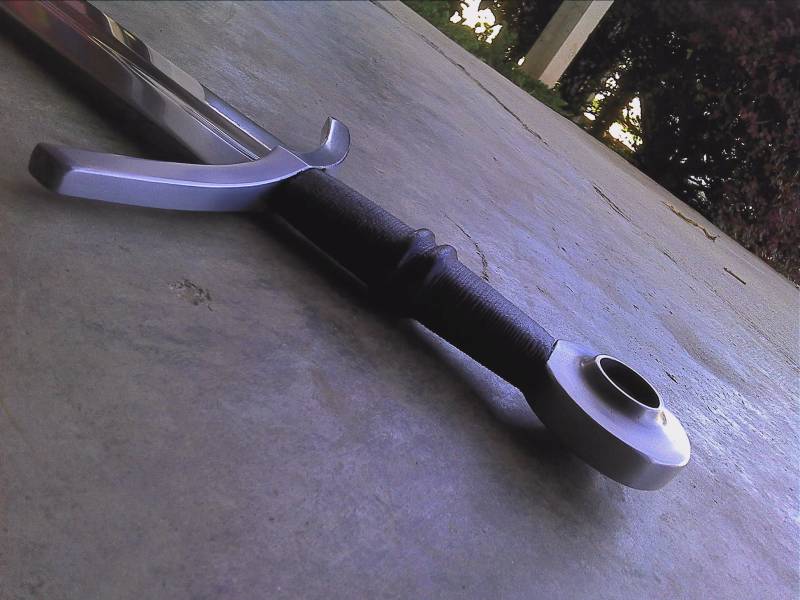
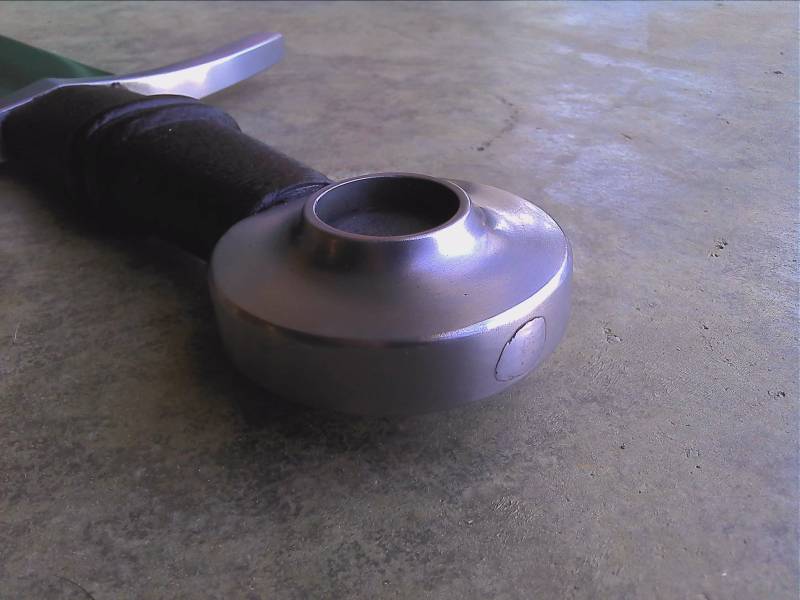