I have been intrigued by the single edged Viking sword found on the Arhus Farm in Norway since I saw pictures of it in Ian Pierce’s “Swords of the Viking Age.” It may be the only single edge Viking sword ever found with a pattern welded blade. About six years ago I convinced Vladimir Cervenka into building a replica of this sword for me. This sword was not meant to be an exact replica of the Arhus Farm find. There are some differences, such as an H pommel instead of the C pommel on the original. If you have not seen this Cervenka sword, I have reviewed it here.
http://www.myArmoury.com/review_cerv_vikse.html
ks


North Arhus Farm find preserved in the Kulturhistorisk (Cultural History) Museum, Oslo Norway. Image compiled from "Swords of the Viking Age" by Ian Pierce

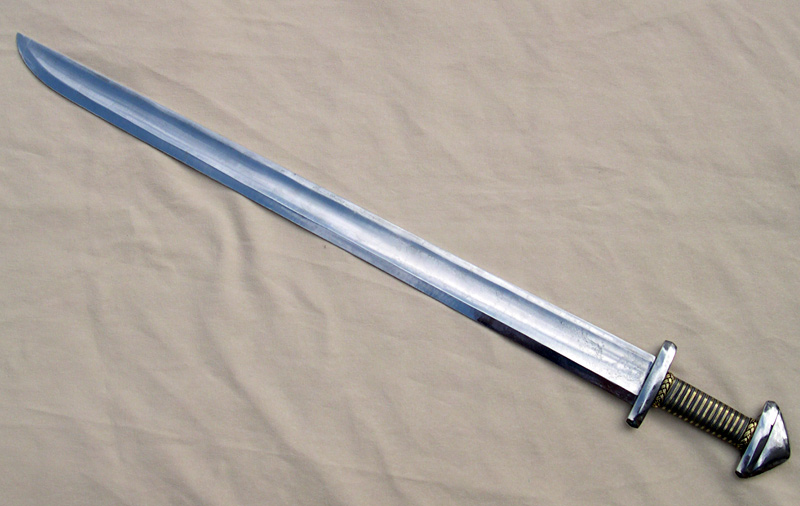
Arhus Farm Recreation by Vladimir Cervenka


Arhus Farm Recreation by Vladimir Cervenka