I bought this small German nicker at a flea market a few days ago. For various reasons I'd like to give it a new chape in the style of a South American gaucho knife with a drag on the end. The puņal criollo shown about halfway down this page is the general shape that I'd like to use, although probably much more detailed than I'd be able to achieve.
How do you make a chape with a drag? The only methods I could figure out are that the chape is made in a front and back half, and the drag is an extension of one or both halves, which are then soldered, brazed or welded together, or that the drag is made separately with tabs inserted into slots or between the halves of the chape and again soldered/brazed/welded.
Also, could anyone venture a guess about what metal the fittings are made of? The green patina seems like verdigris (I can scrape it off with my fingernail), so I would guess maybe nickel silver?

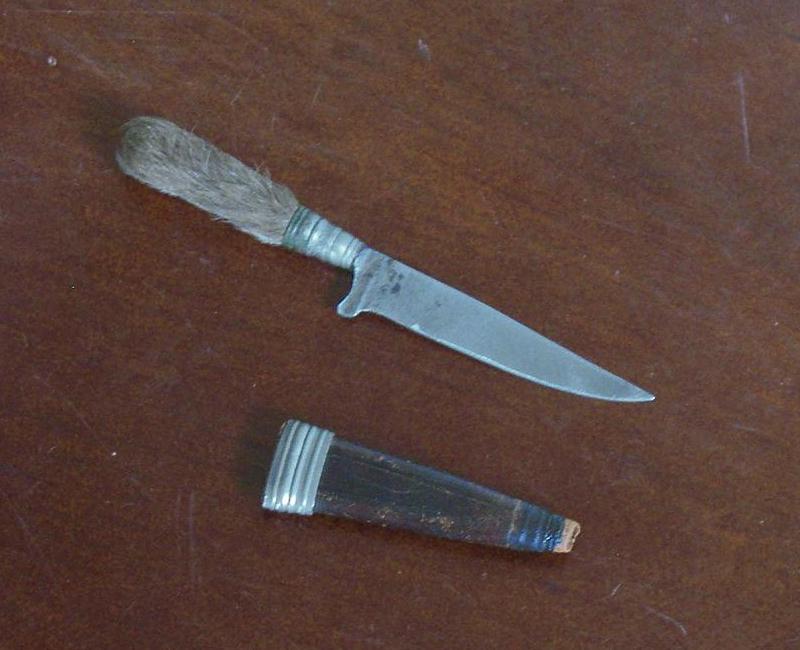