I purchased this sword over 10 years ago from a now defunct shop in Kansas called Skycastle Swords. They, along with their quasi partner Gypsy Madblade made some of the toughest swords I have ever had the pleasure to abuse! I originally purchased the sword sight unseen as a Viking style sword. As can be seen from the “before” pictures, it was anything but a Viking sword. Byzantine? Arabic? Andalusian? Blade geometry was all wrong, not to mention the guard, handle and pommel. But I could not send it back until after the weekend I received it, so I decided to give it a chance. Needless to say, at the end of the weekend I had no intention of sending my treasure back. The only problem as far as I was concerned was the weight. The sword was a beast, with all the swing finesse of a tree branch. It didn’t matter, I still loved it, but that began a 10+ year search for some one willing to add fullers to the Beast, and at the same time reduce some of the weight and terrible handling characteristics (the first picture is the sword before it was sent to Ollin)
During the ensuing 10year search I carried the sword to many medieval events, outings and fairs. But the weight was still the issue. The sword weighed in at just over 3-1/2 pounds, (3 pounds, 8 ounces) a hefty weight for even a hand-and-a-half sword. I cold called machine shops all over the country. No one would touch the project. So, I let the sword sit on the wall, taking it down for the occasional polishing, sharpening or outing to an event. Twice a year or so, I would again cold call machine shops or custom makers on the off chance they would take on the fullering project. It wasn’t until the Spring of this year, 2007, that I had the belatedly brilliant idea to ask the population at large on myArmoury.com if they could assist in my search. Nathan Robinson suggested Phoenix Metals, as they had done similar work for him in the past, but alas I got no response from them. Luckily, Jean Thibodeau responded to my “Off Topic” forum question and suggested Matt and Mark Gryzbowski at Ollin Sword Design. Before committing to the project, they wanted as much information about the sword as I could give them: steel used, blade geometry, take down ability. Unfortunately I could give them very little assistance. So, we agreed on a ballpark price subject to change after they handled the sword. Unfortunately the sword could not be disassembled, and so added to the final cost. (second picture is close up of hilt before any work was done)
I’m still not sure how the hilt is assembled. The steel, as far as I knew, was from a re-worked leaf spring. The blade cross section was hexagonal, with a large ricasso area. I think the over large ricasso helped in the long run with the project’s success, allowing for more work room on the blade. There was no distal taper to the blade. I opted out of adding a distal taper, as this would have added significantly to the final cost of the project. I won’t go into all of the technical work that Ollin put into the sword: instead here is the thread which best describes the process by which the fullers were added. Below is a picture of the sword with the fullers sketched in. The fullers were hand ground into the existing blade without any warp, discoloration or damage to the blade.
The one thing this picture cannot show is the flaws, which were always part of the blade – minor surface pitting, and irregular coloration from a so-so buffing job. Here is how Ollin Sword Design describes the process: “The fuller was put in by grinding against the appropriate diameter contact wheel on a grinder. That's about as clear as mud, isn't it.... There is a couple of pictures and a little write up of the process on this thread about one our project in the works. The final polish was done with hand sanding, which involves holding sandpaper on a block of wood that has been shaped to match the radius of the fuller.” Here is the link: http://www.myArmoury.com/talk/viewtopic.php?t...;start=100
Once the fullers were finished, the entire blade was beveled and then hand sanded. The resulting blade is now a flawless satin finish. No pitting or other imperfections appear on the blade. Unfortunately, the sanding and added fullers only reduced the weight by 3.5 ounces. This at least brought the beast down to a more manageable 3.5 pounds. The PoB was brought back an inch closer to the hilt, so the sword is a bit handier when swung. That being said, it will never be the agile single hand sword I hoped for, but remains the brute it always was – just a bit easier to wield.
Here is a picture of the finished sword, newly ground fullers, and re-beveled to maintain a consistent blade geometry. The entire project took a bit over a month, between sending the sword out and getting it back, with some technical emails sent back and forth. The final cost with shipping was $275.00 dollars. The end result is outstanding. A favorite sword was made better in every sense – the overall “look” is improved, its handling characteristics are improved; generally everything about the appearance and feel are improved, at what I feel is a very reasonable price. But the upshot is, my sword is more beautiful than ever, and I had a fantastic experience on this project from a highly skilled and professional organization. I can’t say enough good things about Matt and Mark Gryzbowski; from start to finish it has been a real pleasure working with them. Thanks again Matt and Mark, and I hope to do more business with you in the future – no higher praise to be sure. Here is the URL for those who would like to contact the Grysbowskis: http://ollinsworddesign.com/

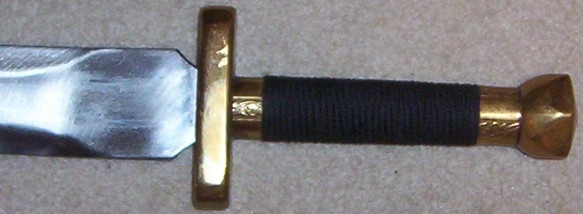
Close-up of hilt before work.

Picture of sword before start of project. [ Download ]

Picture of completed fullers and hand sanding. [ Download ]