an uncle of mine is an amateur historian for WWII items - he had a m1908 bayonet reproduction that was shipped a little broken - so he told me to take it and see if i could make anything of it.
first step was to find out what kind of steel it might be. by spark testing i'm rather sure it's a high carbon steel, not the greatest quality but it at least is easy to work with. secondly by file testing the steel - i was surprised to see my file slip off of the steel and not bit into it. taking a triangle file i wanted to see how hard the metal was, and noticed it's not the best - but it was pretty tuff.
as broke apart the knife, the only truly broken section was the 'quillon' block, it didn't hold tightly to the tang and just slipped right off. i could have just drilled and riveted it back together but my mind was already going on a different path with the project.
i noticed a small dilemma, the blade had looked as it was either welded or press fitted to the handel of the knife, i could see what i though was a small ridge and taking no chances i cut the handel off. i didn't want to take any chances of the blade snapping free if anyone would be horsing around with it later (namely me). i didn't really care for a blade over 20 inches anyway.
using a bench sander with a 40 grit belt, i first gave the blade a little bit of distal taper. the blade also had hammer marks, where it look as if this blade was just stamped out of a blank. so i redressed the bevels of the false edge and 'true' edge. and now there's little distortion that you can see in the blade.
for the hilt i wanted to so something different. i had remembered seeing photos of work from 'todd's stuff" of german hunting knife sets with the big fighter knife having a little shell guard on them. so i though i would give it a try. now i don't have a forge . . . yet . . . so i had to make the quillon and its block out of flat steel. i would find in nearly impossible to cut a quillon block from a block of steel without a forge to drift it, or a mill to cut it out.
the only material i had laying around was 16 gage hot rolled steel laying around. i challenged myself and cold cut all the hilt pieces with a hammer and chisel. with patients, and a good arm, it worked out really well. i just had to grind off where the steel sheared and it looks just a precision cut.
the hard part was that i didn't make the shell guard and quillons from the same piece, i made them sperate. mostly because the shell i did make is really big like everything else on this knife. in order to give the guard a flush look, i cut out the opposing sections so that when they lay together, they look like one sheet of metal.
the bending of the guards was probably the most frustrating. i don't have a torch - and if you think a same propane pluming torch will get the steel hot enough to bend it, if won't - i tried - so it was just a vise and the biggest crescent wrench i could find and i worked the bends in. once i did the bends, i worked on the file work of the guards, it came out o.k. so far. i keep telling myself that they still look a little amateur because their not yet polished in any way.
the material i choose for the grip was just about as hard to work with as the steel. i have a silver maple tree growing in the back yard, some years ago i trimmed it back and kept most of the wood for fire wood. i had a few smaller logs laying around and decided to use it. well i should have remembered that maple is harder than oak once its dried. the log laughed at my table saw and attempted to throw it across the floor. i had to adjust my blade depth to 16th of an inch at a time to make my boards.
i wanted to use the maple because it will show really crisp lines on the wood if i decided to do a wood carving on it. and should be tuff. usually when i make a knife i make a lower guard to protect the grip material. but for this one i thinking on using the maple and a little red oak i have left over.
as i was working on the knife, one day i told myself 'this thing is turing out to be colossal.' and so i dubbed the project with the name Colossus. pictured below i have the key points of the work coming together. it doesn't look like it belongs to any period to the trained eye, but i could see it in bud - k with a 18th century pirate sticker title. :D
i'm open to any suggestions of how to make it look a little more authentic, or if anyone just wants to critique my work up to this point.

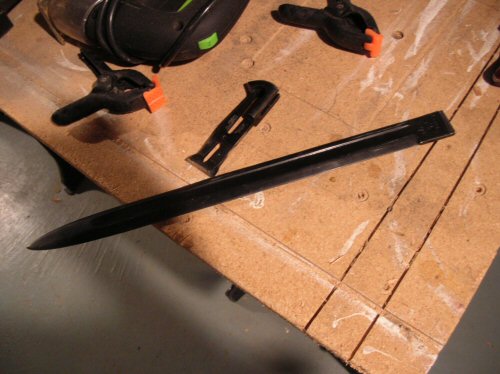
here i have the blade cut from the handel. the blade alone is around 16in

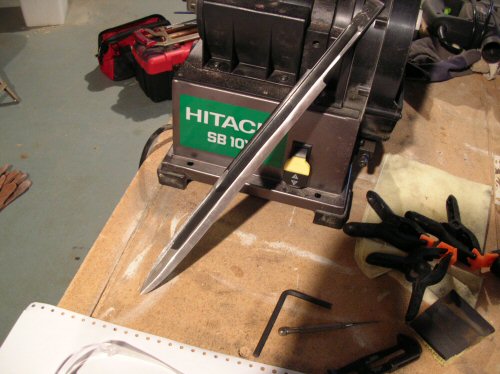
these are details of the work for the new distal taper, and rebeveling the edges.

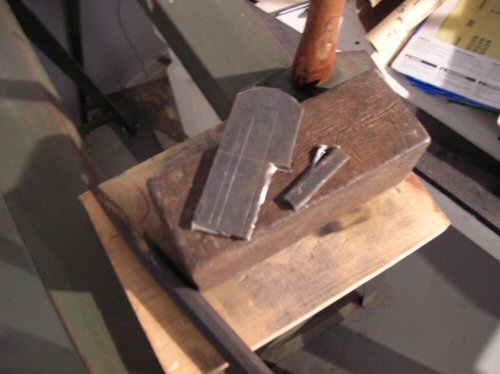
cutting soft steel with a chisel is not as hard as it looks. though i do recomend that you hammer on something solid. what i have there is an old brick of steel that i had laying around my grandfathers house that he used to use to straighten nails out o

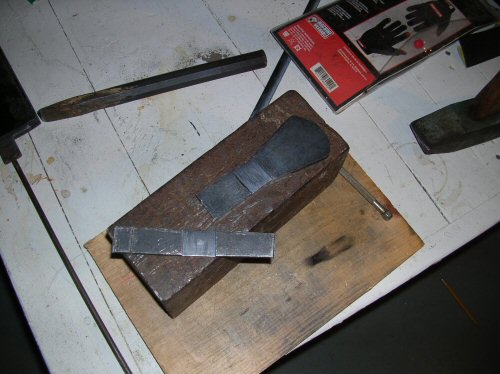
this is the fitting i made for the guards to sit on top of each other. quite tricky to pull off, and easier in carpentry.

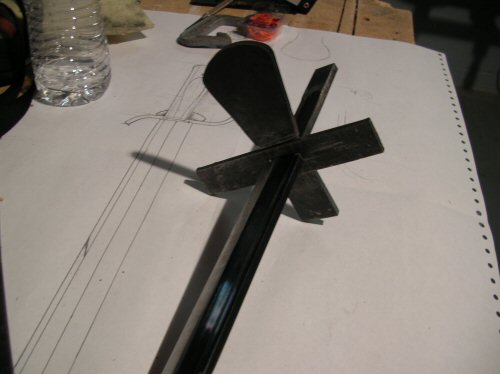
here are the guards fit together

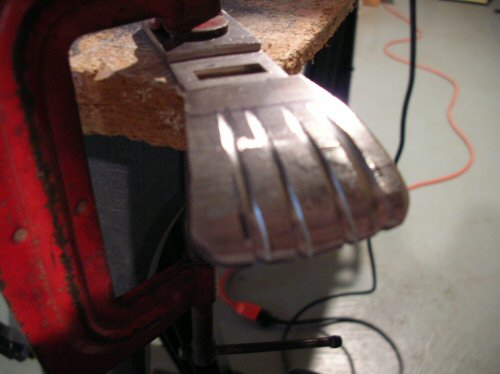
to bend this part took nearly all the mussle my little body could muster. but where there is will there is a way.

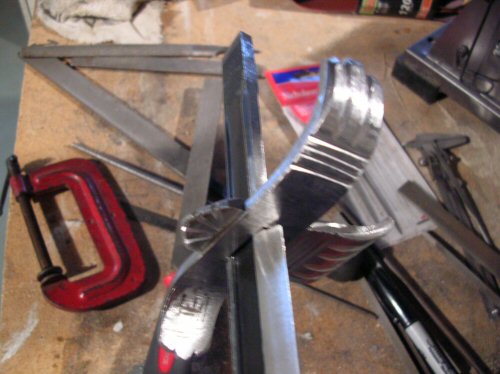
this is just a little more of the file work. i though about repeating the shell look, but it still feels like it needs more shape somewhere.

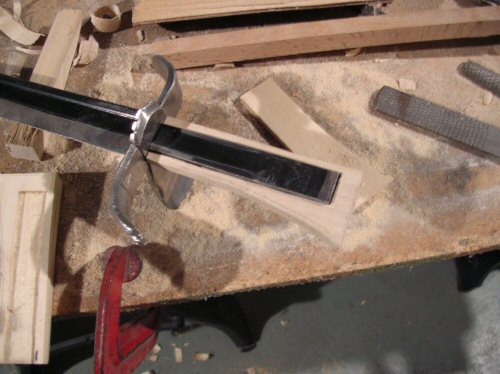
even though it would be quicker to use power tools i often turn away from them for the traditional chisel. but when working with mapel - make sure you have a hammer with that chisel.