So here is a new experience for me and that is making a zweihander - have never made a sword this large before, though I did make a reproduction of the guard a few years ago.
The sword is based on a piece sold by Hermann Historica a few years ago. There are a few basic stats on the piece, but much of the information I would like is unavailable, so I have had to extrapolate a little from what I do know and approached Toby Capwell and Peter Johnsson for any information they could give on likely blade dimensions.
I am making a video diary of the piece and that will appear on You Tube in due course, mainly because this is an interesting piece for a few reasons. The blade is very long at 132cm and the whole sword is 180cm/6ft overall and I thought it wouldn't fit in my grind room, so that was the first spect and then the next is the grip which will be quite a challenge, mainly because right now I still don't know how I am going to handle it. Other than that, it is going to be a stunning piece (I hope), so worthy of me making a an effort to document it.
The blade length is 132cm, the grip is 40cm long and the overall length is 180cm
I started with a strip of 8mm thick EN45 spring steel and forged out the lugs and finished the profiling. At this length, I decided warping in the heat treat could be a real issue, so I had it heat treated with no taper and then ground in the taper after treatment and it is has remained dead straight.
The blade is 8mm thick at the guard, it drops to 6.5mm at the lugs, 5.5 at the end of the fuller, 4mm thick at 45cm from the tip and 1.5mm thick just up from the tip and the blade is hexagonal in form.
As it happened, with moving the grinder around, I just managed to fit the blade in the grind shop and I managed to shape it pretty much in the normal way, so I thinned it down to put the distal taper in and then ground the fuller in. The lower part of the fuller was done with a single wheel and then as the fuller widens, I used a further 3 wheels and then blended the transitions by hand. The ricasso area of the blade has further fullers on each side and they were straight forward enough to grind in, but the transition into the parrying lugs also had to hand blended.
The next stage was to grind the bevels into the blade and I was quite confident that this would be fine. I was wrong.
The blade is, stating the obvious, very long and this means that reaching out to steady and hold the blade is quite difficult and near the lugs it was fine. Toward the tip, it all became a bit flexible and unwieldy and so rather than repeating each move to establish crisp and neat flats for the bevels, I was wandering around a bit and there was no way I was going to get a good result, so I managed to set the edges, but not make it neat. This was unexpected.
So I went back to basics and clamped the blade to a plank and got the angle grinder out with sanding discs and carefully ground to the scribed lines with a medium disc and then a fine disc and it all looked good. I then went back to the grinder using a flexible platten and this has the advantage of giving a slight apple seed edge and also softens the transitions allowing for problem blades to still look good.
Now the blade is polished I am pleased with the result and so went on to making the grip. The grip is very sculptural with lots of cord work under the leather, and sports very prominent central turnings. I took a round billet of wood and sawed it into two halves and then cut out the recesses for the tang. The grip core was then glued back together to give an almost round result. This round core was the turned to make it round and the central turned section was cut in.
And that is far as I got so far...............
I hope you like to so far and let me know if you have any questions or comments.
Tod

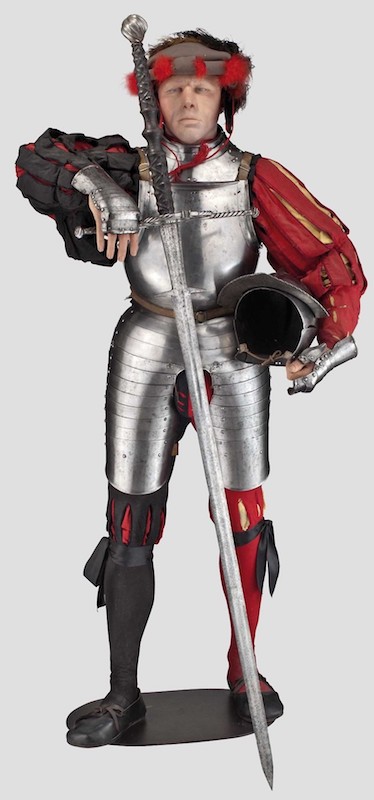

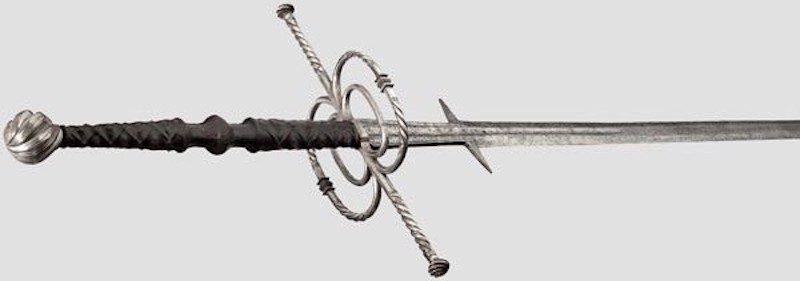

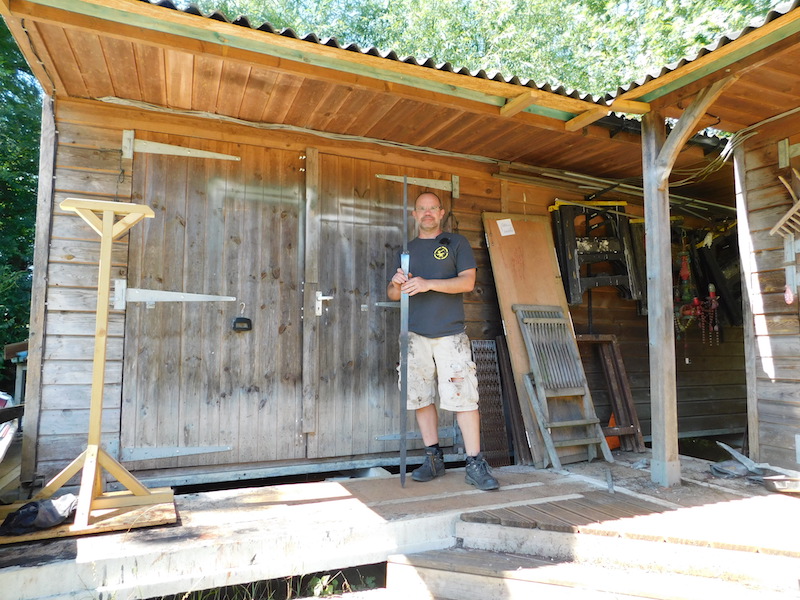



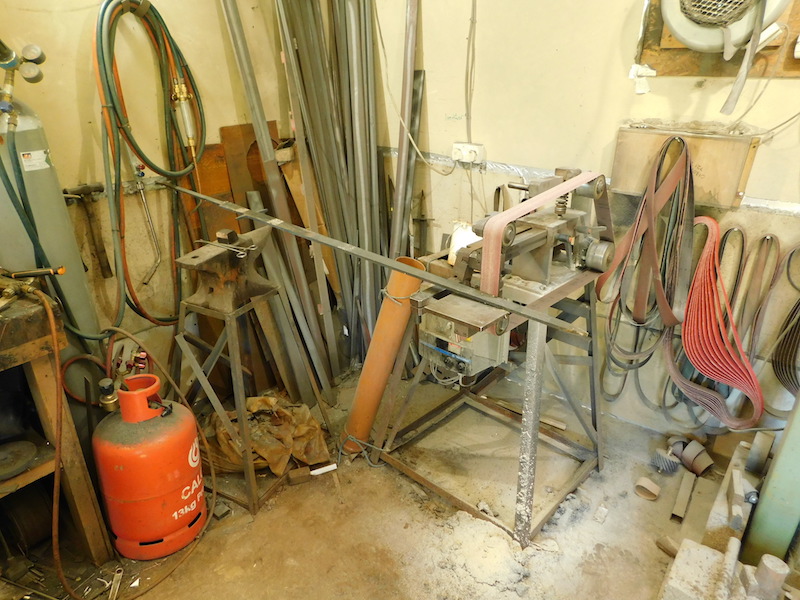

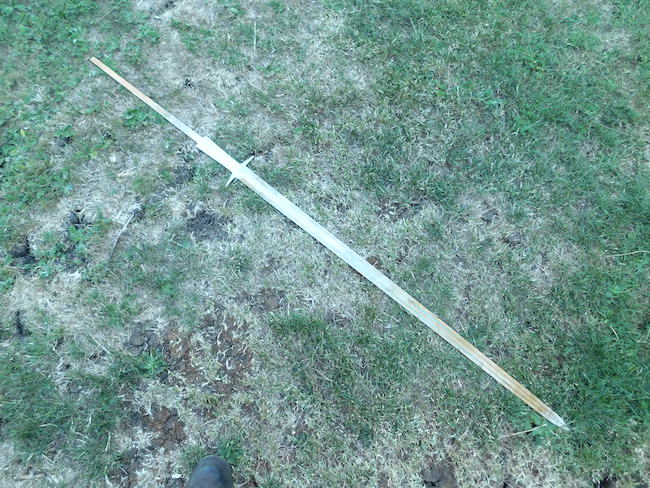

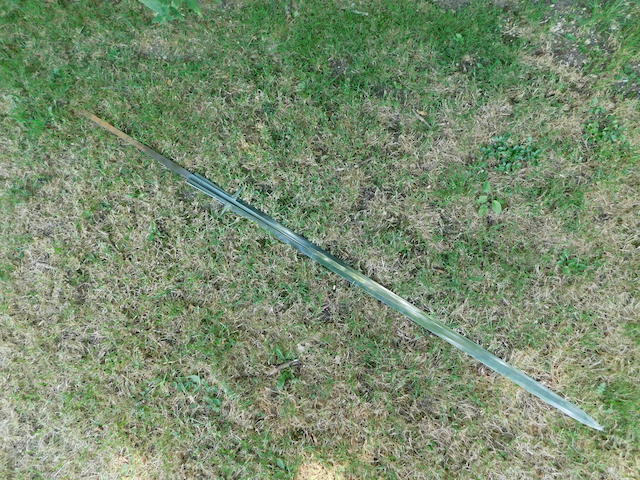

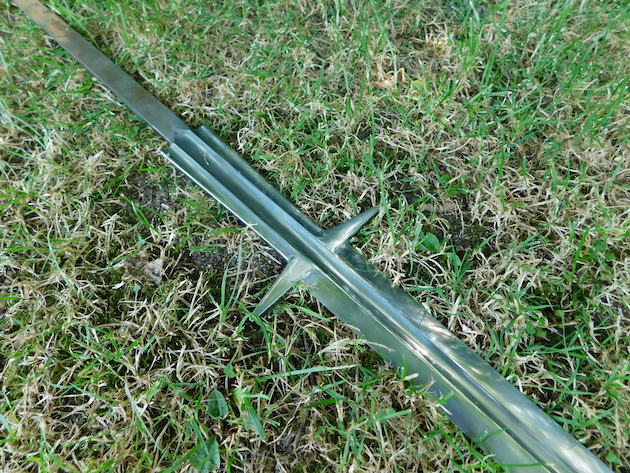

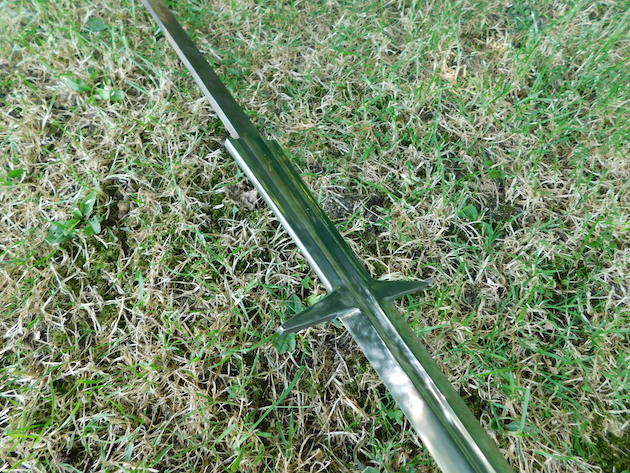

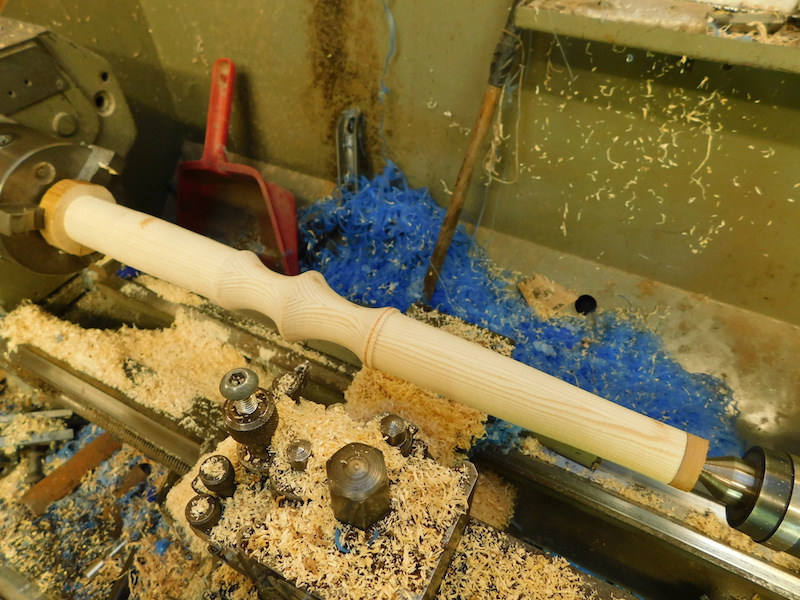