Last autumn I arranged with Arms and Armor for them to recreate a classic Amsterdam Walloon for me. I believe that this is the first time in around 300 years that this particular sword type has been made. It isn't the most ornate of swords, but it definitely has something. It may not be the sword that you would wear to court, but it's one that you would take into battle.
The sword is almost ready - I should receive it in about a week. In the meantime A&A has taken a numboer of photos that I'd like to share with you. It looks like A&A did their usual terrific job.

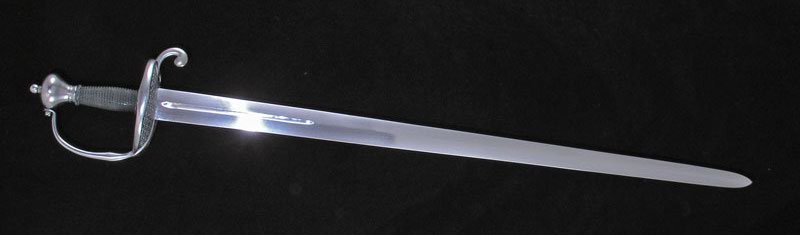

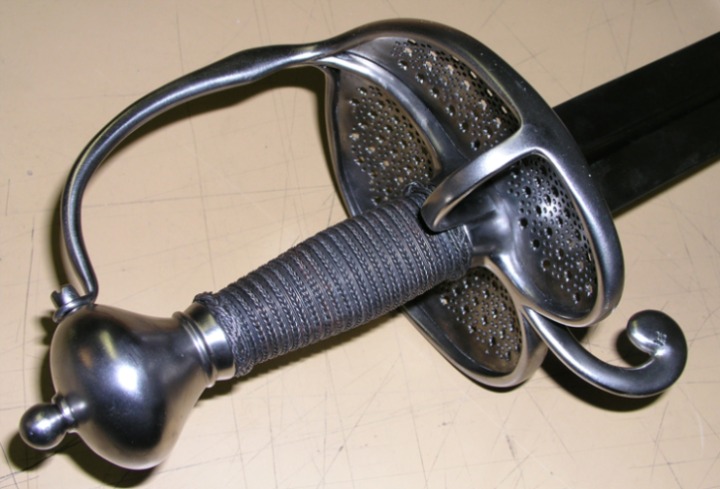

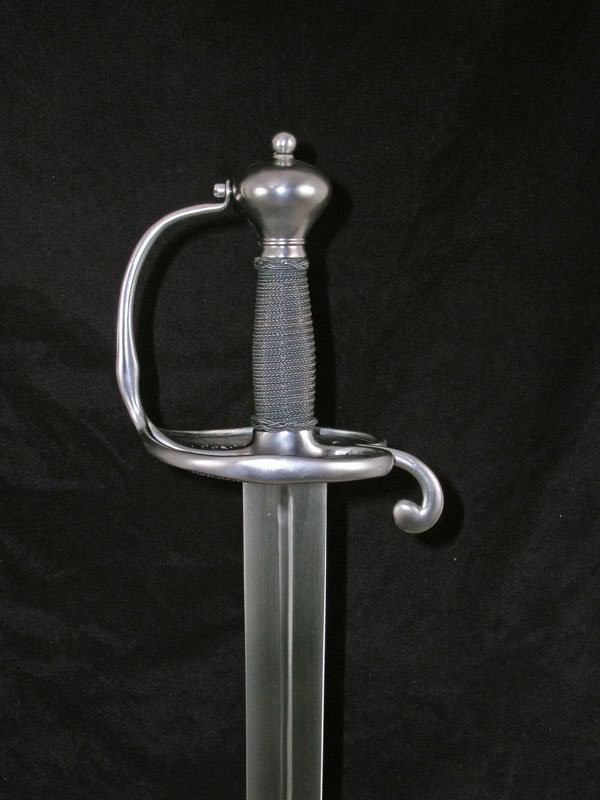

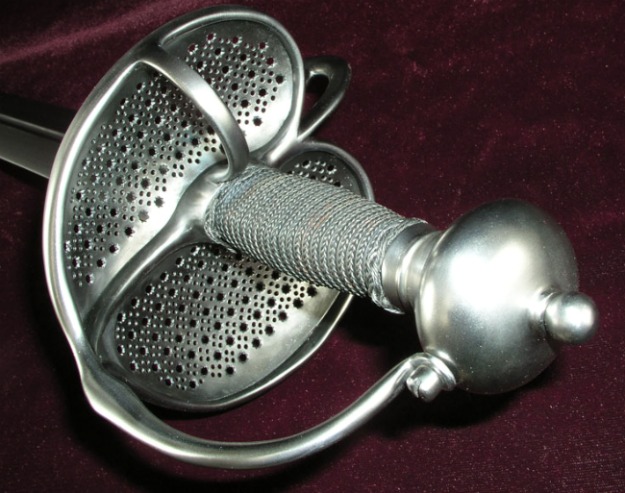

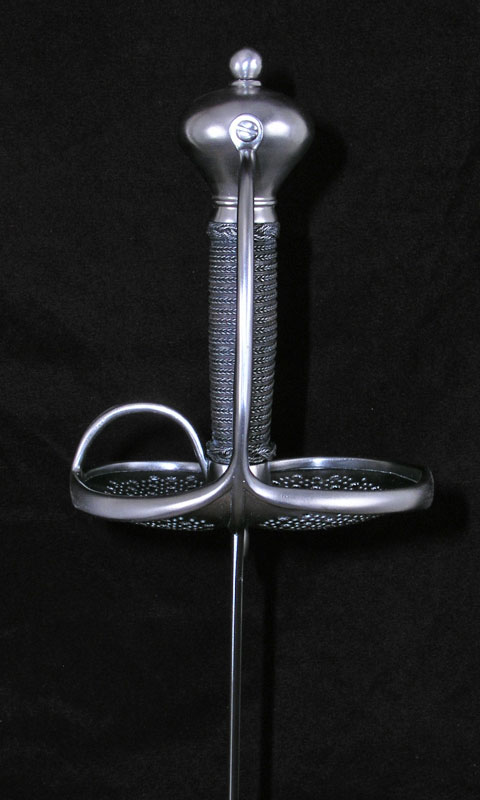

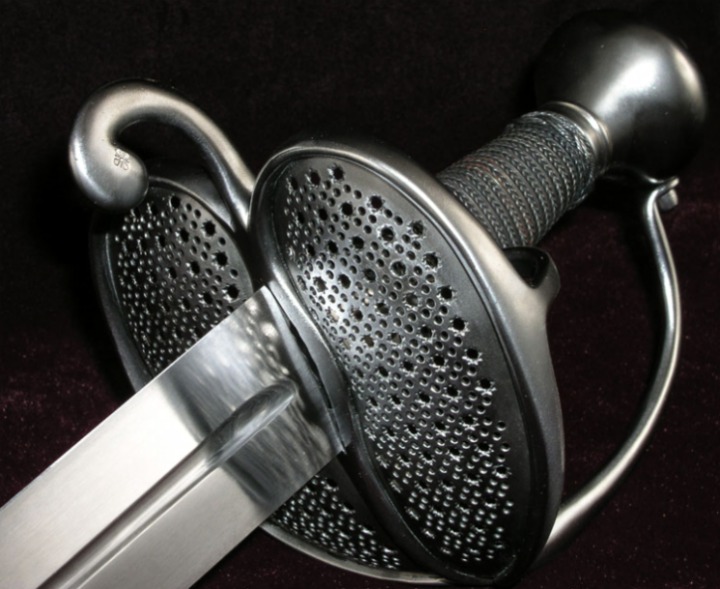

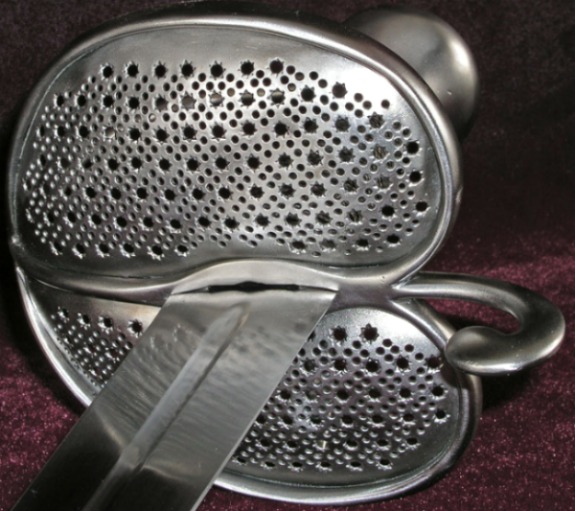