Workplace: not ideal...my computer desk, and alternatively the balcony when I got tired of eating wood dust.
Tools: the bare minimum (one hammer, one large chisel, various grade sand paper sheets, a wood rasp, a set of clamp...and a very noisy £10 jigsaw)
As usual, I had a hard time finding the appropriate materials in central London. In large DIY shops such as B&Q, no one seemed to have ever heard of "poplar wood" (as the largest DIY stores in the UK you would expect otherwise, but they were not helpful nor knowledgeable at all) In the end I settled for the best I could find in there: two boards of pine wood (Knowing very well that this choice wasn't the most suitable for a scabbard, but the dimension of those were spot on for this project). I just won't leave the sword to rest in it (it shouldn’t be kept in the scabbard for long period anyway) since I have read here that pine might eventually cause blade corrosion. Since I have also used regular PVA glue which can also cause corrosion, I will surely do what Justin King suggested in this tread http://www.myArmoury.com/talk/viewtopic.php?p=145264#145264 and use Tung oil to treat the inside of the scabbard.
Any advice on this issue is most welcome.
The rest was fairly straight forward. I traced the shape of the blade on both sides of the two halves of the wood “sandwich”, making sure I placed the blade the same way on all faces. I then traced a second line for each to mark the contours of the outer core using two pens instead of one while moving along the blade. Once this was done, I started hollowing the inside of the wood core. No doubt that this is the most painstaking part of the all thing. It is slow and noisy if (like me) you work in a flat. I had never used a chisel before and made my share of mistakes with it. I first tried to match closely the blade cross-section but gave this up quiet quickly since my much too large and flat chisel was quickly turning this into a nightmare…I finally aimed for an approximate match for the Crecy’s cross section (basically I did this scabbard as if the all blade was entirely of diamond cross section).
In the end, I hollowed the first half much too deeply. When closing both parts of the scabbard together to test the fit, it became obvious that great care will be needed when sanding down the outer core or I would surely pierce it (as Grey experienced here: http://www.myArmoury.com/talk/viewtopic.php?t...t=scabbard ). One the other hand, I would have to narrow the other half much more.
Once this was done, I tested the fit of the blade using clamps and to my great surprise; it was spot on right away. I could draw the sword very easily but yet hold it cross down and it would stay in the shealt (blind luck I’m sure!). I then glued the two halves together and cut out the scabbard using a jigsaw. Now the air in the room was so full of wood particles I had to retreat to the balcony with a wood rasp, sand paper and a bottle of wine and spent the next two or 3 hours flattening and shaping the outer core. As I told you I had to remove much more wood on one half than on the other…and having no power tools at hand this took a fair amount of time and efforts.
Below is how the scabbard currently looks like. Using clamps to compress a piece of leather around the wood core, I get a pretty good idea of how the scabbard will look once leather is applied. My main concern is to end up with a bulky looking scabbard. I may be able to narrow the all thing even further, but as you may have noticed on the picture of the scabbard mouth, one corner of the core is already getting very thin. Again, I am hoping for your advice on this point.
I have questions for the next steps too.
I’ve read here and there that the wood should be oiled (outer core and inside). What’s the purpose and what should I use to do that?
More importantly, I need advice about the leather: I have redone grips in the past, with 1 mm thick lamb skin. Now this will be too thin for that purpose. Looking at Brian BDK custom site in progress section, it is my impression that 2 mm leather would be more appropriate (cow, goat, sheep?). I will probably get the leather from Tod stuff other website here so feel free to advise on what you would pick (http://www.traditionalmaterials.co.uk/html/leathers.php) .
Finaly what kind of thread should I use for the sewing at the back?
I will post more as I go along.
Thanks in advance for your answers/comments and hope this post will help some to get started too :)
J
edit: what about glue btw? Should i use hide glue when applying the leather on the wood core?

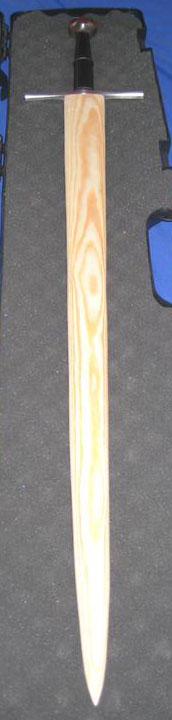

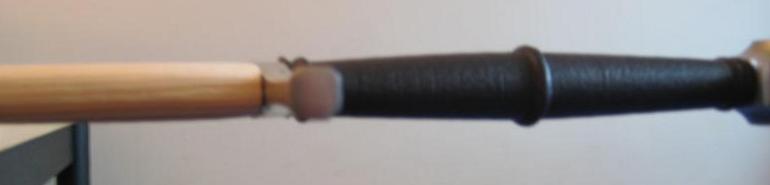

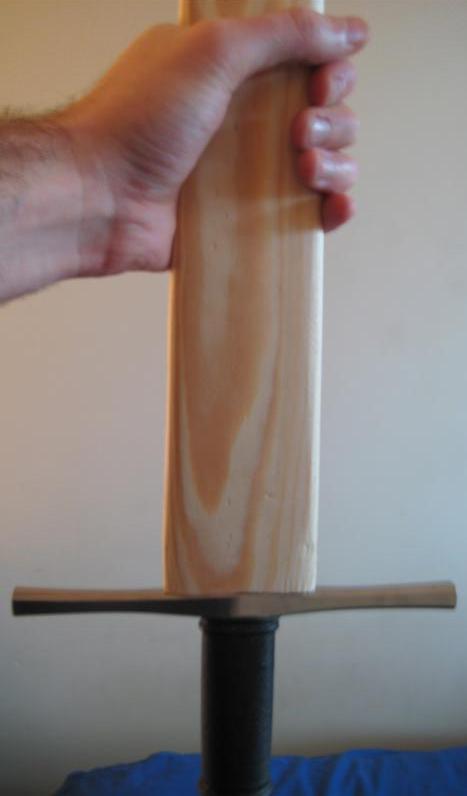

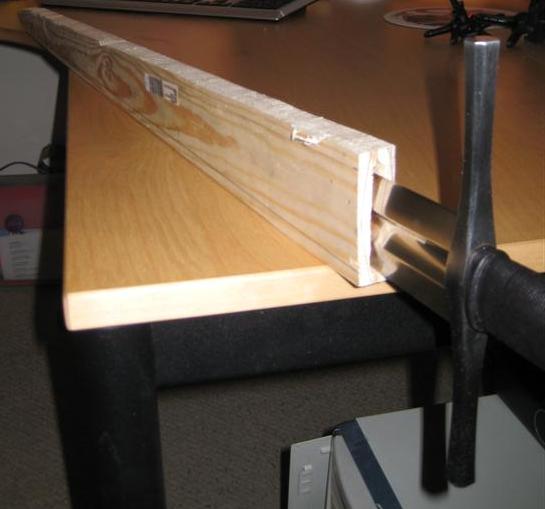

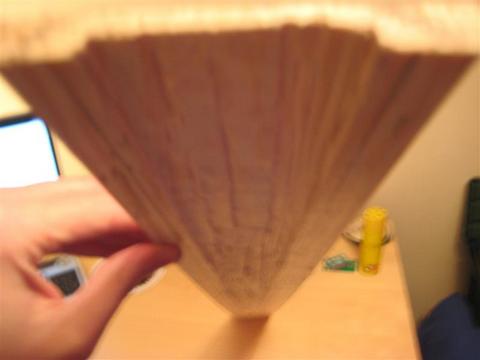