As my yeoman project below is currently on hold because I can't find an effective way to drill through 1 cm of mild steel for a peen block (yeah, simple things can delay completion for month in my world :) ), I decided to start working on another blade, the squire, which I was lucky enough to grab from the moat, as a second blade (again, pristine though I will regrind the tip to a needle).
http://www.myArmoury.com/talk/viewtopic.php?t=21636
For the yeoman, I went all the way for the cross guard, from anvil to grinder. I took a long time and efforts to get it right, so I decided to allow myself a shortcut here, and ordered a bunch of hilt components form Armour Class as they are UK based.
My intention was to rework most on the anvil/grinder, but to use these as a base, the idea being to spare me some painful steps such as punching the tang slot on the anvil etc...(Though some might say I could invest in a drill press...).
I ordered a pommel an 3 crosses. All serviceable and quiet nice but they will need some work to match the precision and finish of an Albion blade (the tang slot is not centered, and the guard much too thick for an Albion).
As soon as I took this guard out of the box, I knew it would be a good fit for the squire, and to be fair, the pommel is adequate as well for a type XVI sword. After some time filing the tang slot, there it is below.
My initial idea what to go for the Copenhagen sword below, which I always liked, but to be fair, I like the ecusson area of the current cross and will likely keep it as it is. It is possible that this time I'll take the easy route without complicating things too much.
So next I will round the pommel and tweak it to adjust weight, will also need to fill the sides of the tang slot with a dab of weld (one thing I don't like is a squarish recess for the blade) then create the blade recess and thin the cross. Then I will even it and fine tune its geometry to match the aesthetic of the blade. Then the usual: grip, leather, scabbard done :) I'm really excited about this sword and glad to have reached that stage of completion with so little efforts.
Let me know what you think!
J
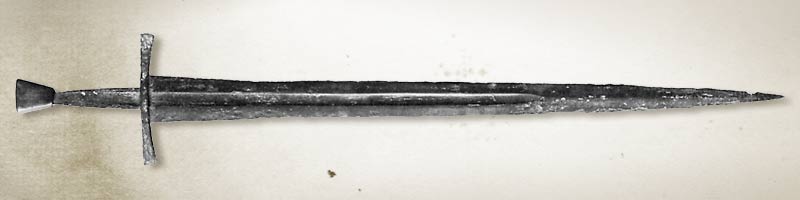
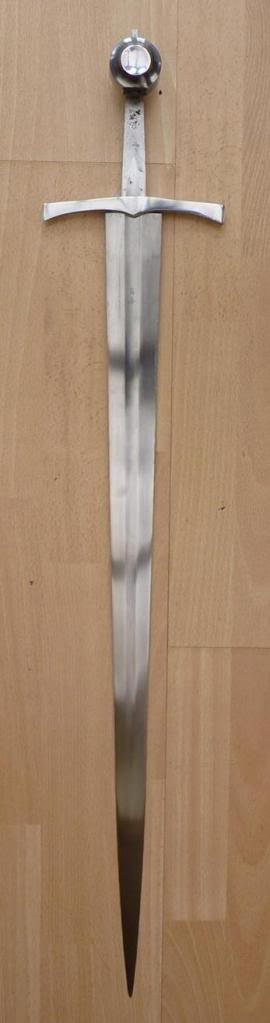
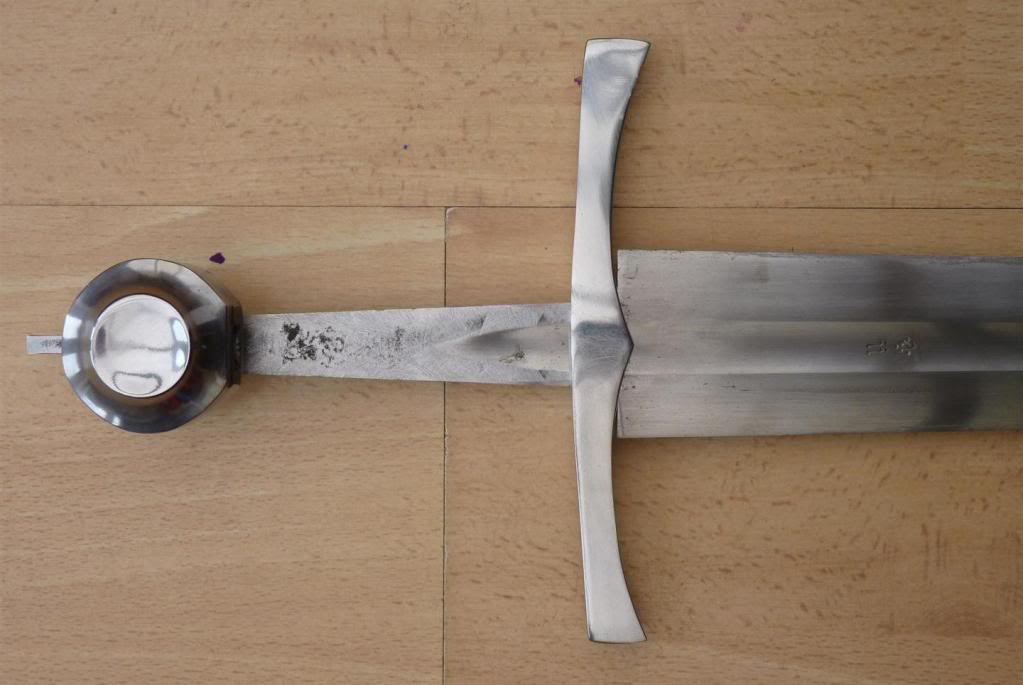