Here is the original sword, bought from MRL years ago. Big and heavy, handle is twisted (carved) wood that I covered in leather. Handle was always too fat, and round so it felt extremely uncomfortable. Blade is a bit rough, always was...has some wavy hammer marks, not perfect looking down the edge...but overall it is nice and symmetrical and most important to me, NOT whippy in the least. Quite a stiff blade. And I always like the near parallel blade profile, very little profile taper. The thing was heavy overall and blade heavy in particular.
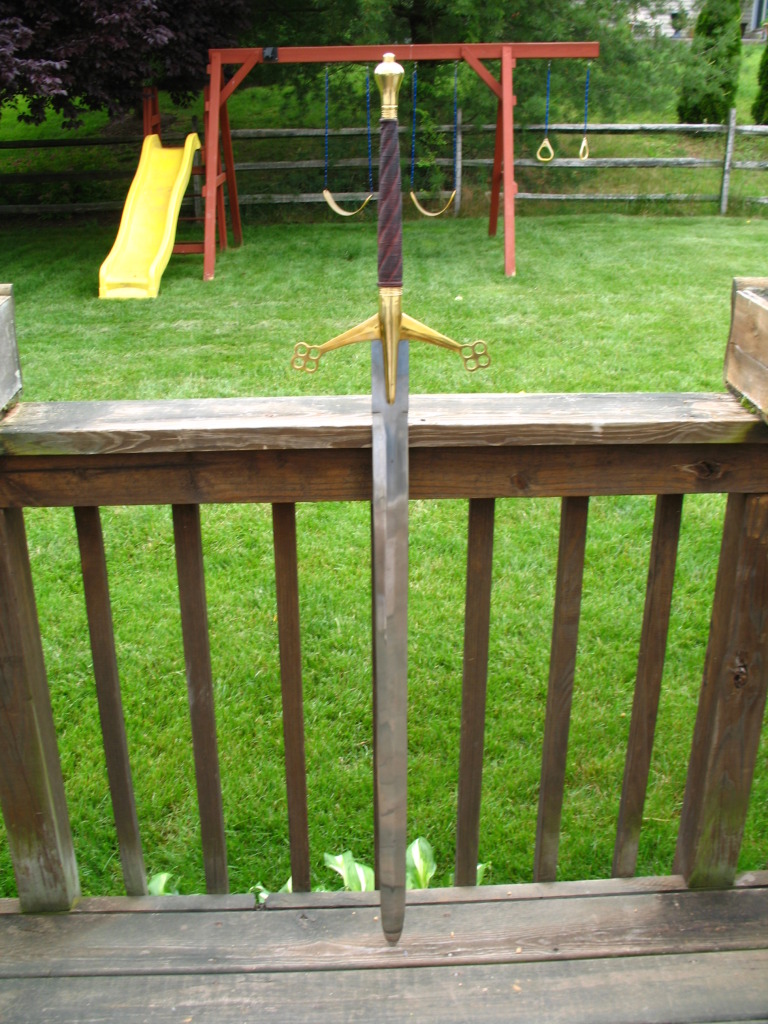
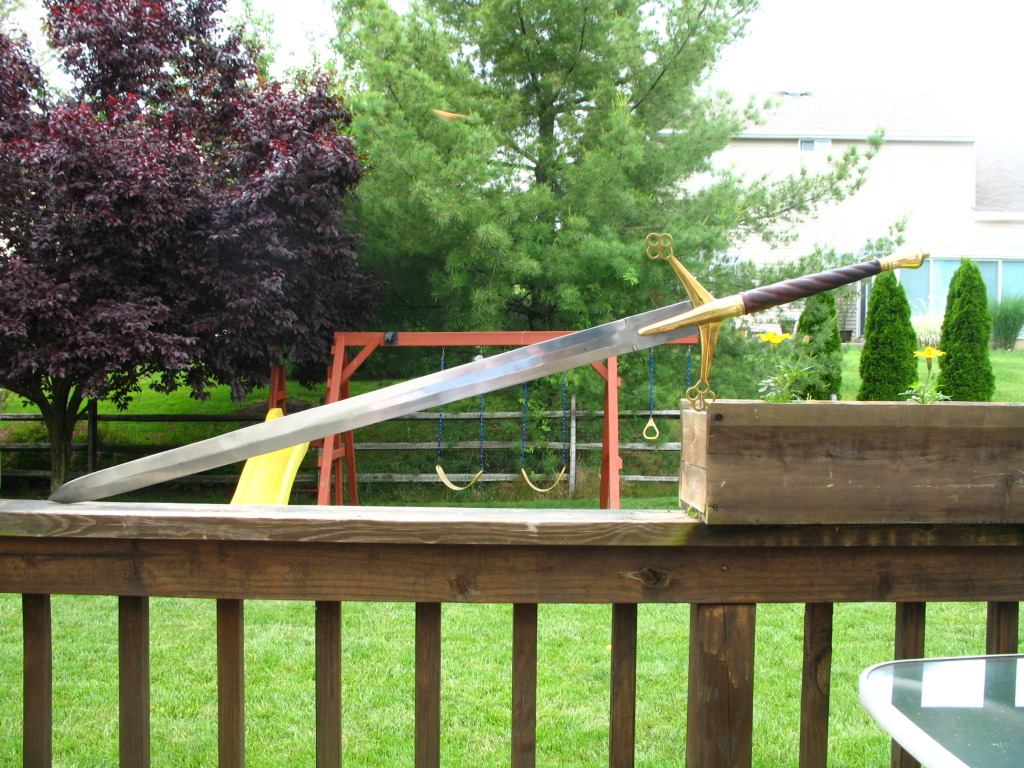
I took it apart, hack sawed almost 3 inches off the shoulder of the blade and cut off the crappy threaded rat tail.
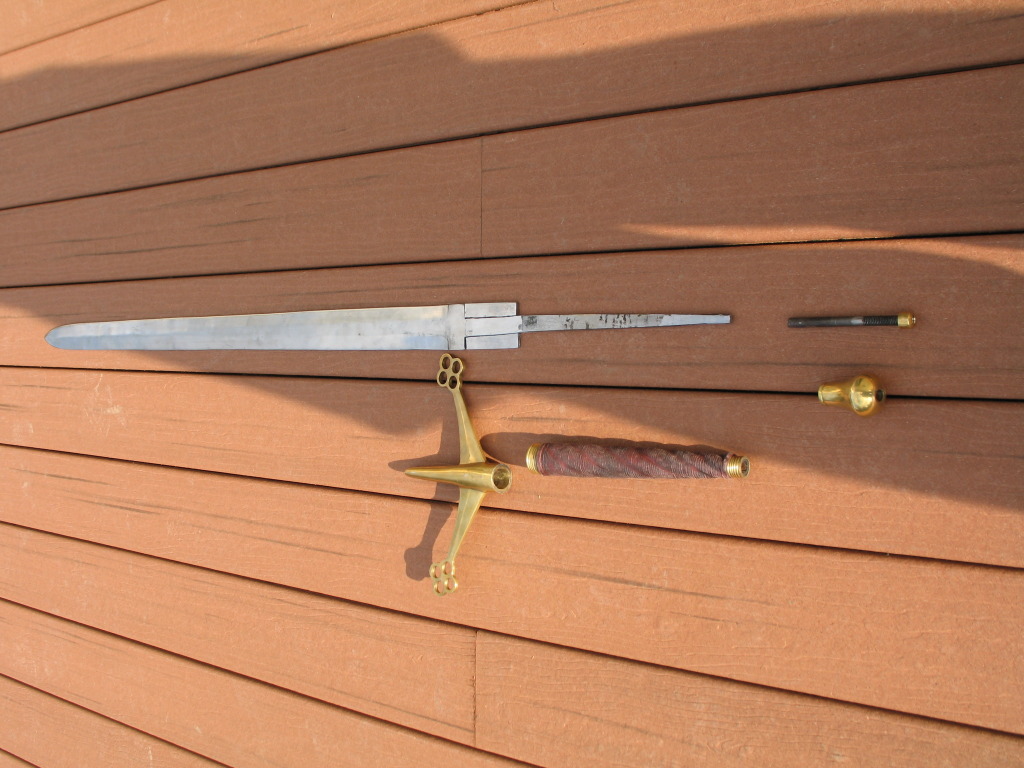

Then I purchased some mild steel from an online vendor in order to "machine" the cross guard and pommel, 1/2 inch square bar (9" long) and round bar 2" by 3/4" thick. I drilled holes through it to rough out the slot and then used a dremel and hand files to finish it off. Its not the greatest machine job, but the rougher areas are inside the slot and will be hidden by the blade when it is seated, so I don't care that much, the important thing for me so far is its tight and fits good.
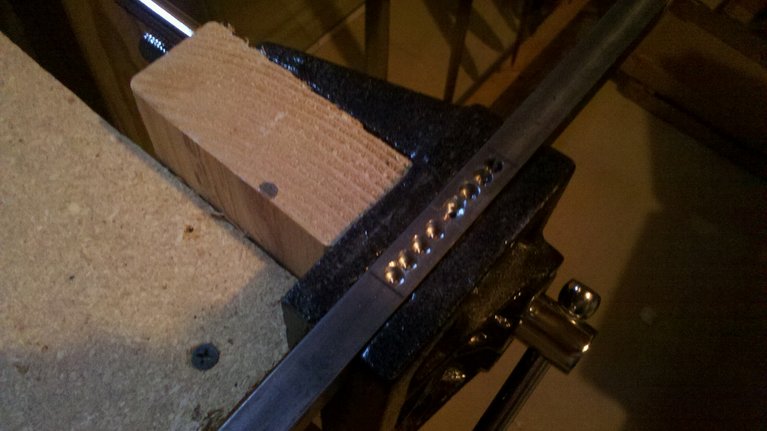

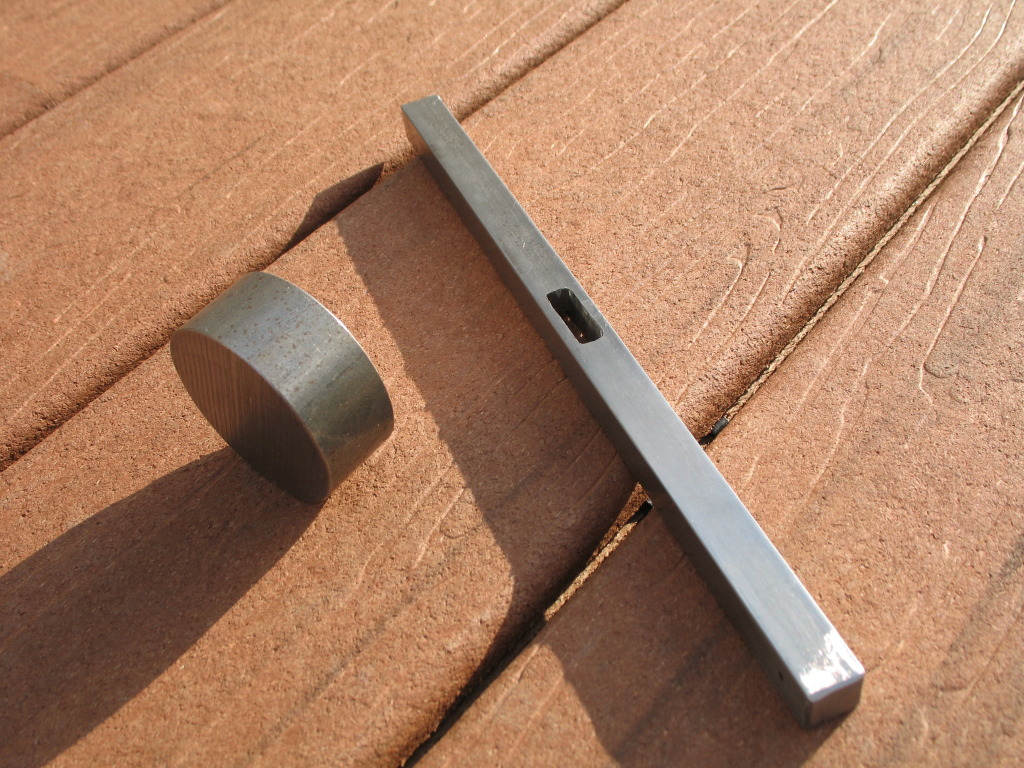
Here is a roughed out idea of what I will end up with. I am going for a no nonsense great sword, straight guard and wheel pommel, I wish the blade was fullered but what can you do? Have yet to decide on the final handle length, its pretty long now, I may keep it approximately this length but I might shorten it some, if I do it won't be by a lot. Next step is to key the pommel, that will be super tough. I have at me disposal a drill press and the aforementioned dremel and hand files. We will see. This is all new territory for me, working with steel like this in order to rebuild a sword, so its a learning experience but one that so far has been rewarding. Wish me luck!
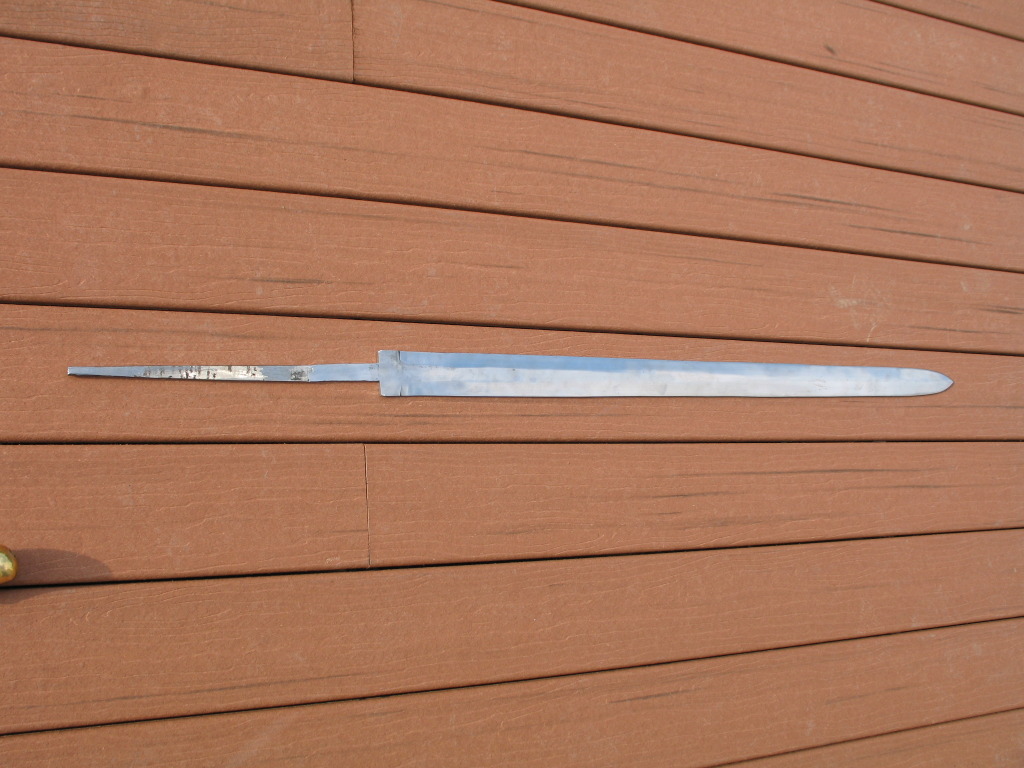
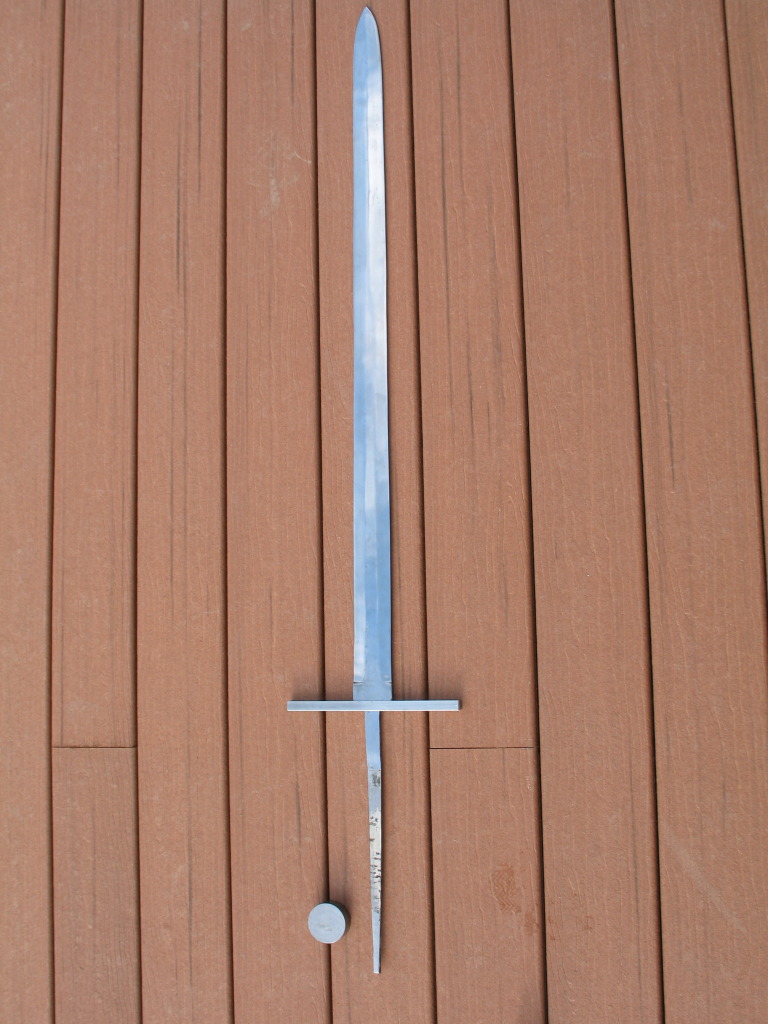
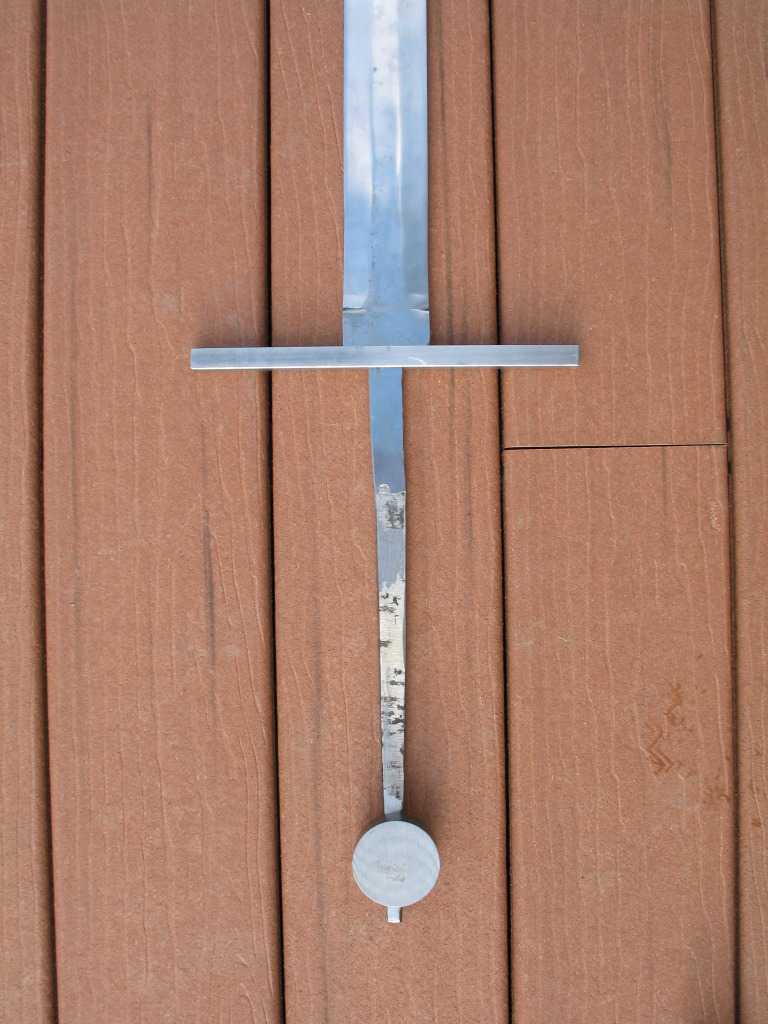
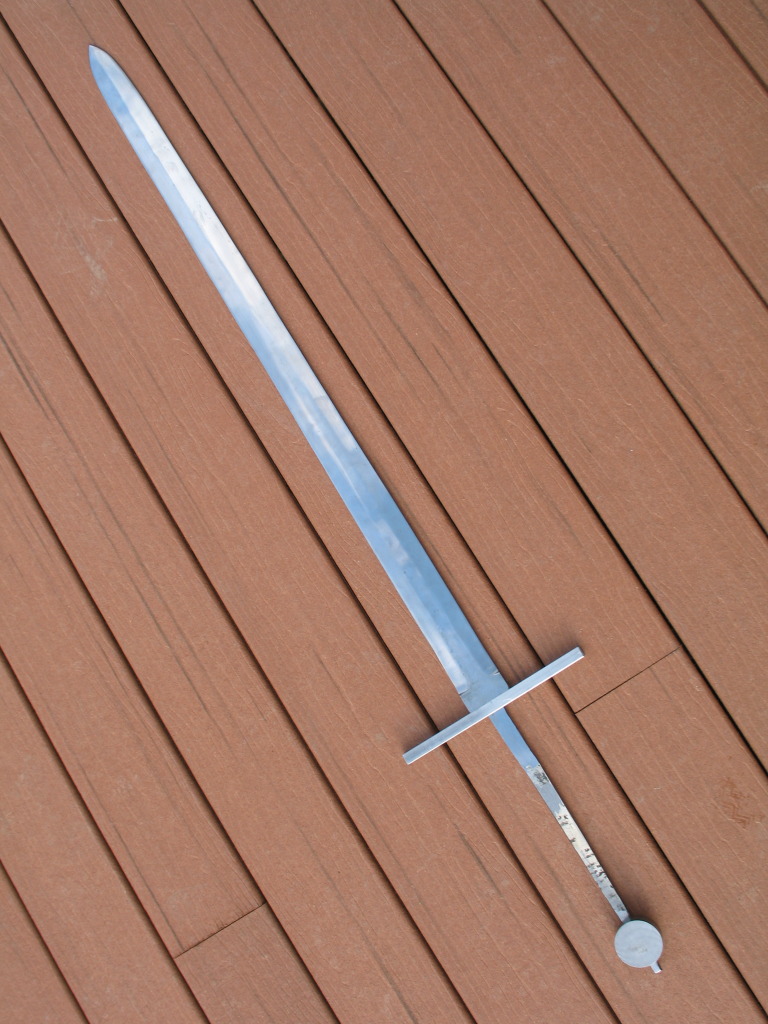