I'm a long time member but not a regular poster, but hopefully that will change. I enjoy following DIY threads and now I have a few DIY projects going on which I would like to share. I'm afraid it's nothing that hasn't been done before but still if you're like me then you probably find it interesting to see how others tackle a certain task. So, I hope some will find this interesting.
A while back I got two dagger blades from Paul Binns. They were quite cheap so I didn't expect them to be brilliant but even with that in mind I was a bit disappointed. However, now I have two dagger blades to play around with without worrying too much about mucking them up.
The blade in the top of the picture is OK-ish so I will leave it alone for now but the bottom one just looks very odd. The edges are wavy and the whole thing is very unevenly ground. As a first step I want to fix the profile of the blade. Eventually I want to make a hilt similar to the daggers found in The Royal Armouries and the Bayerisches Armeemuseum. For those who aren't familiar with these daggers check out the Aunlaz dagger by Arms & Armor you can also find a review by Chad Arnow in the reviews section.

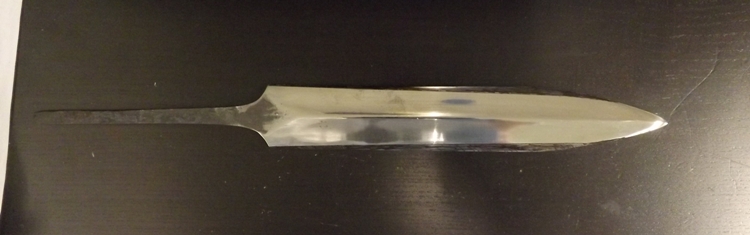
Using a fine tipped permanent marker I drew the new profile on the blade and colored the sections which need to be ground off.


I'm not sure yet what to do with the top one...