Is the pattern of the billet in the picture below historical for the european pattern welding, migration era to 9th century?
http://www.alabamadamascussteel.com/servlet/Detail?no=15
Good question. If the steel was created in the wootz fashion- combining wrought iron, iron ore, charcoal, and glass in a crucible and then heating in a furnace- the pieces of steel that separates from the slags could then be forged together into ingots, ingots into billets, then forged into blades; I would think such a pattern could exist but I haven't seen any extant examples similar to your link. Of course, this is just the musings of an enthusiast and certainly not backed by much training or education. And the obvious question is why couldn't, or wouldn't the smiths of that period be able create patterns as we do today?
Wootz steel was traded to West and North so that part is plausible. And the pattern welding artists were not inferior to today's I would dare to say, but I still wondered if any body has seen something similar on a historical blade...
Edit: The pattern in the link was made with folding, so why would wootz steel exactly be needed for such pattern? Maybe I'm missing something...
Edit: The pattern in the link was made with folding, so why would wootz steel exactly be needed for such pattern? Maybe I'm missing something...
Luka Borscak wrote: |
Edit: The pattern in the link was made with folding, so why would wootz steel exactly be needed for such pattern? Maybe I'm missing something... |
It isn't exactly required, I was using it as an example. I should have used "for example" or something similar.
The pattern is not close to Wootz steel and I don't recall seeing this type of pattern in the research that I have been doing.
Also to the best of my knowledge, wootz is forged at a very low temperature and there is no folding involved. If you get a good ingot out of the crucible there is no need for folding since you are dealing with a clean homogeneous steel.
Also to the best of my knowledge #2, many of the techniques that modern makers us to bring out patterns can involve a lot of material loss. Since back when swords were being made and used material was very expensive, I doubt that they would have used techniques that relied on too much on removing material. So I would lean more towards the wouldn't rather then couldn't.
But I will let someone who knows more elaborate if needed.
Also to the best of my knowledge, wootz is forged at a very low temperature and there is no folding involved. If you get a good ingot out of the crucible there is no need for folding since you are dealing with a clean homogeneous steel.
Also to the best of my knowledge #2, many of the techniques that modern makers us to bring out patterns can involve a lot of material loss. Since back when swords were being made and used material was very expensive, I doubt that they would have used techniques that relied on too much on removing material. So I would lean more towards the wouldn't rather then couldn't.
But I will let someone who knows more elaborate if needed.
"Is the pattern of the billet in the picture below historical for the european pattern welding, migration era to 9th century?"
Not in my experience. During the 2nd to 4th centuries, northern European pattern welding seemed to go through an experimental phase with many ideas being tried out, but the most complicated patterns that I have seen are the diagonal latticework from the Danish bog finds. As time passes, the patterns tend to become more standardised and settle down, by the 6th and 7th centuries 'herringbone' and patterns like those on the Sutton Hoo sword seem to predominate. Occasionally, you get surprises, like the serpent pattern that appears on a late 6th century sword from West Heslerton, England. That is about it. Of course there may be more surprises out there. Pattern welded swords appear to fall from favour, increasingly from the late seventh century.
Paul
Not in my experience. During the 2nd to 4th centuries, northern European pattern welding seemed to go through an experimental phase with many ideas being tried out, but the most complicated patterns that I have seen are the diagonal latticework from the Danish bog finds. As time passes, the patterns tend to become more standardised and settle down, by the 6th and 7th centuries 'herringbone' and patterns like those on the Sutton Hoo sword seem to predominate. Occasionally, you get surprises, like the serpent pattern that appears on a late 6th century sword from West Heslerton, England. That is about it. Of course there may be more surprises out there. Pattern welded swords appear to fall from favour, increasingly from the late seventh century.
Paul
That is a modern pattern. It is sort of a cross between ladder and "snake eye". I am not completely sure how to do it. but am pretty certain that it starts out as a pure linear (multiple flat layers) type arrangement before it is manipulated to produce the final effect.
Historical pattern welding generally involved cores of twisted rods, and edges of layered steel. I theorize that this originally resulted from economy of materials (iron trade bars of varying quality, and the necessary process of drawing out traded ingots into rods or bars of suitable length) with resulting patterns being a circumstantial consequence rather than an end goal.
Historical pattern welding generally involved cores of twisted rods, and edges of layered steel. I theorize that this originally resulted from economy of materials (iron trade bars of varying quality, and the necessary process of drawing out traded ingots into rods or bars of suitable length) with resulting patterns being a circumstantial consequence rather than an end goal.
What Paul said. I also recall seeing a pattern sometimes called "small roses" somewhere.
More or less like this:
[ Linked Image ]
More or less like this:
[ Linked Image ]
There are some good articles and pictures about early pattern welding at the www.vikingsword.com site.
There are many published articles regarding wootz and other crucible steels as well. Too many to list really.
Daryl Meier www.meiersteel.com/ may seem familiar with some and often lost in modern history but has done some very fun and interesting patterns. The American Flag mosaic, maybe one of a kind but quite reproducible.
As to the Alabama cutlery site, I have a hunch that they are probably simply importing most of their billets, along with the camel bone ;) With rolling mills and hydraulic presses in hand, it can be a pretty easy way to go I guess.
For a hands on tutorial regarding more traditional build up of blade components, the work of Kevin Cashen is highlighted in an old and lengthy thread regarding the making of one blade in particular.
http://www.swordforum.com/forums/showthread.php?t=13809
Several of his blades I have seen and handled are anything but what we see with the trendy modern patterns that abound at budget pricing. Kevin explains his methodology fairly in depth and the articles at Viking Sword supplement a basic overview that can certainly be expanded on by the interested. Sorry for the reduced resolution and size but I'm on dial up and loading the big ones is just tedious.
Cheers
GC
These are of the Dennis Boas collection, out on the town in September 2005 with an A&A Danish axe and the dirk by Vince Evans.
There are many published articles regarding wootz and other crucible steels as well. Too many to list really.
Daryl Meier www.meiersteel.com/ may seem familiar with some and often lost in modern history but has done some very fun and interesting patterns. The American Flag mosaic, maybe one of a kind but quite reproducible.
As to the Alabama cutlery site, I have a hunch that they are probably simply importing most of their billets, along with the camel bone ;) With rolling mills and hydraulic presses in hand, it can be a pretty easy way to go I guess.
For a hands on tutorial regarding more traditional build up of blade components, the work of Kevin Cashen is highlighted in an old and lengthy thread regarding the making of one blade in particular.
http://www.swordforum.com/forums/showthread.php?t=13809
Several of his blades I have seen and handled are anything but what we see with the trendy modern patterns that abound at budget pricing. Kevin explains his methodology fairly in depth and the articles at Viking Sword supplement a basic overview that can certainly be expanded on by the interested. Sorry for the reduced resolution and size but I'm on dial up and loading the big ones is just tedious.
Cheers
GC
These are of the Dennis Boas collection, out on the town in September 2005 with an A&A Danish axe and the dirk by Vince Evans.
Glen A Cleeton wrote: |
As to the Alabama cutlery site, I have a hunch that they are probably simply importing most of their billets, along with the camel bone ;) |
They are not imports. The maker is not far from me, and a local knife maker I know sources some of his materials directly with the pattern welder who is a single specific individual. All billets start as stacked layers of flat ground stock. The quality of the billets, as verified from Rockwell testing of finished heat treated blades, is very good. I could track down his name if this is really necessary. I have a pocket knife blade made of some relatively uniquely patterned (included diagonal - candi cane type folds of the billet) manipulation that he did.

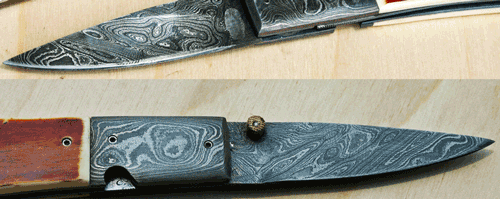
Hi Luka,
For me this Alabamadamascussteel looks much like the swedish Damasteel used for making the 2 swords on the picture, specially the single edged one.
This is stainless damascus made from powder.
Swords made by Anders Fällas from Uppsala (Sweden)
Jean
Attachment: 92.25 KB
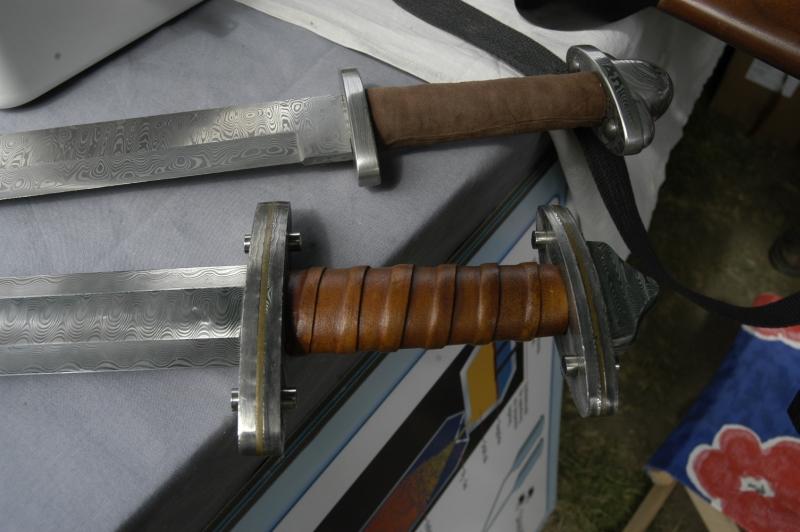
For me this Alabamadamascussteel looks much like the swedish Damasteel used for making the 2 swords on the picture, specially the single edged one.
This is stainless damascus made from powder.
Swords made by Anders Fällas from Uppsala (Sweden)
Jean

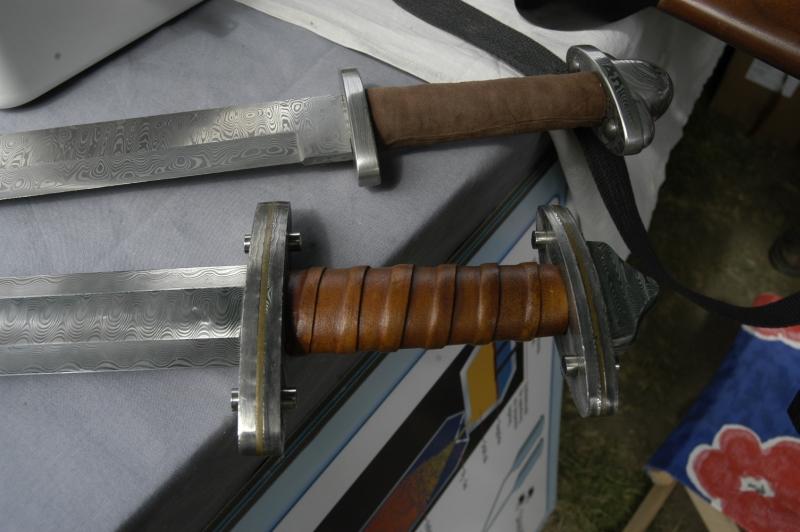
Last edited by Jean Le-Palud on Mon 21 Dec, 2009 6:59 am; edited 2 times in total
Jared Smith wrote: |
That is a modern pattern. It is sort of a cross between ladder and "snake eye". I am not completely sure how to do it. but am pretty certain that it starts out as a pure linear (multiple flat layers) type arrangement before it is manipulated to produce the final effect.
Historical pattern welding generally involved cores of twisted rods, and edges of layered steel. I theorize that this originally resulted from economy of materials (iron trade bars of varying quality, and the necessary process of drawing out traded ingots into rods or bars of suitable length) with resulting patterns being a circumstantial consequence rather than an end goal. |
Hi all...
I would agree with Jared on this one.
I saw a smith make "ladder" damascus once and the way he did it was to take a bar he had made where the layers were simply stacked. The then took an angle grinder and ground out grooves across the bar. Then he put the bar back in the forge and proceeded to hammer the grooves out. As the layers adjusted, moving material to fill the grooves, it produces the distortions.
I remember thinking when he ground out so much of the material of the blade making the grooves that this is not something that would appeal to an ancient smith who wanted to make the most of the steely iron he had on hand.
The fact that the ancients did not produce these ladder (grooves) or "fish eye" (hatching) patterns could possibly be used to argue that the patterns were not as much for looks as for functional (or perceived functional) purposes in the minds of those that made them. Because... with all the experimentation that was going on certainly they would have discovered this method yet chose not to use it... Or maybe next week some archeologist will discover a whole hoard of ladder patterned blades. ;) :D
take care
ks
Well, that will teach me to look at a site superficially.. I see the words Bear MGC knives and draw some conclusions. Then, a look at a twin site from India http://www.ancientarms.biz/servlet/StoreFront and I'm afraid I have to draw some more conclusions. No? that the Alabama boys may offer custom billets and that some associated are well versed and actively making nice blades, I don't doubt. That a lot of makers are using imported blades, I'm fairly certain.
Grinding the billet for a pattern reveal sounds familiar, along with a thread I would likly never find easily. That thread related some of the worked wootz blade patterns that were manipulated by indenting grooves to then further a pattern. Xs, iirc Then there are the noted chevron blades, which are quite spectacukar in person. The Higgins had one up in a gallery some years ago.
The candy cane effect is sometimes called Turkish twist and most of the knife world seems to have accepted damascus as a term for any pattern welding. My Evans bowie is twisted in such a fashion, although I refer to that one as Stripe. I have another more complicated one from Kevin in my files but that one not in hand, also twisted. At least I'm pretty sure that drop point is a Cashen, the work is fairly distinctly his (sambar and brass in symetric symphony).
Cheers
GC
Grinding the billet for a pattern reveal sounds familiar, along with a thread I would likly never find easily. That thread related some of the worked wootz blade patterns that were manipulated by indenting grooves to then further a pattern. Xs, iirc Then there are the noted chevron blades, which are quite spectacukar in person. The Higgins had one up in a gallery some years ago.
The candy cane effect is sometimes called Turkish twist and most of the knife world seems to have accepted damascus as a term for any pattern welding. My Evans bowie is twisted in such a fashion, although I refer to that one as Stripe. I have another more complicated one from Kevin in my files but that one not in hand, also twisted. At least I'm pretty sure that drop point is a Cashen, the work is fairly distinctly his (sambar and brass in symetric symphony).
Cheers
GC
Thanks for great replies and pictures guys! Chris from "Scorpion knives and bows" offered me to make a blade out of this steel for a very reasonable price and I thought it might be a good opportunity. I sent him an email about custom patterns to see how much that would cost...
Glen A Cleeton wrote: |
The candy cane effect is sometimes called Turkish twist and most of the knife world seems to have accepted damascus as a term for any pattern welding. My Evans bowie is twisted in such a fashion, although I refer to that one as Stripe. I have another more complicated one from Kevin in my files but that one not in hand, also twisted. At least I'm pretty sure that drop point is a Cashen, the work is fairly distinctly his (sambar and brass in symetric symphony). GC |
It has no firm basis, but "Turkish Twist" as used by makers is usually a multi-bar composite with some opposing twists. The pocket knife picture I showed was from a single bar. It was folded in "X" type crosses and welded several times prior to twisting the finished billet. This is not common as each crossing diagonal fold requires an individual weld before the multi-folded billet can be twisted. (A lot more time involved.)
The original subject of this post looks like the maker both made grooves and punched "eyes". (A cross between "Pool and Eye" and "Ladder". The grooves can be ground or simply hot chiseled. The eyes can be done with a simple punch while the bar is hot. Alternatively, depending upon how perfectly the maker maintained stratified layers, or did not maintain them, this could just result simply from "laddern patterning" if the layers are somewhat random to start with.
Well, I'm going to play a devil's advocate for a moment... ;) Doesn't the pattern in these pictures from Pierce's Swords of the Viking Age look much like alabama redneck skin (and maybe buckshot pattern too http://www.alabamadamascussteel.com/servlet/Detail?no=43 ) pattern I asked about in the first post? Of course, if I'm not seeing something crucial about these patterns, let me know... :)


Luka Borscak wrote: |
Well, I'm going to play a devil's advocate for a moment... ;) Doesn't the pattern in these pictures from Pierce's Swords of the Viking Age look much like alabama redneck skin (and maybe buckshot pattern too http://www.alabamadamascussteel.com/servlet/Detail?no=43 ) pattern I asked about in the first post? Of course, if I'm not seeing something crucial about these patterns, let me know... :) |
The fact that you sometimes see a lot of material removed is often the case when you have a sword consisting off a layer of torsion damast billets on each side, and even more if it's got an iron core. The thickness of the billets is therefore so thin, that cleaning up the surface after forging takes a relatively large %age of the billets away.
Can you please define the torsion damast? English is not my primary language, I don't really get what that would mean. Is this something else than pattern welding? These swords didn't look like that when they were new?
When you say Alabama steel is not torsion damast, does that mean the look of the Alabama pattern was encountered on historical blades but was product of a different process? Sorry for all the questions, but this sparked my interest quite a bit.
If such pattern was a product of a thin layer of damast on a mono steel blade and looked like that when new that would be a good thing for me because I know I can't get historical construction in my price range but I want something that will at least look historical. Than the difference between historical blade and mine would be that my blade is completely made of such damast while historical blade would have only a thin layer of it?
When you say Alabama steel is not torsion damast, does that mean the look of the Alabama pattern was encountered on historical blades but was product of a different process? Sorry for all the questions, but this sparked my interest quite a bit.
If such pattern was a product of a thin layer of damast on a mono steel blade and looked like that when new that would be a good thing for me because I know I can't get historical construction in my price range but I want something that will at least look historical. Than the difference between historical blade and mine would be that my blade is completely made of such damast while historical blade would have only a thin layer of it?
Luka Borscak wrote: |
Can you please define the torsion damast? English is not my primary language, I don't really get what that would mean. Is this something else than pattern welding? |
Quote: |
These swords didn't look like that when they were new? |
Of course (then they were a lot newer ;) ) You can see what they looked like by taking a look at Patrick Barta's site (though no examples of patterns with a large removal of material). He also has a nice article on patternwelding here: http://www.templ.net/english/making-blades.php
Quote: |
When you say Alabama steel is not torsion damast, does that mean the look of the Alabama pattern was encountered on historical blades but was product of a different process? |
Historical (at least in terms of early medieval) patternwelded blades did not look like the Alabama pattern. There may be some similarity to the untrained eye, but it's not quite the same.
Quote: |
Sorry for all the questions, but this sparked my interest quite a bit.
If such pattern was a product of a thin layer of damast on a mono steel blade and looked like that when new that would be a good thing for me because I know I can't get historical construction in my price range but I want something that will at least look historical. Than the difference between historical blade and mine would be that my blade is completely made of such damast while historical blade would have only a thin layer of it? |
The production process is different, so results in a different pattern. Along with that, the patternwelding is within the fullers, the edges were never patternwelded (piled, but not showing an obvious pattern, as you can see on Patrick Barta's examples). So even if you'd accept that both patterns looked similar enough, you'll still have to weld on the edges. And if you can do that, you can just as well do the pattern welding correct rather then putting a lot of effort in an incorrect pattern.
Hi Luka,
I don't know how to better to describe the information from those articles linked to www.vikingsword.com and Kevin's descriptions of his making that leaf blade. Torsional, twisting patterns occur when rods are forge welded while twisting. The Cashen swords displayed above show that. The core is then encased by the edges of finer steel to create the edges. Those as well will often display the patterns. What we see in most of these modern billets is then most often a product grinding the billets to shape, or profiled and beveled through forging. I hate to say it but that is what many regard as the most economical route for a display that doesn't really relate historical patterns at all. Windlass and Hanwei sell pattern welded viking swords, others do as well. Some appear so greasy/slimy as to have been possibly an etched pattern on plain billets. I don't know how prevalent that is but some will relate that their blades are simply etched to look like folded blades.
Here are some examples from Dark Sword Armory and they will sell such in the $1000-$1500 range. Some look obviously fitted out with duplicates of other sources for guards and pommels. The blades (to Me) look like blades that started as long billets and not the core and edge build type of construction of a more historical manner. Some similar, as mentioned, look as garish as if the pattern is simply painted/etched on plain steel. What one is not getting in these offerings are historic blade work but an anachronistic display of possibility. What they are (apparently) is fairly astonishing and appealing to some.
Faux or even fake, depending on perception.
For a budget sword that wants to make one feel like a viking, the current production offerings are probably the way to go. Those fellows down Texas way may well be able to offer stacked billet and worked blades but they are going to be pricy compared to simply starting with an available billet. That's not necessarily a horrible thing, simply not a historic forging process. Even John Lundemo sources out billet work for some quite fantastic looking and what some consider quite high art (I know I am very jealous of John's metal carving ability, fer instance). I thought enough of my Godfred from the first batches to then reblade it with another after the first broke. There is another consideration to think about.
Take a look again at the Ancient Arms available billets and you will see similar (or the source) for the Alabama gang.
Cheers
GC
I don't know how to better to describe the information from those articles linked to www.vikingsword.com and Kevin's descriptions of his making that leaf blade. Torsional, twisting patterns occur when rods are forge welded while twisting. The Cashen swords displayed above show that. The core is then encased by the edges of finer steel to create the edges. Those as well will often display the patterns. What we see in most of these modern billets is then most often a product grinding the billets to shape, or profiled and beveled through forging. I hate to say it but that is what many regard as the most economical route for a display that doesn't really relate historical patterns at all. Windlass and Hanwei sell pattern welded viking swords, others do as well. Some appear so greasy/slimy as to have been possibly an etched pattern on plain billets. I don't know how prevalent that is but some will relate that their blades are simply etched to look like folded blades.
Here are some examples from Dark Sword Armory and they will sell such in the $1000-$1500 range. Some look obviously fitted out with duplicates of other sources for guards and pommels. The blades (to Me) look like blades that started as long billets and not the core and edge build type of construction of a more historical manner. Some similar, as mentioned, look as garish as if the pattern is simply painted/etched on plain steel. What one is not getting in these offerings are historic blade work but an anachronistic display of possibility. What they are (apparently) is fairly astonishing and appealing to some.
Faux or even fake, depending on perception.
For a budget sword that wants to make one feel like a viking, the current production offerings are probably the way to go. Those fellows down Texas way may well be able to offer stacked billet and worked blades but they are going to be pricy compared to simply starting with an available billet. That's not necessarily a horrible thing, simply not a historic forging process. Even John Lundemo sources out billet work for some quite fantastic looking and what some consider quite high art (I know I am very jealous of John's metal carving ability, fer instance). I thought enough of my Godfred from the first batches to then reblade it with another after the first broke. There is another consideration to think about.
Take a look again at the Ancient Arms available billets and you will see similar (or the source) for the Alabama gang.
Cheers
GC
Page 1 of 2
You cannot post new topics in this forumYou cannot reply to topics in this forum
You cannot edit your posts in this forum
You cannot delete your posts in this forum
You cannot vote in polls in this forum
You cannot attach files in this forum
You can download files in this forum
All contents © Copyright 2003-2006 myArmoury.com All rights reserved
Discussion forums powered by phpBB © The phpBB Group
Switch to the Full-featured Version of the forum
Discussion forums powered by phpBB © The phpBB Group
Switch to the Full-featured Version of the forum