OK, you guys have been really good about answering some of my questions. Now I have a couple of more for you. I really would like your opinions. I will gather them all up, and then make a decisions
First. We plan on making spears. All types. The shafts are expensive to ship, and you can buy them easily. 1 1/8th shafts can be purchased at various drapery and hardware stores. Almost always they are of poplar, which is a light, but very tough wood. Usually the shafts are fluted, sometimes spiralled. I've used them a lot, and have never had any problem, and have been pretty tough on them at times. The other choice is 1 inch diamter. This is readily available, and usually you can get it in various hardwoods, ash, hickory, oak, etc. (hickory not being very authentic, but very tough) Neither of these sizes are paticularly accurate, since spear shaft were in variour sizes and not standardized, but this 2006, and we have to standardise to a degree. The question is which would you like to see available, 1 /18th or 1 inch?
I am also checking out the possiblity of making a Viking Sword with a true blood eddy pattern, complete with high carbon steel edges. I know it would not be cheap, but right now I have no real information on cost. ACtually I am not sure it can be done, but am willing to give it a strong shot if there is any interest in a highly authentic Viking sword. Opinions?
Well, you can shave 1 1/8th" shafts to 1", but you can't really make 1" shafts bigger. :)
David Welch wrote: |
Well, you can shave 1 1/8th" shafts to 1", but you can't really make 1" shafts bigger. :) |
Well you can make a small shaft fit a larger socket by gluing cord to the shaft until it fits or just a little bigger and sanding it down to a close fit.
Since I'm not talking historically accurate assembly here and the cord would not be visible under the spear socket.
An 1/8" difference should be easy enough to compensate for and have a good strong assembly.
Now using a 3/4" shaft using this method for a 1 3/4" socket might work but would look sort of VERY wrong.
So, for me the larger size of socket would be my choice.
A large variety of types of spears and pollarms head of decent quality at somewhere between $100 to even $500 for a complex design would be at an attractive price point for me. I put $500 on the high side but this would have to be of very good design and quality materials, the lower end $100 would have to be at least capable of taking a good edge.
Jean Thibodeau wrote: |
Well you can make a small shaft fit a larger socket by gluing cord to the shaft until it fits or just a little bigger and sanding it down to a close fit. Since I'm not talking historically accurate assembly here and the cord would not be visible under the spear socket. An 1/8" difference should be easy enough to compensate for and have a good strong assembly. |
Just a note to say that I've done this in the past and it works surprisingly well.
Still, I'd prefer the smaller size socket, as it is easier to taper the shaft down to fit.
Greetings Hank,
First of all let me thank you sincerly for wanting to make spears! :D I think the market has been missing them for too long.
Second, I think you are asking what size to make the spearhead sockets, and let the customer find thier own shaft locally ,yes? If that is the case I would say make the sockets the size closest to historicaly accurate, even if it varies from model to model. If I am going to taper a shaft to fit anyway , 1/8th of an inch either way won't make much difference to me.
My biggest complaint with a couple of older MRL spears I have is that thier socket size was too big and as a result the whole spear was heavier than it should be because of the fatter shaft. Just a few years ago most "historicly accurate" replica swords were too heavy and balanced poorly compared to antiques. Today you can buy a sword that matches an antique in handling and appearance. Do we not want our spears up to the same level of quality and accuracy as our swords?
First of all let me thank you sincerly for wanting to make spears! :D I think the market has been missing them for too long.
Second, I think you are asking what size to make the spearhead sockets, and let the customer find thier own shaft locally ,yes? If that is the case I would say make the sockets the size closest to historicaly accurate, even if it varies from model to model. If I am going to taper a shaft to fit anyway , 1/8th of an inch either way won't make much difference to me.
My biggest complaint with a couple of older MRL spears I have is that thier socket size was too big and as a result the whole spear was heavier than it should be because of the fatter shaft. Just a few years ago most "historicly accurate" replica swords were too heavy and balanced poorly compared to antiques. Today you can buy a sword that matches an antique in handling and appearance. Do we not want our spears up to the same level of quality and accuracy as our swords?
For the types of spears that I like I would rather see the 1" sockets. Curtain rods seem too big and bulky to me.
Shane
Shane
My vote is for 1 1/8" socket for thrusting / hewing spears. The 1" socket would be fine for throwing spears. My personal preference is to err on the side of strength, so if the choice is strictly dichotomous, I'd go with the 1 1/8".
I'm glad to read that you're making spears. I think there is a real dearth of affordable, quality spears on the market.
Best wishes in this endeavor,
David
I'm glad to read that you're making spears. I think there is a real dearth of affordable, quality spears on the market.
Best wishes in this endeavor,
David
My vote is for the 1 1/8" socket. I do agree that a 1" socket for throwing spears is a good idea though.
Also, I would absolutely love to see you make a highly authentic Viking sword. Even if the price is high, I would really love to see it done.
-James
Also, I would absolutely love to see you make a highly authentic Viking sword. Even if the price is high, I would really love to see it done.
-James
Hank Reinhardt wrote: |
ACtually I am not sure it can be done, but am willing to give it a strong shot if there is any interest in a highly authentic Viking sword. Opinions? |
I would definitely be interested in highly authentic viking swords...though my personal cap I would be willing to spend on such a sword would be approx. $1,700. At this price, though, i would expect both authentic blade construction as well as authentic hilt/pommel contruction (two piece rivetted pommel).
Dustin
Unless the extra 1/8" provides a considerable increase in strength or durability, I've got to agree with Nathan - the smaller socket makes it easier for folks to use either haft.
Maybe if some of the jousters (running the games) or the WMA folks training in spear could comment it would be useful. I figure these are the folks who most likely have used (and possibly broken) their spears most extensively :)
Maybe if some of the jousters (running the games) or the WMA folks training in spear could comment it would be useful. I figure these are the folks who most likely have used (and possibly broken) their spears most extensively :)
In The Archaeology of Weapons, Oakeshott states that most of the Migration era spear shafts found in one of the bog deposits (I think it was Vimose, or something along those lines) were around one inch in diameter. That would incline me to go with the smaller diameter socket personally. Also, I was playing around with my MRL Long Bladed Hewing spear mounted on a one inch shaft, and that seemed plenty stout to me. To my mind, all that a 1 1/8" socket will really manage is to make the finished piece too heavy.
Just my two cents.
-Grey
Just my two cents.
-Grey
Hank Reinhardt wrote: |
I am also checking out the possiblity of making a Viking Sword with a true blood eddy pattern, complete with high carbon steel edges. I know it would not be cheap, but right now I have no real information on cost. ACtually I am not sure it can be done, but am willing to give it a strong shot if there is any interest in a highly authentic Viking sword. Opinions? |
Please do! I would love to see this piece, even if there's no way I'd be able to afford it :cry:
In the last month I have shaped and broke more javelin shafts than I even care to think about, but it has been a learning experience for sure. Tried a variety of woods as well and got to see some differences there. These javelin shafts were starting off at 3/4" and 7/8", being tapered a good bit to the small sockets. Poplar would not hold up to the stresses from being thrown, not to mention being lighter made it more tricky to balance. So really if strength is a concern for people they will see much more of a difference in picking the right wood to use over increasing shaft and socket sizes.
Shane
Shane
I'll be one of the holdouts for the larger diameter, at least on any later-period spear sockets (earlier than about 1450 is out of my area of interest). Although it's true that Froissart's Chronicles shows late 15th. c. spears with thin, apparently flexible hafts, almost all I'm seeing after ca. 1500 (in combat weapons, as opposed to ceremonial arms etc.) are massive military spears, ox tongues, early partisans and boar spears. These have very robust hafts and are mounted with a flush surface between haft and socket. In other words, the top of the haft is shaped to create a step on which the edge of the socket sits. It's possible this was done purely for aesthetic reasons, but that doesn't ring true to me. These are still weapons, even at this late date, and the examples shown here are relatively plain examples. If there must be a standard size for all periods, I suppose the smallest historically appropriate size is the most efficient ( :( ). It is easier to taper the 1.25" haft down to size than to build up a smaller haft in a way that isn't really stable or accurate.
In addition to World Peace, my great hope is that people will take more time to properly mount their spear heads. :lol: Taper that haft! Cut that step! Rivet or pin that socket!
Attachment: 28 KB
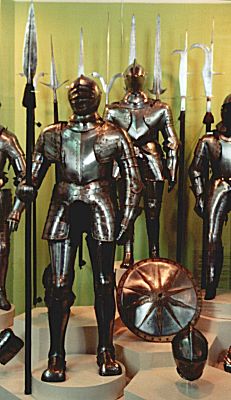
Attachment: 59.85 KB
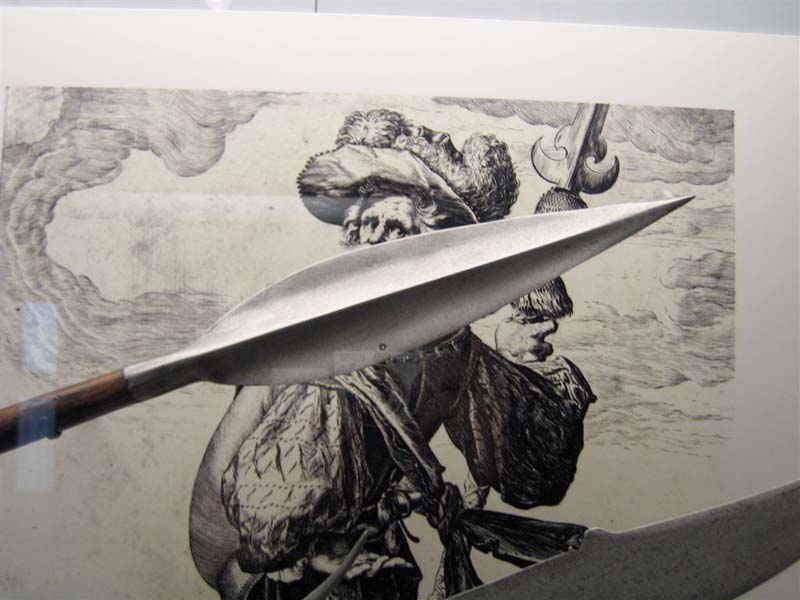
Attachment: 38.41 KB
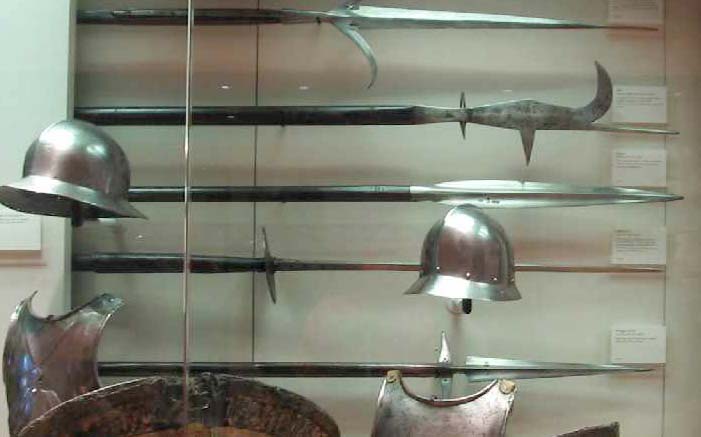
In addition to World Peace, my great hope is that people will take more time to properly mount their spear heads. :lol: Taper that haft! Cut that step! Rivet or pin that socket!

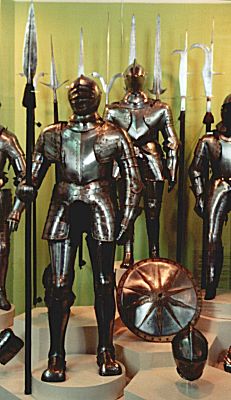

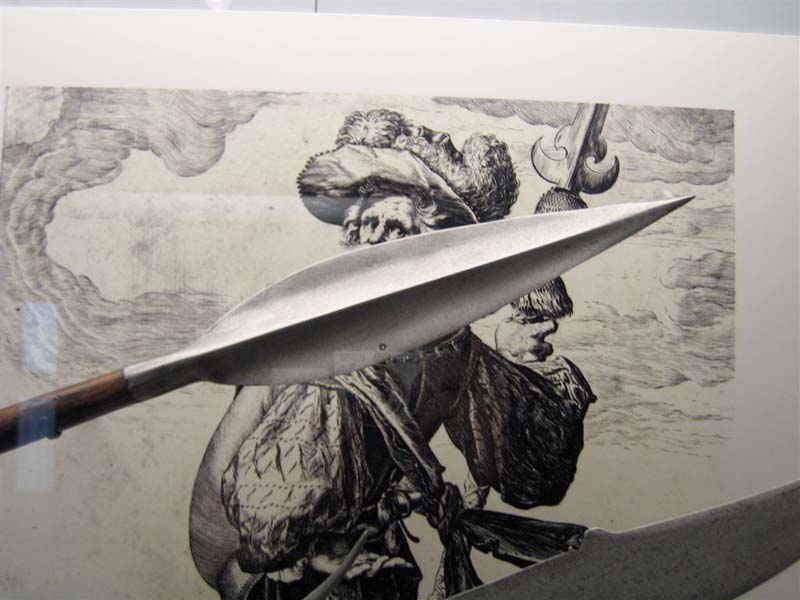

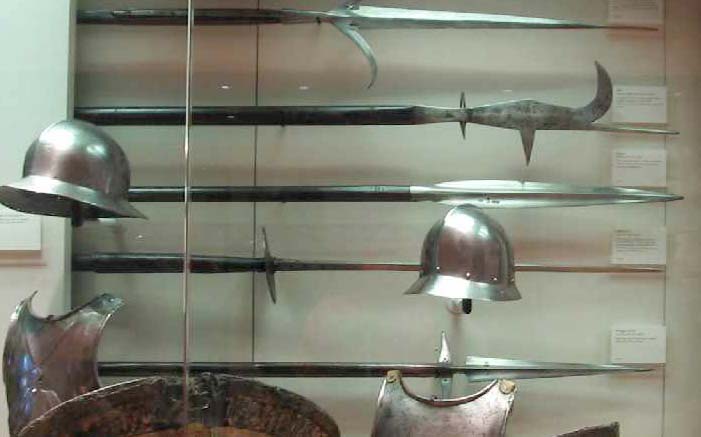
I'll also point out an interesting feature of many late military spears and boar spears. Note that the "small" end of the socket (where it meets the blade) is not much smaller than the "large" end. Note also that the sockets look unreasonably short. It looks to me like these heads were made in the same fashion as halberds, with leaves folded around a mandrel to create a socket within the body of the blade. So, I'm thinking that the hafts of these weapons extend some distance into the blade. All this would make for a very strong mounting.
Don't you just love the hollow grind/socket ridge of these weapons? These are truly terrifying-looking spears. Nothing light or elegant about them. Brutal.
Don't you just love the hollow grind/socket ridge of these weapons? These are truly terrifying-looking spears. Nothing light or elegant about them. Brutal.
Hi Sean,
I read with interest your comments that historically, the shafts of spears were formed with a "step" causing the socket and shaft to be flush. Do you know if this was done in earlier centuries such as the 11th,12th, and 13th? I would like to have my spear and potential polearms finishhed in an appropriate manner. My A&A 12th c. spear is fitted in the usual simple manner of A&A spears i.e. not flush with no bolts or nails. Is this method accurate? I also have a question regarding the edges/point of my spear- the point is sharp but there are no cutting edges to speak of on this spear. Is this accurate?
Thanks,
Jeremy
I read with interest your comments that historically, the shafts of spears were formed with a "step" causing the socket and shaft to be flush. Do you know if this was done in earlier centuries such as the 11th,12th, and 13th? I would like to have my spear and potential polearms finishhed in an appropriate manner. My A&A 12th c. spear is fitted in the usual simple manner of A&A spears i.e. not flush with no bolts or nails. Is this method accurate? I also have a question regarding the edges/point of my spear- the point is sharp but there are no cutting edges to speak of on this spear. Is this accurate?
Thanks,
Jeremy
Jeremy V. Krause wrote: |
Hi Sean,
I read with interest your comments that historically, the shafts of spears were formed with a "step" causing the socket and shaft to be flush. Do you know if this was done in earlier centuries such as the 11th,12th, and 13th? I would like to have my spear and potential polearms finished in an appropriate manner. My A&A 12th c. spear is fitted in the usual simple manner of A&A spears i.e. not flush with no bolts or nails. Is this method accurate? I also have a question regarding the edges/point of my spear- the point is sharp but there are no cutting edges to speak of on this spear. Is this accurate? Thanks, Jeremy |
Well, I've managed to sharpen mine a bit to a useable edge but with the thick spine and narrow blade it's never going to be much of a slashing or cutting type pollarm. My A & A Viking spear is more like a knife or dagger blade on a stick and is thinner and would have a bit more potential being used to cut against an un-armoured foe or an un-armoured body part.
Still a spear is mostly a thrusting weapon: One might compare then to Rapiers with varyingly effective cutting edges, the 12th century spear being closer to the thrust only ones and the Viking spear like a more sword bladed cut & thrust type.
As for the step I don't know what was used in period. One thing I wonder about is whether any leather or cord warping was ever used commonly with spears ? Warping the shaft of a spear with cord, maybe glued on, should reinforce a spear shaft from splitting and keep one together even if it split lengthways ?
What is related to your question about the shaft being flush with the socket is that with the stepped down shaft a cord binding covering the entire shaft would give a flush appearance to this spear: Thus the question about binding with cord being know historically or not ?
Here's a thought. Any chance of getting some sort of very cheap spearheads for simple javelins/darts? Maybe even tanged so we can get them extra cheap?
I think the flush mounting looks more "serious" and authentic, but I don't know about its appropriateness for earlier spear forms. Judging only from the development of other polearms, I would guess that spear hafting methods would have gone from less to more complex. That certainly doesn't apply to Roman pilae--the most complex spear/javelin I can think of-- so my guess probably isn't worth much. :confused: As far as edge sharpness is concerned, I think it does make sense to think of spear blades like we think of sword blades. Broad and thin=sharp edges, narrow and thick=less sharp. By the way, it looks to me like the consensus on use of all polearms is that they are most effective in the thrust.
A few years ago I was fortunate enough to stumble upon a reenactment of the Battle of Hastings at Battle Abbey. In the freestyle mock combat, a spearman held off several swordsmen for a surprisingly long time. This was not choreographed--the swordsmen just couldn't get past the point. That really opened my eyes to the value of the spear, even over the halberd. It's relatively lightweight (so also fast,) durable, inexpensive, easy to make, frugal with limited resources (iron) and free with abundant ones (wood), gives the advantage of range, and is very effective in combat. It's almost a perfect weapon.
Hank: I hope we'll see some late spearheads from your new venture!
A few years ago I was fortunate enough to stumble upon a reenactment of the Battle of Hastings at Battle Abbey. In the freestyle mock combat, a spearman held off several swordsmen for a surprisingly long time. This was not choreographed--the swordsmen just couldn't get past the point. That really opened my eyes to the value of the spear, even over the halberd. It's relatively lightweight (so also fast,) durable, inexpensive, easy to make, frugal with limited resources (iron) and free with abundant ones (wood), gives the advantage of range, and is very effective in combat. It's almost a perfect weapon.
Hank: I hope we'll see some late spearheads from your new venture!
Page 1 of 1
You cannot post new topics in this forumYou cannot reply to topics in this forum
You cannot edit your posts in this forum
You cannot delete your posts in this forum
You cannot vote in polls in this forum
You cannot attach files in this forum
You can download files in this forum
All contents © Copyright 2003-2006 myArmoury.com All rights reserved
Discussion forums powered by phpBB © The phpBB Group
Switch to the Full-featured Version of the forum
Discussion forums powered by phpBB © The phpBB Group
Switch to the Full-featured Version of the forum